一種汽車內飾前門把手後射法氣輔注塑成型模具的製作方法
2023-05-10 06:52:24 2
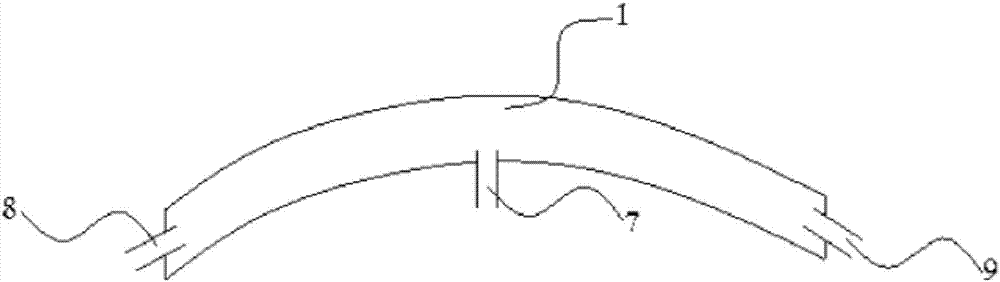
本發明涉及模具設計技術領域,尤其涉及一種汽車內飾前門把手後射法氣輔注塑成型模具。
背景技術:
氣輔注塑成型技術因其殘餘應力低、不易翹曲、尺寸穩定、低鎖模力、生產周期短、成本低等特點,在國內外得到廣泛應用,其原理是通過惰性高壓氣體在注塑產品內部產生中空,完成熔融塑料填充、保壓、冷卻、凝固,優於傳統注塑成型技術。
在汽車門把手注塑成型時,一方面為使注塑成型的門把手內部形成空腔,節約原料,另一方面為彌補門把手在注塑成型時形成縮印缺陷,現有的注塑模具一般採用氣輔成型模具,在注塑時利用氣體(一般為氮氣)進行輔助注塑。
現有的汽車門把手氣輔成型模具,一般包括一端設有進料口的型腔以及用於對型腔內吹氣的吹氣裝置,型腔的進料口同時設有頭部伸入型腔內的氣針,氣針尾部與吹氣裝置連接;即型腔的進料口與型腔的進氣孔位於型腔的同一端面。採用該結構的汽車門把手氣輔成型模具,由於進氣孔位於型腔的端面處,物料(如膠料)自身的重力作用會導致物料堆積於型腔底部造成汽車門把手的壁厚不均勻。
技術實現要素:
針對上述現有技術中存在的問題,本發明提供了一種汽車內飾前門把手後射法氣輔注塑成型模具,有效解決了注塑產品壁厚不均勻所產生的缺陷問題,有效縮短了生產注塑周期,節約了生產原料上的成本,提高了產品表面質量。
一種汽車內飾前門把手後射法氣輔注塑成型模具,包括一端設有進料口的型腔以及用於對型腔內吹氣的吹氣裝置,所述的型腔的底部設有進氣孔,所述的進氣孔與吹氣裝置連接;所述模具採用後射法氣輔注塑成型設計,先將製品的型腔全部填充滿以後,再注射氣體將型腔內多餘的料排除到溢料槽;整個先注射、再注氣的過程中需要一個滑塊閉合來控制溢流槽內熔融料的填充,而這個滑塊的閉合過程需要在模具合模的狀態下完成,控制滑塊的工作由自鎖自鎖油缸完成。
本發明氣輔成型模具將進氣孔設在型腔的底部,這樣能夠防止因物料(如膠料)自身的重力作用而導致物料堆積於型腔底部從而造成注塑產品壁厚不均勻。
所述的進氣孔優選位於型腔底部的中間區域。使用時,將經過高壓壓縮的氣體從型腔底部的中間區域導入熔融物料當中,當氣體在熔融物料中流動時通過置換熔融物料而掏空厚壁截面,氣體沿著阻力最小方向流向型腔的低壓和高溫區域,從而進一步保證製品壁厚的均勻性。
所述的型腔的另一端設有出料口,出料口還可以連接一溢料槽,所述的溢料槽的容積基本等於排出型腔外的物料的體積,用於承接排出型腔外的物料。
所述的溢料槽最好設置為迂迴結構,便於調控排出型腔外的物料的流速。
在所述的出料口和溢料槽之間設有自鎖油缸,所述的自鎖油缸連接滑塊和頂針,所述的滑塊帶動頂針上下運動,用於切斷或連通出料口和溢料槽。
所述的型腔可以為一個,也可以為兩個以上;兩個以上的型腔的進料口通過物料通道與進料裝置連接,可以同時成型多個製品,進一步提高生產效率。兩個以上的型腔最好對稱設置,以有效利用模具空間。所述的物料通道在遠離型腔的一端設有灌嘴,所述的灌嘴與進料裝置連接,通過灌嘴向物料通道灌輸物料更加方便快捷。
所述的吹氣裝置所用的氣體為高壓壓縮的氮氣。所述的吹氣裝置可採用現有裝置,如自封閉式氣輔噴嘴或者氣針等。
本發明氣輔成型模具還能夠應用於厚度變化大的產品,作為厚度變化大的產品的氣輔成型模具。
本發明的有益效果:本發明氣輔成型模具將進氣孔設在型腔的底部,這樣能夠防止因物料自身的重力作用而導致物料堆積於型腔底部從而造成注塑產品壁厚不均勻。本發明氣輔成型模具能節省30%的原材料,降低產品的殘餘應力,使產品不變形,解決和消除產品表面縮痕問題,能夠應用於厚度變化大的產品。本發明氣輔成型模具能夠降低注塑機的鎖模力,減少成型機的損耗,縮短產品生產成型周期時間,提高生產效率;降低模具型腔內的壓力,使模具的損耗減少,同時提高模具的使用壽命。
