短流程軋制合金化鍍層熱成形鋼及其製造方法與流程
2023-05-20 00:13:11 1
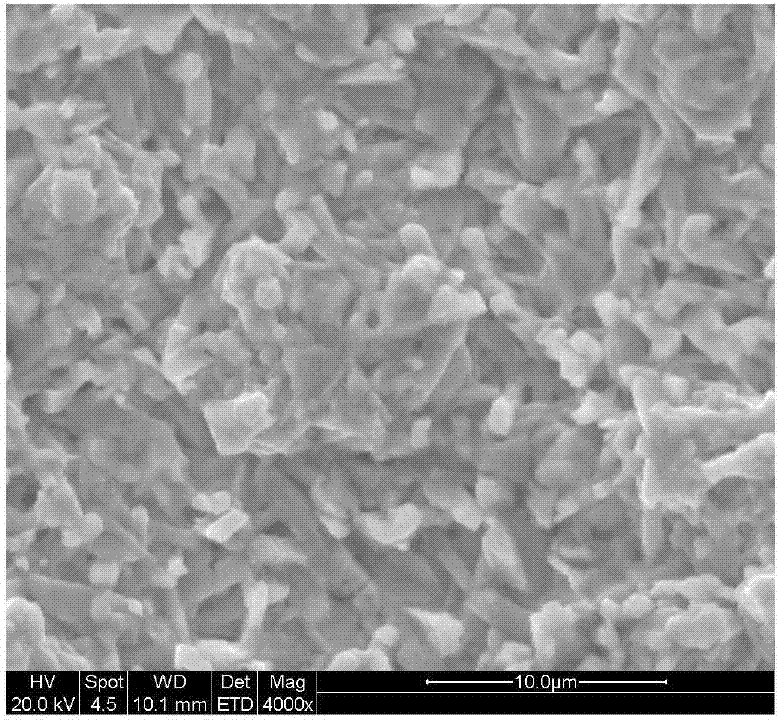
本發明涉及熱壓成形領域,具體用於汽車部件的短流程軋制合金化鍍層熱成形鋼及其製造方法。
背景技術:
熱成形鋼在高溫加熱成形後具有很高的抗拉強度和在高溫下良好的成形性,從而可以成形複雜形狀、超高強度的零件,且具有成形精確,焊接性良好,沒有回彈等優點。作為汽車用鋼中強度級別最高的鋼種,熱成形鋼被廣泛用於汽車防碰撞的安全部件。
隨著熱成形技術的發展,鍍層技術越來越多地應用於熱成形鋼。鍍層既可以防止成形過程中表面氧化和脫碳,又能提高漆裝後的防腐蝕性能。其中,熱鍍鋅具有很好的表面質量和優異的抗腐蝕性能,是鋼鐵材料最常見、最有效、最經濟的耐大氣腐蝕技術之一。但是由於鋅層與鋼板的粘附性不良從而影響表面質量,鍍鋅前的表面狀態一般為酸洗冷軋態。其生產工藝流程為:脫硫鐵水→轉爐冶煉→爐外精煉→連鑄→板坯加熱→熱連軋→酸洗+冷連軋→連續塗鍍→精整包裝→落料→加熱→模具衝壓淬火。生產工藝流程較長,成本較高。
現今,隨著汽車工業的飛速發展,在保證安全和輕量化的前提下,對於表面質量要求較低的非表面覆蓋件等零件,汽車生產廠對於「以熱代冷」從而降低生產成本提出了新的要求。隨著鋼鐵工業的發展,中薄板坯連鑄連軋工藝得到了長足發展,採用中薄板坯連鑄連軋工藝可以直接軋制生產0.8~2.0mm的薄鋼板,一些原來只能使用冷軋高強鋼的薄規格零件已逐步被採用連鑄連軋工藝直接軋制薄鋼板所代替。此類熱軋態表面與常規熱軋和冷軋態表面有較大差異,需要採用新的塗鍍工藝獲得優良的鍍層表面質量。
專利號為cn103658178a的專利發明了一種短流程生產高強度薄帶鋼的方法,所發明的帶鋼屈服強度(rel)≥550mpa,抗拉強度(rm)≥600mpa。其強度較低,不能滿足汽車車身設計對1300mpa以上超高強度零件的需求。cn103987868a公開了980mpa以上的最大拉伸強度合金化熱浸鍍鋅鋼板,所述母材鋼板按質量%計含有c:0.1~0.40%、si:0.5~3.0%、mn:1.5~3.0%,o被限制在0.006%以下、p被限制在0.04%以下、s被限制在0.01%以下、al被限制在2.0%以下、n被限制在0.01%以下。熱浸鋅鍍層含有低於7%的fe,餘量由zn、al和不可避免的雜質組成。其經過酸洗冷軋後再合金化鍍鋅,生產流程較長。
技術實現要素:
本發明的目的在於將短流程生產技術與連續熱浸鍍技術二者合理有機串接,形成一種新型的短流程軋制合金化鍍層熱成形鋼及其製造方法,達到「以熱代冷」1000mpa級以上超高強度熱成形鋼直接鍍鋅,提高產品質量、降低能耗、提高生產效率、降低成本的目的。
