凸凹多曲率類飛機蒙皮製件成形用工裝的製作方法
2023-08-02 00:14:01
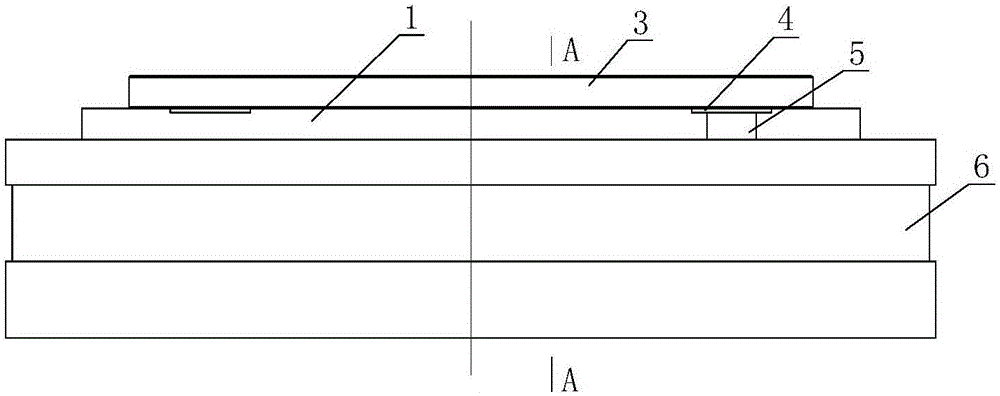
本實用新型屬於鈑金件成形製造技術領域,特別是涉及一種凸凹多曲率類飛機蒙皮製件成形用工裝。
背景技術:
蒙皮拉伸成形是航空製造領域典型的板材成形方法,主要用於生產構成飛機氣動外形的大型蒙皮類製件,其工藝過程為:先將位於板材兩側的夾鉗將板材夾緊,然後通過夾鉗的包覆拉伸運動或拉形模具垂直向上頂升運動,使板材逐漸貼合到拉形模具表面並發生拉伸變形以得到最終的形狀。拉形工藝的特點是在板材彎曲的同時加切向拉力,使板材剖面內的應力趨於均勻一致並減小彎曲變形產生的彎矩,所以拉形工藝回彈較小,成形件精度較高,被廣泛用於對成形質量要求較高的飛機蒙皮類製件的製造中。
蒙皮拉伸成形屬薄板類成形,主要通過拉伸設備的鉗口對拉伸毛料施加拉力和彎矩的運動,使毛料與拉伸成形工裝的貼合面逐步擴展,並最終完全貼合的成形方法。蒙皮拉伸成形過程比其他類型的成形過程複雜的多,它涉及拉、彎、扭複合加載動作及其組合,並同時受到材料性能、材料變形趨勢、拉伸成型方式、設備運行參數等的影響。
在凸凹多曲率類飛機蒙皮製件時,多採用蒙拉成形、落壓成形、手工敲打製造或採用將製件一分為二(或分割為多個)等傳統成形工藝,避開凸凹難成形處的局部特徵,然後再將兩個或多個成形製件通過焊接連接為圖紙所需形狀的凸凹多曲率蒙皮製件。採用傳統成形方式製作的凸凹多曲率蒙皮製件與通過複合成形整體加工的製件相比,其結構整體性較差,影響製件整體強度和剛度;同時需要額外增加連接框,加大了製件的定位難度,生產效率低、需耗費人工安裝等不必要的工時。
在加工凸凹多曲率類飛機蒙皮製件2時(如圖4所示),由於製件具有凸凹多曲率特徵,無法採用蒙拉工藝成形,也無法通過蒙拉過程中增加上壓模來成形。這時,就會考慮採用充液成形技術來成形製件,但如果僅通過充液成形工藝對於成形脊部特徵需要很大的成形壓力,這就需要很大噸位的液壓設備,而且回彈問題也會比較突出,甚至在脊部成形過程中容易出現起皺等缺陷。
技術實現要素:
本實用新型為解決公知技術中存在的技術問題而提供一種可降低凸凹多曲率特徵製件的成形難度、提高製件成形精度和生產效率的凸凹多曲率類飛機蒙皮製件成形用工裝。
本實用新型為解決公知技術中存在的技術問題所採取的技術方案是:
凸凹多曲率類飛機蒙皮製件成形用工裝,其特徵在於:包括上模板、凸模、凹模和密封圈,所述凹模內製有呈倒人字形的模腔並通過螺釘與上模板連接,所述凸模是由壓板和與壓板成一體的立筋構成,在凸模立筋的頭部制有與製件脊部相吻合的型面,所述凸模置於凹模的模腔內並通過定位銷與上模板固接,在凸模的壓板與凹模相接觸部位設有密封圈。
本實用新型還可以採用如下技術方案:
所述凹模與上模板通過導向套和導向銷定位。
所述凸模的壓板上制有多個充液孔。
本實用新型具有的優點和積極效果是:由於本實用新型採用上述技術方案,即利用本工裝來實現凸凹多曲率製件的成形加工,降低凸凹多曲率特徵製件的成形難度,提高製件的成形精度,對於對表面質量要求高的蒙皮製件優勢非常顯著。這樣不僅可保證蒙皮部件的整體性,減少蒙皮製件的分割數量,增加蒙皮製件的整體強度和剛度;而且還可簡化凸凹多曲率類飛機蒙皮製件的工藝和降低加工難度,最大限度地利用材料的塑形成形極限,有效地提高了生產效率,大幅度降低了生產成本,迅速提升了塑性加工領域中板金件的製造水平,本成形用工裝可廣泛的應用於宇航、汽車等工業領域。
附圖說明
圖1是本實用新型的結構示意圖;
圖2是圖1的俯視圖;
圖3是圖1的A-A剖視圖;
圖4是凸凹多曲率類飛機蒙皮製件結構示意圖。
圖中:1、凸模;2、凸凹多曲率類飛機蒙皮製件;3、上模板;4、導向套;5、導向銷;6、凹模;7、定位銷;8、密封圈。
具體實施方式
為能進一步了解本實用新型的實用新型內容、特點及功效,茲例舉以下實施例,並配合附圖詳細說明如下:
請參閱圖1-圖4,凸凹多曲率類飛機蒙皮製件成形用工裝,包括上模板3、凸模1、凹模6和密封圈8,所述凹模內製有呈倒人字形的模腔,通過螺釘與上模板連接,並通過導向套4和導向銷5與上模板導向定位,所述導向銷5與凹模6為過渡配合。所述凸模是由壓板和與壓板成一體的立筋構成,在凸模立筋的頭部制有與製件脊部相吻合的型面,在蒙拉成形過程中,所述凸模1通過緊固件固定在蒙拉模具工作檯上,以防止在蒙拉成形過程中凸模1出現躥動。在充液成形過程中,所述凸模置於凹模的模腔內並通過定位銷7固定在上模板3上,在凸模壓板與凹模相接觸部位設有密封圈8。
本實施例中,所述凸模的壓板上制有多個充液孔。
本實用新型附圖中描述的實施例是示例性的,僅用於解釋本實用新型,而不能理解為對本實用新型的限制。