一種環氧樹脂基複合材料及其製備方法與流程
2023-12-05 13:16:26 2
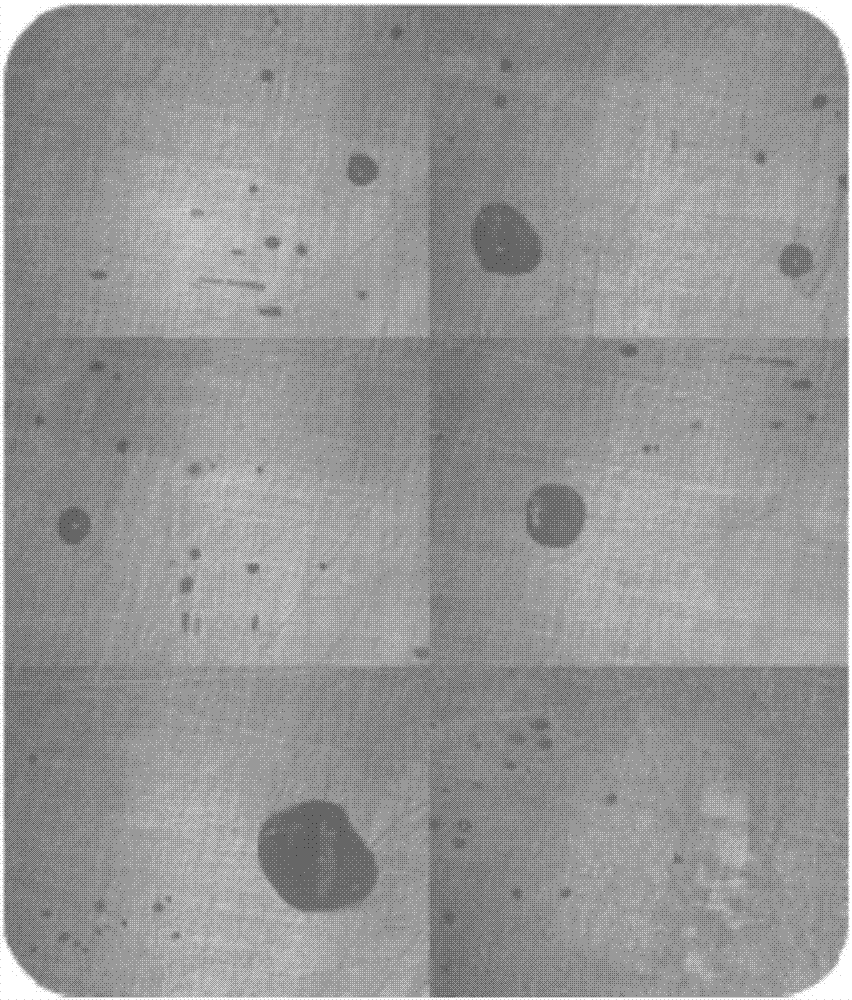
本發明屬於高分子材料領域,涉及一種環氧樹脂材料,尤其涉及一種環氧樹脂基複合材料。
背景技術:
近年來,纖維增強樹脂基複合材料由於其輕質高強的優異力學性能,逐漸在市場上掀起一股熱潮,更是作為高新結構材料已被運用於航天、汽車等領域。在纖維增強樹脂基複合材料中,基體通過界面將載荷有效地傳遞到增強相當中,纖維是承受由基體傳遞來的有效載荷,是主承力相。經過纖維增強後的樹脂體系與純樹脂材料相比,其模量、耐腐蝕性、耐衝擊性、耐熱性等優點得以大幅度提高。眾所周知,凡分子結構中含有環氧基團的高分子化合物統稱為環氧樹脂,它是一種優良的熱固性樹脂。與目前應用的不飽和聚酯樹脂相比,固化後的環氧樹脂具有更優良的力學性能,耐腐蝕性,耐熱性等。當下,環氧樹脂在粉末塗料、封裝料、粘接劑等領域已被廣泛運用,而在纖維增強複合材料領域中更是大顯身手。它與玻璃纖維、凱夫拉縴維、碳纖維等高性能纖維的結合,引來了新一代結構功能材料的萌芽,可被廣泛應用於航空航天、運動器材、建築工程、化工防護等重要領域。
真空輔助樹脂導流工藝,改成型技術即是在真空壓力下,藉助壓力差的驅動,利用樹脂的流動、滲透實現對纖維織物的浸漬,並在真空壓力條件下固化成型。過去的25年以來,真空輔助樹脂導流工藝是複合材料製造行業中應用最為廣泛的成型工藝之一,主要具有以下幾個優點:1)樹脂在真空環境下浸漬纖維增強物,能夠保證體系中不留多餘的樹脂,纖維體積含量很高,制出更高質量產品;2)該工藝可精確控制樹脂用量,使樹脂損耗達到最少,節約成本;3)不同部分的真空壓力相同,意味著通過該工藝製得成品的樹脂分布相對均勻;4)單面模具,另一面為真空袋,僅用一面模具就能得到一面光滑、另一面平整的製品,可以較好的控制產品厚度,節約了模具製造成本和時間。
與傳統製造工藝相比,真空輔助樹脂導流工藝製備出的產品中氣泡少,孔隙率低,質量更低,強度更高,批次之間的區別更穩定。然而,在製備中,仍有缺陷。目前使用真空輔助樹脂導流工藝製備的纖維增強環氧樹脂複合材料表面儘管已經得以改善,但還是存在相當量的針孔。其主要原因還是因為織物表面存在界面空隙,而樹脂因其具有一定黏度,在固化過程中來不及填補,以及由於環氧樹脂本身的熱膨脹性質,產生了針孔狀小孔的現象。目前工業中最常用的解決方案為在形成製品的基礎上進行表面噴塗處理,雖然有效可行,但是多出了後續處理環節略顯累贅;而許多實驗室研究方向為對纖維織物改性從而增強纖維與樹脂間的浸潤性,雖然有些試驗結果效果顯著,但依然屬於科研層次,並不能運用到工業生產。
技術實現要素:
針對現有技術中存在的技術問題,本發明提供一種環氧樹脂基複合材料及其製備方法,所述製備方法解決了材料表面的針孔現象,大大降低了單位表面的氣孔數,幾乎做到了無氣孔的理想效果。
為達到上述目的,本發明採用以下技術方案:
本發明目的之一在於提供一種環氧樹脂基複合材料,所述複合材料包括纖維增強織物以及環氧樹脂材料,其中所述環氧樹脂材料包括環氧樹脂、固化劑以及氟化石墨。
