一種改善腐蝕環境下鎂合金疲勞性能的表面處理方法與流程
2023-04-27 10:23:17 2
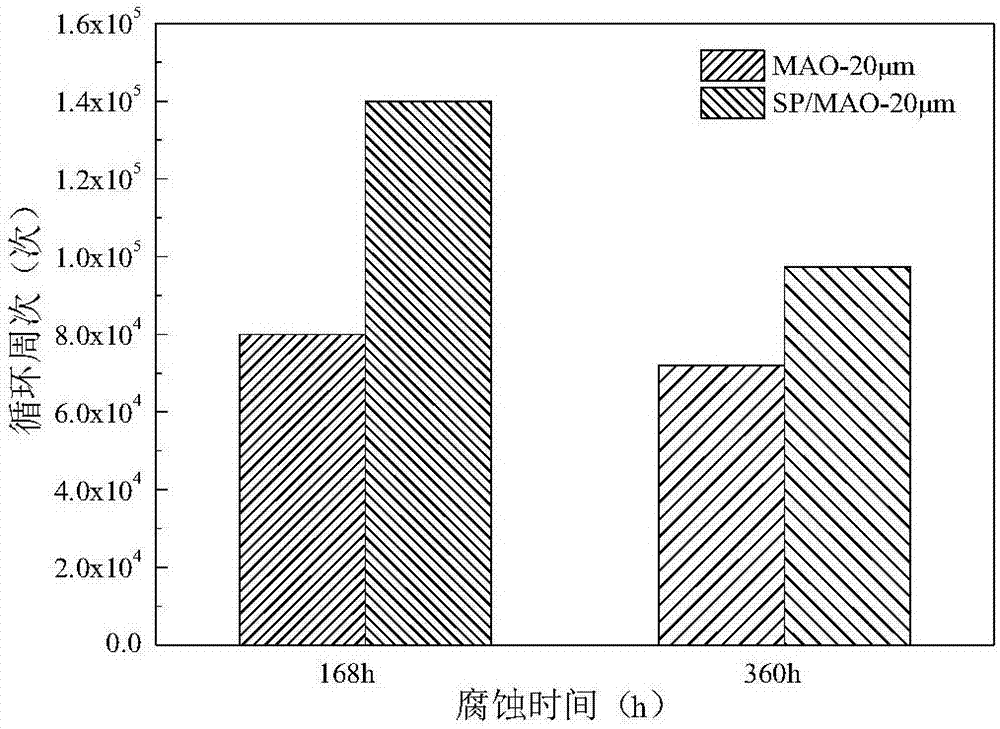
本發明屬於金屬材料表面改性技術領域,涉及一種改善腐蝕環境下鎂合金疲勞性能的表面處理方法。
背景技術:
鎂合金密度介於1.75-1.85g/cm3之間,比強度、比剛度高,比彈性模量與高強度鋁合金、合金鋼相當。其彈性模量絕對值較低,當受到外力作用時,應力分布更為均勻,可避免過高應力集中。在彈性範圍內承受衝擊載荷時,所吸收的能量比鋁高50%左右;其阻尼性能好,適宜製備抗震零部件。與當前用途最廣的輕金屬鋁合金相比,鎂合金不但更輕,散熱性能好、屏蔽電磁幹擾性能好,而且抵抗振動和降低噪聲能力也非常高。最為關鍵的是鎂合金在我國資源豐富,易回收處理。基於以上特性,鎂合金在航空、航天領域有良好的發展前景。
對於飛機結構,在使用中承受著不同大小和頻次的交變載荷,交變載荷作用下疲勞是主要失效方式,根據我國對飛機使用情況的統計,發現與結構強度有關的事故中,有80%是由疲勞失效引起的。然而鎂及鎂合金的比強度雖然較高,其強度較其它金屬材料而言卻較低;而且鎂合金化學活性大,相對其他常見金屬材料而言,鎂合金的電極電位負,Hilbert和Wagner等研究表明即使在大氣環境中鎂合金也易發生腐蝕,而這些腐蝕坑會成為裂紋源,加速鎂合金疲勞失效。鎂合金即使在大氣環境下使用也需要進行表面處理。因此,較差的耐蝕性能會顯著降低鎂合金的疲勞性能。可見,鎂合金的腐蝕性能是限制其作為結構材料應用的首要原因。
目前改善鎂合金耐蝕性的表面技術常見的包括有機層塗覆、化學鍍及化學轉化膜技術等。但有機材料的力學性能較差,其良好的耐蝕性是建立在一定厚度的基礎上(基本都在30μm以上),這樣的厚度對零件的工件尺寸、裝配工藝都有一定的限制性。因此,這種技術對鎂合金疲勞性能的改善作用有限。鎂合金表面化學鍍及化學轉化膜可有效改善表面力學和腐蝕性能,但這些技術又存在工藝複雜、工藝穩定性差、環保性差等問題,同時對鎂合金的牌號及熱處理狀態有較強的選擇性。更為重要的是化學鍍和化學轉化膜在鎂合金表面往往產生拉應力,這對其疲勞壽命有負面影響,因此多數文獻認為大多數化學鍍層對鎂合金表面力學性能及耐蝕性能的提高是以損失鎂基體的強度為代價的。而且,相對鎂合金而言,現有的鍍層均為陰極鍍層,一旦出現點蝕後,這種陰極鍍層加速了鎂合金的腐蝕,導致鎂合金腐蝕程度加劇,而鎂合金應力集中又會加速疲勞,特別是腐蝕疲勞壽命的失效。
微弧氧化技術可有效提高鎂合金的耐腐蝕性能已得到公認。微弧氧化技術是通過電解液與相應電參數的結合,利用試樣表面弧光放電增強並激活在金屬陽極上發生的氧化反應,在鎂合金表面原位生長出MgO陶瓷層。相對於其他表面技術,硬質陶瓷層與基體的結合較好,而膜基結合是陶瓷層改善力學性能的前提;其次,由於等離子體放電通道內溫度高達8000K,這種瞬間的高溫反應過程使微弧氧化陶瓷層存在一個燒結過程,陶瓷層中孔洞以盲孔為主。因此,與其他電化學方法相比,陶瓷層的耐腐蝕、耐磨損、耐熱性等要優於陽極氧化技術。第三,陶瓷層的生長是以氧原子向內擴散為主,對機械零件的尺寸影響較小;且與其他鍍層材料相比,MgO陶瓷層的電極電位與鎂合金最為接近,理論上可最大限度的降低鍍層與鎂基體的電偶腐蝕作用,有利於鍍層的保護作用;最後,陶瓷層的高硬度對鎂合金的疲勞性能也有良好的改善作用。疲勞斷裂往往從表面、或次表面層開始,與鎂基體相比,陶瓷層的高強度和硬度對於裂紋的萌生都有一定的阻礙作用。
