一種氯乙酸反應釜事故應急處理系統的製作方法
2023-05-11 17:23:21 1
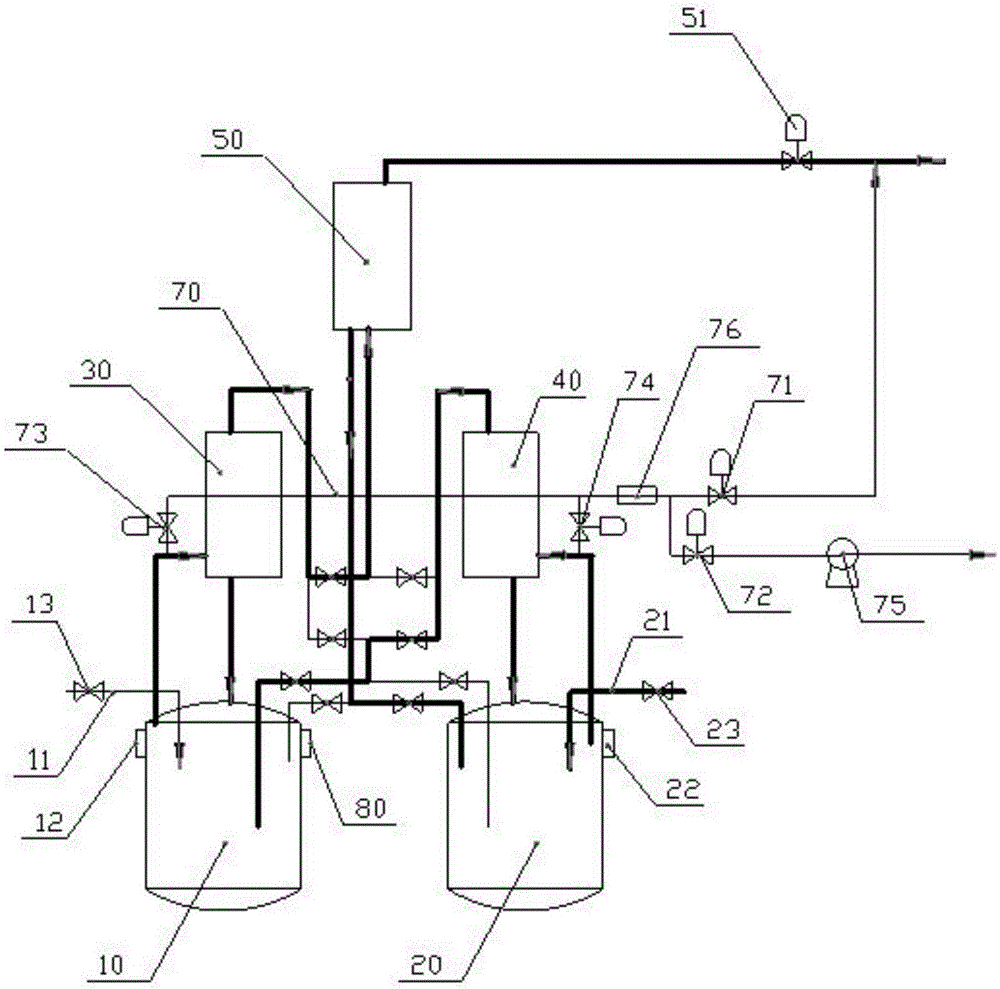
本發明涉及氯乙酸生產領域,尤其涉及一種氯乙酸反應釜事故應急處理系統。
背景技術:
氯乙酸是一種重要的有機化工中間體,廣泛用於醫藥、農藥、染料和多種有機化學產品生產中。隨著科學技術的進步和發展,氯乙酸新的應用領域將逐步得到開發,氯乙酸生產與市場前景非常看好。
目前,已經工業化的生產方法主要有三氯乙烯水解法、氯乙醯氯法以及乙酸催化氯化法三種。而三氯乙烯水解法和氯乙醯氯法由於原料來源有限且成本較高,故在我國均沒有得到應用,應用最多的是乙酸催化氯化法。
乙酸催化氯化法所用的催化劑主要有碘、紅磷、磺醯氯、硫磺粉、硫酸、氯磺酸、三氯化磷和乙酸酐等。其中,以乙酸為原料,用硫磺做催化劑,將氯氣通入乙酸中,進行氯化,氯化液經過結晶和甩濾得到氯乙酸產品,該法現今在國內普遍應用,是目前生產氯乙酸的主要方法,此生產方法的優點是原料乙酸供應充足,生產工藝簡單易行,生產投資少。
由於乙酸催化氯化反應時,反應釜的溫度較高,在70~110℃,會有部分未與乙酸反應的氯氣、乙酸蒸氣和副反應產物氯化氫氣體等溢出,為了提高有效原料的利用率以及副產物鹽酸的純度,所以要在反應釜的出氣口設置冷凝器,以便將氯氣和乙酸蒸氣冷凝成液體並回流至反應釜內再次利用。但是,冷凝器內一般為冷凍鹽水,冷凝器損壞後冷凍鹽水流至反應釜內,鹽水中的氨與氯氣在酸性條件下,反應生成三氯化氮,反應放熱,反應釜的溫度急劇升高,傳統夾套反應釜不能將反應產生的熱量及時有效的傳遞出去,使整個反應系統超壓,如果不能將反應釜內的壓力及時洩掉,會導致爆炸。在冷凝器損壞或其他因素造成反應釜壓力迅速升高後,工作人員需要第一時間穿上防化服進入現場,將尾氣排放閥門和氯氣調節閥關閉,打開與尾氣排放閥並聯的緊急事故排放閥,對系統管路進行抽真空處理,降低系統內壓力。但是,一旦出現更緊急嚴重的情況,人員將無法進入現場,會造成重大的人員傷亡及財產損失。
技術實現要素:
本發明所要解決的技術問題是提供一種氯乙酸反應的安全環境,當反應釜內壓力升高時,能自動切換管路閥門,實現對反應釜內洩壓,有效避免事故發生的一種氯乙酸反應釜事故應急處理系統。
為解決上述技術問題,本發明所採取的技術方案是:
一種氯乙酸反應釜事故應急處理系統,包括氯乙酸生產系統,其特徵在於:還包括應急切換系統;所述氯乙酸生產系統包括反應主釜、反應副釜、一級冷凝迴路、二級冷凝迴路和三級冷凝迴路;所述反應主釜的入口連接有向其內部通入氯氣的第一進氯管;所述一級冷凝迴路包括第一冷凝器,從所述反應主釜出氣口溢出的氣體進入第一冷凝器,經第一冷凝器冷凝成的液體回流入進反應主釜內,形成一級冷凝迴路;所述二級冷凝迴路包括第二冷凝器,從第一冷凝器出氣口溢出的氣體進入反應副釜內反應,從反應副釜出氣口溢出的氣體進入第二冷凝器