一種減震器組裝方法及減震器組裝裝置與流程
2023-12-01 09:14:56 2
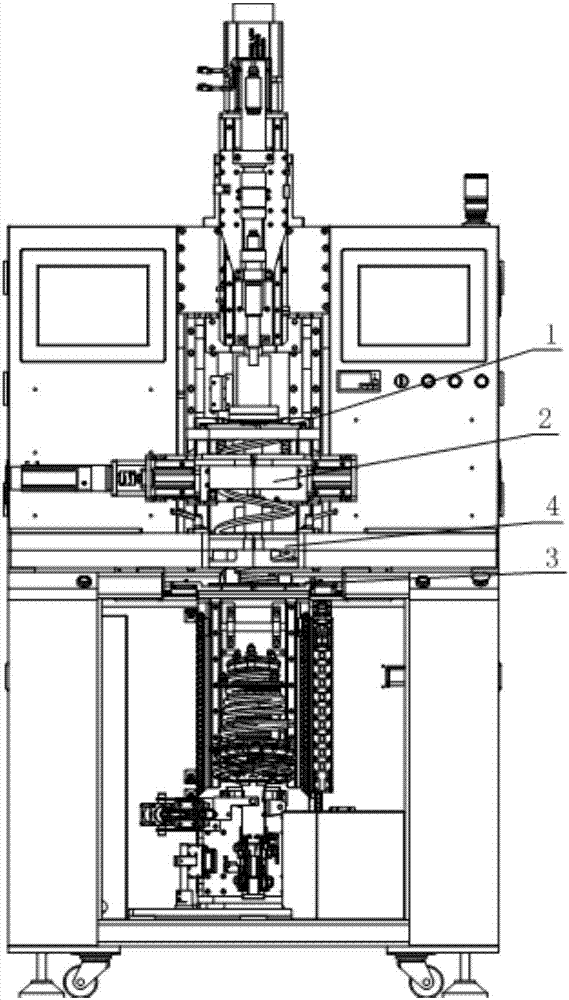
本發明涉及機械技術領域,特別涉及一種減震器組裝方法及減震器組裝裝置。
背景技術:
現有技術中減震器的組裝流程如下:彈簧放在阻尼器的彈簧盤上→將放置有彈簧的阻尼器放入機器定位→壓縮彈簧→組裝防塵套並安裝上支撐→螺母擰緊→下料。從上述流程可以看出,減震器的彈簧在組裝過程中,彈簧與阻尼器組裝完成後再對彈簧進行壓縮,彈簧壓縮後產生的側向力會把阻尼器的活塞杆壓偏,導致用於擰緊螺母的扭力批的軸線與活塞杆的軸線不在同一直線上,扭力批不能對螺母進行擰緊,
增大了減震器組裝的難度。
因此,如何降低減震器的組裝難度,成為本領域技術人員亟待解決的技術問題。
技術實現要素:
有鑑於此,本發明提供了一種減震器組裝裝置,以降低減震器的組裝難度,同時降低減震器組裝的人工勞動強度。本發明還提供了一種減震器組裝方法。
為實現上述目的,本發明提供如下技術方案:
一種減震器組裝裝置,包括:
上支撐定位裝置,所述上支撐定位裝置上開設有與減震器的上支撐配合的安裝孔;
設置在所述上支撐定位裝置的下端面與所述上支撐定位裝置浮動連接用於固定所述減震器的減震彈簧上端面的固定環;
驅動所述上支撐定位裝置沿所述固定環的軸線方向上下運動的驅動裝置;
與所述固定環平行布置用於支撐所述減震彈簧下端面的減震彈簧定位盤;
設置在所述固定環與所述減震彈簧定位盤之間用於對所述減震彈簧的壓縮起導向作用的導向環,所述導向環與所述減震彈簧下部配合;
設置在所述上支撐定位裝置上擰緊用於連接所述上支撐與減震器的活塞杆的螺栓的擰緊裝置。
優選的,在上述減震器組裝裝置中,所述導向環的內壁設置有能夠伸入所述減震彈簧間隙的託塊。
優選的,在上述減震器組裝裝置中,所述導向環包括第一導向半環和第二導向半環;
還包括:
第一開合板,所述第一導向半環安裝於所述第一開合板的上端面;
第二開合板,所述第二導向半環安裝於所述第二開合板的上端面;
與所述第一開合板連接的第一氣缸;
與所述第二開合板連接的第二氣缸;
用於對所述第一開合板和所述第二開合板的運動起導向作用的導向條。
優選的,在上述減震器組裝裝置中,所述第一導向半環與所述第一開合板銷釘連接,所述第二導向半環與所述第二開合板銷釘連接,所述第一開合板的上端面設置有用於壓緊所述第一導向半環的壓塊,所述壓塊與所述第一開合板螺釘連接,所述第二開合板上開端面設置有用於壓緊所述第二導向半環的第二壓塊,所述第二壓塊與所述第二開合板螺釘連接。
優選的,在上述減震器組裝裝置中,所述減震彈簧定位盤包括第一半圓形定位盤和第二半圓形定位盤;
還包括:
第一連接板,所述第一連接板包括第一水平板、與第一水平板連接的第一豎直板和與所述第一豎直板連接的第二水平板,所述第一水平板與所述第二水平板平行布置且所述第一水平板位於所述第二水平板的上方,所述第二水平板的上端面與所述第一半圓形定位盤的下端面連接;
第二連接板,所述第二連接板包括第三水平板、與第三水平板連接的第二豎直板和與所述第二豎直板連接的第四水平板,所述第三水平板與所述第二水平板平行布置且所述第三水平板位於所述第四水平板的上方,所述第四水平板的上端面與所述第二半圓形定位盤的下端面連接;