微弧氧化降低鎂合金的疲勞性能,其本質原因是由於MgO陶瓷層生長過程中的PBR值小於1,同時,MgO和Mg基體的彈性模量及熱膨脹係數不同,在微等離子體的燒熔及冷淬過程導致鎂基體上產生了較大的熱損傷及殘餘拉應力,鎂合金微弧氧化試樣的疲勞裂紋源又是在陶瓷層與金屬基體的界面處產生。因此,儘管MgO陶瓷層可以強化鎂合金的表面力學性能,但是由於成膜過程中對鎂基體的殘餘拉應力的增加使得微弧氧化處理後鎂合金的疲勞性能下降。
形變應力強化是提高金屬材料疲勞性能常見的表面強化方法,其主要作用是通過殘餘壓應力的提高抑制金屬基體中裂紋的擴展,從而提高金屬的疲勞性能。但是對於化學活性大的鎂合金,形變強化後,由於鎂合金的微結構中缺陷增加,化學活性增大,反而會促使表面腐蝕的發生,又增加了裂紋的萌生。因此,這種對於常用改善金屬材料的方法不適合於鎂合金。但是選用預形變/微弧氧化複合處理工藝對鎂合金進行表面處理,則理論上可以提高鎂合金的腐蝕疲勞壽命,原因是:首先,微弧氧化陶瓷層良好的耐蝕性能提高了鎂合金表面抗腐蝕性能,減小了鎂合金腐蝕裂紋源的產生;其次,預形變在基體表面施加宏觀殘餘壓應力,可以在隨後的過程與鎂合金微弧氧化過程產生的拉應力相互作用,抑制裂紋的擴展。因此,這種複合工藝可有效改善鎂合金的疲勞性能,特別是在腐蝕條件下鎂合金結構件的疲勞壽命。
技術實現要素:
本發明的目的是提供一種改善腐蝕環境下鎂合金疲勞性能的表面處理方法,用於改善Cl-腐蝕環境下鎂合金微弧氧化陶瓷層的耐蝕性。
本發明所採用的技術方案是,一種改善腐蝕環境下鎂合金疲勞性能的表面處理方法,具體按以下步驟實施:
步驟1,表面電解拋光:
將表面預處理後的鎂合金置於電解拋光溶液中,鎂合金作為陽極,不鏽鋼板作為陰極,電解拋光;
步驟2,形變強化處理:
對經步驟1拋光後的鎂合金進行噴丸強化處理,使鎂合金表面產生形變;
步驟3,微弧氧化處理:
將經步驟2形變強化處理的鎂合金置於微弧氧化電解液中,不鏽鋼作為陰極,鎂合金作為陽極,微弧氧化處理,得到鎂合金噴丸/微弧氧化複合處理試樣;
步驟4,封孔處理:
將經步驟3微弧氧化處理後鎂合金在矽酸鈉水溶液中進行封孔處理,然後清洗、烘乾、冷卻,即完成對於鎂合金的表面處理。
本發明的特點還在於,
步驟1中電解拋光溶液為磷酸和無水乙醇體積比為3:5的混合溶液。
步驟1中電解拋光時間為550~650s,電壓4~5V,電流0.1~0.2A。
步驟2中噴丸強化處理採用玻璃彈丸,噴丸強度為0.15N,覆蓋率為100%,噴丸得到的硬化層深度為100~120μm。
步驟3中微弧氧化電解液去離子水為溶劑,其中九水偏矽酸鈉的濃度為15~16g/L,氫氧化鉀濃度為8~9g/L,氟化氫銨濃度為18~20g/L,三乙醇胺濃度為5~6mL/L,EDTA-二鈉濃度為2~3g/L,PH=7~8。
