一種超富集植物收穫物資源化利用的系統和方法與流程
2023-06-01 18:15:51 6
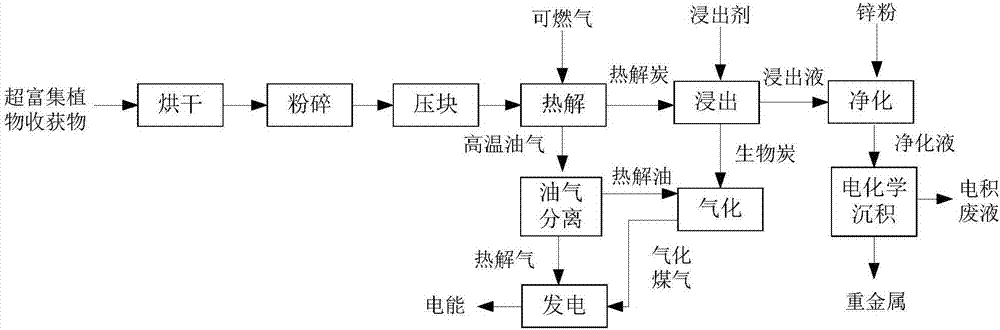
本發明屬於農業資源化技術領域及汙染土壤修復領域,具體地,涉及一種超富集植物收穫物資源化利用的系統和方法。
背景技術:
植物修復是重金屬汙染土壤修復的一種方法,經過近幾年的發展,植物修復技術以其治理效果的永久性、治理過程的原位性、治理成本的低廉性和環境美學的兼容性等特點,已逐漸成為汙染土壤治理的主要途徑之一,並開始進入產業化初期階段。在我國本土也已發現蜈蚣草(富集砷)、berkheyacoddii植物(富集鎳)、東南景天(富集鋅)、brassicacampestris(富集鉛或鎘)等多種超富集植物。現有技術主要集中在超富集植物的篩選、螯合誘導修復、接種菌根強化、基因技術、農藝管理和田間措施等。而關於修復重金屬汙染土壤後的植物收穫物的處理及資源化技術,國內外的研究報導很少,且基本上都是簡單的試驗探索。
實現超富集植物收穫物地有效處理和資源化,是植物修復技術體系需要完善的一個難點,也是植物修復技術在產業化過程中,必須面對和迫切需要解決的關鍵問題之一。這是由於積累了大量重金屬的植物往往會通過腐爛、落葉等途徑使重金屬元素重返土壤,因此必須在植物落葉等途徑使重金屬元素重返土壤,因此必須在植物落葉前收割植株體,並將其及時無害化處理。
現有的超富集植物收穫物的處理方法要麼不能有效的處理重金屬,要麼不能實現超富集植物收穫物的資源化利用,迫切的需要提供一種環境和經濟效益共贏的處理方法。
技術實現要素:
為了克服現有技術的不足,本發明首先提供了一種超富集植物收穫物資源化利用的系統,包括:
熱解裝置,設有熱解原料入口、可燃氣入口、熱解炭出口和高溫油氣出口;
浸出裝置,設有浸出劑入口、熱解炭入口、生物炭出口和浸出液出口,所述熱解炭入口與所述熱解裝置的熱解炭出口相連;
淨化裝置,設有鋅粉入口、浸出液入口和淨化液出口,所述浸出液入口與所述浸出裝置的浸出液出口相連;
電化學沉積裝置,設有淨化液入口、重金屬出口和電積廢液出口,所述淨化液入口與所述淨化裝置的淨化液出口相連;
油氣分離裝置,設有高溫油氣入口、熱解油出口和熱解氣出口,所述高溫油氣入口與所述熱解裝置的高溫油氣出口相連;
流化床,設有生物炭入口、熱解油入口和氣化煤氣出口,所述生物炭入口與所述浸出裝置的生物炭出口相連,所述熱解油入口與所述油氣分離裝置的熱解油出口相連。
進一步地,所述系統還包括:
內燃機,設有熱解氣入口、氣化煤氣入口和發電機組,所述熱解氣入口與所述油氣分離裝置的熱解氣出口相連,所述氣化煤氣入口與所述流化床的氣化煤氣出口相連。
進一步地,所述系統還包括:
烘乾裝置,設有烘乾原料入口和烘乾料出口;
粉碎裝置,設有粉碎原料入口和粉碎料出口,所述粉碎原料入口與所述烘乾裝置的烘乾料出口相連;
壓塊裝置,設有壓塊原料入口和料包出口,所述壓塊原料入口與所述粉碎裝置的粉碎料出口相連,所述料包出口與所述熱解裝置的熱解原料入口相連。
