一種新型輸送帶式自動上料結構的製作方法
2023-09-15 18:04:50
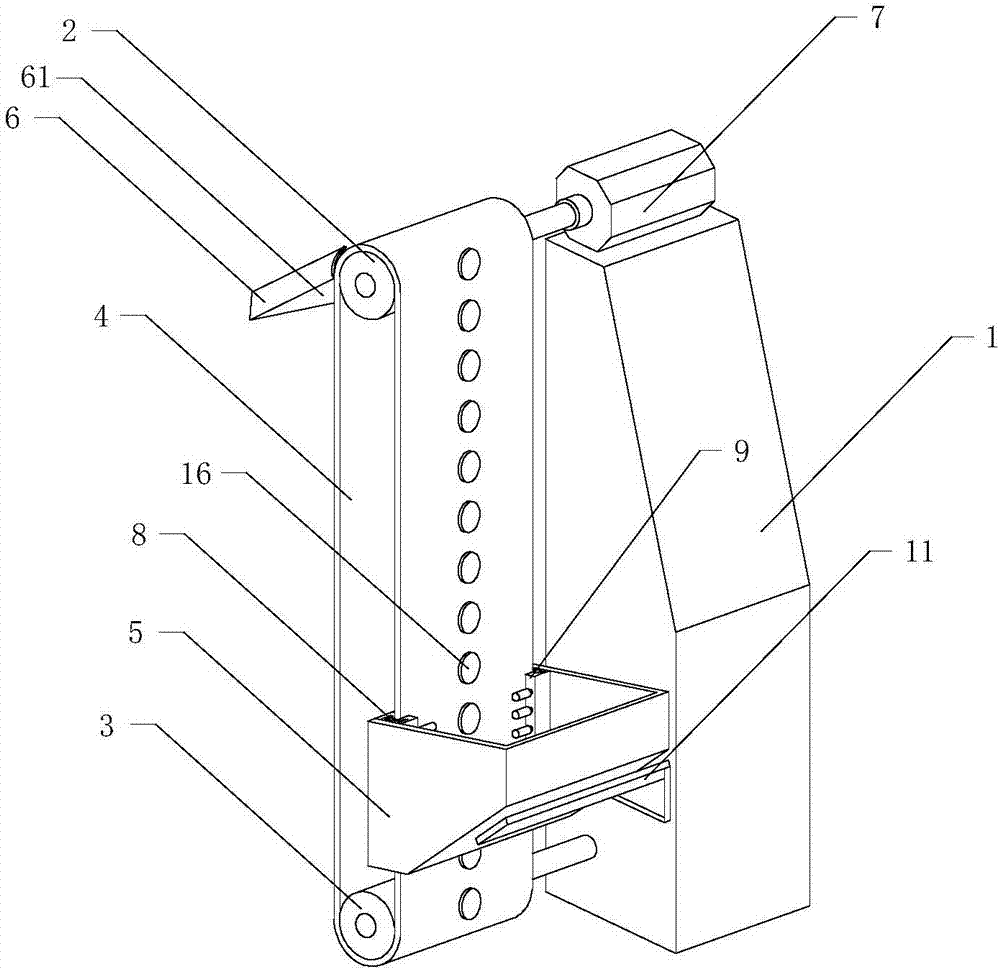
本實用新型涉及機械設備技術領域,具體涉及一種新型輸送帶式自動上料結構。
背景技術:
上料機構通常應用於流水線設備之間,實現對零部件或者半成品的轉運對,即將待加工工件由某一存放區域或加工區域運送至下一個加工工位,此轉運工作通常是由人工來完成的。現有的技術中,某些具有條件的生產部門已經在工業流水線使用上料機構進行工件的轉運,現有的上料機構大多是結構複雜,體積龐大,自動化程度不高,並需要其他機械裝置的高度配合,使工作人員的勞動強度大大提高。目前,對於將小的金屬零部件由低處轉運至高處,現有的上料設備通常使用傾斜的輸送帶,傾斜的輸送帶需要佔用較大的場地,且生產成本高,輸送速度慢,當輸送帶的速度過快或者傾角過大時,小的金屬零部件容易從輸送帶上滾落,造成一定的安全隱患。因此,針對於需要輸送的金屬零部件的特點,設計一種專門用於金屬零部件的上料結構。
技術實現要素:
針對於上述現有技術存在的缺陷,本實用新型的目的在於提出一種結構簡單、佔用空間小、操作簡便、運輸效率高且安全性更好的新型輸送帶式自動上料結構。
本實用新型為了實現上述目的,採用的技術解決方案是:
一種新型輸送帶式自動上料結構,包括工作檯、主動輥、從動輥、輸送帶、料鬥及卸料溜槽,所述主動輥和從動輥均位於工作檯的同一側,且呈一上一下布置。所述主動輥的轉軸與設置在工作檯上的電機相連,從動軸的轉軸的一端與工作檯相連。輸送帶的上部與主動輥相連,其下部與從動軸相連,所述主動輥通過輸送帶驅動從動軸轉動。所述料鬥位於輸送帶後側部分的下部,輸送帶由料鬥的底部穿入且由其頂部穿出,所述料鬥通過託架與工作檯固定相連。所述卸料溜槽位於輸送帶前側部分的上部,卸料溜槽通過支架與工作檯固定相連。
優選地,所述料鬥為頂部敞口的箱體結構,其由左壁板、右壁板、後壁板、斜底板及底板連接構成,底板的前部具有與輸送帶相適配的長圓孔。所述左壁板前端的內壁上豎向設置有左立柱,右壁板前端的內壁上豎向設置有右立柱。左立柱和右立柱相對的一側,均開有豎向的導向槽,兩個導向槽正向相對,且與輸送帶相配合。
優選地,所述料鬥的後部由下往上依次等間距橫向設置有多個後限位輥,所有後限位輥兩端分別左立柱和右立柱位於導向槽前側的部分轉動連接。料鬥後部的兩側分別設置一組前限位輥,每組前限位輥包括由下往上依次等間距橫向設置的若干根前限位輥組成。位於料鬥左側的一組前限位輥的左端與左立柱位於導向槽後側的部分轉動連接,位於料鬥右側的一組前限位輥的右端與右立柱位於導向槽後側的部分轉動連接。
優選地,所述輸送帶的外側表面上,沿其中心線依次等間距設置有若干個吸附件,所有吸附件均位於兩組前限位輥之間。
優選地,所述吸附件為橫向設置的長條狀的第一磁鐵。
優選地,所述吸附件為圓盤狀的第二磁鐵。
優選地,所述卸料溜槽包括導料斜板,導料斜板的左右兩側均向上折彎形成卸料溜槽的左擋板和右擋板,導料斜板呈後端向上的傾斜狀,其後端靠近輸送帶。所述導料斜板後端的中部,開有與吸附件相適配缺口。