為實現上述目的,本發明提供的短流程軋制合金化鍍層熱成形鋼的方法包括電爐或轉爐冶煉、精煉、中薄板坯連鑄、鑄坯均熱、軋制、層流冷卻、卷取、合金化熱浸鍍、光整、落料、加熱奧氏體化和模具衝壓成形淬火的步驟:
所述電爐或轉爐冶煉步驟中化學成分重量百分數為:c:0.14~0.4%,si:0.1~0.4%,mn:0.8~2.0%,al≤0.08%,n≤0.005%,其餘為fe和不可避免的雜質。
所述軋制過步驟中,終軋溫度為850~890℃,帶鋼成品厚度為0.8~2.0mm,軋制過程中採用支撐輥潤滑。
所述合金化熱浸鍍步驟中,首先,將鋼帶在0℃~+50℃的露點範圍內加熱到780℃~840℃,h2體積百分數為25~85%,以10~30℃/s的冷速冷卻至高於鍍液溫度(td)5~30℃,保溫時間不超過100s,隨後浸鍍到鍍液中,鍍液溫度(td)為(熔點+20)~(熔點+60)℃,浸鍍時間不超過15s,鋼帶熱鍍後經氣刀吹掃進入感應加熱爐進行合金化熱處理,再加熱溫度為460~560℃,保溫時間不超過40s,以30~100℃/s的冷速冷卻至室溫並製成鋼卷。
所述奧氏體化和模具衝壓成形淬火步驟中,將合金化熱浸鍍後的鋼卷經光整、落料後,在帶有氮氣保護氣氛的加熱爐內加熱到850~920℃保溫1~10min進行奧氏體化,然後快速置於帶有冷卻裝置的模具內進行衝壓成形,成形過程中同時發生淬火及低溫回火,淬火冷卻速度為20~40℃/s。
優選地,所述合金化熱浸鍍步驟中,所得鍍層的化學成分重量百分數為:al:0.1~0.2%,fe:5~14%,其餘為zn和不可避免的雜質。
優選地,所述合金化熱浸鍍步驟中,加熱溫度為800~820℃,露點範圍為+30~+50℃;h2體積百分數為50~70%。
優選地,所述合金化熱浸鍍步驟中,合金化鍍層中fe含量均值在9~13%,鍍層厚度為15~40μm。經高溫加熱衝壓成形後鍍層連續完整,且前述的合金化熱浸鍍組織發生轉變,形成新的兩相組織γ-fe4zn9(30zn-70fe)和α-fe(zn)(80zn-20fe),該兩相組織中zn含量均整體高於30%,鍍層抗腐蝕性能良好。
優選地,所述熱合金化浸鍍步驟中,浸鍍前冷卻後的溫度為高於鍍液溫度10~20℃,保溫時間為20~30s,浸鍍時間為4~8s。
優選地,所述奧氏體化和模具衝壓成形淬火步驟中,加熱到完全奧氏體化溫度870~900℃,保溫2~5min後進行高溫衝壓成形,成形後以30~40℃/s的冷速冷卻至室溫。
本發明相對現有技術減少了冷連軋工序,其工藝流程大大縮短,鋼水經連續澆鑄成中薄板坯後經短暫加熱後直接軋製成薄板,工序成本大幅降低,且帶鋼的板形良好,厚度精度高,能實現「以熱代冷」目的。另外,本發明表面氧化鐵皮粒度細小可控,厚度在5μm左右,從而突破了現有技術所生產的產品鍍層質量較差的問題。