,經第二冷凝器冷凝的液體回流進入反應副釜中形成二級冷凝迴路;所述三級冷凝迴路包括第三冷凝器,從第二冷凝器出氣口溢出的氣體進入第三冷凝器內,經第三冷凝器冷凝的液體回流入反應主釜中,形成三級冷凝迴路;從第三冷凝器出氣口溢出的氣體進入尾氣吸收系統;所述第一冷凝器與反應副釜、第二冷凝器與第三冷凝器以及第三冷凝器與反應主釜之間的連接管路上均設有切換閥門;所述應急切換系統包括應急管路和控制器;所述應急管路連接反應主釜的出氣口,應急管路上在反應主釜的出氣口處設有第一應急洩放閥,所述反應副釜的出氣口並聯於應急管路,且反應副釜的出氣口與應急管路之間的管路上設有第二應急洩放閥;所述應急管路的出口分出兩條並聯的支路,其中一條支路上設有超壓排放閥,且該支路出口與尾氣吸收系統連通,另一條支路上設有抽真空閥和真空泵,且該支路出口與事故尾氣吸收系統連通;所述第三冷凝器出氣口與尾氣吸收系統之間設有第一電磁閥;所述第一進氯管上設有第二電磁閥;所述反應主釜上設有檢測其內部壓力的第一壓力傳感器;所述控制器的信號輸入端連接第一壓力傳感器的信號輸出端,控制器的控制輸出端分別連接第一電磁閥、第二電磁閥、第一應急洩放閥、超壓排放閥、抽真空閥和真空泵。
進一步的技術方案在於:所述反應副釜的入口連接有向其內部通入氯氣的第二進氯管;所述第二冷凝器的出氣口還與反應主釜內腔的底部連通,從第二冷凝器出氣口溢出的氣體進入反應主釜內反應;所述第一冷凝器的出氣口與第三冷凝器的進氣口連接,從第一冷凝器出氣口溢出的氣體進入第三冷凝器內,第三冷凝器的冷凝出液端與反應副釜連通,經第三冷凝器冷凝的液體回流進入反應副釜內;所述第二冷凝器與反應主釜、第一冷凝器與第三冷凝器以及第三冷凝器與反應主釜之間的連接管路上均設有切換閥門;所述第二進氯管上設有第三電磁閥;所述反應副釜上設有檢測其內部壓力的第二壓力傳感器;所述控制器的信號輸入端還連接第二壓力傳感器的信號輸出端,控制器的控制輸出端還連接第二應急洩放閥。
進一步的技術方案在於:所述應急管路的末端設有壓力傳感器,所述壓力傳感器的信號輸出端連接控制器的信號輸入端,所述控制器的控制輸出端連接報警裝置。
進一步的技術方案在於:所述報警裝置為聲光報警器。
進一步的技術方案在於:所述反應主釜或反應副釜一側設有氯氣洩漏檢測探頭,所述氯氣洩漏檢測探頭的信號輸出端連接控制器的信號輸入端。
採用上述技術方案所產生的有益效果在於:
採用二級串聯氯化,對主反應釜內溢出的氣體進行多級吸收,提高了有效反應物的利用率以及副產物的純度;
在系統壓力急劇升高後,能夠自動切換管路閥門,實現對系統壓力直接洩壓,時間短效率高;並且,為了進一步提高副產物的收集,系統正常反應超壓(0.05~0.07Mpa)時,使主反應釜內壓力直接洩入尾氣吸收系統內,當系統內非正常超壓(超過0.07Mpa)時,兩個反應釜內的氣體藉助真空泵快速排入事故尾氣吸收系統,實現對壓力源直接洩壓,有效避免事故發生。
附圖說明