通過採用上述技術方案,本實用新型的有益技術效果是:本實用新型結構簡單合理,製造成本低,實用性強,自動化程度高,安全性能高,可實現對金屬部件的高效率上料。所述料鬥能夠對輸送帶起到保護作用,避免輸送帶在工作狀態下擺動幅度過大影響輸送效果,同時提高輸送帶的使用壽命。本實用新型佔地空間小,對金屬零部件的上料高度不受場地大小的限制,可將上料後的金屬零部件等間距擺放至下一生產環節的輸送帶上。
附圖說明
圖1是本實用新型一種新型輸送帶式自動上料結構的一種實施方式的結構示意圖。
圖2是本實用新型一種新型輸送帶式自動上料結構的另一種實施方式的結構示意圖。
圖3是圖1中本實用新型某一部分的立體結構原理示意圖,示出的是料鬥。
圖4是圖1中示出的料鬥的俯視結構原理示意圖。
圖5是圖2中示出的料鬥的俯視結構原理示意圖。
具體實施方式
下面結合附圖對本實用新型進行詳細說明:
實施例1,結合圖1、圖3和圖4,一種新型輸送帶式自動上料結構,包括工作檯1、主動輥2、從動輥3、輸送帶4、料鬥5及卸料溜槽6,所述主動輥2和從動輥3均橫向設置在工作檯1的左側,且呈一上一下布置,所述主動輥2位於從動輥3的正上方,兩者相互平行。所述主動輥2的轉軸的右端與設置在工作檯1上的電機7的動力輸出端固定相連,從動軸3的轉軸的右端與設置在工作檯1上的軸承轉動相連。輸送帶4的上部與主動輥2相連,其下部與從動軸3相連,電機7驅動主動輥2轉動,主動輥2通過輸送帶4驅動從動輥3轉動。在工作狀態下,輸送帶4位於後側的部分由下往上運動,輸送帶4位於前側的部分由上往下運動。
所述料鬥5為頂部敞口的箱體結構,其由左壁板51、右壁板52、後壁板53、斜底板54及底板55連接構成,所述左壁板51和右壁板52的後端分別與後壁板53的左、右兩側邊固定焊接在一起,斜底板54位於左壁板51和右壁板52下方的後側,斜底板54的兩側邊分別與左壁板51和右壁板52下端的後部固定相連,且前部向下的傾斜狀,斜底板54的後側邊與後壁板53的下端固定焊接在一起。所述底板55水平布置在斜底板54的前側,其左、右兩側邊分別與左壁板51和右壁板52的下端固定焊接,底板55的後側邊緣與斜底板54的前側邊緣固定焊接在一起,所述底板55的前部具有與輸送帶4相適配的長圓孔56。在使用狀態下,輸送帶4豎向位於料鬥5的前側,可作為料鬥5的前壁板,使料鬥5形成頂部敞口的箱體結構,小的金屬零部件放置於料鬥5內。
所述料鬥5位於輸送帶4後側部分的下部,輸送帶4由料鬥5的底板55的前部的長圓孔穿入,並且由料鬥5頂部的敞口穿出,所述料鬥5的底板55外側焊接有託架11,託架11的右端與工作檯1的左側壁固定相連。所述左壁板51前端的內壁上豎向設置有左立柱8,右壁板52前端的內壁上豎向設置有右立柱9,左立柱8的右側壁上與右立柱9的左側壁上,均開有豎向的導向槽10,分別位於左立柱8和右立柱9上的導向槽10正向相對,輸送帶4的左側邊和右側邊分別位於左立柱8和右立柱9上的導向槽10內。
