一種碳熱還原製備碳載Ru基催化劑的方法與流程
2023-12-01 09:12:06 2
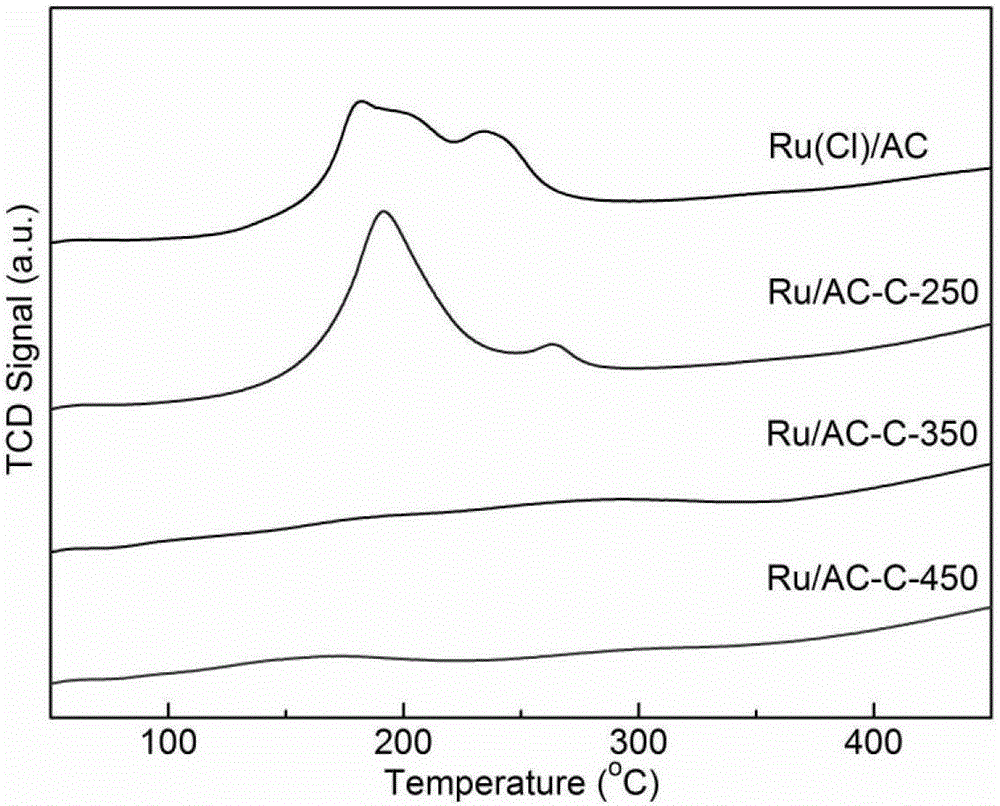
本發明涉及催化化學領域,具體涉及Ru基催化劑的製備方法,適用於含碳載體負載金屬催化劑的製備與還原及相應的催化反應過程。
背景技術:
過渡金屬催化劑由於具有高活性等特點,廣泛應用於各個領域,尤其是釕基催化劑具有較高的加氫活性,在催化加氫裂解等方面有廣泛應用和重要研究。傳統負載型催化劑的製備,以溶液環境分散金屬化合物,實現活性組分和助劑在載體上的高分散,需要反覆乾燥、浸漬、沉澱,催化劑前驅體製備完成後往往還要使用還原劑對負載的金屬組分進行還原得到納米金屬顆粒負載型催化劑。
傳統的還原製備方法主要是化學還原法和氣體還原法,化學還原主要是利用各種強還原性試劑,如硼氫化鉀、水合肼、甲醛等。這些還原劑通常需要過量加入,操作過程及條件要求嚴苛,步驟繁瑣;還原之後需要反覆清洗,金屬組分流失嚴重,金屬的負載量與理論計算值差別較大。此外,化學還原法工藝要求苛刻,設備種類要求多,耗費時間長,生產效率低下,不利於工業生產大規模製備。氣體還原法主要是使用還原性氣體如氫氣、一氧化碳等進行還原,氣體還原效果較好,但氫氣屬於易燃易爆氣體,一氧化碳具有毒性;而且氣體還原通常需要較高的溫度,高溫下金屬粒子容易團聚長大,分散度差。CN1270081A敘述了先用含釕化合物溶液浸漬載體,氫氣氛下還原後再浸漬助催化劑的製備方法,但製備得到的催化劑活性較低。CN1125634,CN10276052所述製備方法是在浸漬釕前體後分別用氣相和液相還原,再浸漬其他組分,工序繁瑣。CN101816935,WO2013041061,CN102600900,CN102794199所述方法是將金屬鹽製成溶液,加入活性炭,得到金屬-炭漿液,再乾燥或分離,洗滌。這些製備方法雖然能夠製備得到一定活性或選擇性的釕碳催化劑,滿足一定的要求,但製備方法都比較繁瑣,且並沒有表現出優異的普適特性。近年來,含碳載體負載型催化劑得到了廣泛的研究與應用。一方面含碳材料由於其具有較高的比表面積,豐富的多孔性質,以及可以燃燒方便金屬回收的特點等,被廣泛用作催化劑載體;另一方面,含碳催化劑的含碳載體具有還原性,能對負載的金屬物種直接進行還原得到負載型金屬催化劑。
技術實現要素:
本發明的目的在於提供一種利用碳熱還原製備均勻分布具有較小粒徑的高活性的碳載釕基催化劑的方法,對現有的催化劑製備方法進行補充與改進,實現在非還原性氣氛中還原製備得到負載型納米金屬催化劑。該方 法工藝過程簡單,使用自身載體的還原性能,節約成本,簡化步驟,製備周期短,效率高,能耗少,不使用有機溶劑,綠色環保。所製備的催化劑金屬分散度高,金屬粒徑分布均勻,有利於提高金屬的利用率,在生物質催化轉化中有機物加氫等反應具有良好的活性。
為了達到上述目的,本發明採用的碳熱還原製備方法的技術方案如下:
一種碳熱還原製備負載型金屬催化劑的方法,所述負載型催化劑以活性炭,介孔碳,焦化炭,泡沫碳等含碳材料為載體,以釕為金屬活性組分,負載量為2~15wt%,金屬前驅體為氯化釕水合物等;以鐵、鈷、銅、鎳、鎢、鋯、錳、錫、鈦等其中的一種為金屬助劑,負載量為0~10wt%。
