一種複合材料增強金屬管道無損檢測裝置及方法與流程
2023-04-27 18:45:21 2
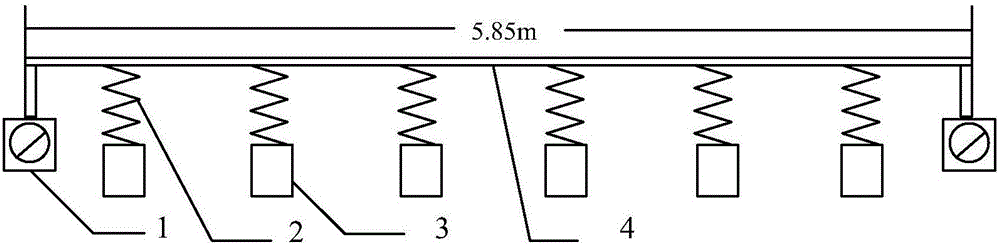
本發明屬於管道無損檢測領域,涉及一種複合材料增強金屬管道無損檢測裝置及方法。
背景技術:
隨著對管道輸送壓力及輸量要求的逐漸增高,提高管道承壓能力是一個重要的發展方向,基於此開發出了複合材料增強金屬管道的複合管道,通常使用纏繞等方法,將纖維與樹脂材料複合並包覆在金屬管道表面,從而提高管道的承壓能力,達到提高金屬管道輸送能力的要求。
目前針對此種管道的檢測方法除了目測法之外,主要是使用水壓爆破的方法,當爆破壓力達到設計要求即認為複合材料成型時工藝良好,複合材料中無明顯缺陷。此種方法局限於表徵單根管道的性能,並且檢測後樣品報廢,因此需要針對複合材料增強金屬管道開發出無損檢測方法。
複合管道的結構主要有金屬層和複合材料層,其中鋼管在複合前需要進行無損檢驗,通常使用的方法為X射線檢測或超聲等,針對金屬無損檢測的方法目前已經比較成熟。針對複合材料的無損檢測方法也主要延續了金屬材料的檢測,除了超聲波法和X射線法外,還包括計算機層析照相法、微波法、目視法等,但是由於複合材料本身固有的特性,這些方法大多適用於複合材料內部較大缺陷,在複合材料無損檢測方面都存在一定的局限性。
技術實現要素:
本發明的目的在於解決複合材料增強金屬管道的檢測問題,提供一種複合材料增強金屬管道無損檢測裝置及方法,該方法在複合管道加工的過程中對複合材料層進行無損檢測,不會對管體進行破壞。並針對此方法在管道上的應用,設計了聲發射傳感器的固定裝置。
為達到上述目的,本發明採用以下技術方案予以實現:
一種複合材料增強金屬管道無損檢測裝置,包括安裝於待測管道表面的支架杆,支架杆上安裝若干聲發射傳感器,支架杆的兩端分別設置開關式磁力座,支架杆的長度小於被測管道的長度,大於被測管道複合材料增強層的長度。
本發明進一步的改進在於:
聲發射傳感器通過彈簧連接在支架杆上,通過彈簧的壓緊作用將聲發射傳感器固定在被測管道表面。
在被測管道表面以0.5m為間隔,每個間隔處固定2個聲發射傳感器,且相隔180°。
相鄰兩個間隔處的聲發射傳感器沿管材徑向的夾角呈90°。
支架杆上共安裝22個聲發射傳感器。
一種複合材料增強金屬管道無損檢測方法,包括以下步驟:
1)複合材料增強鋼管樣管準備
以直徑508mm,長6m的鋼管為內襯,環氧樹脂E51和158B型玻璃纖維製成的複合材料增強鋼管道,其中鋼管壁厚9.5mm,複合材料厚4.6mm,複合材料層中樹脂含量為28%;管道靠近兩端15cm處為管道連接部分,在管道生產階段不進行增強層的纏繞;
2)安裝檢測裝置
將支架杆兩端的開關式磁力座吸附在被測管道末端未纏繞的鋼管表面,通過彈簧的壓緊作用,將聲發射傳感器固定在被測管道表面;
3)施加自緊壓力,聲發射信號記錄與分析
將被測管道兩端密封后加壓,加壓至25MPa時保壓1min後洩壓,記錄此過程的聲發射信號,觀察此過程聲發射信號圖;若出現50dB以下的信號,證明纖維與樹脂基體之間存在界面脫粘、分離現象,纏繞質量較差;測試完畢後卸除聲發射傳感器,卸除複合管,完成聲發射檢測及管道的自緊過程。
