一種壓力洩放閥及醫療器械的氣路系統的製作方法
2023-04-23 03:56:06 1
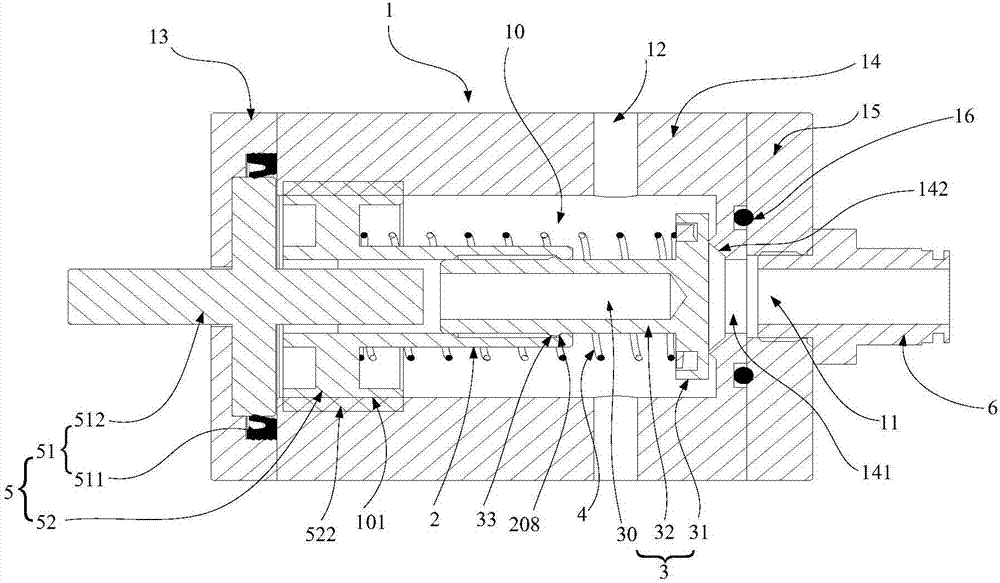
本發明屬於閥門領域,特別涉及一種壓力洩放閥及醫療器械的氣路系統。
背景技術:
壓力洩放閥是一種安裝於壓力容器或閥門管道等部件上的安全閥,當壓力容器或閥門管道的壓力值超過壓力洩放閥設定的數值時,該壓力洩放閥會自動開啟以排洩壓力,使壓力容器或閥門管道內的壓力不致繼續升高,保證了壓力容器或閥門管道的安全。當壓力容器或閥門管道內的壓力值降至一定數值時,壓力洩放閥再自動關閉。
在醫療器械或其他領域中,經常會使用到控制壓力較小(通常是指控制壓力在10-70mbar範圍內)的壓力洩放閥,例如針對麻醉機呼吸迴路的壓力安全控制、呼吸機呼吸迴路的壓力安全控制以及呼吸復甦設備的迴路壓力安全控制等領域,由於這些領域的壓力洩放閥的控制壓力較小,因此對控制精度的要求較高。
目前,主要採用彈簧式壓力洩放閥對壓力進行控制。彈簧式壓力洩放閥一般具有彈簧和實體閥芯,當壓力洩放閥外的氣體壓力值達到一定數值時,壓力洩放閥外的氣體會作用於壓力洩放閥的實體閥芯使其移動,並使彈簧壓縮,此時實體閥芯的移動使得壓力洩放閥打開,壓力洩放閥外的氣體從壓力洩放閥洩放,從而避免了壓力洩放閥外的氣體的氣壓值過高;當氣壓值降低到安全值時,壓縮彈簧會恢復形變使得實體閥芯回復到初始位置,彈簧式壓力洩放閥關閉。
當彈簧式壓力洩放閥水平安裝時,由於實體閥芯受到自身的重力作用向下偏移,導致彈簧式壓力洩放閥不在實際的設定壓力下開啟或關閉,會影響彈簧式壓力洩放閥的控制精度,因此,為保證控制精度,針對醫療器械或其他控制精度要求較高的領域,現有技術中彈簧式壓力洩放閥在使用時一般只能沿重力方向豎直安裝,使實體閥芯和彈簧均沿重力方向設置。然而,豎直安裝也帶來了一些問題:一方面,對某些體積受限的醫療設備而言,豎直安裝使得彈簧式壓力洩放閥佔用了更多的操作空間;另一方面,這也制約了彈簧式壓力洩放閥的使用範圍。
技術實現要素:
本發明的目的在於,提供一種壓力洩放閥,旨在解決現有技術中壓力洩放閥水平安裝時由於實體閥芯的重力作用導致的控制精度低的問題。
為解決上述技術問題,本發明提供了一種壓力洩放閥,包括:閥體,所述閥體具有一沿所述閥體延伸方向開設的第一內腔以及與所述第一內腔連通的進氣口和排氣口;閥芯支撐件,所述閥芯支撐件沿所述閥體的延伸方向固定於所述第一內腔內;以及閥芯,所述閥芯與所述閥芯支撐件之間通過軸孔間隙配合連接,且所述閥芯可沿所述閥體的延伸方向相對於所述閥芯支撐件滑動,所述閥芯用於封堵所述進氣口或使所述進氣口與所述第一內腔之間連通。
進一步的,所述閥芯支撐件具有一沿其延伸方向開設的第二內腔,所述閥芯的一部分通過軸孔間隙配合設置於所述第二內腔中。
進一步的,所述閥芯具有一沿其延伸方向開設的第三內腔,所述閥芯支撐件的一部分通過軸孔間隙配合設置於所述第三內腔中。
進一步的,所述壓力洩放閥還包括彈性元件,所述彈性元件設置於所述第一內腔內;當所述閥芯朝遠離所述進氣口的方向滑動時,所述彈性元件被所述閥芯壓縮,所述進氣口與第一內腔之間連通;當所述彈性元件恢復形變時,所述閥芯在所述彈性元件的作用下朝靠近所述進氣口的方向滑動並封堵所述進氣口。
進一步的,所述閥體包括第一閥蓋、閥殼和第二閥蓋,所述閥殼的一端與所述第一閥蓋連接,所述閥殼的另一端與所述第二閥蓋連接,所述第一閥蓋、閥殼和第二閥蓋圍合形成所述第一內腔,所述進氣口開設於所述第二閥蓋上並與所述第一內腔連通,所述排氣口開設於所述閥殼的側壁上並與所述第一內腔連通。