作為本發明優選的技術方案,所述環氧樹脂材料中固化劑與環氧樹脂的質量比為(0.1~0.5):1,如0.1:1、0.15:1、0.2:1、0.25:1、0.3:1、0.35:1、0.4:1或0.45:1等,但並不僅限於所列舉的數值,該數值範圍內其他未列舉的數值同樣適用。
優選地,所述氟化石墨與環氧樹脂的質量比為(0.03~0.06):1,如0.03:1、0.035:1、0.04:1、0.045:1、0.05:1、0.055:1或0.06:1等,但並不僅限於所列舉的數值,該數值範圍內其他未列舉的數值同樣適用。
作為本發明優選的技術方案,所述纖維增強織物的層數≥2,如2、3、4、5、6、7、8、9、10、12、15、18、20、30、40或50等,但並不僅限於所列舉的數值,該數值範圍內其他未列舉的數值同樣適用。
本發明目的之二在於提供一種上述環氧樹脂基複合材料的製備方法,所述方法包括以下步驟:
(1)將氟化石墨分散於固化劑中,再將固化劑與環氧樹脂混合,得到環氧樹脂材料;
(2)在第一層纖維增強織物一側塗覆步驟(1)得到的環氧樹脂材料,再於第一層纖維增強織物塗覆有環氧樹脂材料的一側依次鋪覆剩餘各層纖維增強織物、脫模布以及導流網,然後抽真空,向纖維增強織物中導入環氧樹脂材料,固化,得到環氧樹脂基複合材料。
環氧樹脂基複合材料中氣孔產生的位置主要是纖維增強織物的交錯位置,因此在第一層纖維增強織物一側塗覆一層預先塗覆一層環氧樹脂材料,在進行後續操作,能夠增加纖維增強織物的浸潤性,降低複合材料的氣孔率。
作為本發明優選的技術方案,步驟(1)所述分散在超聲下進行。
優選地,所述超聲的時間為10~20min,如10min、11min、12min、13min、14min、15min、16min、17min、18min、19min或20min等,但並不僅限於所列舉的數值,該數值範圍內其他未列舉的數值同樣適用。
作為本發明優選的技術方案,步驟(1)所述固化劑與環氧樹脂混合後,對得到溫度環氧樹脂材料進行抽真空處理。
優選地,所述抽真空處理的時間為5~15min,如5min、6min、7min、8min、9min、10min、11min、12min、13min、14min或15min等,但並不僅限於所列舉的數值,該數值範圍內其他未列舉的數值同樣適用。
由於在混合樹脂體系時,會有部分空氣進入環氧樹脂體系中,先用真空罐對其抽真空,對製備得到的環氧樹脂材料進行抽真空處理,可以確保真空條件,環氧樹脂材料在導入纖維增強織物時也會更均勻。對環氧樹脂材料抽真空速度不宜太快,應在5min以上完成,否則會導致環氧樹脂材料的固化。
作為本發明優選的技術方案,步驟(2)中用於塗覆在第一層纖維增強織物一側的環氧樹脂材料為步驟(1)得到的環氧樹脂材料的5~15%,如5%、6%、7%、8%、9%、10%、11%、12%、13%、14%或15%等,但並不僅限於所列舉的數值,該數值範圍內其他未列舉的數值同樣適用。
本發明使用的環氧樹脂、固化劑以及纖維增強織物,以及本發明所述製備方法步驟(2)在第一層纖維增強織物一側塗覆步驟(1)得到的環氧樹脂材料後的其他操作,均為本領域技術人員為了製備纖維增強的環氧樹脂複合材料所公知的技術手段,就不再贅述。
