離合器壓盤自動料庫、自動上下料裝置及自動生產線的製作方法
2023-05-12 19:57:01 3
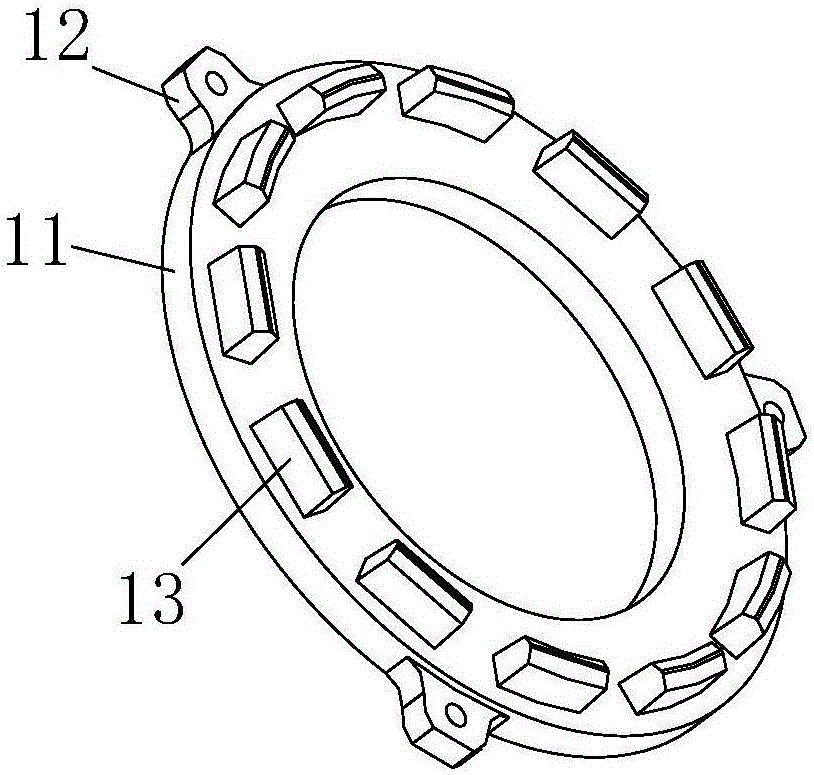
本發明涉及汽車零部件的生產加工,具體涉及離合器壓盤的自動料庫、自動上下料裝置及自動生產線。
背景技術:
離合器安裝在發動機和變速器之間,是汽車傳動系中直接與發動機相聯繫的總成件。參見圖1,現有一種離合器壓盤1包括呈中空盤狀的盤體11、一體均布在盤體邊緣用於安裝螺栓的若干支耳12及均布在盤體其中一個表面的圓弧凸塊13。
在生產這種離合器壓盤的過程中,需要將工件裝夾在工具機的夾具上才能進行加工,目前出現了各種機械手能夠從料庫中抓取工件及能夠將料庫中的零件推送至下一工序的自動送料機構,機械手能夠進行上料、下料,但是現有的料庫僅僅是一個平臺,工件採用疊放或並列放置的方式置於料庫的平臺上,機械手直接抓取零件,每次抓取工件,機械手的位置都會發生改變,下一次機械手抓取工件的軌跡會加長,使得機械手的抓取路徑過於複雜,導致機械手的內部控制程序相應較為複雜,機械手抓取工件所需的時間較長;而現有自動送料結構是利用氣缸或傳輸帶等將工件直接推送至下一工序,不適用於離合器壓盤這種需要裝夾在工具機上加工的工件;另外,離合器壓盤的兩個表面均有需加工的部位,但加工其中一個面時,工具機的夾具會擋住另一個面,使得被擋住的面只能進入下一道工序重新裝夾後才能加工,而目前,兩道工序之間只能利用人工改變裝夾面。
技術實現要素:
針對現有技術中所存在的不足,本發明的目的在於提供一種離合器壓盤自動料庫、自動上下料裝置及自動生產線,以簡化機械手的抓取路徑,縮短機械手抓取該離合器壓盤所需的時間,提高生產效率。
為實現上述目的,本發明採用了如下技術方案:
一種離合器壓盤自動料庫,包括:
機架;
凸輪分割器,所述凸輪分割器設置在機架上,所述凸輪分割器設有出力軸;
工件存儲組件,所述工件存儲組件包括水平設置的轉盤、圓周均布在轉盤上用於託起工件的託盤、設置在轉盤上用於限制託盤和工件滑動方向的導向限位件,所述轉盤同心設置在凸輪分割器的出力軸上並隨出力軸間歇性轉動,每個託盤上層疊放置有若干工件,所述導向限位件使得託盤和工件能夠沿導向限位件豎直滑動,每個託盤中心對應轉盤的位置上設有頂出孔;
頂升裝置,所述頂升裝置位於轉盤底部所在的一側,所述頂升裝置上設有可伸縮的頂杆,該頂杆在出力軸靜止狀態下與轉盤上的其中一個頂出孔的位置對應,該頂杆用於穿過與其位置對應的頂出孔並頂起對應的託盤和該託盤上的工件,使得託盤上最頂部的工件沿導向限位件滑動至指定位置供機械手抓取,並在抓取完成後收縮回位;
第一傳感器,所述第一傳感器設置在機架上,用於監測與頂杆對應的託盤最頂部的工件是否位於機械手的指定抓取位置;
及第二傳感器,所述第二傳感器設置在機架上,用於監測頂杆是否回位。
可選的,所述導向限位件包括至少三根垂直於轉盤表面的限位軸,所述限位軸固定在轉盤上,託盤上設有與限位軸位置和數量對應的託盤限位孔,限位軸穿過該託盤限位孔,各限位軸的連線構成的三角形中至少有一個三角形為銳角三角形或直角三角形,每根限位軸均與工件的內圈相切使得工件能夠沿限位軸上下滑動。