步驟3中微弧氧化參數為:正負脈衝電壓分別為420~490V/90V,頻率為1000~2000Hz/800~1000Hz,佔空比10~20%/10%,級數比1:1。
步驟4中矽酸鈉水溶液的濃度為55~65g/L。
步驟4中封孔處理封孔溫度為90~100℃,封孔時間為10~20min。
本發明的有益效果是,
1.本發明通過預形變/微弧氧化複合處理技術有效提高了鎂合金在腐蝕環境下,特別是在含Cl-的腐蝕環境下的抗疲勞性能。
2.本發明通過對鎂合金表面進行預形變處理,形成一定深度的形變層,增加基體殘餘壓應力值,抑制了鎂合金的疲勞裂紋的萌生和擴展。
3.本發明通過預形變改善了鎂基體的微結構,顯著改善了陶瓷層的緻密性,提高了微弧氧化陶瓷層的耐蝕性能,且陶瓷層可以降低形變對鎂合金表面活性的影響,減小鎂合金表面的腐蝕坑等裂紋源的產生。
4.本發明通過預形變,提高了鎂合金微弧氧化陶瓷層的生長速率,降低微弧氧化電耗能。
附圖說明
圖1是本發明製備的不同厚度試樣預腐蝕360h後在83.5MPa應力幅作用下的疲勞壽命;
圖2是本發明製備的20μm厚度試樣預腐蝕168h和360h後在83.5MPa應力幅作用下的疲勞壽命;
圖3為本發明製備的20μm厚度試樣預腐蝕360h後在78MPa和83.5MPa應力幅作用下的疲勞壽命。
具體實施方式
下面結合附圖和具體實施方式對本發明進行詳細說明。
本發明提供了一種改善腐蝕環境下鎂合金疲勞性能的表面處理方法,具體按以下步驟實施:
步驟1,鎂合金表面形變強化:
1.1對鎂合金進行表面預處理:
使用400#,800#,1000#和2000#水砂紙在金相試樣預磨機上對鎂合金板材依次進行打磨,並對邊緣進行倒角處理,對打磨後的試樣採用酒精、去離子水進行超聲波清洗,然後用吹風機烘乾保存,得到預處理的試樣。
1.2鎂合金表面電解拋光:
將預處理後的鎂合金置於磷酸和無水乙醇體積比為3:5的混合溶液中,以不鏽鋼為陰極,試樣為陽極,在室溫條件下進行電解拋光,以去除預磨時所產生的機械應力。電解拋光時間為550~650s,電壓4~5V,電流0.1~0.2A。電解拋光完成後,立即用去離子水清洗試樣,隨後採用無水乙醇進行超聲波清洗。
1.3鎂合金形變強化處理:
形變強化處理選擇噴丸強化工藝,對步驟1.2中得到的電解拋光鎂合金進行噴丸處理,噴丸強度為0.15N所用彈丸為玻璃丸,覆蓋率為100%,得到的硬化層深度為100~120μm。
步驟2,微弧氧化處理:
2.1鎂合金微弧氧化處理:
將步驟1.3所得的噴丸預處理的鎂合金置於以去離子水為溶劑的電解液中,其中九水偏矽酸鈉的濃度為15~16g/L,氫氧化鉀濃度為8~9g/L,氟化氫銨濃度為18~20g/L,三乙醇胺濃度為5~6mL/L,EDTA-二鈉濃度為2~3g/L,PH=7~8。在雙脈衝電源模式下以不鏽鋼作為陰極,鎂合金試樣為陽極進行微弧氧化,處理時間為2~14min,其中正負脈衝電壓分別為420~490V/90V,頻率為1000~2000Hz/800~1000Hz,佔空比10~20%/10%,級數比1:1,得到預噴丸/微弧氧化複合處理的鎂合金樣品。
步驟3,封孔處理:
3.1封孔:
將步驟2.1得到的複合處理試樣在矽酸鈉水溶液中進行封孔處理,其中矽酸鈉的濃度為55~65g/L,封孔溫度為90~100℃,封孔時間為10~20min。
