一種錳氧化物氣基還原製備碳化錳的方法與流程
2023-06-18 05:28:47 1
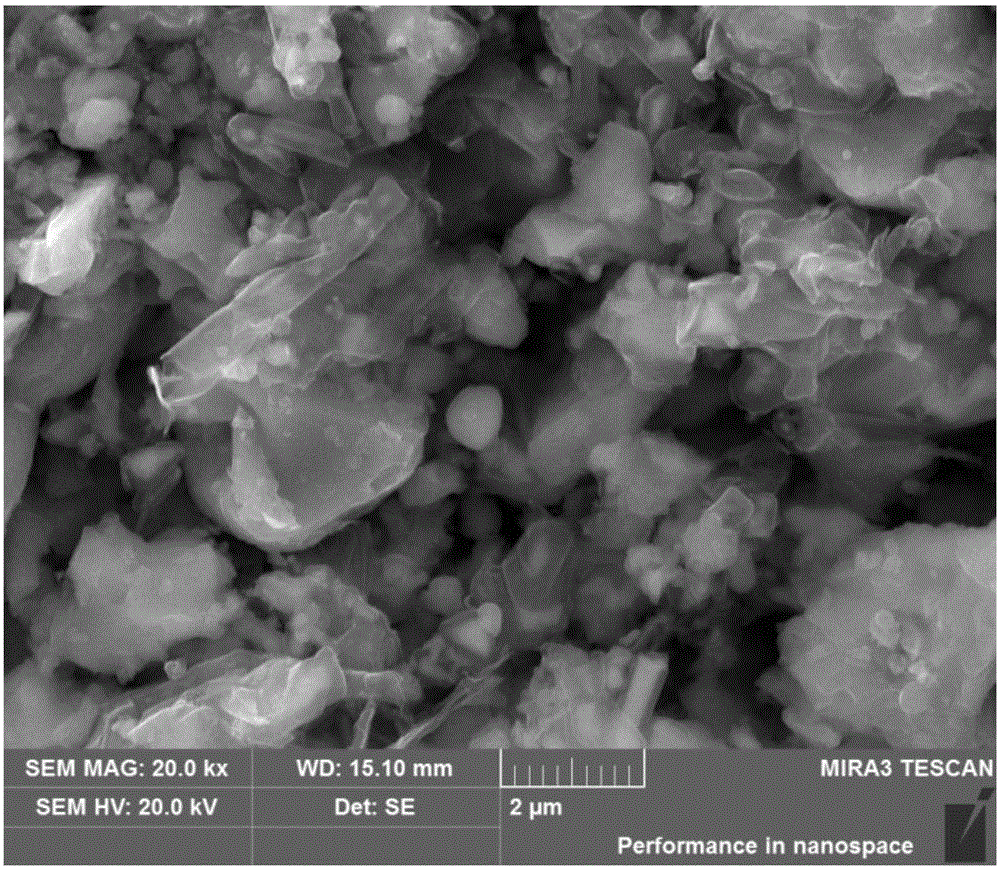
本發明涉及一種錳氧化物氣基還原製備碳化錳的方法,特別涉及一種錳氧化物氣基固態還原製備碳化錳的方法,屬於功能材料前驅體製備領域。
背景技術:
四氧化三錳是電子工業生產錳鋅鐵氧體軟磁材料的重要原料之一,應用非常廣泛。據報導,碳化錳水解法是四氧化三錳微粉的製備方法之一。一種用碳錳合金生產四氧化三錳的方法(申請號200810203968.9)、用碳錳合金一步法生產低硒和高比表面積四氧化三錳的方法(申請號:200910044828.6)、碳化錳水解氧化法製備Mn3O4納米粉(中國錳業,2010年,第28卷第1期,17-20頁)公開了利用碳化錳(過渡金屬碳化物)水解氧化法製備Mn3O4微粉的方法,由於不涉及催化劑、酸、鹼等化學試劑,與電解金屬錳粉懸浮液氧化法製備Mn3O4相比顯然是一種名符其實的綠色工藝。
然而,碳化錳的製備是碳化錳水解法製備Mn3O4材料的關鍵。此方法中,將質量比92%的電解金屬錳(純度高)和8%的石墨用50kg感應爐熔煉(溫度高達1500℃以上),將金屬錳和石墨置於石墨坩堝中,石墨破碎成細粒使它儘可能多的熔解在液相合金中,待爐料充分溶化後保溫一定時間,快速冷卻得到碳化錳合金塊。將合金塊碾碎成粉。然後將獲得的碳化錳粉末進行氧化水解反應,製備Mn3O4材料。
現有金屬錳和石墨熔煉製備碳化錳的技術存在以下問題,1)原料要求苛刻,以電解金屬錳為原料。由於電解金屬錳的製備工藝流程複雜,主要有碳酸錳礦和氧化錳礦經酸解、除雜、電解獲得。碳酸錳礦酸浸法可以直接利用硫酸與碳酸錳化合反應製取硫酸錳溶液,再通過中和、淨化、過濾等一系列工藝製備為電解液,經加入添加劑如二氧化硒、亞硫酸銨等即可進入電解槽進行電解;氧化錳礦還原-酸浸法生產電解錳的工藝與用碳酸錳生產工藝有所差別,主要是二氧化錳在一般條件下不與硫酸反應,必須經處理為二價錳後再與硫酸反應製備硫酸錳溶液,其處理方法一般為焙燒法,是將二氧化錳與還原性物質(一般為煤炭)共同混合後密閉加熱,在一定溫度下C將四價錳還原為二價錳,粉碎後再酸浸、除雜得電解液。2)熔煉溫度高,高達1300℃~1500℃。由Mn-C二元相圖分析可知,Mn-C體系的熔點高達1300℃以上,為使反應進行徹底,需保證很高的溫度,常採用感應爐熔煉。3)由於整個過程處於熔融狀態,對焙燒設備的材質和耐火材料要求高。
目前我國工業正在向環保節能的方向發展,因此開發一種低溫、經濟、清潔、高效製備碳化錳的新技術具有重要的現實意義。
技術實現要素:
針對現有金屬錳和石墨高溫熔煉法製備碳化錳技術的不足,本發明的目的是在於提供一種在低溫下通過氣基固態還原高效製備碳化錳的方法。