進一步地,所述電化學沉積裝置的陽極材料為鋁板或不鏽鋼板,陰極材料為惰性材料。
進一步地,所述熱解裝置為無熱載體蓄熱式旋轉床。
本發明還提供了一種採用上述系統資源化利用超富集植物收穫物的方法,包括如下步驟:
準備超富集植物收穫物;
將所述超富集植物收穫物送入所述熱解裝置中進行熱解,獲得熱解炭、高溫油氣;
將所述熱解炭送入所述浸出裝置,用(nh4)2co3-nh3-h2o體系將所述熱解炭中的重金屬浸出,獲得浸出液和生物炭;
將所述浸出液送入所述淨化裝置,用鋅粉置換所述浸出液中的雜質元素,獲得淨化液;
將所述淨化液送入所述電化學沉積裝置進行電化學沉積,獲得重金屬;
將所述高溫油氣送入所述油氣分離裝置進行分離,獲得熱解油和熱解氣;
將所述熱解油和所述生物炭送入所述流化床進行氣化,獲得氣化煤氣。
進一步地,上述方法還包括如下步驟:
將所述熱解氣和所述氣化煤氣燃燒發電。
進一步地,所述電化學沉積過程中的電流效率≥90%。
進一步地,所述超富集植物收穫物的熱解溫度為400-700℃,熱解時間為30-60min,熱解結束後保溫20-45min。
進一步地,所述(nh4)2co3-nh3-h2o體系中,[nh4]+的濃度為2-10mol/l,氨水的濃度為1-6mol/l;浸出步驟的固液比為2:1-5:1,浸出時間為30-300min,浸出溫度為30-50℃。
本發明將超富集植物收穫物進行熱解,並將超富集植物熱解產生的熱解炭經浸提液浸提重金屬後與熱解油一併進入流化床產生氣化煤氣,既能確保植物修復技術的完整性,又回收重金屬,實現了環境和經濟效益的統一。
附圖說明
圖1為本發明實施例中的一種超富集植物收穫物資源化利用的系統的結構示意圖;
圖2為本發明實施例中的一種超富集植物收穫物資源化利用的工藝流程圖。
具體實施方式
以下結合附圖和實施例,對本發明的具體實施方式進行更加詳細的說明,以便能夠更好地理解本發明的方案以及其各個方面的優點。然而,以下描述的具體實施方式和實施例僅是說明的目的,而不是對本發明的限制。
如圖1所示,本發明提供的超富集植物收穫物資源化利用的系統包括烘乾裝置1、粉碎裝置2、壓塊裝置3、熱解裝置4、浸出裝置5、淨化裝置6、電化學沉積裝置7、油氣分離裝置8、流化床9和內燃機10。
烘乾裝置1用於乾燥超富集植物收穫物,有助於超富集植物收穫物在熱解裝置4中更好的被熱解。烘乾裝置1設有烘乾原料入口和烘乾料出口。
粉碎裝置2用於破碎超富集植物收穫物,設有粉碎原料入口和粉碎料出口,粉碎原料入口與烘乾裝置1的烘乾料出口相連。
壓塊裝置3用於將破碎後的破碎超富集植物收穫物壓成料包,以便更好的送入熱解裝置4。壓塊裝置3設有壓塊原料入口和料包出口,壓塊原料入口與粉碎裝置2的粉碎料出口相連。
熱解裝置4用於熱解超富集植物收穫物。熱解裝置4設有熱解原料入口、可燃氣入口、熱解炭出口和高溫油氣出口,熱解原料入口與壓塊裝置3的料包出口相連。
浸出裝置5用於將重金屬從熱解炭中浸出。浸出裝置設有浸出劑入口、熱解炭入口、生物炭出口和浸出液出口,熱解炭入口與熱解裝置4的熱解炭出口相連。
