一種鍛造風機主軸用的成型裝置的製作方法
2023-06-25 05:19:36 1
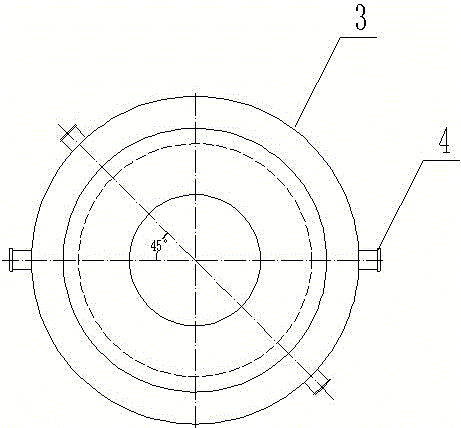
本實用新型屬於鍛造技術領域,主要涉及一種鍛造風機主軸用的成型裝置。
背景技術:
目前國內大多數油壓機鍛造風機軸時,法蘭的成型主要是用模具局部鐓粗擠壓成型,成型之後再在上下平砧上滾圓精整成型,因為法蘭的厚度和直徑之比一般在0.1~0.2之間,滾圓精整過程中必然會導致法蘭發生扭曲,從而滾圓之後仍然需要將風機軸倒立在平臺上進行校直法蘭和軸身臺階,這種生產風機軸的缺點是鍛造火次多,鍛造效率低,影響產品的生產周期,不利於市場競爭和企業的節能降耗。
技術實現要素:
本實用新型的目的在於克服上述現有技術中的不足提供一種控制精度高,不需要滾圓成型法蘭和立料校直的快速成型裝置。
本實用新型的技術方案是這樣實現的:一種鍛造風機主軸用的成型裝置,該裝置主要包括上模口和下支撐,所述上模口與所述下支撐是分開的兩部分,所述下支撐頂部設有錐形凹槽,所述上模口放置在所述下支撐的錐形凹槽中, 所述上模口與所述下支撐均開設有通孔且兩者中心線重合,所述上模口上部內壁設有一個型腔,所述下支撐下部內壁設有一個帶錐度的導向面,所述型腔的中心線、所述導向面的中心線與所述上模口的中心線重合。
所述下支撐頂部的錐形凹槽深度為50mm,斜面為15°。
所述上模口外壁兩側設置有兩組上模口吊耳,每組上模口吊耳之間的夾角為45°。
所述上模口軸身內壁與所述型腔底面設置有R200的倒角且兩者之間圓滑過渡。
所述型腔內壁與垂直方向設有一個2°的脫模夾角。
所述下支撐外壁上端的兩側設置有兩組下支撐吊耳,每組下支撐吊耳之間的夾角為45°。
所述下支撐上端面外徑大於所述上模口下端面外徑。
所述下支撐上端面內徑大於所述上模口下端面內徑。
在距離所述下支撐底面100mm的位置,所述下支撐外表面上沿圓周方向開設有四個100×100mm的觀察孔,所述觀察孔貫穿所述下支撐的內壁。
本實用新型的技術方案產生的積極效果如下:T形坯料的小端接觸到導向面,然後採用上平砧將T形坯料局部鐓粗碾壓至充滿整個型腔,法蘭在型腔中成型,此時法蘭外圓非常規則,節省了傳統方法鍛造風機軸的法蘭滾圓工序,在此過程中T形坯料受到壓應力作用,金屬必然向下流動,產生拉料,此時向下流動的金屬沿著所述導向面運動,導向面起到校直作用,節省了傳統方法鍛造風機軸的立料校直工序,採用本實用新型鍛造的風機軸外觀尺寸控制精度高,鍛坯機加餘量小,鍛坯重量較輕,鋼錠利用率高,從而提高了鍛造效率,節約成本,本實用新型結構簡單,製作方便,吊裝便捷,鍛造效率高且安全可靠。
附圖說明
圖1為本實用新型鍛造風機主軸用的成型裝置的上模口的主視圖。
圖2為本實用新型鍛造風機主軸用的成型裝置的上模口的俯視圖。
圖3為本實用新型鍛造風機主軸用的成型裝置的下支撐的主視圖。
圖4為本實用新型鍛造風機主軸用的成型裝置的下支撐的俯視圖。
圖5為本實用新型鍛造風機主軸用的成型裝置鍛造法蘭和校直過程成型示意圖。
圖中標註為:1、油壓機上平砧;2、T形坯料;3、上模口;4、吊耳;5、下支撐,6、導向面;7、觀察孔;8、型腔。
具體實施方式
一種鍛造風機主軸用的成型裝置,如圖1到5所示,在油壓機上先做好鍛造風機軸所需要的T形坯料2,先將T形坯料放置在所述上模口3中,大端放在上模口的型腔8中,再用鏈條掛住上模口的吊耳4,天車吊起鏈條,最後將T形坯料和所述上模口一起吊運至下支撐5上開始裝卡,上模口和下支撐裝卡成功後,此時T形坯料的小端剛好接觸到導向面6,然後採用油壓機上平砧1將T形坯料局部鐓粗碾壓至充滿整個型腔,在此過程中T形坯料受到壓應力作用,金屬必然向下流動,產生拉料,此時向下流動的金屬沿著所述導向面運動,導向面起到校直作用,防止在局部鐓粗碾壓過程中T形坯料在下支撐中擺動,產生彎曲。在距離所述下支撐底面100mm的位置,所述下支撐外表面上沿圓周方向開設有四個100×100mm的觀察孔7,所述觀察孔貫穿所述下支撐的內壁。當金屬完全充滿整個上模口型腔時,天車吊起鏈條,將上模口和法蘭成型後的坯料一起吊走,取出坯料,因為法蘭在型腔中成型,此時法蘭外圓非常規則,不需要再用傳統的鍛造方式在上下平砧上滾圓、修整,同時軸身受到導向面的作用,軸身和法蘭面互相垂直,不需要校直,最後將風機軸軸身其餘臺階在上下砧上成型,從而可以提高鍛造效率,節約成本。
此過程操作簡單,取料方便,避免傳統的法蘭滾圓修整和立料校直工序。