所述方法為:按照金屬活性組分和助劑的負載量,配製金屬活性組分和助劑前驅體浸漬液,與碳材料混合浸漬,靜置12~48h後,置於烘箱中於80~120℃乾燥,然後研磨過篩得到粉末催化劑前驅體,在惰性氣體氛圍中經碳熱還原反應製得負載型金屬催化劑。
具體工藝方法為:
所述碳材料為活性炭,介孔碳,焦化炭,泡沫碳等含碳材料,經研磨過篩得到80~100目的粉末,置於120℃烘箱中乾燥12h備用。所述碳材料的比表面積為100~1300m2/g。優選成本低廉、來源廣泛、應用普遍的高比表面的活性炭和介孔碳,所述活性炭是指以椰殼為原料比表面積800~1300m2/g的催化劑載體專用活性炭。
所述金屬活性組分和金屬助劑前驅體為金屬活性組分的氯化物、羰基配合物、有機金屬化合物、硝酸鹽中的一種或一種以上的組合。本發明中以釕作為金屬活性組分,前驅體優選RuCl3·xH2O。本發明實施例中優選金屬助劑的硝酸鹽為金屬助劑前驅體。
所述金屬活性組分的負載量為2~15wt%,更優選2~5wt%,所述金屬助劑的負載量為0~10wt%。負載量是金屬組分質量與載體質量的百分比。
所述浸漬混合手段包括磁攪拌,手動攪拌或超聲混合,優選磁攪拌與超聲,所述均勻混合條件為攪拌超聲2~30min。
所述浸漬方法為等體積溼浸漬法,浸漬條件為室溫浸漬12~48h後,置於烘箱中於80~130℃乾燥10~24h。優選條件為室溫浸漬24h後,置於烘箱中110℃乾燥12h。
所述還原方法為碳熱還原,在非還原性氣氛如N2,He,Ar等惰性氣氛利用自身載體所含的碳材料在一定溫度下進行金屬組分的還原。
所述還原溫度為350~600℃下進行還原,優選400~500℃;所述還原過程使用程序升溫,升溫速率1~10℃/min,優選3~5℃/min;還原時長為0.5~12h,優選3~6h。
與現有製備方法相比,本發明方法具有以下特點:
1.本發明所採用的製備方法是採用成本低廉來源廣泛的活性炭作為載體製備負載型金屬催化劑,可適用於其他含碳載體和金屬組分的負載型催 化劑的製備。
2.本發明利用含碳載體自身的還原性,在惰性氣氛中對負載的金屬組分進行碳熱還原,節約了還原劑,避免了還原性氣體的危險性,以及對自身載體的充分使用,間接提高了金屬的負載量。
附圖說明
圖1Ru(Cl)/AC以及不同碳熱還原溫度下的Ru/AC-C樣品的H2-TPR圖。
圖2在N2氣氛中不同碳熱還原溫度下得到的Ru基催化劑TEM圖:(a)350℃;(b)400℃;(c)450℃;(d)500℃;(e)550℃。
圖3在H2氣氛中不同還原溫度下得到的Ru基催化劑TEM圖:(a)350℃;(b)450℃;(c)500℃。
具體實施方式
下列實施例將有助於理解本發明,但本發明內容並不局限於此。
實施例1
將活性炭載體研磨過篩80~100目後,置於120℃烘箱中過夜乾燥;採用等體積浸漬法,配製與載體飽和吸水量等量的三氯化釕前驅體浸漬液,攪拌緩慢加入載體使其混合均勻,超聲處理後,靜置24h,然後於110℃烘箱中乾燥過夜得到負載量為5wt%的粉末催化劑前驅體(Ru(Cl)/AC)。
實施例2