下面結合附圖和具體實施方式對本發明作進一步詳細的說明。
圖1是本發明的結構示意圖;
圖2是本發明的另一結構示意圖。
具體實施方式
下面結合本發明實施例中的附圖,對本發明實施例中的技術方案進行清楚、完整地描述,顯然,所描述的實施例僅僅是本發明的一部分實施例,而不是全部的實施例。基於本發明中的實施例,本領域技術人員在沒有做出創造性勞動前提下所獲得的所有其他實施例,都屬於本發明保護的範圍。
在下面的描述中闡述了很多具體細節以便於充分理解本發明,但是本發明還可以採用其他不同於在此描述的其它方式來實施,本領域技術人員可以在不違背本發明內涵的情況下做類似推廣,因此本發明不受下面公開的具體實施例的限制。
實施例1
如圖1所示,一種氯乙酸反應釜事故應急處理系統,包括氯乙酸生產系統,還包括應急切換系統;所述氯乙酸生產系統包括反應主釜10、反應副釜20、一級冷凝迴路、二級冷凝迴路和三級冷凝迴路。
在反應主釜10作為主反應釜,而反應副釜20與之串聯,從反應主釜10中溢出的氣體依次經過一級冷凝迴路回流、反應副釜20輔助反應吸收、二級冷凝迴路回流和三級冷凝迴路回流,從而進行有效反應物的回收。
具體的設備連接及反應如下:
所述反應主釜10的入口連接有向其內部通入氯氣的第一進氯管11,且反應主釜10內盛有乙酸和催化劑硫磺,在高溫和硫磺的催化作用下氯氣與乙酸反應生成產物氯乙酸和副產物氯化氫;由於反應主釜10的溫度在70~110℃,所以會有氣體(氯化氫54%、二氧化硫0.2%、氯氣32%和乙酸蒸氣13%和其它氣體0.8%)溢出;
所述一級冷凝迴路包括第一冷凝器30,從所述反應主釜10出氣口溢出的氣體進入第一冷凝器30,經第一冷凝器30冷凝成的液體(液氯和乙酸)回流入進反應主釜10內,形成一級冷凝迴路;
所述二級冷凝迴路包括第二冷凝器40,從第一冷凝器30出氣口溢出的氣體(氯化氫、二氧化硫、氯氣和乙酸蒸氣等)進入反應副釜20內反應,反應副釜20內同樣盛有乙酸和催化劑硫磺,且反應副釜處於保溫狀態,所以反應副釜20能夠吸收一部分氯氣和乙酸蒸氣,從反應副釜20出氣口溢出的氣體(氯化氫、二氧化硫、氯氣和乙酸蒸氣等)進入第二冷凝器40,經第二冷凝器40冷凝的液體(液氯和乙酸)回流進入反應副釜20中形成二級冷凝迴路;
所述三級冷凝迴路包括第三冷凝器50,從第二冷凝器40出氣口溢出的氣體(氯化氫、二氧化硫、氯氣和乙酸蒸氣等)進入第三冷凝器50內,經第三冷凝器50冷凝的液體(液氯和乙酸)回流入反應主釜10中,形成三級冷凝迴路;
從第三冷凝器50出氣口溢出的氣體(氯化氫96%、乙酸3%、二氧化硫0.2%和其它氣體0.8%)進入尾氣吸收系統;
從反應主釜10中溢出的有效氣體(氯氣和乙酸蒸氣)經過第一冷凝器30冷凝回流、反應副釜20反應吸收、第二冷凝器40冷凝回流和第三冷凝器50冷凝回流。通過採用二級串聯氯化,對反應主釜10內溢出的氣體進行多級吸收,提高了有效反應物的利用率。