淨化裝置6用鋅粉置換浸出液中的雜質元素,獲得淨化液。淨化裝置6設有鋅粉入口、浸出液入口和淨化液出口,浸出液入口與浸出裝置5的浸出液出口相連。
電化學沉積裝置7用於進行電化學沉積反應,使重金屬從淨化液中脫除。電化學沉積裝置7設有淨化液入口、重金屬出口和電積廢液出口,淨化液入口與淨化裝置6的淨化液出口相連。
油氣分離裝置8用於分離熱解產生的高溫油氣。油氣分離裝置8設有高溫油氣入口、熱解油出口和熱解氣出口,高溫油氣入口與熱解裝置4的高溫油氣出口相連。
流化床9用於製備氣化煤氣。流化床9設有生物炭入口、熱解油入口和氣化煤氣出口,生物炭入口與浸出裝置5的生物炭出口相連,熱解油入口與油氣分離裝置8的熱解油出口相連。
內燃機10用於燃燒發電。內燃機10設有熱解氣入口、氣化煤氣入口和發電機組,熱解氣入口與油氣分離裝置8的熱解氣出口相連,氣化煤氣入口與流化床9的氣化煤氣出口相連。
本發明將超富集植物收穫物進行熱解,並將超富集植物熱解產生的熱解炭經浸提液浸提重金屬後與熱解油一併進入流化床產生氣化煤氣,既能確保植物修復技術的完整性,又回收重金屬,實現了環境和經濟效益的統一。
圖1所示的系統中,熱解氣和氣化煤氣用於發電,實現了資源的循環利用。在本發明其他的實施例中,解氣和氣化煤氣也可另做他用。
圖1所示的系統中,超富集植物收穫物先乾燥,然後經過粉碎和壓塊後再進行熱解。顯然,超富集植物收穫物也可不經乾燥、粉碎和壓塊,直接進行熱解。
本發明使用的熱解裝置內為高溫絕氧環境,熱解揮發氣與高溫煙氣隔絕,避免了二次汙染。熱解過程中物料相對料床靜止,不受壓,不翻動,輻射管內流體與反應爐膛完全隔離,避免了產生飛灰的問題。在本發明優選的實施例中,所用的熱解裝置為熱載體蓄熱式旋轉床,熱效率高,達到86%以上。
在本發明優選的實施例中,電化學沉積裝置的陽極材料為鋁板或不鏽鋼板,陰極材料為惰性材料。可用的惰性材料包括:高純石墨、塗釕鈦板、硼化鈦板、碳化鈦或硼化鋯。高純石墨、塗釕鈦板、硼化鈦板、碳化鈦和硼化鋯等,得到的電積金屬質量好,而且也不會產生二次汙染。
如圖2所示,本發明提供的採用上述系統資源化利用超富集植物收穫物的方法,包括如下步驟:
準備超富集植物收穫物;
將超富集植物收穫物依次送入烘乾裝置1、粉碎裝置2和壓塊裝置3中進行乾燥、破碎和壓塊;
將壓塊後的超富集植物收穫物送入熱解裝置4中進行熱解,獲得熱解炭、高溫油氣;
將熱解炭送入浸出裝置5,用(nh4)2co3-nh3-h2o體系將熱解炭中的重金屬浸出,獲得浸出液和生物炭;
將浸出液送入淨化裝置6,用鋅粉置換浸出液中的雜質元素,獲得淨化液;
將淨化液送入電化學沉積裝置7進行電化學沉積,獲得重金屬;
將高溫油氣送入油氣分離裝置8進行分離,獲得熱解油和熱解氣;
將熱解油和生物炭送入流化床9進行氣化,獲得氣化煤氣;
將熱解氣和氣化煤氣送入內燃機10燃燒發電。
同前所述,熱解氣和氣化煤氣也可另做他用。
同前所述,超富集植物收穫物也可不經乾燥、粉碎和壓塊,直接進行熱解。優選地,超富集植物收穫物烘乾至含水量為20wt%(重量百分比)左右,然後粉碎至10cm左右,再壓成堆密度為0.2-0.4t/m3的料包。