附圖說明
圖1是本發明的汽車門把手模具的結構示意圖;
圖2是本發明的汽車門把手模具中型腔與進氣孔的結構示意圖;
圖3是本發明的汽車門把手模具氣道、溢料槽系統設計示意圖;
圖中1為型腔,2為溢料槽,3為進料槽,4為吹氣裝置,5為灌嘴,6為自鎖油缸,7為進氣孔,8為進料口,9為出料口,10為滑塊。
具體實施方案
下面通過具體實施方式結合附圖對本發明作進一步詳細說明。
如附圖1、附圖2所示,本發明的汽車內飾前門把手後射法氣輔注塑成型模具,包括一端設有進料口8且另一端設有出料口9的型腔1以及用於對型腔1內吹氣的吹氣裝置4,型腔1的底部設有進氣孔7,進氣孔7與吹氣裝置4連接。
該模具將進氣孔7設在型腔1的底部,這樣能夠防止因物料自身的重力作用而導致物料堆積於型腔1底部從而造成注塑產品壁厚不均勻。
進氣孔7最好位於型腔1底部的中間區域,如圖2所示。使用時,將經過高壓壓縮的氣體(如氮氣)從型腔1底部的中間區域的進氣孔7導入熔融物料當中,當氣體在熔融物料中流動時通過置換熔融物料而掏空厚壁截面,氣體沿著阻力最小方向流向型腔1的低壓和高溫區域,從而進一步保證製品壁厚的均勻性。
型腔1的出料口9還可以連接一溢料槽2,溢料槽2的容積基本等於排出型腔1外的物料的體積,用於承接排出型腔1外的物料。
溢料槽2最好設置為迂迴結構,便於調控排出型腔1外的物料的流速。
在出料口9和溢料槽2之間設有自鎖油缸6,自鎖油缸6連接滑塊和頂針(圖1中省略,未畫出,可參見附圖3),滑塊帶動頂針上下運動,用於切斷或連通出料口9和溢料槽2。
型腔1可以為一個,也可以為兩個以上;兩個以上的型腔1的進料口8通過物料通道與帶進料槽3的進料裝置連接,可以同時成型多個製品,進一步提高生產效率。兩個以上的型腔1最好對稱設置,以有效利用模具空間。物料通道在遠離型腔1的一端設有灌嘴5,灌嘴5與進料裝置的進料槽3連接,通過灌嘴5向物料通道灌輸物料更加方便快捷。
吹氣裝置4所用的氣體為高壓壓縮的氮氣。吹氣裝置4可採用現有裝置,如自封閉式氣輔噴嘴或者氣針等。
如附圖3所示,本發明採用後射法氣輔注塑成型設計,先將製品的型腔全部填充滿以後,再注射氣體將型腔內多餘的料排除到溢料槽,所以這裡的溢料槽的體積必須大於等於產品要掏空部位的體積。整個先注射、再注氣的過程中需要一個滑塊閉合來控制溢流槽內熔融料的填充,而這個滑塊的閉合過程需要在模具合模的狀態下完成,控制滑塊的工作由自鎖自鎖油缸完成。這種方式對於製品表面光滑要求較高的時候使用,缺點是排出的溢料較多,原料比較浪費,注塑工藝也比較複雜。
本發明的模具還能夠應用於厚度變化大的產品,作為厚度變化大的產品的氣輔成型模具。
本發明的模具使用時,打開型腔1的進料口8並關閉出料口9和進氣孔7,將熔融物料依次通過進料裝置的進料槽3、灌嘴5和進料口8通入型腔1內,熔融物料遇到溫度較低的型腔1內壁厚形成一層較薄的凝固層,關閉型腔1的進料口8並通過自鎖油缸6打開出料口9,打開進氣孔7,利用吹氣裝置4向型腔1內吹氣,將經過高壓壓縮的氣體從型腔1底部導入熔融物料當中,當氣體在熔融物料中流動時通過置換熔融物料而掏空厚壁截面,氣體沿著阻力最小方向流向型腔1的低壓和高溫區域,從而保證製品壁厚的均勻性,被吹出的物料經出料口9排出型腔1至溢料槽2進行回收利用。
以上內容是結合具體的優選實施方式對本發明所作的進一步詳細說明,不能認定本發明的具體實施只局限於這些說明。對於本發明所屬技術領域的普通技術人員來說,在不脫離本發明構思的前提下,還可以做出若干簡單推演或替換,都應當視為屬於本發明的保護範圍。