進一步的,所述第一閥蓋與所述閥殼的一端可拆卸連接,所述第二閥蓋與所述閥殼的另一端可拆卸連接或一體化設置。
進一步的,所述壓力洩放閥還包括彈性元件以及調節所述彈性元件形變量的調節機構,所述調節機構貫穿所述第一閥蓋並與所述閥芯支撐件連接;所述彈性元件設置於所述第一內腔內,所述彈性元件的兩端分別設置於所述調節機構和所述閥芯上,當所述閥芯朝遠離所述進氣口的方向滑動時,所述彈性元件被所述閥芯壓縮,所述進氣口與第一內腔之間連通;當所述彈性元件恢復形變時,所述閥芯在所述彈性元件的作用下朝靠近所述進氣口的方向滑動並封堵所述進氣口。
進一步的,所述彈性元件為彈簧,所述彈簧套設於所述閥芯支撐件和所述閥芯上,其兩端分別設置於所述調節機構和所述閥芯上。
進一步的,所述閥芯包括閥杆以及設置於所述閥杆一端的閥帽,所述閥杆的一部分通過軸孔間隙配合設置於所述第二內腔內,所述閥杆的另一部分以及所述閥帽延伸出所述第二內腔,所述彈性元件套設於所述閥芯支撐件和所述閥杆上,所述彈性元件的一端設置於所述閥帽上,另一端設置於所述調節機構上,所述閥帽用於封堵所述進氣口或使所述進氣口與所述第一內腔之間連通。
進一步的,所述閥殼靠近所述第二閥蓋的端部具有一連接接口,所述連接接口兩端分別與所述第一內腔和所述進氣口連通,所述閥帽用於封堵所述連接接口或使所述連接接口與所述第一內腔之間連通。
進一步的,所述第一內腔與所述連接接口的交界面上設有一第一環狀突起,所述閥帽為圓柱體,所述第一環狀突起的直徑大於所述連接接口的直徑且小於所述閥帽的直徑,所述閥帽用於與所述第一環狀突起密封接觸或與所述第一環狀突起分離不接觸。
進一步的,所述調節機構包括調節部和旋轉部,所述調節部的一端貫穿所述第一閥蓋安裝於所述旋轉部的一端,所述旋轉部的另一端與所述閥芯支撐件連接,所述旋轉部的另一端設有一與所述彈性元件相匹配的凹槽,所述彈性元件的另一端設置於所述凹槽中,所述調節部用於調節所述旋轉部使其沿所述閥體的軸向來回往復運動。
進一步的,所述調節部包括調節阻尼環和調節杆,所述調節杆的一端貫穿所述第一閥蓋安裝於所述旋轉部的一端,所述調節阻尼環套設於所述調節杆的另一端上。
進一步的,所述旋轉部與所述閥芯支撐件一體化設置。
進一步的,所述旋轉部外表面設有外螺紋,所述第一內腔靠近所述第一閥蓋的部分具有與所述外螺紋相匹配的內螺紋,所述內螺紋的長度大於所述外螺紋的長度,所述旋轉部與所述閥體螺紋連接,所述調節部用於調節所述旋轉部的旋轉。
進一步的,所述旋轉部靠近其一端的部分開設有一孔洞,所述調節部的一端的形狀和尺寸與所述孔洞的形狀和尺寸相匹配並貫穿所述第一閥蓋設置於所述孔洞內,所述調節部的一端旋轉用於帶動所述旋轉部旋轉。
進一步的,所述孔洞的橫截面形狀為橢圓形、正多邊形或不規則形狀。
進一步的,所述閥芯採用聚四氟乙烯、尼龍和聚甲醛中的一種或幾種混合製成。
進一步的,所述閥芯支撐件與所述閥芯接觸的表面的表面粗糙度rz值小於3.2微米。
進一步的,所述閥芯與所述閥芯支撐件之間的軸孔間隙配合的間隙值為0-0.15mm。
進一步的,所述第二內腔為臺階狀圓柱體,其包括沿所述閥體延伸方向並遠離所述進氣口的第四子內腔和靠近所述進氣口的第五子內腔,所述第五子內腔的直徑大於所述第四子內腔的直徑,所述閥芯的一部分通過軸孔間隙配合設置於所述第四子內腔和所述第五子內腔內。