熱解溫度過低、時間過短,超富集植物收穫物不能被熱解完全;熱解溫度過高、時間過長,增加了系統的能耗。在本發明優選的實施例中,超富集植物收穫物在熱解裝置中的熱解溫度為400-700℃,熱解時間為30-60min。超富集植物收穫物熱解後最好再保溫一段時間,能夠使其熱解更充分。優選地,熱解結束後保溫20-45min。
本發明採用(nh4)2co3-nh3-h2o體系浸出重金屬。在本發明優選的實施例中,(nh4)2co3-nh3-h2o體系中,[nh4]+的濃度為2-10mol/l,氨水的濃度為1-6mol/l。在此條件下,浸出步驟的固液比優選為2:1-5:1,浸出時間優選為30-300min,浸出溫度優選為30-50℃。
電化學沉積過程中的電流效率越高,得到的重金屬越多。在本發明優選的實施例中,電化學沉積過程中的電流效率≥90%。
下面參考具體實施例,對本發明進行說明。下述實施例中所取工藝條件數值均為示例性的,其可取數值範圍如前述發明內容中所示。下述實施例所用的檢測方法均為本行業常規的檢測方法。
實施例1
本實施例採用圖1所示的系統和圖2所示的工藝流程資源化利用超富集植物收穫物。本實施例所用的超富集植物收穫物為紫苜蓿,原料含水率為48.5wt%,鉛的濃度為725mg/kg(乾物質重)。具體如下:
11)將1t(噸)紫苜蓿原料送入烘乾機1,烘乾溫度為80℃,烘乾至水分含量為21.6wt%,而後送入粉碎機2粉碎至10cm左右,並送入壓塊機3進行壓塊,料包的堆密度為0.4t/m3。
12)將壓塊後的紫苜蓿送入蓄熱式旋轉床熱解裝置4,其中熱解溫度為400℃,熱解時間為60min,熱解結束後保溫45min,獲得熱解炭和高溫油氣。
13)將產生的熱解炭輸送至浸出裝置5,採用(nh4)2co3-nh3-h2o體系浸出,獲得浸出液和生物炭。[nh4]+的濃度為6mol/l,氨水的濃度為4mol/l;浸出步驟的固液比為3:1,浸出時間為60min,浸出溫度為40℃。
14)將浸出液送入淨化裝置6,用鋅粉置換浸出液中的雜質元素,獲得淨化液。
15)將淨化液送入電化學沉積裝置7進行電化學沉積,獲得重金屬。電化學沉積裝置的陽極材料為不鏽鋼板,陰極材料為高純石墨。電化學沉積過程中的電流效率為95%。
16)將高溫油氣送入油氣分離裝置8進行分離,獲得熱解油和熱解氣。
17)將熱解油和生物炭送入流化床9進行氣化,獲得氣化煤氣。
18)將熱解氣和氣化煤氣送入內燃機10燃燒發電。
本實施例回收的鉛為0.28kg,回收率約為76%,發電315kwh。
實施例2
本實施例採用圖1所示的系統和圖2所示的工藝流程資源化利用超富集植物收穫物。本實施例所用的超富集植物收穫物為蜈蚣草,原料含水率為47.5wt%,砷的濃度為1746mg/kg(乾物質重)。具體如下:
21)將1t蜈蚣草原料送入烘乾機1,烘乾溫度為100℃,烘乾至水分含量為21.6wt%,而後送入粉碎機2粉碎至10cm左右,並送入壓塊機3進行壓塊,料包的堆密度為0.2t/m3。