可選的,所述轉盤上設有用於安裝限位軸的U型孔,該U型孔的兩圓弧中心連線的延伸線穿過轉盤的迴轉中心,所述限位軸包括依次設置的軸頭、定位段和軸身段,所述定位段穿過頂出孔,定位段上配合設置有定位螺母,所述軸頭位於轉盤底部所在一側,該定位螺母位於轉盤另一側,所述定位段的外輪廓呈由兩個切面和兩個圓弧面構成的雙切邊圓柱狀,定位段兩側的切面與U型孔配合,定位段的圓弧面上設有與定位螺母配合的螺紋,所述圓弧段的兩切面之間的距離不小於軸身段的軸徑使得定位段和軸身段之間形成臺階,託盤置於該臺階上。
可選的,所述轉盤上設有用於防止工件自轉的防轉件。
可選的,所述防轉件包括槽鋼及用於將槽鋼豎直固定在轉盤上的過渡連接板,所述槽鋼一體焊接在過渡連接板上,所述過渡連接板安裝在轉盤上,每個工件中有一個支耳位於槽鋼的凹槽內。
可選的,所述轉盤上設有用於調節槽鋼與託盤中心距離的調節組件,每個槽鋼對應一組調節組件,所述調節組件包括用於使過渡連接板能夠靠近或遠離託盤中心連接板導向件及用於壓緊過渡連接板使其不能與連接板導向件產生相對位移的快速夾鉗;所述連接板導向件包括固定設置在轉盤上的兩根導軌,兩根導軌對稱設置在過渡連接板兩側,每根導軌上均設有用於卡入過渡連接板的導向槽。
可選的,所述機架上設有用於置換工件被抓取面的換面組件。
可選的,所述換面組件包括旋轉件、用於將立放的工件夾緊在旋轉件上的換面夾具、用於驅動旋轉件轉動的旋轉氣缸及用於將旋轉氣缸安裝在機架上的安裝件。
一種離合器壓盤自動上下料裝置,包括上述方案中任意一種離合器壓盤自動料庫及用於抓取自動料庫上指定位置的工件的機械手。
一種離合器壓盤自動生產線,包括設有上述任意一種設有換面組件的離合器壓盤自動料庫、用於加工離合器壓盤其中一個面的第一工具機、用於加工離合器壓盤其中另一個面的第二工具機及用於抓取工件的機械手。
相比於現有技術,本發明具有如下有益效果:
本發明的離合器壓盤自動料庫,可利用工件存儲組件有序的存放大量工件,並在凸輪分隔器和頂升裝置的共同作用下及時向指定位置補給工件,使得機械手每次抓取工件的位置均不變,抓取軌跡單一,簡化了機械手的抓取路徑,從而可簡化機械手內部的控制系統或控制程序,縮短了機械手抓取零件所需的時間。
本發明的離合器壓盤自動上下料裝置,利用自動料庫簡化機械手抓取路徑,提高了生產效率。
本發明的離合器壓盤自動生產線,利用自動料庫簡化機械手抓取路徑,提高了生產效率;還設有換面組件和兩臺工具機,使得該生產線不僅可以自動將離合器壓盤裝夾到第一工具機上加工壓盤的其中一個面,還能利用機械手將零件置於換面組件上換面後,直接裝夾到第二工具機上加工另一面,自動完成壓盤的雙面加工,減少了人力資本,並提高了生產效率。
附圖說明
圖1為離合器壓盤的結構示意圖;
圖2為本發明的結構示意圖;
圖3為凸輪分割器的結構示意圖;
圖4為工件存儲組件的結構示意圖;
圖5為託盤和工件的安裝結構示意圖;