進一步的,所述第五子內腔與所述第四子內腔之間還包括過渡部位,所述過渡部位的直徑沿靠近所述第四子內腔的方向逐漸變小。
進一步的,所述第五子內腔遠離所述第四子內腔的部分設有一第二環狀突起,所述第二環狀突起的直徑等於所述第四子內腔的直徑。
進一步的,位於所述第五子內腔中的所述閥芯的外表面上設有一第三環狀突起,所述第三環狀突起的直徑大於所述第二環狀突起的直徑。
進一步的,所述第二環狀突起和/或所述第三環狀突起具有彈性。
本發明還提供了一種醫療器械的氣路系統,含有如上所述的壓力洩放閥,所述壓力洩放閥為水平放置。
進一步的,所述醫療器械繫統為麻醉機或呼吸機。
與現有技術相比,本發明提供了一種壓力洩放閥及醫療器械的氣路系統,所述壓力洩放閥通過設置閥芯支撐件,有效的解決了具有閥芯的壓力洩放閥在水平安裝過程中由於受到閥芯重力影響導致的控制精度低的問題,確保了壓力洩放閥可水平安裝,這樣可以為用戶節省出更多的操作空間,且水平安裝也使得壓力洩放閥的操作控制更符合一般的操作習慣,可應用於需要高精度控制的醫療器械或其他領域中。
其次,閥芯採用輕量且帶有自潤性的材料(如聚四氟乙烯)製成,可以進一步降低重力影響,提高壓力洩放閥的控制精度。
再者,閥芯支撐件的第二內腔採用高光潔內表面(表面粗糙度rz值小於3.2微米),可進一步降低閥芯與第二內腔之間的摩擦力,提高了壓力洩放閥在水平安裝時的控制精度。
另外,本發明還通過設置調節機構,可以對壓力洩放閥的開啟壓力進行定量控制。
附圖說明
圖1是本發明一實施例提供的一種壓力洩放閥的結構剖視圖示意圖;
圖2是本發明一實施例提供的一種壓力洩放閥的旋轉部與閥芯支撐件一體化設置時的結構示意圖;
圖3是本發明一實施例提供的一種壓力洩放閥的外觀示意圖;
附圖標記說明:
1-閥體;2-閥芯支撐件;3-閥芯;4-彈性元件;5-調節機構;6-進氣接口;10-第一內腔;101-內螺紋;11-進氣口;12-排氣口;13-第一閥蓋;14-閥殼;141-連接接口;142-第一環狀突起;15-第二閥蓋;16-密封圈;20-第二內腔;201-第四子內腔;202-第五子內腔;203-過渡部位;204-第二環狀突起;30-第三內腔;31-閥帽;32-閥杆;33-第三環狀突起;51-調節部;511-調節阻尼環;512-調節杆;52-旋轉部;521-凹槽;522-外螺紋;523-孔洞。
具體實施方式
以下結合附圖和具體實施例對本發明提出的一種壓力洩放閥及醫療器械的氣路系統作進一步詳細說明。根據下面說明和權利要求書,本發明的優點和特徵將更清楚。需說明的是,附圖均採用非常簡化的形式且均使用非精準的比例,僅用以方便、明晰地輔助說明本發明實施例的目的。附圖中相同或相似的附圖標記代表相同或相似的部件。
圖1是本發明一實施例提供的一種壓力洩放閥的示意圖。圖2是本發明一實施例提供的一種壓力洩放閥的旋轉部與閥芯支撐件一體化設置時的結構示意圖;圖3是本發明一實施例提供的一種壓力洩放閥的外觀示意圖。請參考圖1和圖2以及圖3,一種壓力洩放閥,包括閥體1、閥芯支撐件2和閥芯3;所述閥體1具有一沿所述閥體1延伸方向開設的第一內腔10以及與所述第一內腔10連通的進氣口11和排氣口12;所述閥芯支撐件2沿所述閥體1的延伸方向固定於所述第一內腔10內;所述閥芯3與所述閥芯支撐件2之間通過軸孔間隙配合連接,且所述閥芯3可沿所述閥體1的延伸方向相對於所述閥芯支撐件2滑動,所述閥芯3用於封堵所述進氣口11或使所述進氣口11與所述第一內腔10之間連通。在本實施例中,所述閥體為圓柱形,所述進氣口11可以設置於所述閥體1沿軸向的一端,所述排氣口12可以設置在所述閥體1垂直於其軸向的側壁上,氣體可以從所述排氣口12進入所述第一內腔10,然後從所述排氣口12流出所述第一內腔10。在另一實施例中,所述閥體10也可以為其他形狀,例如立方體或六邊形柱體等。