3.2清洗、乾燥:
將步驟3.1得到的複合處理試樣在去離子水中清洗,然後取出用烘乾後冷卻,即完成對於鎂合金的表面處理。
本發明通過採用玻璃丸對鎂合金進行噴丸強化處理,降低了彈丸對鎂合金造成的微裂紋、褶皺等損傷,避免了彈丸殘留導致的微弧氧化陶瓷層無法生長的情況;其次,通過預形變提高了鎂合金微弧氧化的耐蝕性,減小鎂合金表面的腐蝕坑等裂紋源的產生,且有效地提高了鎂合金在腐蝕環境下的疲勞性能;此外,預形變提高了微弧氧化的生長速率,節省了時間及電能源消耗的成本。
本發明通過對鎂合金進行微弧氧化處理形成微弧氧化陶瓷層可有效提高鎂合金的抗腐蝕性能,減小鎂合金表面的腐蝕坑等裂紋源的產生。預形變強化技術在鎂基體形成一定深度的形變層,增加基體殘餘壓應力值,抑制鎂合金的裂紋擴展。因此,預形變/微弧氧化複合處理技術在提高鎂合金特別是在強腐蝕環境下的疲勞性能。
並且本發明通過預形變改善了鎂基體的微結構,顯著改善了陶瓷層的緻密性,可提高微弧氧化陶瓷層的耐蝕性能。同時,形變後鎂合金微弧氧化陶瓷層的生長速率提高,還可降低微弧氧化電耗能。
實施例1
步驟1,對AZ31鎂合金表面進行預處理,去油、SiC砂紙打磨。將預處理的鎂合金在磷酸酒精混合溶液中室溫條件下進行電解拋光,電壓為4~5V,電流為0.1~0.2A,時間550~650s,隨後用超聲波進行清洗。對拋光後的樣品進行強度為0.15N的噴丸強化處理,彈丸採用玻璃丸,覆蓋率為100%,硬化層深度為100~120μm。
步驟2,將噴丸處理的鎂合金放入電解液中,其中九水偏矽酸鈉的濃度為15.41g/L,氫氧化鉀濃度為8.75g/L,氟化氫銨濃度為18g/L,三乙醇胺濃度為5mL/L,EDTA-二鈉濃度為2g/L,在雙脈衝電源模式下以不鏽鋼作為陰極,鎂合金試樣為陽極進行微弧氧化,時間分別為2min40sec、5min、14min,對應的正脈衝電壓分別為420V、450V、490V,負脈衝電壓為90V,正/負脈衝頻率為1000Hz/800Hz,佔空比10%/10%,級數比1:1,得到厚度為5μm、10μm、20μm的噴丸/微弧氧化複合處理樣品。
步驟3,將試樣放入矽酸鈉溶液中進行封孔,其中矽酸鈉的濃度為55g/L,封孔溫度為90℃,封孔時間為10min。
預腐蝕試驗:將微弧氧化試樣放入鹽霧箱中進行中性鹽霧腐蝕試驗,其中腐蝕環境為5wt.%NaCl,腐蝕時間為360h。
疲勞試驗:對預腐蝕後的試樣進行三點彎曲疲勞試驗,其中預加應力幅為83.5MPa,頻率為20Hz,應力比為0.2。
結果表明:如圖1所示,不同厚度試樣預腐蝕360h後在83.5MPa應力幅作用下的疲勞壽命,可見噴丸/微弧氧化試樣的疲勞壽命均高於微弧氧化試樣及AZ31鎂合金,因為噴丸/微弧氧化複合處理一方面提高了微弧氧化鎂合金的耐蝕性,減小鎂合金表面的腐蝕坑等裂紋源的產生,另一方面噴丸在基體表面施加壓應力,降低了鎂合金初期微弧氧化生長的拉應力,從而預噴丸/微弧氧化複合處理有效的提高了鎂合金在腐蝕環境下的疲勞壽命。
實施例2
