汽車密封條前置噴塗裝置的製作方法
2023-05-01 09:07:31 3
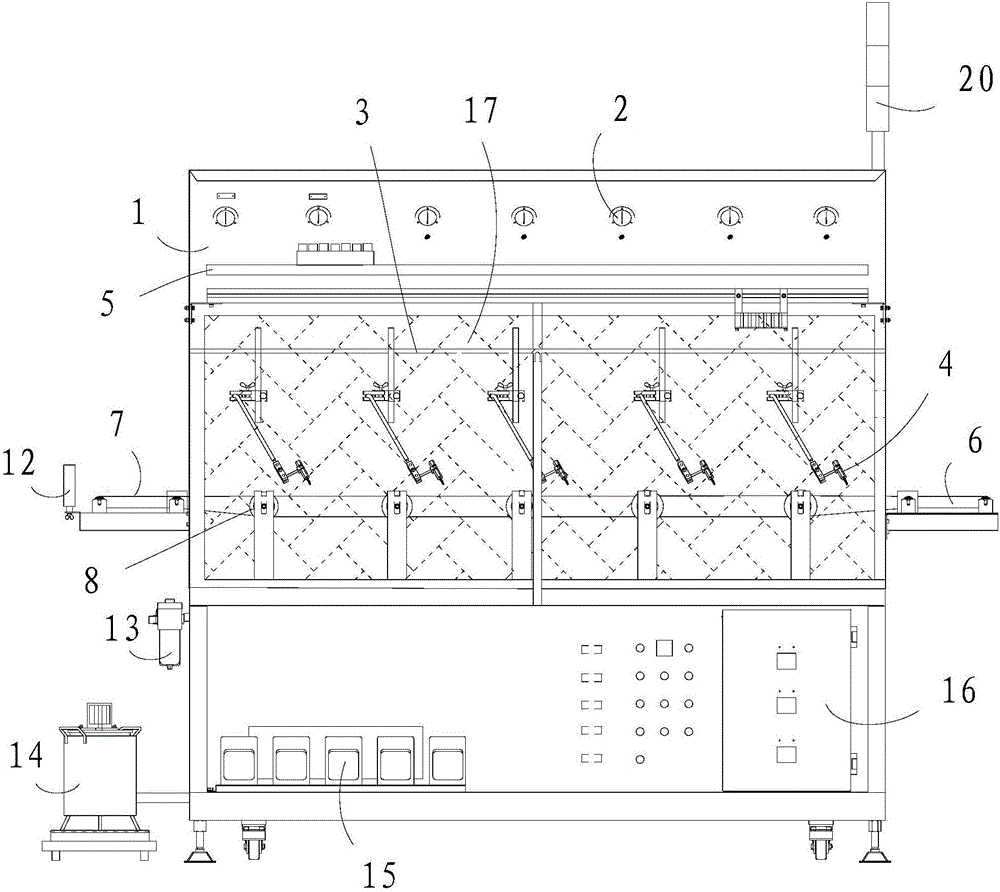
本發明涉及汽車密封條生產技術領域,特別涉及一種汽車密封條前置噴塗裝置。
背景技術:
轎車或SUV車型上普遍使用有密封條,密封條包括玻璃呢槽、門框密封條、後背門框密封條及部分機艙或車門系統的輔件密封條等。以汽車門框密封條的結構為例,其主體由海綿泡管、密實膠及芯材構成,海綿泡管部位在生產中需要進行噴塗有機矽或聚氨酯成分的塗層,以提升密封條的降噪、耐磨、密封及抗凍性能,並可防止汙染鈑金而美化外觀等。
密封條產品的生產工藝多數為擠出機擠出→製品硫化→製品冷卻→製品成型→製品表面處理→製品噴塗→塗層固化→製品冷卻→製品打碼→製品打孔等。生產流程為橡膠密封條硫化完畢後進行噴塗,具體上在制品硫化完畢後,經過降溫、表面處理,然後使用壓力泵(桶)、重力桶、蠕動泵或齒輪泵等輸送塗料至噴槍,噴槍將霧化的塗料噴塗至膠條表面,進而膠條再進入固化爐加熱,水分揮發,塗料交聯固化形成膜狀塗層。
具體上,現有的噴塗裝置一般包含噴塗箱、噴塗料桶、塗料輸送部件、氣源、噴槍等。噴塗箱包含排風裝置,料桶有重力式料桶、壓力式料桶及常規的帶攪拌的料桶等,能夠適合不同的輸送方式。塗料輸送部件一般為重力式自流、壓力泵送或蠕動泵泵送,噴槍主要為帶噴塗針的大噴槍和無針的小噴槍兩種。
目前,常規工藝下的擠出線體一般設定的較長,多數擠出線體長度超過80米,從而會造成其佔用廠地面積較大,同時前期設備採購投入的費用較高,且後期的設備能源耗費較大。為解決上述生產工藝存在的問題,以實現節能減排以及生產成本的降低,人們試圖在擠出機擠出膠條後進入微波硫化爐前即進行噴塗,也就是採用前置噴塗工藝。在膠條噴塗後再藉助微波硫化及熱風硫化加熱的溫度同時實現膠條的硫化及塗層的同步固化,從而減少相應的表面預處理、塗層固化、及膠條冷卻工序,同時也節約相應的設備、廠地,以及設備所消耗的能源。
前置噴塗工藝採用先噴塗後硫化的方式,此工藝雖可解決傳統工藝線體長,設備投入高以及能耗高的問題,但由於製品未進行硫化,橡膠製品較軟,無挺性,極易造成變形和劃傷,產品出現變形則意味著產品報廢,生產成本上升,對於結構中含有海綿泡管尤其是壁薄的車門密封條等更加容易出現此問題。因此,現有前置噴塗工藝僅能針對玻璃呢槽或門框密封條等挺性好的產品,其已成為局限車門密封條等製品前置噴塗工藝推進的主要問題。
技術實現要素:
有鑑於此,本發明旨在提出一種汽車密封條前置噴塗裝置,以能夠適於較軟的密封條產品採用前置噴塗工藝。
為達到上述目的,本發明的技術方案是這樣實現的:
一種汽車密封條前置噴塗裝置,以在硫化工序前對由擠出機擠出的密封條膠條進行噴塗,該汽車密封條前置噴塗裝置包括箱體,於所述箱體上設有具有進口及出口的噴塗通道,與所述噴塗通道連通設有排風機構,還包括具有噴槍的噴塗機構,所述噴槍設於所述噴塗通道內,以及,