在本實施例中,所述閥芯3與所述閥芯支撐件2之間為軸孔間隙配合連接,兩者之間有間隙,所述閥芯支撐件2可以支撐所述閥芯3,使所述閥芯3能夠沿所述閥體1的延伸方向放置,當所述壓力洩放閥水平放置時,即可實現閥芯3在水平放置有所述閥芯支撐件2提供的支撐力,該支撐力可以抵消重力對於閥芯3的影響,避免了因重力引起的閥芯向下偏移,有利於提高壓力洩放閥水平安裝時的控制精度。
其中,所述閥芯3與所述閥芯支撐件2之間的軸孔間隙配合連接,可以是所述閥芯3套接在所述閥芯支撐件2的外部,所述閥芯3具有一沿其延伸方向開設的第三內腔30,所述閥芯支撐件2的一部分通過軸孔間隙配合設置於所述第三內腔30中。作為優選的,也可以是所述閥芯支撐件2套接在所述閥芯3的外部,所述閥芯支撐件2具有一沿其延伸方向開設的第二內腔20,所述閥芯3的一部分通過軸孔間隙配合設置於所述第二內腔20中。本實施例優選採用第二種方案,所述閥芯支撐件2套接在所述閥芯3的外部,這樣所述閥芯3的一部分可以容置在閥芯支撐件2內,使得所述閥芯支撐件2可以更好的提供支撐給所述閥芯3,減小閥芯3自身的重力影響。
所述閥體1可包括第一閥蓋13、閥殼14和第二閥蓋15,所述閥殼14的一端與所述第一閥蓋13連接,所述閥殼14的另一端與所述第二閥蓋15連接,所述第一閥蓋13、閥殼14和第二閥蓋15圍合形成所述第一內腔10,所述進氣口11開設於所述第二閥蓋15上並與所述第一內腔10連通,所述排氣口12開設於所述閥殼14的側壁上並貫穿所述閥殼141的側壁,使所述排氣口12與所述第一內腔10連通。所述第一閥蓋13與所述閥殼14的一端優選為可拆卸連接,所述第二閥蓋15與所述閥殼14的另一端優選為可拆卸連接或一體化設置。此處,所述閥殼14的一端和另一端是指所述閥殼14延伸方向上相對的兩端。
將所述第一閥蓋13所述閥殼14之間設置成可拆卸連接,當所述壓力洩放閥組裝時,打開所述第一閥蓋13,將所述第一內腔10內的組件安裝好後,即可連接所述第一閥蓋13與所述閥殼14。
所述排氣口12的數量可設置為一個或多個,例如在所述閥殼14上設置對稱的兩個排氣口12(即兩個排氣口12沿閥殼14徑向對稱分布),可以使所述第一內腔10中的氣體迅速排出,提高壓力洩放閥的靈敏度。
在本實施例中,所述第二閥蓋15與所述閥殼14之間可以通過螺釘連接,也可以為可拆卸連接或一體化設置(即二者是一體成型的),當然,所述第二閥蓋15與所述閥殼14也可以採用其他方式連接,本發明對此不予限制。較佳的,所述第二閥蓋15與所述閥殼14之間除所述進氣口11與所述第一內腔10連通的部位外,其餘部分均密封連接,例如通過在所述第二閥蓋15與所述閥殼14之間設置密封圈16來實現密封連接,這樣有利於防止所述進氣口11的氣體從所述第二閥蓋15與所述閥殼14的連接部位漏出,避免影響壓力洩放閥的控制精度。
另外,本實施例中還可以在所述第二閥蓋15遠離所述閥殼14的一端安裝一個與所述進氣口11連通的進氣接口6,設置所述進氣接口6的目的是為了使外界氣體管路方便的通過所述進氣接口6與壓力洩放閥安裝。
