一種用於矽芯拉制的吹氣裝置的製作方法
2023-06-15 02:19:21 3
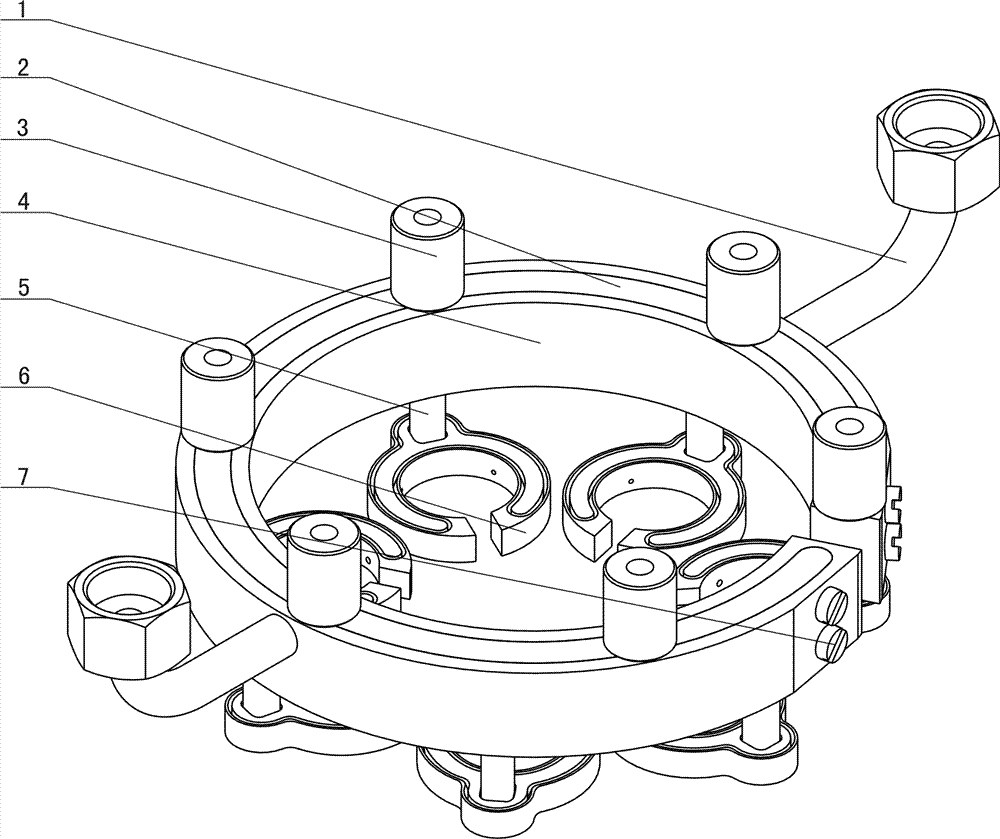
本實用新型涉及人工晶體領域,具體涉及一種用於矽芯拉制時提高矽芯結晶速度的吹氣裝置。
背景技術:
在現有技術的矽芯拉制過程中,一般使用籽晶進行引晶。待引晶完成後再進行矽芯的拉制。在此過程中,籽晶需要藉助籽晶夾頭夾持。待高頻線圈將原料棒的端頭局部融化成液體後,籽晶夾頭帶動籽晶下降,穿過高頻線圈的拉制孔後插入原料棒上端的溶液內。隨後通過籽晶夾頭帶動籽晶上升,籽晶帶動溶液上升並重新結晶,最終形成所需長度的矽芯。
在籽晶帶著融液上升的過程中,當融液離開高頻線圈的拉制孔後會逐漸冷卻並重新結晶。此時帶動籽晶上升的上軸的提升速度較慢,拉制直徑為¢8mm的矽芯時,上軸的提升速度為14mm/min,拉制直徑為¢10mm的矽芯時,上軸的提升速度為12mm/min,拉制矽芯的直徑一般都在¢8~¢10mm之間。所拉制的矽芯直徑越大,其後期在還原爐內的生長速度越快,生產效率越高,所以如何提高矽芯的生產效率和增大矽芯的直徑就成了本領域的技術訴求之一。
針對上述技術問題,申請人提出過「一種拉制矽芯時提高矽芯結晶速度的裝置」的專利申請(專利申請號為201410175547.5、申請日為2014年04月21日、公開號為CN105002556A)。該申請藉助於一吹氣裝置(具體結構詳見附圖1),有效的提高了矽芯的結晶速度,該申請在本申請中被用作參考。
上述專利申請雖然解決了矽芯結晶速度慢的問題,但在拉制矽芯的過程中由於連續吹氣的不穩定性,會導致新拉制的矽芯結晶速度不一致,影響晶體質量。
技術實現要素:
經研究,申請人認為導致新拉制的矽芯結晶速度不一致的主要原因是吹氣裝置吹向矽芯的氣流分布不均勻,從而造成矽芯結晶速度的差異。
本實用新型提供了一種用於矽芯拉制時提高矽芯結晶速度的吹氣裝置,通過改進吹氣裝置的結構,使最終吹向矽芯的氣體更加均勻和穩定,從而解決了新拉制的矽芯結晶速度均勻性的問題。
本實用新型的原理包括兩個方面:一是在矽芯的冷卻過程中,沿不同方向對每根矽芯進行吹氣,使矽芯的冷卻更加均勻化;二是採用多級進氣管的方式對進入吹氣裝置的氣體進行多次緩衝再分配,以實現氣體分布和流動的均勻化。
為實現上述發明目的,本實用新型採用如下技術方案:
環繞每一根矽芯設置一個吹氣嘴,吹氣嘴上開設多個吹氣孔,使從吹氣孔吹出的氣體沿多個方向均勻吹向矽芯。
為了穩定氣流,可以在吹氣嘴的上遊設置一個或多個環形進氣通道,通過連接管將吹氣嘴與環形進氣通道相連通,環形進氣通道之間通過多個進氣孔相互連通,使進入吹氣裝置的氣流在進氣通道及吹氣環內多次分布,實現吹出氣流的均勻化。
在一優選實施例中,所述的進氣通道可以為多個平行疊置的環形通道,冷卻氣體經進氣管進入吹氣裝置之後,經第一進氣通道進入第二進氣通道,再經連接管進入第三進氣通道,最終經吹氣孔吹向矽芯。