圖6為轉盤的主視圖;
圖7為限位軸的結構示意圖;
圖8為頂升裝置的結構示意圖;
圖9為防轉件和調節組件的結構示意圖;
圖10為換面組件的結構示意圖;
圖11本發明的離合器壓盤自動上下料裝置、
圖12本發明的離合器壓盤自動生產線。
其中,1-離合器壓盤、2-機架、3-凸輪分割器、4-工件存儲組件、5-頂升裝置、6-第一傳感器支架、7-第二傳感器支架、8-換面組件、11-盤體、12-支耳、13-圓弧凸塊、31-出力軸、41-轉盤、42-託盤、43-導向限位件、44-防轉件、45-調節組件、51-頂杆、81-旋轉件、82-旋轉氣缸、83-安裝件、411-頂出孔、412-U型孔、431-限位軸、431a-軸頭、431b-定位段、431c-軸身段、441-槽鋼、442-過渡連接板、443-把手、451-導軌、452-快速夾鉗、451a-導向槽、841-換面限位件、842-換面氣缸、100-機械手、200-第一工具機、300-第二工具機、400-輸送線。
具體實施方式
下面將參考附圖來描述本發明所述的離合器某零件自動料庫、自動上下料裝置及自動生產線的實施例。
本實施例中,提供一種離合器壓盤自動料庫,參見圖2至圖5,包括:
機架2;
凸輪分割器3,所述凸輪分割器3設置在機架2上,所述凸輪分割器3設有出力軸31;
工件存儲組件4,所述工件存儲組件4包括水平設置的轉盤41、圓周均布在轉盤41上用於託起工件的託盤42、設置在轉盤41上用於限制託盤42和工件滑動方向的導向限位件43,所述轉盤41同心設置在凸輪分割器3的出力軸31上並隨出力軸31間歇性轉動,每個託盤42上層疊放置有若干工件,所述導向限位件43使得託盤42和工件能夠沿導向限位件43豎直滑動,每個託盤42中心對應轉盤41的位置上設有頂出孔411;
頂升裝置5,所述頂升裝置5位於轉盤41底部所在的一側,所述頂升裝置5上設有可伸縮的頂杆51,該頂杆51在出力軸31靜止狀態下與轉盤41上的其中一個頂出孔411的位置對應,該頂杆51用於穿過與其位置對應的頂出孔411並頂起對應的託盤42和該託盤42上的工件,使得託盤42上最頂部的工件沿導向限位件43滑動至指定位置供機械手抓取,並在抓取完成後收縮回位;
第一傳感器(圖未示),所述第一傳感器設置在機架2上,用於監測與頂杆51對應的託盤42最頂部的工件是否位於機械手的指定抓取位置;
及第二傳感器(圖未示),所述第二傳感器設置在機架2上,用於監測頂杆51是否回位。
其中,凸輪分割器3可採用電機驅動(圖未示,驅動方式不限於電機),利用現有技術控制出力軸每次轉動的時間間隔和單次轉動角度。將相鄰兩託盤分別與出力軸中心的連線構成的夾角定義為轉動角,若該轉動角等於凸輪分割器的單次轉動角度,則可實現轉盤上的工件在圓周方向上被均勻的抓取,使得轉盤的重心保持在轉盤的中心,轉盤能夠更平穩的隨出力軸轉動,提高自動料庫的可靠性。另外,該凸輪分割器3的安裝方式不限,可直接固定在機架2上,也可在機架2上設置一個安裝座,將凸輪分割器3安裝在該安裝座上,在具體實施過程中,可通過安裝不同高度的安裝座或是設置高度可調的安裝座,以改變轉盤41的高度。