傳送部,在所述噴塗通道的進口和出口處分別設置的可同步運轉的兩個;
轉動支撐部,在所述噴塗通道內沿所述密封條膠條的運動方向間隔布置有多個,且相鄰轉動支撐部之間的距離為20~30cm;
約束導向部,在所述噴塗通道的出口設置,以可於滑經所述噴塗通道的密封條膠條的兩相對側施加約束力,而對所述密封條膠條的運動進行導向。
進一步的,所述噴槍採用無針的低霧化氣壓噴槍。
進一步的,所述噴槍為沿密封條膠條運動方向間隔布置的多個,且各所述噴槍的噴射方向與所述轉動支撐部錯開布置。
進一步的,所述噴塗機構包括與所述噴槍連接的塗料供應單元及壓縮氣體供應單元,所述塗料供應單元包括塗料料桶,及經由輸料管連接於所述塗料料桶和各所述噴槍之間的多個蠕動泵。
進一步的,在所述塗料料桶內設有冷卻機構及攪拌機構,在所述塗料料桶的底部設有電子稱重機構,並在所述箱體上設有與所述電子稱重機構聯接的重量報警單元。
進一步的,所述傳送部包括轉動設於所述箱體上的傳送帶,以及設於所述箱體上的驅使所述傳送帶運轉的電機,所述轉動支撐部為轉動設於所述箱體上的轉動支撐輥。
進一步的,在各所述轉動支撐輥與兩個所述傳送部之一間傳動連接有承接該傳送部的驅使,而使各所述轉動支撐輥轉動的傳動部。
進一步的,在所述箱體上對應於各所述轉動支撐輥設有清理機構,在所述轉動支撐輥轉動時,所述清理機構可對所述轉動支撐輥的外周面進行清理。
進一步的,所述排風機構包括形成於所述箱體內的與所述噴塗通道相連通的排風通道,以及與所述排風通道連通的排風機,在所述排風通道與所述噴塗通道間設有塗料吸附件,並在所述箱體的一端設有吸附件更換口。
進一步的,所述約束導向部包括並排設置於所述箱體上的兩個導向轉輥,兩個所述導向轉輥的轉動軸線與所述密封條膠條的運動方向垂直布置,且兩個所述導向轉輥之間的距離可調。
相對於現有技術,本發明具有以下優勢:
本發明所述的汽車密封條前置噴塗裝置通過傳送部、多個轉動支撐部以及約束導向部的設置,可使得密封條膠條按設定的位置通過噴塗通道,能夠防止密封條膠條通過時因發生翻轉而出現劃傷問題,且相鄰轉動支撐部的距離設定為20~30cm,可防止因轉動支撐部間距過大導緻密封條膠條出現下垂堆積和變形問題,從而可保證較軟的密封條膠條順利通過噴塗通道,並由噴槍進行噴塗而完成前置噴塗工藝。
附圖說明
構成本發明的一部分的附圖用來提供對本發明的進一步理解,本發明的示意性實施例及其說明用於解釋本發明,並不構成對本發明的不當限定。在附圖中:
圖1為本發明實施例所述的汽車密封條前置噴塗裝置的結構簡圖;
圖2為圖1的左視圖;
圖3為本發明實施例所述的傳送帶及轉動支撐輥的結構簡圖;
圖4為本發明實施例所述的刮板的結構簡圖;
圖5為圖2中A部分的局部放大圖;
附圖標記說明:
1-箱體,2-氣壓表,3-噴槍安裝支架,4-噴槍,5-照明燈,6-進口傳送帶,7-出口傳送帶,8-轉動支撐輥,9-皮帶,10-第一電機,11-第二電機,12-約束轉棍,13-油氣分離器,14-塗料料桶,15-蠕動泵,16-電控櫃,17-吸附棉,18-排風機,19-擋板,20-聲光報警器,21-吸附件更換口,22-轉動支撐輥安裝架,23-刮板,24-密封條膠條,25-噴塗通道,26-排風通道。
具體實施方式
需要說明的是,在不衝突的情況下,本發明中的實施例及實施例中的特徵可以相互組合。
下面將參考附圖並結合實施例來詳細說明本發明。
本發明涉及一種汽車密封條前置噴塗裝置,其可在硫化工序前對由擠出機擠出的密封條膠條進行噴塗,以實現較軟的汽車密封條的前置噴塗工藝的實施。本發明的汽車密封條前置噴塗裝置包括箱體,在箱體上設有具有進口及出口的噴塗通道,與該噴塗通道連通設置有排風機構,該前置噴塗裝置還包括具有噴槍的噴塗機構,所述噴槍設於所述噴塗通道內,以及在噴塗通道的進口和出口處分別設置的可同步運轉的兩個傳送部,在噴塗通道內沿密封條膠條的運動方向間隔布置的多個轉動支撐部,和在噴塗通道的出口設置的、可於滑經噴塗通道的密封條膠條的兩相對側施加約束力,而對密封條膠條的運動進行導向的約束導向部,其中,相鄰轉動支撐部之間的距離設置為20~30cm。
本汽車密封條前置噴塗裝置通過傳送部、多個轉動支撐部以及約束導向部的設置,可使得密封條膠條按設定的位置通過噴塗通道,能夠防止密封條膠條通過時因發生翻轉而出現劃傷問題,且相鄰轉動支撐部的距離設定為20~30cm,也可防止因轉動支撐部間距過大導緻密封條膠條出現下垂堆積和變形問題,從而可保證較軟的密封條膠條順利通過噴塗通道,並由噴槍進行噴塗而完成前置噴塗工藝。
基於如上的設計思想,本實施例的汽車密封條前置噴塗裝置的一種示例性結構由圖1結合圖2所示,箱體1為一方形結構,其沿密封條膠條24運動方向的兩端間的距離可在100~150cm之間,如可為120cm。在箱體1的底部安裝有可自鎖的萬向輪,以可用於裝置的移動,除了萬向輪,在箱體1的底部也設置有地腳,在箱體1移動至設定位置後,將萬向輪鎖定,再將地腳放好並調整好箱體1的水平便可。噴塗通道25即設置於箱體1的中部並靠近於箱體1的一側布置,噴塗通道25的進口和出口分別位於箱體1的兩端,箱體1具有噴塗通道25的一側可採用透明外殼,以可對噴塗過程進行觀察,而為便於觀察,在箱體1內的頂部也設置有照明燈5。
本實施例中與噴塗通道25相連通的排風機構包括形成於箱體1內的位於噴塗通道25的一側,並與噴塗通道25連通的排風通道26,還包括設置於箱體1外並與排風通道26相連通的排風機18。而位於噴塗通道25中的噴槍4固定在箱體1內的噴槍安裝支架3,且噴槍4為沿滑經噴塗通道25內的密封條膠體24的運動方向間隔布置的多個。本實施例中,噴槍4採用無針的低霧化氣壓噴槍,以此可使噴射壓力降低,而避免密封條膠條24被吹變形的問題。