與現有技術相比,本發明具有以下有益效果:
本發明使用預應力法(自緊)處理複合結構管道,即將壓力增加至內層鋼管發生屈服,產生塑性變形後再將壓力卸載。此時,由於鋼管發生了塑性變形,外層的複合材料有殘餘的拉伸應力,內層的鋼管有殘餘的壓縮應力。當再次加壓時,複合材料承擔更高的載荷,鋼層與複合材料層之間的應力分配更均勻,預應力也是複合材料增強金屬管道成型的最後一個加工步驟。針對複合結構管道需要進行預應力處理這一特點,在此階段對管道進行聲發射檢測,並且由於預應力處理是複合管道首次受壓,此過程中會產生大量的聲發射信號,這些信號在一定程度上可以反應管道外層複合材料層的工藝質量及其它缺陷在此階段的擴展情況。預應力處理為單根複合結構管道成型的最後一個過程,在此過程中對其進行聲發射檢測不僅不會破壞管道結構,還節省了檢測時間。
【附圖說明】
圖1為本發明聲發射傳感器位置管道表面的展開圖;
圖2為本發明聲發射傳感器磁性支架的設計圖;
圖3為本發明的聲發射檢測信號幅值圖;
圖4為本發明纏繞質量較差時的聲發射檢測信號幅值圖。
其中:1-開關式磁力座;2-彈簧;3-聲發射傳感器;4-支架杆。
【具體實施方式】
下面結合附圖對本發明做進一步詳細描述:
參見圖1和圖2,本發明複合材料增強金屬管道的無損檢測裝置,在管材加工期間使用聲發射的方法對複合管進行無損檢測,並配合管材形狀及尺寸,使用特製的傳感器支架。聲發射探頭通過彈簧連接在支架上,彈簧的長度、剛度、最大預壓量可調節,保證傳感器與管體的緊密連接。傳感器支架固定方法採用開關式磁力座,檢測結束後調整到無磁力狀態,方便將傳感器整體卸除。特製的傳感器支架可以根據管道長度進行調節,保證長度大於增強層長度,磁力座吸附在未纏繞的接頭部分。開關式磁力座可根據傳感器數量,並配合使用的連接彈簧,確定磁力強度,保證測試過程中傳感器的固定。聲發射檢測纏繞層質量根據信號幅值圖確定,如在低幅值,即50dB以下出現大量信號點,纏繞層質量較差。
本發明複合材料增強金屬管道的無損檢測方法,包括以下步驟:
(1)複合材料增強鋼管樣管準備
以直徑508mm,長6m的鋼管為內襯,環氧樹脂E51和158B型玻璃纖維製成的複合材料增強鋼管道,其中鋼管壁厚9.5mm,複合材料厚4.6mm,複合材料層中樹脂含量為28%。管道靠近兩端15cm處為管道連接部分,在管道生產階段不進行增強層的纏繞。
(2)聲發射傳感器位置設計
在管道表面以0.5m為間隔,每個間隔處固定聲發射傳感器2個,相隔180°,相鄰兩個間隔處的傳感器相互呈90°,如圖1所示,共22個傳感器。此設計是在大量實驗基礎上制定的,傳感器之間的距離保證了聲發射探頭對管道的全部覆蓋。
(3)聲發射傳感器固定支架的設計
為了在最短的時間內完成對管道的檢測,應減少傳感器的安裝固定時間,對鋼管進行聲發射檢測時,每個傳感器配置一個磁性基座,將傳感器直接吸附在鋼管表面。而在本測試系統中,由於複合材料層無磁性並且厚度較厚,使用普通的磁性基座不能將傳感器可靠地固定在管道表面,使用膠帶固定的方法又需要較長的準備時間,因此設計出一種傳感器基座,如圖2所示。