與所述第一水平板的下端面連接的第一滑塊,所述第一滑塊的下端設置有第一導軌;
與所述第一滑塊連接的第三氣缸;
與所述第三水平板的下端面連接的第二滑塊,所述第二滑塊的下端設置有第二導軌;
與所述第二滑塊連接的第四氣缸;
與所述第一導軌連接的第一安裝板,所述第一安裝板與所述導向條連接;
與所述第二導軌連接的第二安裝板,所述第二安裝板與所述導向條連接。
優選的,在上述減震器組裝裝置中,所述固定環包括第一固定半環和第二固定半環;
還包括:
第一固定板,所述第一固定板與所述第一固定半環連接,所述第一固定板上開設有與所述第一固定半環配合的第一半圓形凹槽;
第二固定板,所述第二固定板與所述第二固定半環連接,所述第二固定板上開設有與所述第二固定半環配合的第二半圓形凹槽;
與所述第一固定板垂直布置的第三固定板;
與所述第二固定板垂直布置的第四固定板,所述第三固定板和所述第四固定板沿所述第一固定半環和所述第二固定半環的開合方向相對布置;
左右旋螺杆,所述左右旋螺杆的第一螺母與所述第三固定板連接,所述左右旋螺杆的第二螺母與所述第四固定板連接;
與所述左右旋螺杆連接的伺服電機。
優選的,在上述減震器組裝裝置中,還包括安裝板,所述上支撐定位裝置與所述安裝板通過銷釘連接,所述減震彈簧定位盤與所述安裝板通過銷釘連接。
優選的,在上述減震器組裝裝置中,所述上支撐定位裝置包括第三豎直板和第五水平板,所述第三豎直板與所述安裝板銷釘連接;
還包括:
導向柱,所述導向柱的下端與所述固定環連接;
導向孔,所述第五水平板上開設有所述導向孔,所述導向孔與所述導向柱的上端滑動配合;
套設在所述導向柱外壁的彈簧,所述彈簧一端與所述固定環相抵,另一端與所述第五水平板相抵。
優選的,在上述減震器組裝裝置中,所述驅動裝置為伺服電機。
一種減震器組裝方法,減震器組裝方法採用上述任意一項記載的減震器組裝裝置,包括:
步驟1)安裝減震器的上支撐於所述減震器組裝裝置的上支撐定位裝置;
步驟2)安裝所述減震器的減震彈簧於所述減震器組裝裝置的固定環、所述導向環和減震彈簧定位盤上,實現對所述彈簧的固定;
步驟3)啟動所述減震器組裝裝置的驅動裝置帶動所述上支撐定位裝置和所述固定環運動實現對所述彈簧的壓縮;
步驟4)將所述減震器的活塞杆自下而上依次穿過所述減震彈簧定位盤、所述導向環和所述固定環,使所述活塞杆與所述上支撐配合,通過擰緊裝置實現活塞杆與上支撐的螺栓連接。
從上述技術方案可以看出,本發明提供的減震器組裝裝置,包括上支撐定位裝置、固定環、驅動裝置、彈簧減震定位盤、導向環和擰緊裝置。減震器組裝步驟:第一步,將上支撐通過上支撐定位裝置進行固定;第二步,將彈簧放置在固定環與彈簧定位盤之間,導向環套設在彈簧的外壁;第三步,驅動裝置驅動上支撐定位裝置下降,上支撐定位裝置帶動固定環下降,實現彈簧在固定環與彈簧定位盤之間的壓縮;第四步,活塞杆依次通過彈簧定位盤、導向環和固定環與上支撐定位裝置的上支撐配合,通過擰緊裝置擰緊螺栓,完成減震器組裝過程。本方案提供的減震器組裝裝置通過固定環、導向環和彈簧定位盤實現對彈簧的固定且壓縮的彈簧通過固定環和彈簧定位盤保持壓縮狀態,導向環能夠有效消除彈簧壓縮產生的側向力,在擰緊用於連接上支撐與活塞杆的螺栓的過程中,保證阻尼器的活塞杆的軸線與與擰緊裝置的軸線在同一直線上,有效降低了減震器組裝的難度。通過擰緊裝置對螺栓進行擰緊,代替人工擰緊螺栓,進一步降低了減震器組裝的人工勞動強度。