在本實施例中,所述壓力洩放閥還可以包括一彈性元件4,所述彈性元件4設置於所述第一內腔10內。所述彈性元件4可以設置在所述閥芯3的外圍,本實施例中,所述彈性元件環繞所述閥芯3設置,兩端分別設置於所述閥芯3上和所述閥體1遠離所述進氣口11的部分上。
當所述閥芯3朝遠離所述進氣口11的方向滑動時,所述彈性元件4被所述閥芯3壓縮並且隨著所述閥芯3朝遠離所述進氣口11的方向移動,所述進氣口11與第一內腔10之間連通;當所述彈性元件4恢復形變時,所述閥芯3在所述彈性元件4的作用下朝靠近所述進氣口11的方向滑動並封堵所述進氣口11。所述彈性元件4壓縮時可以給所述閥芯3提供作用力,該作用力與所述進氣口11處的氣體提供給所述閥芯3的壓力相抵消,限制閥芯3無限制的朝遠離進氣口11的方向運動;另一方面,當所述進氣口11處的氣體壓力減小時,所述彈性元件4可以恢復形變提供推力給所述閥芯3,推動所述閥芯3復位至封堵所述進氣口11。在另一實施例中,所述彈性元件4也可以設置在所述閥芯3與所述進氣口11之間,其兩端分別設置在所述閥芯3上和所述閥體靠近所述進氣口11的部分上。
繼續參考圖1所示,所述壓力洩放閥還可包括調節所述彈性元件4形變量的調節機構5,所述調節機構5貫穿所述第一閥蓋13並與所述閥芯支撐件2連接。所述彈性元件4分別設置於所述調節機構5和所述閥芯3上。當所述閥芯3朝遠離所述進氣口11的方向滑動時,所述彈性元件4被所述閥芯3壓縮,所述進氣口11與第一內腔10之間連通;當所述彈性元件4恢復形變時,所述閥芯3在所述彈性元件4的作用下朝靠近所述進氣口11的方向滑動並封堵所述進氣口11,使所述進氣口11與所述第一內腔10之間密封不連通。其中,所述彈性元件4的兩端既可以與所述閥芯3和所述調節機構5連接固定在一起,也可以僅與所述閥芯3和所述調節機構5接觸設置處於不連接固定的狀態。
調節結構5的設置是為了調節彈性元件4的初始形變量,這樣可以根據需要設置壓力洩放閥的開啟壓力,例如,當利用調節機構5調節彈性元件4使其壓縮後,彈性元件4會朝靠近所述進氣口11方向施加壓力給所述閥芯3,這樣,只有當進氣口11的進氣壓力大於彈性元件4施加的壓力時,所述閥芯3才會朝遠離所述進氣口11的方向移動,從而使得進氣口11與所述第一內腔10連通,由於所述第一內腔10與排氣口12連通,氣體將通過所述排氣口12排出,從而完成了壓力洩放閥開啟洩放氣體的工作,因此,調節機構5的作用就是為了調節彈性元件4的形變量,從而設定壓力洩放閥的開啟壓力。
作為一個非限制性的例子,所述彈性元件4可以為彈簧,所述彈簧套設於所述閥芯支撐件2和所述閥芯3上,其兩端分別設置於所述調節機構5和所述閥芯3上。具有彈簧的壓力洩放閥可稱之為彈簧式壓力洩放閥,本實施例中的彈簧式壓力洩放閥設置了閥芯支撐件2,可實現水平安裝且具有較高的控制精度。相對於壓力先導式安全洩放閥而言,具有閥芯的彈簧式壓力洩放閥的閥總體結構更加緊湊集成,且可實現水平安裝,增加了該類具有實體閥芯的壓力洩放閥的優勢和使用範圍。
所述閥芯3可包括閥杆32以及設置在所述閥杆32一端的閥帽31。所述閥杆32的一部分通過軸孔間隙配合設置於所述第二內腔20內,所述閥杆32的另一部分以及所述閥帽31延伸出所述第二內腔20,所述彈性元件4(如彈簧)套設於所述閥芯支撐件2和所述閥杆32上,所述彈性元件4(如彈簧)的一端與設置於所述閥帽31上,可以與所述閥帽31連接固定,也可以僅與所述閥帽31接觸設置,接觸設置同樣可以使得所述閥帽31能夠提供作用力給所述彈性元件4使其壓縮,另一端設置於所述調節機構5上,所述閥帽31用於封堵所述進氣口11或使所述進氣口11與所述第一內腔10之間連通。