其中,第一進氣通道和第二進氣通道均設置在同一吹氣環內,第一進氣通道設置在該吹氣環的上方,第二進氣通道設置在該吹氣環的下方,第一進氣通道和第二進氣通道由多個進氣孔相互連通。
吹氣嘴設置在所述吹氣環的下方,第三進氣通道位於該吹氣嘴內部,通過連接管將第二進氣通道與相第三進氣通道連通,吹氣孔設置在吹氣嘴上,均勻環繞在矽芯周圍,對準矽芯的結晶區。
為了便於維修,在吹氣環環形的開口A與第一進氣通道及第二進氣通道端部相對應的位置設有排汙口,在排汙口處設有封堵螺釘。
所述吹氣環上還可以設有若干個固定柱,用於安裝導心板。
由於採用如上所述的技術方案,本實用新型具有如下有益效果:
採用本實用新型的技術方案,解決了現有技術中矽芯冷卻不均勻的問題。矽芯的快速均勻冷卻可以提高晶體的拉制速度、增加所拉制的矽芯的直徑,而矽芯直徑的加大,又使其後期在還原爐內的生長速度加快,由此提高了生產效率。
【附圖說明】
圖1是上述現有技術中的吹氣裝置;
圖2是本實用新型一優選實施例的立體結構示意圖;
圖3是圖2實施例另一方向的示意圖;
圖4是是圖2實施例的俯視結構示意圖;
圖5是圖4結構中A-A剖視結構示意圖;
圖6是圖4結構中B-B剖視結構示意圖;
圖7是圖4結構中C-C剖視結構示意圖。
附圖2-7中的標號與部件之間的對應關係為:
1、進氣管;2、蓋板A;3、固定柱;4、吹氣環;5、連接管;6、吹氣嘴;7、封堵螺釘;8、開口A;9、蓋板B;10、開口B;11、吹氣孔;12、蓋板C;13、第一進氣通道;14、第二進氣通道;15、進氣孔;16、第三進氣通道。
【具體實施方式】
如上所述,本實用新型的主要構思是採用多級進氣的方式對氣體進行緩衝分散,以實現氣體的均勻化;同時沿不同方向對每根矽芯進行吹氣,使矽芯的冷卻更加均勻化。
以下結合一優選實施例對本實用新型做進一步詳細的說明。
圖1是「一種拉制矽芯時提高矽芯結晶速度的裝置」的專利申請中所公開的吹氣裝置示意圖。該吹氣裝置包括進氣管、吹氣環和吹氣孔,氣流通過吹氣環經吹氣孔直接吹向矽芯。
附圖2-7詳細描述了本實用新型吹氣裝置的一個優選實施例。
如圖2所示,本實用新型的吹氣裝置包括進氣管1、吹氣環4、連接管5和吹氣嘴6。
如圖5所示,在所述吹氣環4的上方設有第一進氣通道13,在吹氣環4的下方設有第二進氣通道14。所述第一進氣通道13與第二進氣通道14通過進氣孔15相連通。
進氣管1設置在吹氣環4的外緣面上,所述進氣管1的一端連通爐室內部的進氣管道,另一端連通第一進氣通道13。
在吹氣環4的下方設有若干個吹氣嘴6,所述吹氣嘴6通過連接管5連通第二進氣通道14。所述吹氣嘴6的數量、位置與高頻線圈上設置的拉制孔的數量和位置一致,吹氣嘴6上的吹氣孔11對準矽芯的結晶區。