由於尾氣吸收系統採用低濃度的鹽酸進行氯化氫氣體的吸收,當該鹽酸濃度達到31%之後進行採出售賣,被低濃度的鹽酸吸收的氣體主要為氯化氫,提高了副產物的純度。
所述第一冷凝器30與反應副釜20、第二冷凝器40與第三冷凝器50以及第三冷凝器50與反應主釜10之間的連接管路上均設有切換閥門,將上述的切換閥門均保持打開狀態,則上述反應能夠進行。
為了檢測反應主釜10內的壓力變化,並根據檢測反應主釜10內的壓力值做出相應洩壓管路的切換,應急切換系統包括應急管路70和控制器。
具體的結構及切換操作如下:
所述應急管路70連接反應主釜10的出氣口,應急管路70上在反應主釜10的出氣口處設有第一應急洩放閥73,所述反應副釜20的出氣口並聯於應急管路70,且反應副釜20的出氣口與應急管路70之間的管路上設有第二應急洩放閥74;所述應急管路70的出口分出兩條並聯的支路,其中一條支路上設有超壓排放閥71,且該支路出口與尾氣吸收系統連通,另一條支路上設有抽真空閥72和真空泵75,且該支路出口與事故尾氣吸收系統連通;
所述第三冷凝器50出氣口與尾氣吸收系統之間設有第一電磁閥51;
所述第一進氯管11上設有第二電磁閥13;
所述反應主釜10上設有檢測其內部壓力的第一壓力傳感器12;
所述控制器的信號輸入端連接第一壓力傳感器12的信號輸出端,控制器的控制輸出端分別連接第一電磁閥51、第二電磁閥13、第一應急洩放閥73、超壓排放閥71、抽真空閥72和真空泵75。
在氯乙酸生產系統正常反應時,第一電磁閥51和第二電磁閥13處於常開狀態,第一應急洩放閥73、第二應急洩放閥74、超壓排放閥71、抽真空閥72和真空泵75均處於常閉狀態。
第一壓力傳感器12實時檢測反應主釜10內的壓力。氯乙酸生產系統正常反應時,反應主釜10內的壓力值為0.03~0.05Mpa(不包含0.05Mpa);當反應主釜10內反應正常超壓,壓力值在0.05~0.07Mpa;而當第一冷凝器30或第三冷凝器50損壞,冷凍鹽水流至反應主釜10內,或當第二冷凝器40損壞,冷凍鹽水流至反應副釜20內,都會造成鹽水中的氨與氯氣在酸性條件下反應急劇放熱,由於傳統夾套反應釜不能將反應產生的熱量及時有效的傳遞出去,造成整個反應系統壓力急劇升高,壓力值超過0.07Mpa。第一壓力傳感器12將檢測到的反應主釜10內的壓力值傳輸給控制器,控制器為PLC控制器。當該壓力值為0.03~0.05Mpa(不包含0.05Mpa)時,控制器不做出任何控制操作;當該壓力值在0.05~0.07Mpa時,控制器控制第二電磁閥13關閉,第一應急洩放閥73和超壓排放閥71打開,反應主釜10內的壓力直接排入尾氣吸收系統,不再流經其它管路,當反應主釜10內的壓力值降到0.05Mpa以下時,控制器控制第二電磁閥13打開,第一應急洩放閥73和超壓排放閥71關閉,系統恢復正常工作狀態;而當該壓力值超過0.07Mpa時,控制器控制第一電磁閥51和第二電磁閥13關閉,第一應急洩放閥73、第二應急洩放閥74、抽真空閥72和真空泵75打開,反應主釜10內的壓力藉助真空泵75快速抽入事故尾氣吸收系統,避免系統發生爆炸,直至系統內壓力將至0.03Mpa以下,工作人員進入檢修或更換損壞的冷凝器。
