印刷電路板樹脂塞孔加工構件的製作方法
2023-12-01 23:53:36 1
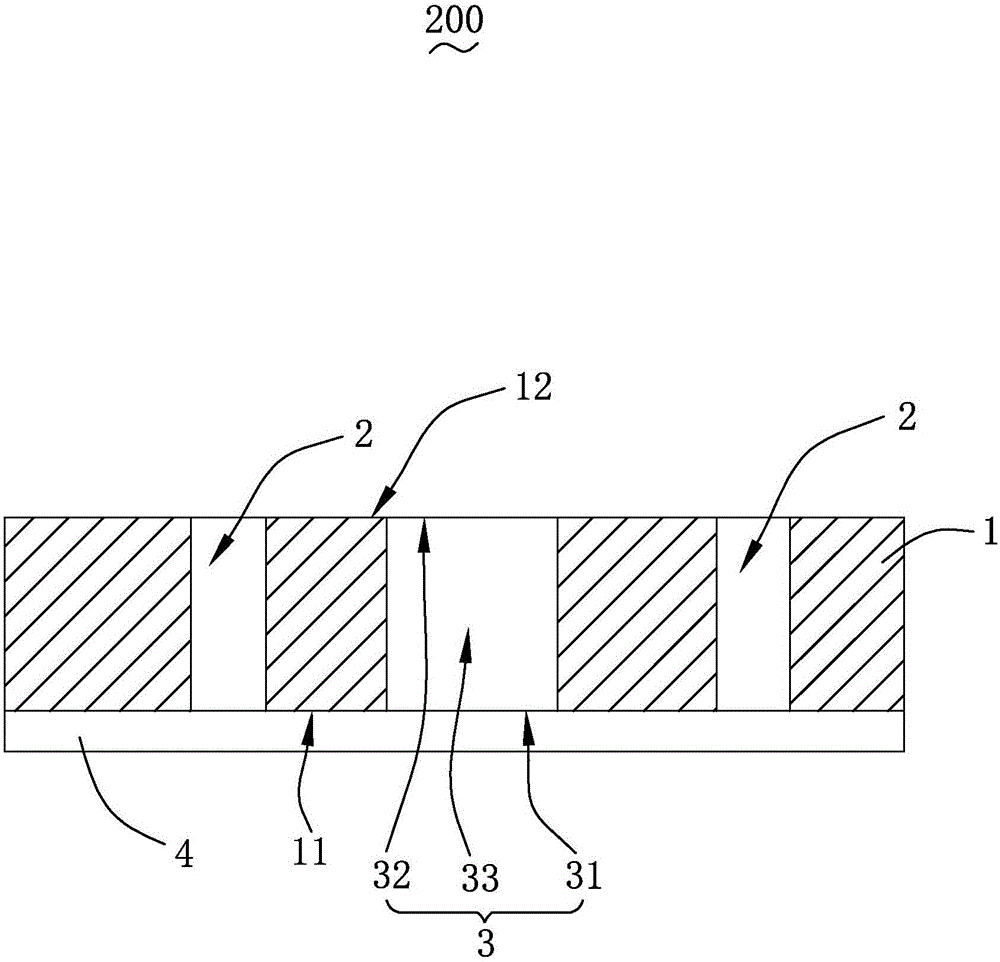
本實用新型涉及印刷電路板製作技術領域,尤其涉及到一種印刷電路板樹脂塞孔加工構件。
背景技術:
隨著電子產品越來越微小型化、多功能化、高集成化的發展,要求PCB板件具有更高的布線密度。為了保證信號的互連和防止銅基短路的產生,必須在相應導電孔之間的位置開通槽以絕緣。但為了保證銅基板表面的平整性,通槽必須採用樹脂塞孔填平,使保持良好的平整度。
相關技術中,由於銅基板的內槽尺寸相對較大,採用傳統的樹脂塞孔法,一方面會因樹脂的稀釋和重力原因,使通槽無法塞住;另一方面,易導致樹脂下垂,使得銅基板表面的樹脂凹陷,無法滿足表面的平整度的要求。
因此,有必要提供一種新的印刷電路板樹脂塞孔加工構件解決上述問題。
技術實現要素:
本實用新型需要解決的技術問題是提供一種可實現大尺寸槽孔的樹脂塞孔製作的印刷電路板樹脂塞孔加工構件。
為解決上述技術問題,本實用新型提供一種印刷電路板樹脂塞孔加工構件,包括設有多個導電孔的銅基板,所述銅基板包括內表面和與所述內表面相對設置的外表面,所述導電孔之間設有貫穿所述銅基板並用於物理隔離相鄰兩所述導電孔的通槽,所述通槽包括位於所述內表面的第一開口、位於所述外表面的第二開口以及連通所述第一開口和所述第二開口並用於填充樹脂的填充部,所述內表面貼設有高溫膜且所述高溫膜覆蓋所述第一開口,所述第二開口用於向所述填充部注入樹脂。
優選的,所述導電孔為圓形孔或方形孔。
優選的,所述導電孔排列方式包括並排、平行或者參錯設置。
優選的,所述樹脂為環氧樹脂。
優選的,所述高溫膜的厚度為30-50μm。
與相關技術相比,本實用新型的印刷電路板樹脂塞孔加工構件通過在所述銅基板的單面貼設所述高溫膜作保護,再從所述銅基板的另外一面進行向所述通槽內注入樹脂塞孔,使所述高溫膜阻擋樹脂油墨的下垂,從而樹脂固化後的表面平整度好,可實現大尺寸槽孔的樹脂塞孔製作。