所述閥帽31例如是圓柱狀結構、矩形結構或者六角形結構,只要能夠實現閥芯3與進氣口11的密封即可。所述閥帽31的徑向尺寸大於所述彈性元件4(如彈簧)和所述進氣口11的徑向尺寸,以使所述彈性元件4能夠與所述閥帽31接觸,並在所述閥帽31朝遠離所述進氣口11的方向移動時,所述彈性元件4能夠被所述閥帽31壓縮,同時,在所述閥帽31朝靠近所述進氣口11的方向移動時,所述閥帽31能夠完全封堵住所述進氣口11。應理解,閥芯3不僅限於閥帽與閥杆的結構,只要閥芯3能夠實現封堵進氣口31以及閥芯3遠離進氣口31使進氣口31與所述第一內腔10連通即可,比如,所述閥芯3還可以為單獨的圓柱形結構,其直徑大於所述進氣口11的徑向寬度,同時,彈性元件4(如彈簧)與圓柱形的閥芯的端部連接,使圓柱形閥芯遠離所述進氣口11運動時,彈性元件4能夠被壓縮。
作為優選方案,本實施例中的所述閥芯3可以是空心的,以減輕閥芯3整體的重量,使得閥芯3在水平放置時受到的重力因素影響進一步減小。
請參考圖1,所述閥殼14靠近所述第二閥蓋15的端部具有一連接接口141,所述連接接口141兩端分別與所述第一內腔10和所述進氣口11連通,所述閥帽31用於封堵所述連接接口141或使所述連接接口141與所述第一內腔10之間連通。
具體來說,本實施例中所述閥帽31的尺寸大於所述連接接口141的尺寸。當所述閥芯3沿所述閥體1的延伸方向(軸向)朝靠近所述進氣口11的方向滑動時,所述閥帽31可以覆蓋並封堵所述連接接口141從而使所述連接接口141與所述第一內腔10之間密封不連通,從而使得所述進氣口11也與所述第一內腔10之間密封不連通;當所述閥帽31朝遠離所述進氣口11的方向移動時,所述連接接口141與所述第一內腔10之間連通,從而也使得所述進氣口11與所述第二內腔10之間連通。
在本實施例中,通過設置連接接口141,可以使得所述閥殼14與所述第二閥蓋15之間的接觸部位變得更小,這樣所述閥芯3的閥帽31隻需封堵住所述連接接口141後即可密封所述進氣口11和所述第一內腔10,利於所述閥殼14與所述第二閥蓋15之間的密封連接,防止進氣口11的氣體從連接部位漏出。
其中,在所述第一內腔10與所述連接接口141的交界面上可以設有一第一環狀突起142,所述第一環狀突起142的直徑大於所述連接接口141的直徑且小於所述閥帽31的尺寸,當所述閥帽31為圓柱體時,所述第一環狀突起142的直徑小於所述閥帽31的直徑。所述閥帽31用於與所述第一環狀突起142密封接觸或與所述第一環狀突起142分離不接觸。設置第一環狀突起142的目的是為了使閥芯3密封所述連接接口141時,閥芯3隻需與所述第一環狀突起142密封接觸即可實現將所述連接接口141密封,減小了接觸面積,進一步了加強密封效果。
本實施例中,所述調節機構5可包括調節部51和旋轉部52,所述調節部51用於調節所述旋轉部52以使其沿所述閥體1的軸向來回往復運動。具體的,所述調節部51的一端沿閥體1的軸向貫穿所述第一閥蓋13安裝於所述旋轉部52的一端,所述旋轉部52的另一端與所述閥芯支撐件2連接,所述旋轉部52的另一端設有一與所述彈性元件4相匹配的凹槽521,所述彈性元件4的另一端設置於所述凹槽521中。本實施例中通過所述旋轉部52的前進(即向靠近進氣口11的方向移動)對所述彈性元件4施加壓力,實現提高壓力洩放閥開啟壓力的目的,同時,所述旋轉部52後退(即向遠離進氣口11的方向移動)時,所述彈性元件4會逐漸恢復形變,實現降低壓力洩放閥開啟壓力的目的。