前述的噴塗機構還包括與噴槍4相連的塗料供應單元以及壓縮氣體供應單元,其中塗料供應單元具體包括位於箱體1外的塗料料桶14,以及通過輸料管而分別連接於塗料料桶14和各噴槍4之間的蠕動泵15,蠕動泵15可與無針噴槍相適配。而壓縮氣體供應單元則包括與外部壓縮氣源連通的氣管,且在氣管上也串接有安裝在箱體1上的油氣分離器13,通過油氣分離器13可進一步保證壓縮氣體的品質,避免對噴塗造成影響,此外,在箱體1上也設置有串接於氣管上的氣壓表2及可對壓縮氣體壓力進行調節的調節閥件。
本實施例中為避免存儲於塗料料桶14中的塗料因室溫較高而發生交聯結塊的問題,在塗料料桶14內設置有冷卻機構,具體上塗料料桶14可採用具有中空夾層的雙層結構,冷卻機構即包括形成於塗料料桶14上的中空的夾層,以及與夾層相連通的進、出水管,進水管與外部的低溫水源連通,從而通過流經夾層的低溫水,便可實現對塗料料桶14內的降溫。本實施例中在塗料料桶14內也設置有對塗料進行攪拌的攪拌機構,該攪拌機構具體可採用電動攪拌,且攪拌速度可經由數顯變頻器控制而實現可調。
採用電動攪拌方式可解決塗料使用中因攪拌速度部穩定而造成塗料內產生氣泡或分層等問題。本實施例中進一步的,在塗料料桶14的底部還設置有可對塗料料桶14進行稱重的電子稱重機構,該電子稱重機構採用現有電子稱結構便可,而在箱體1上也設置有與該電子稱重機構聯接的重量報警單元。重量報警單元具體可為設置於箱體1頂部的聲光報警器20,在噴塗過程中當塗料料桶14內的塗料剩餘量到達設定的低值時,聲光報警器20即可發出聲光報警信號,以可實現對塗料餘量的自動監控,避免因塗料添加不及時而帶來斷料問題。
本實施例中前述的傳送部具體包括分別於噴塗通道25的進口及出口處設置在箱體1上的進口傳送帶6和出口傳送帶7,由圖3中所示,在箱體1上也分別設置有用於驅使進口傳送帶6及出口傳送帶7運轉的第一電機10和第二電機11。第一電機10和第二電機11由設於電控櫃16內的同一個控制器控制而實現同步轉動,而前述的轉動支撐部則具體為轉動設置於箱體1上的轉動支撐輥8,相鄰轉動支撐輥8間距20~30cm設置,如為22cm、25cm或28cm等。本實施例中在各轉動支撐輥8和出口傳送帶7處的第一電機10之間也設置有可承接第一電機10的轉動驅使,而使各轉動支撐輥8轉動的傳動部。
本實施例中所述傳動部具體為傳動連接於第一電機10的動力輸出端與各轉動支撐輥8之間的皮帶9,為適配於皮帶9,在第一電機10的動力輸出端以及各轉動支撐輥8的端部均套裝有皮帶輪。當然,除了採用皮帶傳動結構,第一電機10與各轉動支撐輥8之間的傳動也可採用鏈條傳動形式。此外,除了由第一電機10驅使各轉動支撐輥8,當然也可通過第二電機11對各轉動支撐輥8進行驅動。