如圖3所示,所述吹氣嘴6為環形開口結構,即設有開口B10。吹氣嘴6上設有第三進氣通道16,與設置在吹氣嘴6內緣面上的吹氣孔11相連通。
在吹氣環4上也設有開口A8。在該開口處,第一進氣通道13及第二進氣通道14兩端相對應的位置上分別設有排汙口,在排汙口處設有封堵螺釘7。
如圖2所示,所述吹氣環4的上面設有若干個固定柱3,該固定柱3可以用於安裝導心板(導心板已另行申報專利)。
如圖5所示,第一進氣通道13為設置在吹氣環4的上方、向下凹陷的上凹槽,在該上凹槽的開口端設有蓋板A2,上凹槽與蓋板A2形成第一進氣通道13。第一進氣通道13為環形開口(C形)結構,其兩端頭分別設有排汙口。
第二進氣通道14為設置在吹氣環4的下方、向上凹陷的下凹槽,在該下凹槽的開口端設有蓋板B9,下凹槽與蓋板B9形成第二進氣通道14。第二進氣通道14為環形開口(C形)結構,其兩端頭分別設有排汙口。
如圖6所示,為了使第二進氣通道14與第一進氣通道13連通,在下凹槽的底部設有若干個進氣孔15。
如圖5所示,工作時,氣體首先由進氣管1進入第一進氣通道13,並經由進氣孔15進入第二進氣通道14。經進氣孔15的分散作用,第二進氣通道14內氣體相對於第一進氣通道13內的氣體更為均勻。
如圖5-7所示,吹氣嘴6也設置為C形結構,在吹氣嘴6上方設有向下凹陷的凹槽,在所述凹槽的開口端設有蓋板C12,兩者構成第三進氣通道16,第三進氣通道16通過連接管5連接第二進氣通道14。在吹氣嘴6的內緣面上設有若干個吹氣孔11,吹氣孔11與第三進氣通道16相連通,與矽芯的結晶區相對應。
吹氣環4內的氣體可以選擇氦氣、氖氣、氬氣、氪氣、氙氣或氡氣中的任意一種。
該實施例中,用於冷卻矽芯的氣體,經進氣管1進入吹氣裝置之後,經過第一進氣通道13進入第二進氣通道14,然後經進氣孔15再進入第三進氣通道16,最終通過吹氣孔11吹向矽芯。吹向矽芯的氣體更加均勻、穩定,從而確保了矽芯結晶的均勻化。
以使用矽芯爐拉制矽芯為例,待爐體內的原料棒上端頭融化後,通過控制系統將由籽晶夾頭帶動的籽晶緩緩穿過高頻線圈上的拉制孔,並插入到原料棒上端頭的融液內,待籽晶的端頭與原料棒上端頭的融液融為一體後,通過控制系統控制將由籽晶夾頭帶動的籽晶緩慢提升,當融液離開高頻線圈上的拉制孔後逐漸開始結晶並形成所需的矽芯。此時通過控制系統開啟進氣閥門,氬氣通過進氣管1進入吹氣環4上的第一進氣通道13內,然後通過進氣孔15分散進入到第二進氣通道14。第二進氣通道14內的氣體通過連接管5進入到第三進氣通道16內,再通過吹氣孔11將氣體吹到矽芯的結晶區,實現對結晶區的快速冷卻。
以拉制直徑為10mm的矽芯為例,採用本實用新型的吹氣裝置後,上軸的提升速度「即矽芯的拉制速度」為14mm/min;拉制直徑為14mm的矽芯,上軸的提升速度為10mm/min。由此大大提高了晶體的拉制速度。由於矽芯的結晶速度加快,也加大了矽芯的可拉制直徑。