所述調節部51進一步可包括調節阻尼環511和調節杆512,所述調節杆512的一端貫穿所述第一閥蓋13安裝於所述旋轉部52的一端,所述調節阻尼環套511設於所述調節杆512的另一端上。設置所述調節阻尼環511,可以將壓力洩放閥的開啟壓力進行標定展示出來,進一步方便壓力洩放閥的使用。
本實施例中,所述旋轉部52與所述閥芯支撐件2一體化設置,即二者是一體成型的,使得結構更緊湊。應當注意,旋轉部52與所述閥芯支撐件2之間不限於一體化設置,也可以通過卡扣連接、焊接等方式使所述旋轉部52與所述閥芯支撐件2連接在一起即可,用來實現所述旋轉部52與所述閥芯支撐件2的同步運動。
結合圖1和圖2所示,所述旋轉部52外表面設有外螺紋522,所述第一內腔10靠近所述第一閥蓋13的部分具有與所述外螺紋522相匹配的內螺紋101,所述內螺紋101的長度大於所述外螺紋522的長度,所述旋轉部52與所述閥體1螺紋連接,所述調節部51用於調節所述旋轉部52旋轉。當所述調節部51用於調節所述旋轉部52旋轉時,可使得所述外螺紋522與所述內螺紋101之間匹配旋緊或旋鬆,從而實現所述旋轉部52在所述閥體1軸向方向上的直線運動,由於所述旋轉部52上的凹槽521與所述彈性元件4接觸設置,因此所述旋轉部52的直線運動會帶動所述彈性元件4壓縮或恢復形變。
主要參考圖2,所述旋轉部52靠近其一端的部分開設有一孔洞523,所述調節部51的一端的形狀和尺寸與所述孔洞523的形狀和尺寸相匹配,所述調節部51的一端貫穿所述第一閥蓋13進入所述孔洞523內,所述調節部51的一端旋轉用於帶動所述旋轉部52旋轉。所述孔洞523的橫截面形狀優選為橢圓形、正多邊形或不規則形狀,通過設置孔洞523,且將所述孔洞523的橫截面設置成非圓形,當所述調節部51旋轉時,由於所述孔洞523的形狀限制,所述調節部51旋轉會帶動所述旋轉部52旋轉。
優選方案中,所述閥芯3採用輕量且帶有自潤性的材料製成。所述閥芯3的質量越小,其受重力因素影響越小,同時帶有自潤性時,可以進一步減小閥芯3與所述閥芯支撐件2之間摩擦力,使得閥芯運動時受到外力幹擾因素大大降低,提高了壓力洩放閥的控制精度。典型的輕量且帶有自潤性特點的材料是聚四氟乙烯(ptfe)、尼龍和聚甲醛(pom),可以採用上述三種材料中的一種或幾種組合製成所述閥芯3,所述閥芯3優選採用聚四氟乙烯製成,當然,也可採用其他公知的輕量且帶有自潤性的材料製成所述閥芯3。
進一步的,所述閥芯支撐件2與所述閥芯3接觸的表面的表面粗糙度rz值小於3.2微米。將所述閥芯支撐件2與所述閥芯3接觸的表面設置成高光潔表面,可減小所述閥芯3與其之間的摩擦力,進一步提高壓力洩放閥的控制精度。
所述閥芯3與所述閥芯支撐件2之間的軸孔間隙配合的間隙值為0-0.15mm。將間隙值設置在0-0.15mm,可在保證加工精度的基礎上,儘可能的使得所述閥芯支撐件2能夠支撐所述閥芯3,使所述閥芯3保持水平,降低閥芯3在運動過程中受到的重力因素影響,提高壓力洩放閥的控制精度。