本方案還提供了一種減震器組裝方法,該減震器組裝方法此採用上述任意一項記載的減震器組裝裝置,由於減震器組裝裝置具有上述技術效果,採用了該減震器組裝裝置的減震器組裝方法也具有同樣的技術效果,在此不再贅述。
附圖說明
為了更清楚地說明本發明實施例或現有技術中的技術方案,下面將對實施例或現有技術描述中所需要使用的附圖作簡單地介紹,顯而易見地,下面描述中的附圖僅僅是本發明的一些實施例,對於本領域普通技術人員來講,在不付出創造性勞動的前提下,還可以根據這些附圖獲得其他的附圖。
圖1為本發明實施例提供的減震器組裝裝置的結構示意圖;
圖2為本發明實施例提供的上支撐定位裝置與固定環的結構示意圖;
圖3為本發明實施例提供的上支撐定位裝置與固定環的主視圖;
圖4為本發明實施例提供的上支撐定位裝置與固定環的左視圖;
圖5為本發明實施例提供的導向環的結構示意圖;
圖6為本發明實施例提供的導向環的俯視圖;
圖7為本發明實施例提供的減震彈簧定位盤的結構示意圖;
圖8為本發明實施例提供的減震彈簧定位盤的主視圖;
圖9為本發明實施例提供的減震器組裝方法的流程圖。
1、上支撐定位裝置,2、固定環,21、左右旋螺杆,22、伺服電機,3、減震彈簧定位盤,31、第三氣缸,32、第四氣缸,33、第一連接板,34、第二連接板,35、第一滑塊,36、第二滑塊,4、導向環,41、託塊,42、第一氣缸,43、第二氣缸,44、導向條,5、導向柱。
具體實施方式
本發明公開了一種減震器組裝裝置,以降低減震器的組裝難度,同時降低減震器組裝的人工勞動強度。本發明還公開了一種減震器組裝方法。
下面將結合本發明實施例中的附圖,對本發明實施例中的技術方案進行清楚、完整地描述,顯然,所描述的實施例僅僅是本發明一部分實施例,而不是全部的實施例。基於本發明中的實施例,本領域普通技術人員在沒有做出創造性勞動前提下所獲得的所有其他實施例,都屬於本發明保護的範圍。
請參閱圖1-圖9,圖1為本發明實施例提供的減震器組裝裝置的結構示意圖;圖2為本發明實施例提供的上支撐定位裝置與固定環的結構示意圖;圖3為本發明實施例提供的上支撐定位裝置與固定環的主視圖;圖4為本發明實施例提供的上支撐定位裝置與固定環的左視圖;圖5為本發明實施例提供的導向環的結構示意圖;圖6為本發明實施例提供的導向環的俯視圖;圖7為本發明實施例提供的減震彈簧定位盤的結構示意圖;圖8為本發明實施例提供的減震彈簧定位盤的主視圖;圖9為本發明實施例提供的減震器組裝方法的流程圖。
本發明公開了一種減震器組裝裝置,包括上支撐定位裝置1、固定環2、驅動裝置、彈簧減震定位盤、導向環和擰緊裝置。
上支撐定位裝置1上開設有與減震器的上支撐配合的安裝孔,用於實現對上支撐的固定。
固定環2用於固定減震器的減震彈簧的上端面,固定環2的環內壁與減震彈簧的外壁配合,固定環2與上支撐定位裝置1的安裝孔同軸布置。固定環2不僅能夠實現對減震彈簧上端面的壓緊,還能夠實現對減震彈簧上端周向的定位。
固定環2位於上支撐定位裝置1的下端面且與上支撐定位裝置1浮動連接。
驅動裝置驅動上支撐定位裝置1沿固定環2的軸線方向上下運動,同時上支撐定位裝置1帶動固定環2上下運動,從而實現對減震彈簧上端施加壓力。固定環2與上支撐定位裝置1的浮動連接方式能夠緩衝上支撐定位裝置1對固定環2的壓力,對固定環2起到保護作用。