本發明通過使用氟化石墨對環氧樹脂材料進行改性,增強了環氧樹脂的流動性,提高了環氧樹脂在纖維增強織物中的分散性,同時通過製備過程中在第一層纖維增強織物一側預先塗覆一層環氧樹脂材料,增加纖維增強織物對環氧樹脂材料的浸潤性,二者協同作用,減少了環氧樹脂基複合材料的氣孔率,而通過對環氧樹脂材料進行抽真空處理,進一步降低了複合材料的氣孔率,提高了複合材料的機械性能。
與現有技術方案相比,本發明至少具有以下有益效果:
(1)本發明提供一種環氧樹脂基複合材料,所述複合材料具有優異的機械性能;
(2)本發明提供一種環氧樹脂基複合材料的製備方法,所述製備方法很好地解決了材料表面的針孔現象,大大降低了單位表面的氣孔率,肉眼觀察所述複合材料表面幾乎無氣孔;
(3)本發明提供一種環氧樹脂基複合材料的製備方法,所述製備方法省去了現有技術中的表面噴塗處理工藝,降低了產品製作成本;
(4)本發明提供一種環氧樹脂基複合材料的製備方法,所述製備方法工藝簡單,可用於工業化生產。
附圖說明
圖1是本發明製備得到的環氧樹脂基複合材料的金相顯微鏡圖;
圖2是採用現有技術製備得到的環氧樹脂基複合材料的金相顯微鏡圖。
具體實施方式
下面結合附圖並通過具體實施方式來進一步說明本發明的技術方案。
為更好地說明本發明,便於理解本發明的技術方案,本發明的典型但非限制性的實施例如下:
實施例1
一種環氧樹脂基複合材料的製備方法,所述方法包括以下步驟:
(1)將7.5g氟化石墨超聲分散於50g固化劑中10min,再將含有氟化石墨的固化劑與200g環氧樹脂混合,得到環氧樹脂材料,對得到的環氧樹脂材料進行抽真空處理,抽真空時間為5min;
(2)在第一層纖維增強織物一側塗覆步驟(1)得到的環氧樹脂材料30g,再於第一層纖維增強織物塗覆有環氧樹脂材料的一側依次鋪覆剩餘9層纖維增強織物、脫模布以及導流網,然後抽真空,向纖維增強織物中導入環氧樹脂材料,固化,得到環氧樹脂基複合材料。
實施例2
一種環氧樹脂基複合材料的製備方法,所述方法包括以下步驟:
(1)將6g氟化石墨超聲分散於20g固化劑中12min,再將含有氟化石墨的固化劑與200g環氧樹脂混合,得到環氧樹脂材料,對得到的環氧樹脂材料進行抽真空處理,抽真空時間為10min;
(2)在第一層纖維增強織物一側塗覆步驟(1)得到的環氧樹脂材料11.3g,再於第一層纖維增強織物塗覆有環氧樹脂材料的一側依次鋪覆剩餘2層纖維增強織物、脫模布以及導流網,然後抽真空,向纖維增強織物中導入環氧樹脂材料,固化,得到環氧樹脂基複合材料。
實施例3
一種環氧樹脂基複合材料的製備方法,所述方法包括以下步驟:
(1)將12g氟化石墨超聲分散於100g固化劑中20min,再將含有氟化石墨的固化劑與200g環氧樹脂混合,得到環氧樹脂材料,對得到的環氧樹脂材料進行抽真空處理,抽真空時間為15min;
(2)在第一層纖維增強織物一側塗覆步驟(1)得到的環氧樹脂材料46.8g,再於第一層纖維增強織物塗覆有環氧樹脂材料的一側依次鋪覆剩餘15層纖維增強織物、脫模布以及導流網,然後抽真空,向纖維增強織物中導入環氧樹脂材料,固化,得到環氧樹脂基複合材料。
實施例4
一種環氧樹脂基複合材料的製備方法,所述方法包括以下步驟:
(1)將8g氟化石墨超聲分散於40g固化劑中15min,再將含有氟化石墨的固化劑與200g環氧樹脂混合,得到環氧樹脂材料,對得到的環氧樹脂材料進行抽真空處理,抽真空時間為8min;