進一步的,所述第二內腔20優選為臺階狀圓柱體,其包括沿所述閥體延伸方向並遠離所述進氣口11的第四子內腔201和靠近進氣口11的第五子內腔202,所述第五子內腔202的直徑大於所述第四子內腔201的直徑,所述閥芯3的一部分通過軸孔間隙配合設置於所述第四子內腔201和所述第五子內腔202內。將所述第二內腔20設置成兩部分,並且所述第五子內腔202的直徑大於所述第四子內腔201的直徑,是為了進一步降低所述閥芯3與所述第二內腔20之間的接觸面積,設置於所述第二內腔20中的所述閥芯3分成了兩部分,一部分位於所述第四子內腔201中並與其接觸,所述第四子內腔201支撐所述閥芯3,另一部分位於所述第五子內腔202中,但由於所述第五子內腔202的直徑大於所述第四子內腔201和所述閥芯3的直徑,故位於所述第五子內腔202中的這部分閥芯處於懸空狀態,減小了所述閥芯3與所述第二內腔20之間的接觸面積,從而減小所述閥芯3與所述第二內腔20之間的摩擦力,提高壓力洩放閥的控制精度。
優選方案中,所述第五子內腔202與所述第四子內腔201之間還包括過渡部位203,所述過渡部位203的直徑沿靠近所述第四子內腔201的方向逐漸變小。過渡部位203的存在是為了使得所述第五子內腔202與所述第四子內腔201之間的分界面更加平滑,防止所述閥芯3的端部在運動過程中接觸到所述過渡部位203時受到過大的阻力影響。
其中,所述第五子內腔202遠離所述第四子內腔201的部分設有一第二環狀突起204,所述第二環狀突起204的直徑等於所述第四子內腔201的直徑。所述第二環狀突起204的作用是與所述第四子內腔201配合支撐所述閥芯3,使得位於所述第二內腔20中的閥芯部分的兩端均有支撐。
本實施例中,位於所述第五子內腔202中的所述閥芯3的外表面上設有一與所述第一環狀凸起204相匹配的第三環狀突起33,所述第三環狀突起33的直徑大於所述第二環狀突起204的直徑。所述第三環狀突起33的作用是對所述閥芯3進行限位,防止所述第三環狀突起33脫出所述第五子內腔202,從而可以控制所述閥芯3向靠近所述進氣口11方向運動的距離,防止所述閥芯3脫出所述第五子內腔202。
結合圖1及圖2,所述第二環狀突起204和/或所述第三環狀突起33採用彈性材料製成。將兩者中的一個或兩個設置成彈性材料製成,可以方便在安裝時,將所述第三環狀突起33經由所述第二環狀突起204擠入所述第四子內腔中。
本發明還提供了一種醫療器械的氣路系統,含有如上所述的壓力洩放閥,所述壓力洩放閥為水平放置。其中,所述醫療器械繫統優選為麻醉機或呼吸機。
綜上所述,本發明提供了一種壓力洩放閥,通過設置閥芯支撐件,有效的解決了具有閥芯的壓力洩放閥在水平安裝過程中由於受到閥芯重力影響導致的控制精度低的問題,確保了壓力洩放閥可水平安裝,這樣可以為用戶節省出更多的操作空間,且水平安裝也使得壓力洩放閥的操作控制更符合一般的操作習慣,可應用於需要高精度控制的醫療器械或其他領域中。
其次,閥芯採用輕量且帶有自潤性的材料製成,可以進一步降低重力影響,提高壓力洩放閥的控制精度。
再者,閥芯支撐件與閥芯接觸的表面採用高光潔表面,可進一步降低閥芯與閥芯支撐件之間的摩擦力,提高了壓力洩放閥在水平安裝時的控制精度。
另外,本發明還通過設置調節機構,可以對壓力洩放閥的開啟壓力進行定量控制。
上述描述僅是對本發明較佳實施例的描述,並非對本發明範圍的任何限定,本發明領域的普通技術人員根據上述揭示內容做的任何變更、修飾,均屬於權利要求書的保護範圍。