所述料鬥5的後部由下往上依次等間距橫向布置有多個後限位輥13,所有後限位輥13的軸線均相互平行,它們的左端與左立柱8位於導向槽10前側的部分轉動連接,右端與右立柱9位於導向槽10前側的部分轉動連接,所有後限位輥13的表面與輸送帶4的內側表面靠在一起。料鬥5後部的兩側分別設置一組前限位輥,每組前限位輥包括由下往上依次等間距橫向設置的若干根前限位輥14組成,位於兩組前限位輥的每根前限位輥14均正向相對布置,且兩組前限位輥之間具有間隔。位於料鬥5左側的一組前限位輥的左端與左立柱8位於導向槽10後側的部分轉動連接,位於料鬥5右側的一組前限位輥的右端與右立柱9位於導向槽10後側的部分轉動連接,所有前限位輥14的表面均與輸送帶4的外側表面靠在一起。
所述輸送帶4的外側表面上,沿其中心線依次等間距固定安裝有若干個吸附件,所述吸附件為長條狀的第一磁鐵15,所有第一磁鐵15均橫向布置在兩組前限位輥之間,第一磁鐵15的左右兩側分別與前限位輥14的末端之間具有間隙,避免第一磁鐵15隨輸送帶4運動時與前限位輥14接觸受損。所述底板55位於長圓孔56的後側部分的中部具有與第一磁鐵15的缺口,以保證安裝於輸送帶4的外側表面上的第一磁鐵15能夠順利通過底板55。每個第一磁鐵15的吸附力均大於兩個金屬零件的重量,以保證每個第一磁鐵15至少吸起兩個金屬零件,且輸送過程中貼緊在第一磁鐵15的表面。
所述卸料溜槽6位於輸送帶4前側部分的上部,卸料溜槽6的底部通過支架與工作檯1的左側固定相連。所述卸料溜槽6包括導料斜板61,導料斜板61的左右兩側均向上折彎形成卸料溜槽6的左擋板和右擋板,導料斜板61呈前低後高的傾斜狀,其後端靠近輸送帶。所述導料斜板61後端的中部,開有與第一磁鐵15相適配缺口,保證安裝於輸送帶4的外側表面上的第一磁鐵15能夠順利通過導料斜板61向下運動,吸附在第一磁鐵15外側的金屬零件被導料斜板61阻擋,與第一磁鐵15分離後沿導料斜板61的上表面向前滑落,進入下一個輸送機構或加工工位。
實施例2,結合圖2和圖5,一種新型輸送帶式自動上料結構,包括工作檯1、主動輥2、從動輥3、輸送帶4、料鬥5及卸料溜槽6,所述主動輥2和從動輥3均橫向設置在工作檯1的左側,且呈一上一下布置,所述主動輥2位於從動輥3的正上方,兩者相互平行。所述主動輥2的轉軸的右端與設置在工作檯1上的電機7的動力輸出端固定相連,從動軸3的轉軸的右端與設置在工作檯1上的軸承轉動相連。輸送帶4的上部與主動輥2相連,其下部與從動軸3相連,電機7驅動主動輥2轉動,主動輥2通過輸送帶4驅動從動輥3轉動。在工作狀態下,輸送帶4位於後側的部分由下往上運動,輸送帶4位於前側的部分由上往下運動。
所述料鬥5為頂部敞口的箱體結構,其由左壁板51、右壁板52、後壁板53、斜底板54及底板55連接構成,所述左壁板51和右壁板52的後端分別與後壁板53的左、右兩側邊固定焊接在一起,斜底板54位於左壁板51和右壁板52下方的後側,斜底板54的兩側邊分別與左壁板51和右壁板52下端的後部固定相連,且前部向下的傾斜狀,斜底板54的後側邊與後壁板53的下端固定焊接在一起。所述底板55水平布置在斜底板54的前側,其左、右兩側邊分別與左壁板51和右壁板52的下端固定焊接,底板55的後側邊緣與斜底板54的前側邊緣固定焊接在一起,所述底板55的前部具有與輸送帶4相適配的長圓孔56。在使用狀態下,輸送帶4豎向位於料鬥5的前側,可作為料鬥5的前壁板,使料鬥5形成頂部敞口的箱體結構,小的金屬零部件放置於料鬥5內。