減震彈簧定位盤3用於支撐減震彈簧的下端面,減震彈簧定位盤3對減震彈簧的下端面起到支撐作用,減震彈簧定位盤3與固定環2配合實現對減震彈簧的固定,減震彈簧定位盤3與固定環2平行布置,減震彈簧定位盤3上開設有與減震器的活塞杆配合的孔,該孔與固定環2同軸布置。
設置在固定環2與減震彈簧定位盤3之間用於對減震彈簧的壓縮起導向作用的導向環4,導向環4與減震彈簧下部配合。減震彈簧壓縮過程中,導向環4能夠對減震彈簧的下部外壁起導向作用,消除彈簧壓縮產生的側向力,保證阻尼器的活塞杆的軸線與擰緊裝置的軸線在同一直線上。導向環4的環內壁與壓縮減震彈簧的外壁貼合,導向環4沿其軸線方向具有一定的長度。
擰緊裝置設置在上支撐定位裝置1的上方,能夠用來擰緊用於連接上支撐與減震器的活塞杆的螺栓。優選的,擰緊裝置為扭力批。
減震器組裝步驟:
第一步,將上支撐通過上支撐定位裝置1進行固定;
第二步,將減震彈簧放置在固定環2與減震彈簧定位盤3之間,導向環4套在彈簧的外幣;
第三步,驅動裝置驅動上支撐定位裝置1下降,上支撐定位裝置1帶動固定環2下降,實現減震彈簧在固定環2與減震彈簧定位盤3之間的壓縮;
第四步,活塞杆依次通過減震彈簧定位盤3和固定環2與上支撐定位裝置1的上支撐配合,通過擰緊裝置擰緊螺栓,完成減震器組裝過程。
本方案提供的減震器組裝裝置通過固定環2、導向環4和減震彈簧定位盤3實現對減震彈簧的固定且壓縮的減震彈簧通過固定環2和減震彈簧定位盤3保持壓縮狀態,導向環能夠有效消除彈簧壓縮產生的側向力,在擰緊用於連接上支撐與活塞杆的螺栓的過程中,保證阻尼器的活塞杆的軸線與與擰緊裝置的軸線在同一直線上,有效降低了減震器組裝的難度。
通過擰緊裝置對螺栓進行擰緊,代替人工擰緊螺栓,進一步降低了減震器組裝的人工勞動強度。
上支撐定位裝置1與固定環2在驅動裝置的作用下同步下降,保證了上支撐與減震彈簧之間的相對位置不變,不需要後續對減震彈簧與上支撐之間的位置進行調整,進一步降低了減震器的組裝難度。
為了進一步優化上述技術方案,在本方案的一個具體實施例中,導向環4的內壁設置有能夠伸入減震彈簧間隙的託塊41,優選的,託塊41的個數為多個,且多個託塊41的布置高度沿著減震彈簧的螺旋方向及高度進行設置,從而實現對減震彈簧的有效支撐,且不影響減震彈簧的壓縮。
導向環4包括第一導向半環和第二導向半環,第一導向半環和第二導向半環均為半圓形環,第一導向半環與第二導向半環的開口方向相對,第一導向半環與第二導向半環組合後形成一個完整的圓環。
本方案提供的減震器組裝裝置還包括第一開合板、第二開合板、第一氣缸42、第二氣缸43和導向條44。
第一導向半環安裝在第一開合板的上端面,第二導向半環安裝在第二開合板的上端面,第一導向半環的開口位於第一開合板的邊緣,第二導向半環的開口位於第二開合板的邊緣,即第一開合板和第二開合板不影響第一導向半環與第二導向半環組成一個完整的圓環。
第一開合板的運動由第一氣缸42驅動,第二開合板的運動由第二氣缸43驅動,優選的,第一氣缸42與第一導向半環的開口端面垂直,第二氣缸43與第二導向半環的開口端面垂直,第一氣缸42帶動第一開合板水平運動,進而帶動第一導向半環水平運動,第二氣缸43帶動第二開合板水平運動,進而帶動第二導向半環水平運動。