(2)在第一層纖維增強織物一側塗覆步驟(1)得到的環氧樹脂材料24.8g,再於第一層纖維增強織物塗覆有環氧樹脂材料的一側依次鋪覆剩餘5層纖維增強織物、脫模布以及導流網,然後抽真空,向纖維增強織物中導入環氧樹脂材料,固化,得到環氧樹脂基複合材料。
實施例5
一種環氧樹脂基複合材料的製備方法,所述方法包括以下步驟:
(1)將10g氟化石墨超聲分散於80g固化劑中15min,再將含有氟化石墨的固化劑與200g環氧樹脂混合,得到環氧樹脂材料,對得到的環氧樹脂材料進行抽真空處理,抽真空時間為12min;
(2)在第一層纖維增強織物一側塗覆步驟(1)得到的環氧樹脂材料35g,再於第一層纖維增強織物塗覆有環氧樹脂材料的一側依次鋪覆剩餘12層纖維增強織物、脫模布以及導流網,然後抽真空,向纖維增強織物中導入環氧樹脂材料,固化,得到環氧樹脂基複合材料。
實施例6
一種環氧樹脂基複合材料的製備方法,所述方法除了對步驟(1)製備得到的環氧樹脂材料不進行抽真空處理外。
對比例1
一種環氧樹脂基複合材料的製備方法,所述方法除了步驟(1)不加入氟化石墨外,其他條件均與實施例1相同。
對比例2
一種環氧樹脂基複合材料的製備方法,所述方法除了步驟(2)不在第一層纖維增強織物一側塗覆步驟(1)得到的環氧樹脂材料外,其他條件均與實施例1相同。
對比例3
一種環氧樹脂基複合材料的製備方法,所述方法除了步驟(1)所述抽真空的時間為3min外,其他條件均與實施例1相同。
選取的樣本面積25cm*25cm,對實施例1-6以及對比例1-3製備得到的環氧樹脂基複合材料的表面平均氣孔數以及平均氣孔直徑進行測試,結果如表1所示。
表1
從表1可以看出,實施例1-5製備得到的環氧樹脂基複合材料表面幾乎無氣孔,而實施例6由於步驟(1)得到的環氧樹脂材料沒有進行抽真空處理,表面會有少量氣孔產生,且氣孔直徑較小。而對比例1沒有加入氟化石墨,平均氣孔個數達0.68個/cm2,且平均氣孔直徑較大,平均氣孔直徑達230μm;對比例2中步驟(2)不在第一層纖維增強織物一側塗覆步驟(1)得到的環氧樹脂材料,平均氣孔個數達0.60個/cm2,平均氣孔直徑達50μm;對比例3抽真空速度較快,導致部分環氧樹脂固化,在纖維增強織物中分部不夠均勻,導致平均氣孔個數達0.65個/cm2,平均氣孔直徑達150μm。
申請人聲明,本發明通過上述實施例來說明本發明的詳細結構特徵,但本發明並不局限於上述詳細結構特徵,即不意味著本發明必須依賴上述詳細結構特徵才能實施。所屬技術領域的技術人員應該明了,對本發明的任何改進,對本發明所選用部件的等效替換以及輔助部件的增加、具體方式的選擇等,均落在本發明的保護範圍和公開範圍之內。
以上詳細描述了本發明的優選實施方式,但是,本發明並不限於上述實施方式中的具體細節,在本發明的技術構思範圍內,可以對本發明的技術方案進行多種簡單變型,這些簡單變型均屬於本發明的保護範圍。
另外需要說明的是,在上述具體實施方式中所描述的各個具體技術特徵,在不矛盾的情況下,可以通過任何合適的方式進行組合,為了避免不必要的重複,本發明對各種可能的組合方式不再另行說明。
此外,本發明的各種不同的實施方式之間也可以進行任意組合,只要其不違背本發明的思想,其同樣應當視為本發明所公開的內容。