其中,頂升裝置5可採用氣缸、油缸或電動推桿等裝置。
其中,第一傳感器可通過設置在機架2上的第一傳感器支架6安裝在機架2上,第二傳感器可通過設置在機架2上的第二傳感器支架7安裝在機架2上,
工作前,先將大量工件層疊放置在每個託盤上,利用導向限位件,使得託盤和工件的可滑動方向受限。
工作時,凸輪分割器3的出力軸31間歇性轉動,每次出力軸靜止時,轉盤41上均有一個頂出孔411的位置與頂升裝置5的頂杆51位置對應,也就是頂杆51正好位於其中一個託盤42下方,此時,頂杆51穿過該頂出孔411,對託盤42施加向上的推力,使得託盤42和託盤42上的工件豎直向上運動,當該託盤42頂部的工件到達指定位置時,第一傳感器反饋該信息,使得頂杆51停止上升;在機械手抓取該指定位置的零件後,該指定位置無工件,第一傳感器反饋該信息,可控制頂杆51收縮回位,當頂杆51端部也從頂出孔411退出後,第二傳感器反饋該信息,使得出力軸31轉動,當出力軸31停止轉動時,循環上述步驟。
本實施例的離合器壓盤自動料庫,能夠利用工件存儲組件4有序的存放大量工件,並在凸輪分割器3和頂升裝置5的共同作用下及時向指定位置補給工件,使得機械手每次抓取工件的位置均不變,抓取軌跡單一,簡化了機械手的抓取路徑,從而可簡化機械手內部的控制系統或控制程序,縮短了機械手抓取零件所需的時間。
在一個可選的實施例中,該導向限位件43包括至少三根垂直於轉盤41表面的限位軸431,限位軸431固定在轉盤41上,託盤42上設有與限位軸431位置和數量對應的託盤42限位孔,限位軸431穿過該託盤42限位孔,各限位軸的連線構成的三角形中至少有一個三角形為銳角三角形或直角三角形,每根限位軸均與工件的內圈相切使得工件能夠沿限位軸上下滑動。這種導向限位件結構簡單,便於加工。在具體實施過程中,也可選用其他結構形式的導向限位件,比如:在託盤42和工件外圍設置其他形狀的導向限位件。優化的,導向限位件包括三根限位軸,三根限位軸構成等邊三角形,可使得三根限位軸與工件之間的滑動摩擦力相等,從而使得導向限位件對工件的限位導向更為可靠。另外,該限位軸的截面可採用任意一種形狀,在一種可選的實施方式中,該限位軸的截面為圓形,使得限位軸與工件之間為線接觸,限位軸與工件之間的摩擦力較小,可減小工件演限位軸滑動過程中的阻力。
在一個可選的實施例中,該轉盤41上設有用於安裝限位軸431的U型孔412,該U型孔412的兩圓弧中心連線的延伸線穿過轉盤41的迴轉中心,該限位軸431包括依次設置的軸頭431a、定位段431b和軸身段431c,所述定位段431b穿過頂出孔411,定位段431b上配合設置有定位螺母(圖未示),軸頭431a位於轉盤41底部所在一側,該定位螺母位於轉盤41另一側,定位段431b的外輪廓呈由兩個切面和兩個圓弧面構成的雙切邊圓柱狀,定位段431b兩側的切面與U型孔412配合,定位段431b的圓弧面上設有與定位螺母配合的螺紋,所述圓弧段的兩切面之間的距離不小於軸身段431c的軸徑使得定位段431b和軸身段431c之間形成臺階,託盤42置於該臺階上。此時,轉盤41上設置的U型孔412使得限位軸431相對轉盤41迴轉中心的距離可調,使得該自動料庫能夠適用於大小不同的離合器壓盤的加工;;而該定位段431b呈雙切邊圓柱狀使得該定位段431b與U型孔412之間為面接觸,限位軸431與U型孔412之間的連接更為可靠。