第一開合板和第二開合板的運動方向由導向條44進行導向,優選的,第一開合板的兩側設置有兩個導向條44,第二開合板的兩側設置有兩個導向條44,導向條44的設置能夠保證第一導向半環與第二導向半環組合形成一個完整的圓環。
導向環4通過第一導向半環、第二導向半環、第一開合板、第二開合板、第一氣缸42和第二氣缸43,實現了導向環4的開啟和閉合,導向環4開啟,能夠方便減震彈簧的安裝,降低了減震彈簧安裝的難度,同時進一步降低了減震彈簧安裝的人工勞動強度。
第一導向半環與第一開合板銷釘連接,第二導向半環與第二開合板銷釘連接,該種連接方式能夠降低第一導向半環和第二導向半環的連接難度。
為了防止在使用過程中第一導向半環和第二導向半環脫落,第一開合板的上端面設置有用於壓緊第一導向半環的壓塊,第二開合板上開端面設置有用於壓緊第二導向半環的第二壓塊,壓塊和第二壓塊為l型壓塊,l型壓塊的水平部分壓在第一導向半環和第二導向半環上,l型壓塊的豎直部分壓在第一開合板和第二開合板的上表面。
壓塊與第一開合板螺釘連接,第二壓塊與第二開合板螺釘連接,通過調整螺釘的鬆緊度,進而調整壓塊對第一導向半環的壓緊力和第二壓塊對第二導向半環的壓緊力。
本方案提供的減震器組裝裝置還包括用於防止第一開合板和第二開合板分離的鎖緊裝置,當第一導向半環和第二導向半環閉合後,鎖緊裝置發揮作用,防止在減震器的組裝過程中導向環打開,影響對彈簧的定位。
鎖緊裝置包括第五氣缸、連接板和插板。
第五氣缸為鎖緊裝置的動力部件,用於驅動連接板和插板運動。
連接板與第五氣缸連接,連接板與第五氣缸的活塞杆垂直布置,連接板用於實現插板與第五氣缸的連接。
插板與活塞杆平行布置,相應的插板與連接板垂直布置,且位於連接板長度方向的兩側,插板的個數為兩個。
為了實現插板對第一開合板和第二開合板的鎖緊,第一開合板和第二開合板上開設的與插板配合的插槽,插槽與導向條44垂直,且插槽的長度延伸方向與第一開合板或者第二開合板所在的平面方向平行,且插槽與第一氣缸和第二氣缸的伸縮方向垂直。
導向環閉合後,第五氣缸的活塞杆伸出,推動連接板帶動插板運動,直至插板伸入插槽,實現對導向環的鎖緊;導向環需要開啟時,第五氣缸的活塞杆縮回,拉動連接板帶動插板運動,直至插板從插槽內抽出,解除對導向環的鎖緊作用,導向環在第一氣缸和第二氣缸的驅動作用下開啟。
減震彈簧定位盤3包括第一半圓形定位盤和第二半圓形定位盤,第一半圓形定位盤和第二半圓形定位盤均為半圓形定位盤,第一半圓形定位盤和第二半圓形定位盤上均開設有與減震彈簧配合的孔,第一半圓形定位盤上的孔為半圓形孔,第二半圓形定位盤上的孔為半圓形孔,第一半圓形定位盤和第二半圓形定位盤組合成一個完成的減震彈簧定位盤3,第一半圓形定位盤上的半圓形與第二半圓形定位盤上的半圓形孔組成一個圓孔,該圓孔的孔壁與減震彈簧的外壁貼合。
減震彈簧定位盤3的圓周設置有與減震彈簧下端面配合的定位塊,定位塊為l型定位塊,l型定位塊的水平部分與減震彈簧定位盤3的上端面連接,l型定位塊的豎直部分用於與減震彈簧的外壁配合,多個l型定位塊的豎直部分的高度不同,用以配合減震彈簧螺旋高度不同的多個位置。
本方案提供的減震器組裝裝置還包括第一連接板33、第二連接板34、第一滑塊35、第二滑塊36、第三氣缸31、第四氣缸32、第一導軌、第二導軌、第一安裝板和第二安裝板。