所述料鬥5位於輸送帶4後側部分的下部,輸送帶4由料鬥5的底板55的前部的長圓孔穿入,並且由料鬥5頂部的敞口穿出,所述料鬥5的底板55外側焊接有託架11,託架11的右端與工作檯1的左側壁固定相連。所述左壁板51前端的內壁上豎向設置有左立柱8,右壁板52前端的內壁上豎向設置有右立柱9,左立柱8的右側壁上與右立柱9的左側壁上,均開有豎向的導向槽10,分別位於左立柱8和右立柱9上的導向槽10正向相對,輸送帶4的左側邊和右側邊分別位於左立柱8和右立柱9上的導向槽10內。
所述料鬥5的後部由下往上依次等間距橫向布置有多個後限位輥13,所有後限位輥13的軸線均相互平行,它們的左端與左立柱8位於導向槽10前側的部分轉動連接,右端與右立柱9位於導向槽10前側的部分轉動連接,所有後限位輥13的表面與輸送帶4的內側表面靠在一起。料鬥5後部的兩側分別設置一組前限位輥,每組前限位輥包括由下往上依次等間距橫向設置的若干根前限位輥14組成,位於兩組前限位輥的每根前限位輥14均正向相對布置,且兩組前限位輥之間具有間隔。位於料鬥5左側的一組前限位輥的左端與左立柱8位於導向槽10後側的部分轉動連接,位於料鬥5右側的一組前限位輥的右端與右立柱9位於導向槽10後側的部分轉動連接,所有前限位輥14的表面均與輸送帶4的外側表面靠在一起。
所述輸送帶4的外側表面上,沿其中心線依次等間距固定安裝有若干圓盤狀的第二磁鐵16,所有第二磁鐵6均布置在兩組前限位輥之間,第二磁鐵16的左右兩側分別與前限位輥14的末端之間具有間隙,避免第二磁鐵16隨輸送帶4運動時與前限位輥14接觸受損。所述底板55位於長圓孔56的後側部分的中部具有與第二磁鐵16的缺口,以保證安裝於輸送帶4的外側表面上的第二磁鐵16能夠順利通過底板55。每個第二磁鐵16的吸附力均大於一個金屬零件的重量,且小於兩個金屬零件的重量,以保證每個第二磁鐵16僅吸附一個金屬零件,且輸送過程中貼緊在第一磁鐵15的表面。
所述卸料溜槽6位於輸送帶4前側部分的上部,卸料溜槽6的底部通過支架與工作檯1的左側固定相連。所述卸料溜槽6包括導料斜板61,導料斜板61的左右兩側均向上折彎形成卸料溜槽6的左擋板和右擋板,導料斜板61呈前低後高的傾斜狀,其後端靠近輸送帶。所述導料斜板61後端的中部,開有與第二磁鐵16相適配缺口,保證安裝於輸送帶4的外側表面上的第二磁鐵16能夠順利通過導料斜板61向下運動,吸附在第二磁鐵16外側的金屬零件被導料斜板61阻擋,與第二磁鐵16分離後沿導料斜板61的上表面向前滑落。由於每個第二磁鐵16吸附一個金屬零件,金屬零件與第二磁鐵16分離後會間隔相等時間從卸料溜槽6滑落,如果卸料溜槽6的下方設置水平輸送帶,金屬零件從卸料溜槽6滑落後將等間距排列在水平輸送帶上,向下一個工位進行輸送。
當然,上述說明並非是對本實用新型的限制,本實用新型也並不僅限於上述舉例,本技術領域的技術人員在本實用新型的實質範圍內所做出的變化、改型、添加或替換,也應屬於本實用新型的保護範圍。