本發明在系統內壓力升高後,能夠自動切換管路閥門,實現對系統壓力源直接洩壓,時間短效率高;並且,為了進一步提高副產物的收集,反應主釜10正常反應超壓(0.05~0.07Mpa)時,使反應主釜10內壓力直接洩入尾氣吸收系統內,當系統內非正常超壓(超過0.07Mpa)時,兩個反應釜內的氣體藉助真空泵快速排入事故尾氣吸收系統,實現對壓力源直接洩壓,有效避免事故發生。
並且,所述反應主釜10或反應副釜20一側設有氯氣洩漏檢測探頭80,所述氯氣洩漏檢測探頭80的信號輸出端連接控制器的信號輸入端。當管路出現故障、閥門或法蘭故障,出現氯氣洩漏時,氯氣洩漏檢測探頭80檢測到氯氣,將該信號傳輸給控制器,控制器控制第一電磁閥51和第二電磁閥13關閉,第一應急洩放閥73、第二應急洩放閥74、抽真空閥72和真空泵75打開,將系統內的有害氣體(氯氣)抽淨,以便後期工人進入維修,有效避免事故發生及減少人員傷害。
實施例2
如圖2所示,在實施例1的結構基礎上增加以下結構,以便在反應主釜10完成反應後,不用停產,而是利用反應副釜20作為主反應釜,在對反應副釜20升溫的過程中,將反應主釜10內的料液倒走,然後向反應主釜10內再次加入乙酸和催化劑硫磺後保溫。充分利用時間,提高工作效率。
具體的結構為:
所述反應副釜20的入口連接有向其內部通入氯氣的第二進氯管21;
所述第二冷凝器40的出氣口還與反應主釜10內腔的底部連通,從第二冷凝器40出氣口溢出的氣體進入反應主釜10內反應;
所述第一冷凝器30的出氣口與第三冷凝器50的進氣口連接,從第一冷凝器30出氣口溢出的氣體進入第三冷凝器50內,第三冷凝器50的冷凝出液端與反應副釜20連通,經第三冷凝器50冷凝的液體回流進入反應副釜20內;
所述第二冷凝器40與反應主釜10、第一冷凝器30與第三冷凝器50以及第三冷凝器50與反應主釜10之間的連接管路上均設有切換閥門。
當反應主釜10完成反應後,對反應副釜20升溫,利用反應副釜20作為主反應釜時,將實施例1中的所述第一冷凝器30與反應副釜20、第二冷凝器40與第三冷凝器50以及第三冷凝器50與反應主釜10之間的連接管路上上的切換閥門均關閉。而將第二冷凝器40與反應主釜10、第一冷凝器30與第三冷凝器50以及第三冷凝器50與反應主釜10之間的連接管路的切換閥門均打開。
反應副釜20作為主反應釜,而反應主釜20與之串聯,從反應副釜20中溢出的氣體依次經過第二冷凝器40冷凝回流、反應主釜10輔助反應吸收、第一冷凝器30冷凝回流和第三冷凝器50冷凝回流。
具體反應如下:
反應副釜10內盛有乙酸和催化劑硫磺,在高溫和硫磺的催化作用下氯氣與乙酸反應生成產物氯乙酸和副產物氯化氫;由於反應副釜20的溫度在70~110℃,所以會有氣體(氯化氫60%、二氧化硫0.2%、氯氣32%和乙酸蒸氣7%和其它氣體0.8%)溢出;
從所述反應副釜20出氣口溢出的氣體進入第二冷凝器40,經第二冷凝器40冷凝成的液體(液氯和乙酸)回流入進反應副釜20內;
從第二冷凝器40出氣口溢出的氣體(氯化氫、二氧化硫、氯氣和乙酸蒸氣等)進入反應主釜10內反應,反應主釜10處於保溫狀態,所以反應主釜10能夠吸收一部分氯氣和乙酸蒸氣,從反應主釜10出氣口溢出的氣體(氯化氫、二氧化硫、氯氣和乙酸蒸氣等)進入第一冷凝器30,經第一冷凝器30冷凝的液體(液氯和乙酸)回流進入反應主釜10中;
從第一冷凝器30出氣口溢出的氣體(氯化氫、二氧化硫、氯氣和乙酸蒸氣等)進入第三冷凝器50內,經第三冷凝器50冷凝的液體(液氯和乙酸)回流入反應副釜20中;
從第三冷凝器50出氣口溢出的氣體(氯化氫96%、乙酸3%、二氧化硫0.2%和其它氣體0.8%)進入尾氣吸收系統。
從反應副釜20中溢出的有效氣體(氯氣和乙酸蒸氣)依次經過第二冷凝器40冷凝回流、反應主釜10輔助反應吸收、第一冷凝器30冷凝回流和第三冷凝器50冷凝回流。通過採用二級串聯氯化,反應副釜20在之前作為副釜的使用過程中,已經吸收了部分氯氣,縮短可本次分反應時間。通過對反應副釜20內溢出的氣體進行多級吸收,提高了有效反應物的利用率以及副產物的純度。而且在反應主釜10完成反應後,不用停產,而是直接對反應副釜20升溫,利用反應副釜20作為主反應釜,縮短了時間,提高工作效率。
為了檢測反應副釜20內的壓力變化,並根據檢測反應副釜20內的壓力值做出相應洩壓管路的切換,應急切換系統在實施例1的基礎上還增加以下結構:
所述第二進氯管21上設有第三電磁閥23;
所述反應副釜20上設有檢測其內部壓力的第二壓力傳感器22;
所述控制器的信號輸入端還連接第二壓力傳感器22的信號輸出端,控制器的控制輸出端還連接第二應急洩放閥74。
在反應副釜20作為主反應釜,氯乙酸生產系統正常運行時,第一電磁閥51和第三電磁閥23處於常開狀態,第二電磁閥13、第一應急洩放閥73、第二應急洩放閥74、超壓排放閥71、抽真空閥72和真空泵75均處於常閉狀態。
應急切換系統具體的切換操作如下:
第二壓力傳感器22實時檢測反應副釜20內的壓力。氯乙酸生產系統正常反應時,反應副釜20內的壓力值為0.03~0.05Mpa(不包含0.05Mpa);當反應副釜20內反應正常超壓,壓力值在0.05~0.07Mpa;而當第一冷凝器30或第三冷凝器50損壞,冷凍鹽水流至反應主釜10內,或當第二冷凝器40損壞,冷凍鹽水流至反應副釜20內,都會造成鹽水中的氨與氯氣在酸性條件下反應急劇放熱,由於傳統夾套反應釜不能將反應產生的熱量及時有效的傳遞出去,造成整個反應系統壓力急劇升高,壓力值超過0.07Mpa。