按照本發明製造的耐蝕高強度合金化鍍層汽車板,強度大於1000mpa。經高溫加熱衝壓成形後鍍層連續完整,未發現有擴展至基體的裂紋。且合金化熱浸鍍組織發生轉變,形成兩相組織γ-fe4zn9(30zn-70fe)和α-fe(zn)(80zn-20fe),合金相中zn含量整體高於30%,保證鍍層具有良好的防腐性能,成品鋼基組織為馬氏體,其中馬氏體的體積百分數不小於95%。鋼板在高溫成形後,鍍層完整無脫落。
附圖說明
圖1為本發明基板表面氧化鐵皮掃描形貌。
圖2為本發明熱成形前合金化鍍層掃描形貌。
圖3為本發明熱成形後合金化鍍層掃描形貌。
具體實施方式
以下結合附圖是具體實施例對本發明作進一步詳細的說明。
本發明的短流程軋制合金化鍍層熱成形鋼的方法,主要包括電爐或轉爐冶煉、精煉、中薄板坯連鑄、鑄坯均熱、軋制、層流冷卻、卷取、合金化熱浸鍍、光整、落料、加熱奧氏體化、模具衝壓成形淬火,具體工藝為:
按照化學成分冶煉並連鑄連軋;
所述軋制過程的終軋溫度為850~890℃,帶鋼成品厚度為0.8~2.0mm,軋制過程中採用支撐輥潤滑;
將鋼帶在0℃~+50℃的露點範圍內加熱到780℃~840℃,h2體積百分數為25~85%,以10~30℃/s的冷速冷卻至高於鍍液溫度(td)5~30℃,保溫時間不超過100s,隨後浸鍍到鍍液中,鍍液溫度(td)為(熔點+20)~(熔點+60)℃,浸鍍時間不超過15s;鋼帶熱鍍後經氣刀吹掃進入感應加熱爐進行合金化熱處理,再加熱溫度為460~560℃,保溫時間不超過40s,以30~100℃/s的冷速冷卻至室溫並製成鋼卷;
根據汽車車身零件尺寸的大小,將板卷落料成相應的規格,在帶有氮氣保護氣氛的加熱爐內加熱到850~920℃保溫1~10min進行奧氏體化,然後快速置於帶有冷卻裝置的模具內進行衝壓成形,成形過程中同時發生淬火及低溫回火,淬火冷卻速度20~40℃/s,成品鋼基組織為馬氏體,其中馬氏體的體積百分數不小於95%。鋼板在高溫成形後,鍍層完整無脫落。
下面對本發明予以詳細描述:
合金化鍍鋅工藝參數、鍍層質量及熱衝壓工藝參數見表1、2。
表1合金化工藝參數
表2(續1)合金化鍍層質量及熱衝壓工藝參數
從圖1~3和表1~2可以看出:
軋制後的鋼板按照表1、2所示工藝參數合金化熱浸鍍後,氧化鐵皮的成分和形態發生改變,鋼基表面氧化鐵皮由較為疏鬆的fe2o3和fe3o4轉變為細小緻密的feo和少量的fe3o4(圖1),厚度在5~10μm,鍍層在鋼基表面附著性良好。合金化熱浸鍍鍍層主要由δ相構成,表面有少量ζ相(圖2)。鋼板在高溫(854~920℃)成形後,鍍層完整無脫落,微裂紋未擴展至鋼基內(圖3)。
經過本發明的工藝製造的合金化鍍層產品可以改變短流程生產的鋼基表面氧化鐵皮性狀,可耐受高溫成形並無鍍層脫落或裂紋擴展情況發生,鍍層耐蝕性良好,滿足現代鍍層熱成形鋼的生產和使用要求。