附圖說明
圖1為本實用新型印刷電路板樹脂塞孔加工構件的結構示意圖。
具體實施方式
下面將結合附圖和實施方式對本實用新型作進一步說明。
請參照圖1,為本實用新型印刷電路板樹脂塞孔加工構件的結構示意圖。所述印刷電路板樹脂塞孔加工構件200包括銅基板1和貫穿所述銅基板1的多個導電孔2以及設於所述導電孔2之間的通槽3。
所述銅基板1包括內表面11和與所述內表面相對設置的外表面12。
所述通槽3貫穿所述銅基板1並用於物理隔離絕緣相鄰兩所述導電孔2。所述通槽3包括位於所述內表面11的第一開口31、位於所述外表面12的第二開口32以及連通所述第一開口31和所述第二開口32用於填充樹脂的填充部32。所述內表面11貼設有高溫膜4且所述高溫膜4覆蓋所述第一開口31,所述通槽3的所述第二開口32用於向所述填充部32注入樹脂,其中,該樹脂為環氧樹脂。
具體的,通過貼膜機在銅基板1的所述內表面11貼所述高溫膜4,再從所述通槽3的所述第二開口32注入樹脂,待樹脂固化後,並將表面的樹脂磨平,使實現所述通槽3內的樹脂填平。所述高溫膜4厚度為30-50μm。相比於傳統的樹脂塞孔法,通過在所述銅基板1的單面貼所述高溫膜4作保護,再從所述銅基板1的另外一面進行樹脂塞孔,因有所述高溫膜4的阻擋作用,可以防止樹脂下垂,固化後達到表面平整效果。
本實施方式中,所述導電孔2為圓形孔或方形孔。所述導電孔2排列方式包括並排、平行或者參錯設置。
與相關技術相比,本實用新型的印刷電路板樹脂塞孔加工構件通過在所述銅基板的單面貼設所述高溫膜作保護,再從所述銅基板的另外一面進行向所述通槽內注入樹脂塞孔,使所述高溫膜阻擋樹脂油墨的下垂,從而樹脂固化後的表面平整度好,可實現大尺寸槽孔的樹脂塞孔製作。
以上所述僅為本實用新型的實施例,並非因此限制本實用新型的專利範圍,凡是利用本實用新型說明書及附圖內容所作的等效結構或等效流程變換,或直接或間接運用在其它相關的技術領域,均同理包括在本實用新型的專利保護範圍內。