本實施例中為避免塗料噴射於轉動支撐輥8上,而造成密封條膠體24與轉動支撐輥8之間摩擦阻力過大的麻煩,噴槍4的噴射方向也與轉動支撐輥8錯開布置,其具體可如圖1中所示,使噴槍4位於相鄰的轉動支撐輥8之間,或者是位於轉動支撐輥8與箱體1的內壁之間。為對粘附於轉動支撐輥8外周面上的塗料進行清理,並避免採用人工清理而可能出現的膠條劃傷、拉伸等問題,本實施例中在箱體1內對應於各轉動支撐輥8也設置有可對轉動中的轉動支撐輥8的外周面進行清理的清理機構。
如圖4中所示,本實施例中轉動支撐輥8可由位於兩側的轉動支撐輥安裝架22轉動設置於箱體1內,而清理機構則包括位於兩側的轉動支撐輥安裝架22之間,並安裝在箱體1上的刮板23,刮板23具有沿轉動支撐輥8軸向延展的寬度,且刮板23的端部也靠近於轉支撐輥8的外周面布置,從而在轉動支撐輥8轉動時,可通過刮板23實現對轉動支撐輥8上塗料的刮除。
本實施例中,在箱體1內於排風通道26和噴塗通道25之間也設置有塗料吸附件,該塗料吸附件具體可為設置在箱體1中的吸附棉17,吸附棉17實現了噴塗通道25和排風通道26之間的分隔,通過吸附棉17的吸附,可避免塗料進入排風機18而造成大氣汙染。為在吸附棉17吸附飽和後,便於對其進行更換,本實施例中在箱體1形成有噴塗通道25出口的一端也設置有吸附件更換口21,吸附件更換口21可為一卡扣在箱體1端部的蓋板,需要更換吸附棉17時拆下蓋板進行更換即可。而為增加箱體1的排風效果,在箱體1內位於排風通道26中還設置有一擋板19,擋板19擋置在吸附棉17上,以減小噴塗通道25與排風通道26之間的排風截面,進而增加對風塵的吸力。
本實施例中如圖5中所示,前述的約束導向部包括並排設置於箱體1上的兩個導向轉輥12,兩個導向轉輥12的轉動軸線與密封條膠條24的運動方向垂直,且兩個導向轉輥12之間的距離也是可調節的,其具體結構上,可為在箱體1上開設一與密封條膠條24的運動方向垂直的滑槽,並使兩個導向轉輥12經由螺栓副結構安裝在滑槽內,當需要調節兩個導向轉輥12之間的距離是,旋鬆螺母,移動兩個導向轉輥12使兩者間距離與密封條膠條24寬度適配後,再旋緊螺母便可。
本汽車密封條前置噴塗裝置在使用時,噴塗壓力設定在0.08~0.20bar之間,由擠出機擠出的密封條膠條24通過擠出機出口處的調整羅拉定型後,再通過進口傳送帶6進入噴塗通道25內,在噴塗通道25內各噴槍4對密封條膠條24進行均勻噴塗,噴塗後的密封條膠條24通過出口傳送帶7滑出噴塗通道,並經兩個導向轉輥12對運動方向進行導向。然後密封條膠條24進入硫化裝置內,進行微波、熱風硫化,硫化後冷卻、打碼、打孔,並收容即可。其中,為保證噴塗於密封條膠條24上的塗層中水分的有效揮發,以減少進入硫化裝置時因快速升溫引起氣泡現象,靠近於噴塗通道25出口的噴槍4與硫化裝置入口之間的距離應不小於0.5m。
以上所述僅為本發明的較佳實施例而已,並不用以限制本發明,凡在本發明的精神和原則之內,所作的任何修改、等同替換、改進等,均應包含在本發明的保護範圍之內。