第一連接板33包括第一水平板、與第一水平板連接的第一豎直板和與第一豎直板連接的第二水平板,第一連接板33整體呈z型。第一水平板與第二水平板平行布置,第一水平板位於第二水平板的上方,第一豎直板上端與第一水平板連接,第一豎直板下端與第二水平板連接,第二水平板的上端面與第一半圓形定位盤的下端面連接。
第二連接板34包括第三水平板、與第三水平板連接的第二豎直板和與第二豎直板連接的第四水平板,第二連接板34整體呈z型。第三水平板與第二水平板平行布置,第三水平板位於第四水平板的上方,第二豎直板上端與第三水平板連接,第二豎直板下端與第四水平板連接,第四水平板的上端面與第二半圓形定位盤的下端面連接。
第一滑塊35與第一水平板的下端面連接,第一滑塊35的下端設置有第一導軌,第一滑塊35與第一導軌配合為第一連接板33的運動起到導向作用。
第三氣缸31與第一滑塊35連接,第三氣缸31為第一連接板33的運動提供了動力。
第二滑塊36與第三水平板的下端面連接,第二滑塊36的下端設置有第二導軌,第二滑塊36與第二導軌配合為第二連接板34的運動起到導向作用。
第四氣缸32與第二滑塊36連接,第四氣缸32為第二連接板34的運動提供了動力。
第三氣缸31帶動第一滑塊35運動,第一滑塊35帶動第一連接板33運動,進而帶動第一半圓形定位盤運動,第四氣缸32帶動第二滑塊36運動,第二滑塊36帶動第二連接板34運動,進而帶動第二半圓形定位盤運動,實現第一半圓形定位盤與第二半圓形定位盤的開合。
第一半圓形定位盤安裝在第二水平板的上端面,第二半圓形定位盤安裝在第四水平板的上端面,第一半圓形定位盤的開口位於第二水平板的邊緣,第二半圓形定位盤的開口位於第四水平板的邊緣,即第一連接板33和第二連接板34不影響第一半圓形定位盤與第二半圓形定位盤組成一個完整的圓盤。
減震彈簧定位盤3的開合,能夠方便減震彈簧的安裝,降低了減震彈簧的安裝難度,同時降低了減震彈簧安裝的人工勞動強度。
第一安裝板與第一導軌連接,第二安裝板與第二導軌連接,第一安裝板與導向條44連接,第二安裝板與導向條44連接。第一安裝板實現了減震彈簧定位盤3與導向環4的連接。
固定環2包括第一固定半環和第二固定半環,第一固定半環和第二固定半環均為半圓形環,第一固定半環和第二固定半環的開口方向相抵,第一固定半環和第二固定半環組合後形成一個完整的圓環。
固定環2的環壁上設置有與減震彈簧上端面配合的壓塊,壓塊的下端面與減震彈簧的上端面配合,實現對減震彈簧上端面的壓緊。
本方案提供的減震器組裝裝置還包括第一固定板、第二固定板、第三固定板、第四固定板、左右旋螺杆21和伺服電機22。
第一固定板與第一固定半環連接,第一固定板上開設有與第一固定半環配合的第一半圓形凹槽,第二固定板與第二固定半環連接,第二固定板上開設有與第二固定半環配合的第二半圓形凹槽,第一半圓形凹槽與第二半圓形凹槽的開口方向相對,且第一半圓形凹槽和第二半圓形凹槽組合後形成一個完成的圓,第一半圓形凹槽和第二半圓形凹槽相對布置的一側均為開放端,保證第一固定半環與第二固定半環組合後形成一個完整的圓環。
第三固定板與第一固定板垂直布置,第四固定板與第二固定板垂直布置,第三固定板和第四固定板沿第一固定半環和第二固定半環的開合方向相對布置,第三固定板和第四固定板與左右旋螺杆21垂直布置,且沿固定環的軸線方向布置,第三固定板和第四固定板與左右旋螺杆21連接。