步驟1,對AZ31鎂合金表面進行預處理,去油、SiC砂紙打磨。將預處理的鎂合金在磷酸酒精混合溶液中室溫條件下進行電解拋光,電壓為4~5V,電流為0.1~0.2A,時間550~650s,隨後用超聲波進行清洗。對拋光後的樣品進行強度為0.15N的噴丸強化處理,彈丸採用玻璃丸,覆蓋率為100%,硬化層深度為100~120μm。
步驟2,將噴丸處理的鎂合金放入電解液中,其中九水偏矽酸鈉的濃度為16g/L,氫氧化鉀濃度為9g/L,氟化氫銨濃度為20g/L,三乙醇胺濃度為6mL/L,EDTA-二鈉濃度為3g/L,在雙脈衝電源模式下以不鏽鋼作為陰極,鎂合金試樣為陽極進行微弧氧化,時間為13min50sec,對應的正/負脈衝為490V/90V,頻率為2000Hz/1000Hz,佔空比20%/10%,級數比1:1,得到厚度為20μm的噴丸/微弧氧化複合處理樣品。
步驟3,將試樣放入矽酸鈉溶液中進行封孔,其中矽酸鈉的濃度為60g/L,封孔溫度為95℃,封孔時間為15min。
預腐蝕試驗:將微弧氧化試樣放入鹽霧箱中進行中性鹽霧腐蝕試驗,其中腐蝕環境為5wt.%NaCl,腐蝕時間為168h和360h。
疲勞試驗:對預腐蝕後的試樣進行三點彎曲疲勞試驗,其中預加應力幅為83.5MPa,頻率為20Hz,應力比為0.2。
結果表明:如圖2所示,20μm厚度試樣預腐蝕168h和360h後在83.5MPa應力幅作用下的疲勞壽命,可見預腐蝕168h後噴丸/微弧氧化複合處理試樣的疲勞壽命比微弧氧化試樣提高了15.5%,預腐蝕360h後複合處理樣品的疲勞壽命比微弧氧化試樣提高了22.2%,腐蝕時間越長,噴丸/微弧氧化複合處理改善鎂合金疲勞性能的作用越明顯,同時說明了預噴丸對鎂合金微弧氧化耐蝕性的作用是顯著的。
實施例3
步驟1,對AZ31鎂合金表面進行預處理,去油、SiC砂紙打磨。將預處理的鎂合金在磷酸酒精混合溶液中室溫條件下進行電解拋光,電壓為4~5V,電流為0.1~0.2A,時間550~650s,隨後用超聲波進行清洗。對拋光後的樣品進行強度為0.15N的噴丸強化處理,彈丸採用玻璃丸,覆蓋率為100%,硬化層深度為100~120μm。
步驟2,將噴丸處理的鎂合金放入電解液中,其中九水偏矽酸鈉的濃度為15g/L,氫氧化鉀濃度為8g/L,氟化氫銨濃度為19g/L,三乙醇胺濃度為5.5mL/L,EDTA-二鈉濃度為2.5g/L,在雙脈衝電源模式下以不鏽鋼作為陰極,鎂合金試樣為陽極進行微弧氧化,時間為14min,對應的正/負脈衝為490V/90V,頻率為1000Hz/800Hz,佔空比10%/10%,級數比1:1,得到厚度為20μm的噴丸/微弧氧化複合處理樣品。
步驟3,將試樣放入矽酸鈉溶液中進行封孔,其中矽酸鈉的濃度為65g/L,封孔溫度為100℃,封孔時間為20min。
預腐蝕試驗:將微弧氧化試樣放入鹽霧箱中進行中性鹽霧腐蝕試驗,其中腐蝕環境為5wt.%NaCl,腐蝕時間為360h。
疲勞試驗:對預腐蝕後的試樣進行三點彎曲疲勞試驗,其中預加應力幅為78MPa和83.5MPa,頻率為20Hz,應力比為0.2。
結果表明:如圖3所示,20μm厚度試樣預腐蝕360h後在78MPa和83.5MPa應力幅作用下的疲勞壽命,可見在78MPa下的疲勞壽命明顯高於83.5MPa,且噴丸/微弧氧化試樣和微弧氧化試樣疲勞壽命差距稍有減小,說明此時疲勞以應力作用為主。