22)將壓塊後的蜈蚣草送入蓄熱式旋轉床熱解裝置4,其中熱解溫度為700℃,熱解時間為30min,熱解結束後保溫20min,獲得熱解炭和高溫油氣。
23)將產生的熱解炭輸送至浸出裝置5,採用(nh4)2co3-nh3-h2o體系浸出,獲得浸出液和生物炭。[nh4]+的濃度為2mol/l,氨水的濃度為1mol/l;浸出步驟的固液比為2:1,浸出時間為300min,浸出溫度為50℃。
24)將浸出液送入淨化裝置6,用鋅粉置換浸出液中的雜質元素,獲得淨化液。
25)將淨化液送入電化學沉積裝置7進行電化學沉積,獲得重金屬。電化學沉積裝置的陽極材料為不鏽鋼板,陰極材料為塗釕鈦板。電化學沉積過程中的電流效率為93%。
26)將高溫油氣送入油氣分離裝置8進行分離,獲得熱解油和熱解氣。
27)將熱解油和生物炭送入流化床9進行氣化,獲得氣化煤氣。
28)將熱解氣和氣化煤氣送入內燃機10燃燒發電。
本實施例回收的砷為0.75kg,回收率約為82%,發電354kwh。
實施例3
本實施例採用圖1所示的系統和圖2所示的工藝流程資源化利用超富集植物收穫物。本實施例所用的超富集植物收穫物為蜈蚣草,原料含水率為40.3wt%,砷的濃度為1850mg/kg(乾物質重)。具體如下:
31)將1t蜈蚣草原料送入烘乾機1,烘乾溫度為110℃,烘乾至水分含量為24.5wt%,而後送入粉碎機2粉碎至10cm左右,並送入壓塊機3進行壓塊,料包的堆密度為0.3t/m3。
32)將壓塊後的蜈蚣草送入蓄熱式旋轉床熱解裝置4,其中熱解溫度為600℃,熱解時間為50min,熱解結束後保溫30min,獲得熱解炭和高溫油氣。
33)將產生的熱解炭輸送至浸出裝置5,採用(nh4)2co3-nh3-h2o體系浸出,獲得浸出液和生物炭。[nh4]+的濃度為10mol/l,氨水的濃度為6mol/l;浸出步驟的固液比為5:1,浸出時間為30min,浸出溫度為30℃。
34)將浸出液送入淨化裝置6,用鋅粉置換浸出液中的雜質元素,獲得淨化液。
35)將淨化液送入電化學沉積裝置7進行電化學沉積,獲得重金屬。電化學沉積裝置的陽極材料為鋁板,陰極材料為硼化鋯。電化學沉積過程中的電流效率為91%。
36)將高溫油氣送入油氣分離裝置8進行分離,獲得熱解油和熱解氣。
37)將熱解油和生物炭送入流化床9進行氣化,獲得氣化煤氣。
38)將熱解氣和氣化煤氣送入內燃機10燃燒發電。
本實施例回收的砷為0.94kg,回收率約為85%,發電328kwh。
從上述實施例可知,採用本發明提供的工藝處理超富集植物收穫物,重金屬回收率高且無二次汙染。
綜上,本發明將超富集植物收穫物進行熱解,並將超富集植物熱解產生的熱解炭經浸提液浸提重金屬後與熱解油一併進入流化床產生氣化煤氣,既能確保植物修復技術的完整性,又回收重金屬,實現了環境和經濟效益的統一。
顯然,上述實施例僅僅是為清楚地說明本發明所作的舉例,而並非對實施方式的限定。對於所屬領域的普通技術人員來說,在上述說明的基礎上還可以做出其它不同形式的變化或變動。這裡無需也無法對所有的實施方式予以窮舉。而由此所引申出的顯而易見的變化或變動仍處於本發明的保護範圍之中。