左右旋螺杆21的第一螺母與第三固定板連接,左右旋螺杆21的第二螺母與第四固定板連接,伺服電機22與左右旋螺杆21連接。伺服電機22驅動左右旋螺杆21轉動,進而第一螺母和第二螺母分別帶動第三固定板和第四固定板運動,從而分別帶動第一固定板和第二固定板運動,最終實現第一固定半環和第二固定半環的開合。
固定環2的開合能夠方便減震彈簧的安裝,降低了減震彈簧安裝的難度,同時進一步降低了減震彈簧安裝的人工勞動強度。
左右旋螺杆21為第一固定半環和第二固定半環的運動提供了導向作用。
本方案提供的減震器組裝裝置還包括安裝板,上支撐定位裝置1與安裝板通過銷釘連接,減震彈簧定位盤3與安裝板通過銷釘連接,固定環2與上支撐定位裝置1浮動連接,減震彈簧定位盤3與導向環4連接。當更換的減震彈簧的直徑尺寸發生變化時,將上支撐定位裝置1、減震彈簧定位盤3、固定環2和導向環4整套從安裝板上拆除,更換與減震彈簧尺寸配合的上支撐定位裝置1、減震彈簧定位盤3、固定環2和導向環4,從而省去了人工調整組裝工裝的步驟,降低了對工作人員的要求,同時降低了人工勞動強度,也節省了時間,提高了減震器組裝的效率。
上支撐定位裝置1包括第三豎直板和第五水平板,第三豎直板與安裝板銷釘連接。
本方案提供的減震器組裝裝置還包括導向柱5、導向孔和彈簧,實現了上支撐定位裝置1與固定環2的浮動連接。
第五水平板上開設有導向孔,導向柱5的下端與固定環2連接,導向柱5的上端與導向孔滑動配合,彈簧套設在導向柱5的外壁,彈簧一端與固定環2相抵,另一端與第五水平板相抵。導向柱5的上端設置有螺母,螺母的下端面與導向孔的上端相抵,且螺母位於第五水平板的上端面。
上支撐定位裝置1的第五水平板下壓彈簧,導向孔沿著導向柱5上下運動,從而實現上支撐定位裝置1與固定環2之間的浮動配合。
在本方案的一個具體實施例中,驅動裝置為伺服電機。
一種減震器組裝方法,其特徵在於,所述減震器組裝方法採用上述任意一項記載的震器組裝裝置,該減震器組裝方法包括:
步驟1)安裝減震器的上支撐於減震器組裝裝置的上支撐定位裝置1,實現對上支撐的固定;
步驟2)安裝減震器的減震彈簧於減震器組裝裝置的固定環2、導向環4和減震彈簧定位盤3上,實現對彈簧的固定,該步驟中,減震彈簧的上面端通過固定環2固定,減震彈簧的下端面通過減震彈簧定位盤3支撐,減震彈簧的下部通過導向環4固定;
步驟3)啟動減震器組裝裝置的驅動裝置帶動上支撐定位裝置1和固定環2運動實現對彈簧的壓縮,壓縮後的彈簧位於固定環2與減震彈簧定位盤3之間;
步驟4)將減震器的活塞杆自下而上依次穿過減震彈簧定位盤3、導向環4和固定環2,使活塞杆與上支撐配合,通過擰緊裝置實現活塞杆與上支撐的螺栓連接。
步驟3)和步驟4)中減震彈簧始終處於壓縮狀態,且該壓縮狀態的保持通過減震彈簧定位盤3和固定環2實現,在活塞杆與上支撐連接的過程中,減震彈簧定位盤3和固定環2能夠對彈簧提供穩定而有效的壓緊力,不需要人工操作,從而降低了減震器組裝的難度和人工勞動強度。
對所公開的實施例的上述說明,使本領域專業技術人員能夠實現或使用本發明。對這些實施例的多種修改對本領域的專業技術人員來說將是顯而易見的,本文中所定義的一般原理可以在不脫離本發明的精神或範圍的情況下,在其它實施例中實現。因此,本發明將不會被限制於本文所示的這些實施例,而是要符合與本文所公開的原理和新穎特點相一致的最寬的範圍。