在一個可選的實施例中,頂杆51裝置的頂杆51包括桿身和設置在桿身端部呈盤狀的頂出頭,這種形狀的頂杆51可增大頂杆51端部與託盤42的接觸面積,頂杆51對託盤42施加頂出力時,可使得頂出力更為均勻,能夠避免託盤42在頂出過程中卡滯,提高了設備的可靠性。優化的,該盤狀的頂出頭頂部同心設置有柱狀凸起,託盤42中心設有用於容納該柱狀凸起的容納孔,頂升過程中,該凸起伸入該容納孔內,可防止頂杆51與託盤42發生相對偏移,進一步提高了設備的可靠性。更為優化的,該柱狀凸起頂部設有倒角,頂升過程中,該倒角具有導向作用,柱狀凸起更易進入容納孔內,更可靠。
在一個可選的實施例中,轉盤41上設有用於防止工件自轉的防轉件44,能夠使得機械手每次抓取工件時,機械手卡爪張開的寬度一致,並可控制該寬度為與工件匹配的最小張開尺寸,從而能夠簡化機械手的程序,並縮短卡爪的行程,驅動機械手卡爪所需的能量相應減小,能夠達到節能的效果。
在一個可選的實施例中,該防轉件44包括槽鋼441及用於將槽鋼441豎直固定在轉盤41上的過渡連接板442,所述槽鋼441一體焊接在過渡連接板442上,所述過渡連接板442安裝在轉盤41上,每個工件中有一個支耳12位於槽鋼441的凹槽內。這種結構的防轉件44直接利用槽鋼441焊接在過渡連接板442上,利用的是已經成型的型材,無需額外加工凹槽,減少了製造防轉件44所需的工序,從而降低了成本。
在一個可選的實施例中,轉盤41上設有用於調節槽鋼441與託盤42中心距離的調節組件45,每個槽鋼441對應一組調節組件45。該調節組件45使得該自動料庫適用於外圍尺寸不同的離合器壓盤,能夠對度不同尺寸的離合器壓盤自轉,使得整個自動料庫的適用範圍更廣。
在一個可選的實施例中,該調節組件45包括用於使過渡連接板442能夠靠近或遠離託盤42中心連接板導向件及用於壓緊過渡連接板442使其不能與連接板導向件產生相對位移的快速夾鉗452;所述連接板導向件包括固定設置在轉盤41上的兩根導軌451,兩根導軌451對稱設置在過渡連接板442兩側,每根導軌451上均設有用於卡入過渡連接板442的導向槽451a,所述快速夾鉗452設置在過渡連接板442和導軌451之間。這種結構的調節組件45,可利用快速夾鉗452使得過渡連接板442能夠快速固定,也可快速鬆開,在需要加工不同尺寸的離合器壓盤時,利用這種結構調節組件45可縮短工作前的準備時間,提高了生產效率。具體的,該快速夾鉗452的結構可採用圖所示的結構,也可採用其他現有快速夾鉗452的結構。