為了實現上述技術目的,本發明提供了一種錳氧化物氣基還原製備碳化錳的方法,將錳氧化物、粘結劑和水混勻後,造塊、乾燥,所得幹塊置於含H2、CH4、CO和N2的混合氣氛中,在1100~1300℃溫度下焙燒,即得碳化錳產品;
所述含H2、CH4、CO和N2的混合氣氛中H2、CH4和CO的總體積百分比濃度不低於50%,且H2與CH4的體積比為3~8;H2與CO的體積比為1~5。
本發明的技術方案關鍵在於控制合理的焙燒氣氛,將含H2、CH4、CO和N2的混合氣氛中的H2、CH4和CO等控制在適當的比例,各種氣體組分協同增效作用明顯。混合氣氛中的CH4的強還原能力,能夠實現在較低的溫度下使錳氧化物活化,轉化成錳碳化物;但是CH4在高溫狀態下不穩定,極易裂解為H2和C,從而降低了CH4的還原能力,通過合理調配氣相中H2和CO組分的配比,可以在較高溫度下抑制CH4的裂解,保證氣相中CH4的有效含量;同時,H2和CO也對錳氧化物等具有一定的活化作用,與CH4產生協同增效作用,降低反應溫度,縮短反應時間。
優選的方案,錳氧化物包括二氧化錳、三氧化二錳、四氧化三錳、氧化亞錳中的至少一種。
優選的方案,錳氧化物粒度滿足-325目粒級的質量百分比含量不低於90%。
優選的方案,焙燒溫度為1150~1250℃。
較優選的方案,焙燒時間30~120min;焙燒時間進一步優選為60~100min。
本發明的技術方案採用的粘結劑為常規的粘結劑,膨潤土、腐殖酸、CMC等,其主要起到粘結作用有利於錳氧化物造塊;而水是溶解分散粘結劑的介質,更有利於粘結劑發揮粘結作用;兩者的用量都為常規用量,屬於本領域技術人員可以理解的範圍。
優選的方案,焙燒產物置於保護氣氛中冷卻至室溫。所述的保護氣氛一般指氮氣或惰性氣體及它們的組合。如N2和/或Ar。
相對現有技術,本發明的技術方案帶來的有益技術效果:
1)本發明的技術方案通過在含H2、CH4、CO和N2的混合氣氛下還原錳氧化物,能夠大大活化錳氧化物,大大降低了還原焙燒溫度,相對傳統的金屬錳和石墨高溫熔煉法(熔煉溫度1500℃左右)降低200℃左右,大大降低了能耗,降低生產成本。
2)本發明的技術方案製備錳碳的工藝流程簡單,成本低;錳氧化物來源廣泛,與金屬錳和石墨高溫熔煉法相比,省去了現將二氧化錳還原-酸浸-電解為金屬錳的過程,顯著縮短了生產流程,使生產工藝簡化,節約成本。
3)本發明的技術方案製備錳碳的過程對設備的要求低,操作安全,反應是進行氣固反應,而金屬錳和石墨高溫熔煉法是在熔融狀態下進行,其對反應器和熔煉設備的材質要求較高。
4)本發明的技術方案製備錳碳晶相較純,滿足各種功能材料前驅體製備的要求。
附圖說明
【圖1】是實施例1所獲得的碳化錳的XRD圖譜。
【圖2】是實施例1所獲得的碳化錳顆粒的SEM圖片。
具體實施方式