取適量上述催化劑前驅體Ru(Cl)/AC置於石英管中,於25ml/min的Ar氣氛下,以3℃/min程序分別升溫至250℃,350℃,450℃恆溫保持3個小時,得到Ru/AC-C-250,Ru/AC-C-350,Ru/AC-C-350。
實施例3
H2-TPR表徵:取適量上述實施例2中的三種催化劑樣品和催化劑前驅體Ru(Cl)/AC置於U型石英管中,在化學吸附儀上於25ml/min的10%H2/Ar氣氛下,以10℃/min程序升溫至600℃。表徵結果如圖1所示,結果表明在惰性氛圍中,Ru(Cl)/AC可以在350℃以上的溫度範圍發生碳熱還原得到Ru/AC-C。
實施例4
TEM表徵:取適量上述催化劑前驅體Ru(Cl)/AC置於石英管中,於20ml/min的N2氣氛下,以3.5℃/min程序分別升溫至350℃,400℃,450℃,500℃,550℃,恆溫保持3個小時,得到Ru/AC-C-350,Ru/AC-C-400,Ru/AC-C-450,Ru/AC-C-500,Ru/AC-C-550。將這些催化劑進行TEM表徵,表徵結果如圖2所示,結果表明碳熱還原需要適宜的還原溫度以形成粒徑分布均勻且較小的負載型納米金屬催化劑。
實施例5
以蔗糖為碳源,以氣相二氧化矽,介孔矽MCM~41為模板,使用硫酸高溫碳化得到的介孔碳材料分別標記為C1,C2。採用上述方法,不使用模板 直接使用硫酸高溫碳化得到的碳材料標記為C3。按照實施例1中的方法分別採用C1,C2,C3為載體製備碳載催化劑前驅體Ru(Cl)/C1,Ru(Cl)/C2,Ru(Cl)/C3。取適量上述催化劑前驅體Ru(Cl)/AC置於U型石英管中,在化學吸附儀上於25ml/min的He氣氛下,以5℃/min程序升溫至400~500℃,即可得到碳熱還原的催化劑:Ru/C1-C,Ru/C2-C,Ru/C3-C。
實施例6
按照實施例1中的方法,在三氯化釕前驅體浸漬液中加入一定量的含有鐵、鈷、銅、鎳、鎢、鋯、錳、錫、鈦等其中的一種的金屬鹽,摻雜的金屬助劑的負載量為1wt%。按照實施例1和2中的方法,在惰性氣氛中碳熱還原得到雙組份的金屬催化劑如Ru-Ti/AC-C,Ru-Zr/AC-C,Ru-Ni/AC-C,Ru-W/AC-C等。
實施例7
將0.2g還原後的催化劑即Ru/AC-C和5wt%的順丁烯二酸水溶液加入到反應釜中,並攪拌分散均勻。氫氣置換後,置壓到3MPa,加熱到100℃,反應1h後取樣進行液相色譜分析。反應後催化劑離心過濾洗滌後循環使用,循環反應6次,反應結果如表1所示,順丁烯二酸轉化率可達99%,產物丁二酸收率為90%以上。結果表明碳熱還原製備得到的釕基催化劑在順丁烯二酸加氫反應中具有較高的催化活性和穩定性。
表1 Ru/AC-C催化順丁烯二酸加氫的循環催化效應
對比例TEM表徵:取適量上述催化劑前驅體Ru(Cl)/AC置於石英管中,於20ml/min的H2氣氛下,以3.5℃/min程序分別升溫至350℃,400℃,450℃,500℃,550℃,650℃恆溫保持3個小時,得到Ru/AC-H-350,Ru/AC-H-450,Ru/AC-H-500,將這些催化劑進行TEM表徵,表徵結果如圖3所示,與實施例4圖2中的結果對比,表明碳熱還原方法可以製備得到粒徑分布均勻且較小的金屬催化劑。