基座的基本結構為一個長杆,按照上述傳感器的距離固定彈簧,傳感器通過彈簧的壓緊作用固定在管道表面。由於複合材料增強鋼管的兩端15cm處為接頭部分,表面無纏繞層,因此支架杆的長度小於被測管道,大於複合材料增強層的長度,為5.85m。在基座長杆的兩頭安裝開關式磁力座,一方面通過磁性傳感器可吸附在管道未纏繞的鋼管表面,另一方面當檢測結束後方便傳感器的拆卸,若管道長度或直徑增加,傳感器數量也隨之增加,支架兩端所需的磁性也會提高,高磁性會增加基座拆卸的難度,因此選擇開關式磁力座,減少操作時間。
(4)施加自緊壓力,聲發射信號記錄與分析
傳感器安裝好後,將管道兩頭密封后加壓,加壓至25MPa時保壓1min後洩壓,記錄此過程的聲發射信號,
觀察此過程聲發射信號圖,如圖3所示。圖3截取了4個聲發射信號探頭測得的聲發射信號,從圖中可以看出,所有信號出現在50dB以上,無低幅值信號。根據聲發射在複合材料方面的研究,不同類型缺陷的聲發射信號強度一般為:纖維斷裂的強度≥基體開裂的強度≥脫粘的信號強度,因此高幅值信號主要源自基體的開裂以及少量纖維的斷裂,如果出現很多低幅值信號,即在50dB以下的信號,證明纖維與樹脂基體之間存在界面脫粘、分離現象,纏繞質量較差,信號圖如圖4所示。
測試完畢後卸除聲發射傳感器,卸除複合管,完成聲發射檢測及管道的自緊過程。
本發明的原理:
聲發射是通過接收和分析材料的聲發射信號來評定材料性能或結構完整性的無損檢測方法。材料在塑性變形或損傷破壞的過程中會釋放應變能,同時產生應力波,這種信號可以通過聲發射設備的傳感器進行接收,並通過系統軟體進行信號處理和缺陷分析。纖維增強複合材料的主要聲發射來源包括基材開裂、纖維斷裂、纖維與基體分離、分層等損傷機制。
對於複合材料增強金屬管道,目前使用最多的複合材料是玻璃纖維增強環氧或不飽和聚酯等熱固性樹脂。玻璃纖維複合材料的模量為35-45GPa,鋼的模量為206GPa,兩個結構層之間的模量相差較大,因此在內壓力作用下,複合材料承載較低,其增強作用不易發揮。為了解決這一問題,使用預應力法(自緊)處理複合結構管道,即將壓力增加至內層鋼管發生屈服,產生塑性變形後再將壓力卸載。此時,由於鋼管發生了塑性變形,外層的複合材料有殘餘的拉伸應力,內層的鋼管有殘餘的壓縮應力。當再次加壓時,複合材料承擔更高的載荷,鋼層與複合材料層之間的應力分配更均勻,預應力也是複合材料增強金屬管道成型的最後一個加工步驟。
針對複合結構管道需要進行預應力處理這一特點,在此階段對管道進行聲發射檢測,並且由於預應力處理是複合管道首次受壓,此過程中會產生大量的聲發射信號,這些信號在一定程度上可以反應管道外層複合材料層的工藝質量及其它缺陷在此階段的擴展情況。預應力處理為單根複合結構管道成型的最後一個過程,在此過程中對其進行聲發射檢測不僅不會破壞管道結構,還節省了檢測時間。
以上內容僅為說明本發明的技術思想,不能以此限定本發明的保護範圍,凡是按照本發明提出的技術思想,在技術方案基礎上所做的任何改動,均落入本發明權利要求書的保護範圍之內。