以下實施例旨在進一步說明本發明內容,而不是限制本發明權利要求的保護範圍。
實施例1
將-325目粒級所佔質量百分含量均為90%分析純二氧化錳和四氧化三錳的混合物配加0.5%的CMC和7.5%的水分後造球,然後乾燥,將乾燥後的樣品於CH4體積百分數10%,H2體積百分數30%,CO體積百分數10%,N2體積百分數50%的氣氛中進行焙燒,焙燒溫度1150℃,焙燒時間為120min,然後在N2氣氛中冷卻至室溫,所得焙燒產物即為碳化錳產品,二氧化錳的轉化率為95%。該條件下獲得的碳化錳的XRD圖譜如圖1所示,碳化錳顆粒的SEM圖片如圖2所示。
實施例2
將-325目粒級所佔質量百分含量為92%純礦物二氧化錳配加0.5%的膨潤土和7.5%的水分後造球,然後乾燥,將乾燥後的樣品於CH4體積百分數8%,H2體積百分數62%,CO體積百分數20%,N2體積百分數10%的氣氛中進行焙燒,焙燒溫度1250℃,焙燒時間為30min,然後在N2氣氛中冷卻至室溫,所得焙燒產物即為碳化錳產品,二氧化錳的轉化率為94%。
實施例3
將-325目粒級所佔質量百分含量為95%純礦物氧化亞錳配加0.5%的腐殖酸和7.5%的水分後造球,然後乾燥,將乾燥後的樣品於CH4體積百分數20%,H2體積百分數60%,CO體積百分數12%,N2體積百分數8%的氣氛中進行焙燒,焙燒溫度1200℃,焙燒時間為90min,然後在N2氣氛中冷卻至室溫,所得焙燒產物即為碳化錳產品,二氧化錳的轉化率為96%。
對比實施例1
將-325目粒級所佔質量百分含量為95%分析純二氧化錳配加0.5%的CMC和7.5%的水分後造球,然後乾燥,將乾燥後的樣品於CH4體積百分數40%,H2體積百分數20%,CO體積百分數20%,N2體積百分數20%的氣氛中進行焙燒,焙燒溫度1250℃,焙燒時間為90min,然後在N2氣氛中冷卻至室溫,所得焙燒產物中二氧化錳轉化為碳化錳的轉化率僅為70%。
對比實施例2
將-325目粒級所佔質量百分含量為95%分析純二氧化錳配加0.5%的CMC和7.5%的水分後造球,然後乾燥,將乾燥後的樣品於CH4體積百分數10%,H2體積百分數30%,CO體積百分數50%,N2體積百分數10%的氣氛中進行焙燒,焙燒溫度1200℃,焙燒時間為90min,然後在N2氣氛中冷卻至室溫,所得焙燒產物中二氧化錳轉化為碳化錳的轉化率僅為83%。
對比實施例3
將-325目粒級所佔質量百分含量為95%分析純二氧化錳配加0.5%的CMC和7.5%的水分後造球,然後乾燥,將乾燥後的樣品於CH4體積百分數10%,H2體積百分數10%,CO體積百分數20%,N2體積百分數60%的氣氛中進行焙燒,焙燒溫度1200℃,焙燒時間為100min,然後在N2氣氛中冷卻至室溫,所得焙燒產物中二氧化錳轉化為碳化錳的轉化率僅為65%。