在一個可選的實施例中,該導向槽451a由導軌451上的兩個直角面和轉盤41的頂面構成,使得過渡連接板442與轉盤41貼合,此時,過渡連接板442壓緊在轉盤41頂面上,能夠防止過渡連接板442因受到快速夾鉗452的壓力而變形。
在一個可選的實施例中,所述槽鋼441上一體設置有便於拉動防轉件44沿導向槽451a滑動的把手443,調節過程中更省力。
在一個可選的實施例中,所述機架2上設有用於置換工件被抓取面的換面組件8。該換面組件8能夠對改變工件朝向機械手的面,使得加工時能夠根據需求改變抓取面,離合器壓盤的兩個面上所需加工的部位均能夠自動在工具機上加工。
在一個可選的實施例中,所述換面組件8包括旋轉件81、用於將立放的工件夾緊在旋轉件81上的換面夾具、用於驅動旋轉件81轉動的旋轉氣缸82及用於將旋轉氣缸82安裝在機架2上的安裝件83。
在一個可選的實施例中,所述夾具包括設置旋轉件81上的換面限位件841及用於將工件壓緊在換面限位件841上的換面氣缸842。換面氣缸842包括固定設置在換面限位件841上的缸體和可伸縮的設置在缸體上的氣缸杆。換面時,機械手將工件立放在換面限位件841和換面氣缸842之間,氣缸杆伸出並將工件壓緊在限位件上,待壓穩後,旋轉氣缸82轉動換面,然後機械手抓取工件,同時氣缸回縮,完成換面。
本實施例中還提供了一種離合器壓盤自動上下料裝置,參見圖,該上下料裝置包括上述實施例和可選實施例中的任意一種離合器壓盤自動料庫及用於抓取自動料庫上指定位置的工件的機械手100。本實施例的離合器壓盤自動上下料裝置,利用自動料庫簡化機械手100抓取路徑,提高了生產效率。
本實施例中還提供了一種離合器壓盤自動生產線,包括設有上述任意一種設有換面組件8的離合器壓盤自動料庫、用於加工離合器壓盤其中一個面的第一工具機200、用於加工離合器壓盤其中另一個面的第二工具機300及用於抓取工件的機械手100。
工作時,機械手100先抓取轉盤41上指定位置的工件,將其裝夾到第一工具機200上加工其中一個面,待第一工具機200加工完畢後,將工件取下並置於換面組件8上換面,待換面完成後,再將其抓取到第二工具機300上加工另一個未加工的面。
本實施例的離合器壓盤自動生產線,利用自動料庫簡化機械手100抓取路徑,提高了生產效率;還設有換面組件8和兩臺工具機,使得該生產線不僅可以自動將離合器壓盤裝夾到第一工具機200上加工壓盤的其中一個面,還能利用機械手100將零件置於換面組件8上換面後,直接裝夾到第二工具機300上加工另一面,自動完成壓盤的雙面加工,減少了人力資本,並提高了生產效率。
在一個可選的實施例中,該離合器壓盤自動生產線還包括用於將已加工的工件送入下一工序的輸送線400。工作時,機械手100將加工完成的工件放入輸送線400進入下一工序,進一步提高了自動化程度,提高了生產效率。
最後說明的是,以上實施例僅用以說明本發明的技術方案而非限制,儘管參照較佳實施例對本發明進行了詳細說明,本領域的普通技術人員應當理解,可以對本發明的技術方案進行修改或者等同替換,而不脫離本發明技術方案的宗旨和範圍,其均應涵蓋在本發明的權利要求範圍當中。