第二壓力傳感器22將檢測到的反應副釜20內的壓力值傳輸給控制器,控制器為PLC控制器。當該壓力值為0.03~0.05Mpa(不包含0.05Mpa)時,控制器不做出任何控制操作;當該壓力值在0.05~0.07Mpa時,控制器控制第三電磁閥23關閉,第二應急洩放閥74和超壓排放閥71打開,反應副釜20內的壓力直接排入尾氣吸收系統,不再流經其它管路,當反應副釜20內的壓力值降到0.05Mpa以下時,控制器控制第三電磁閥23打開,第二應急洩放閥74和超壓排放閥71關閉,系統恢復正常工作狀態;而當該壓力值超過0.07Mpa時,控制器控制第一電磁閥51和第三電磁閥23關閉,第一應急洩放閥73、第二應急洩放閥74抽真空閥72和真空泵75打開,反應副釜20內的壓力藉助真空泵75快速抽入事故尾氣吸收系統,避免系統發生爆炸,直至系統內壓力將至0.03Mpa以下,工作人員進入檢修或更換損壞的冷凝器。
本發明在系統內壓力升高後,能夠自動切換管路閥門,實現對系統壓力源直接洩壓,時間短效率高;並且,為了進一步提高副產物的收集,反應副釜20正常反應超壓(0.05~0.07Mpa)時,使反應副釜20內壓力直接洩入尾氣吸收系統內,當系統內非正常超壓(超過0.07Mpa)時,兩個反應釜內的氣體藉助真空泵快速排入事故尾氣吸收系統,實現對壓力源直接洩壓,有效避免事故發生。
當出現氯氣洩漏時,氯氣洩漏檢測探頭80檢測到氯氣,將該信號傳輸給控制器,控制器除控制切換實施例1中的所述的閥門外,還控制第三電磁閥23關閉。
實施例3
與實施例1不同之處在於,所述應急管路70的末端設有壓力傳感器76,所述壓力傳感器76的信號輸出端連接控制器的信號輸入端,所述控制器的控制輸出端連接報警裝置。當氯乙酸生產系統正產反應時,第一應急洩放閥73應處於關閉狀態,壓力傳感器76能夠檢測第一應急洩放閥73是否關閉緊,避免反應氣體直接從應急管路70排出,造成原料浪費。當壓力傳感器76傳輸給控制器的壓力值大於0時,說明應急管路70內有氣體通過,控制器就會控制報警裝置啟動,警示工作人員對第一應急洩放閥73進行維修。其中,報警裝置為聲光報警器。
實施例4
與實施例2不同之處在於,所述應急管路70的末端設有壓力傳感器76,所述壓力傳感器76的信號輸出端連接控制器的信號輸入端,所述控制器的控制輸出端連接報警裝置。當氯乙酸生產系統正產反應時,第一應急洩放閥73和第二應急洩放閥74應處於關閉狀態,壓力傳感器76能夠檢測第一應急洩放閥73和第二應急洩放閥74是否關閉緊,避免反應氣體直接從應急管路70排出,造成原料浪費。當壓力傳感器76傳輸給控制器的壓力值大於0時,說明應急管路70內有氣體通過,控制器就會控制報警裝置啟動,警示工作人員對第一應急洩放閥73和第二應急洩放閥74進行維修。
其中,報警裝置為聲光報警器。
以上僅是本發明的較佳實施例,任何人根據本發明的內容對本發明做出的些許的簡單修改、變形及等同替換均落入本發明的保護範圍。