一種用於對片狀零件進行組裝的衝壓裝置及衝壓方法與流程
2023-04-26 22:05:21 3
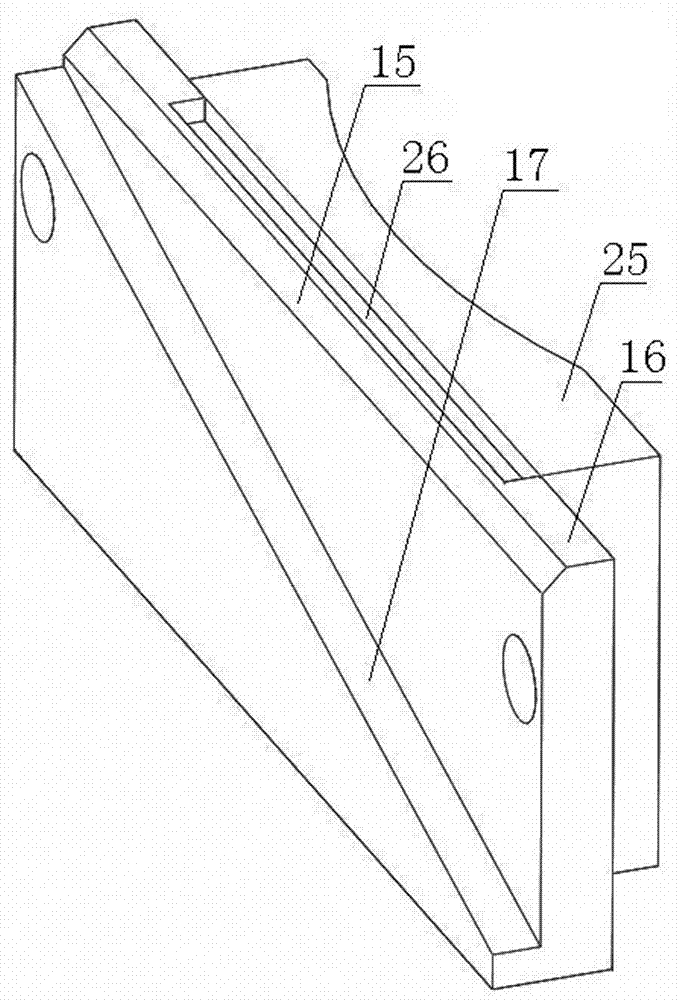
本發明屬於機械加工技術領域,尤其涉及一種用於對片狀零件進行組裝的衝壓裝置及衝壓方法。
背景技術:
在對片狀零件進行加工的過程中,很多片狀零件過於精細,尤其是片狀零件需要通過很多小零部件組裝在一起,傳統的方式通過外力將多個零部件結合在一起,在自動化領域,常採用機械衝壓的方式,藉助瞬間的衝擊力將多個零部件衝壓成一體的結構。目前工人進行衝壓工作時,手工將多個小零部件按照需要裝置的位置關係進行安裝後放在自動衝床板上,踩下離合器,利用衝床將組裝後的小零部件組合進行衝壓成一個整體的片狀零件。這樣的工作模式每分鐘最快約加工15件,工人在選取小零部件時相對雜亂並且不方便,需要分別取選取,還要手動做初步按壓工作,不僅效率低下,衝壓精度不高,而且存在工作危險。
技術實現要素:
針對現有技術的不足,本發明提供一種用於對片狀零件進行組裝的衝壓裝置及衝壓方法,實現對小零部件的自動分揀,採用機械組裝代替人工組裝,並自動控制衝壓過程,不僅提高裝配效率也提高小零部件之間結合的緊密性。
為解決上述技術問題,本發明的是通過以下技術方案實現的:
本發明提供一種用於對片狀零件進行組裝的衝壓裝置,其特殊之處在於:所述衝壓裝置包括動力機構、衝壓頭4、定位機構、衝壓臺13,所述衝壓頭4位於衝壓臺13上方,所述定位機構位於動力機構與衝壓臺13之間。
進一步地,所述衝壓臺13頂部的臺面設置有衝壓區16、與衝壓區16銜接的緩衝區15;在衝壓區16設置有衝壓板14,衝壓臺13與定位機構相連的一側壁設置有下料區17,所述下料區17位於緩衝區15的下方。
進一步地,所述衝壓區16為平面狀,所述緩衝區15為與衝壓區16形成彎折的斜面、在衝壓區16上設置有凹槽26,所述衝壓板14內嵌在凹槽26內,下料區17所在的衝壓臺13側壁設置成臺階狀,臺階狀的臺面為斜坡狀。
進一步地,所述衝壓臺13還連接有過渡臺,衝壓臺13的一側壁與過渡臺的一側壁固定貼合,所述衝壓臺13的頂部衝壓板14的上表面與過渡臺上表面位於同一平面。
進一步地,所述定位機構包括固定板11、定位板10、滑動結構,其中定位板10上設置有限位塊12,所述定位板10位於固定板11上方,且定位板10的中心開設有滑槽9,限位塊12位於滑槽9內;所述滑動結構為雙層滑軌結構,上層滑軌結構的第一滑塊18位於安裝在底板22上表面的第一滑軌19上方,在底板22的下表面安裝有下層滑軌結構的第二滑塊20,第二滑塊20下方設置第二滑軌21;固定板11的上表面與定位板10活動連接,固定板11的下表面與第一滑塊18固定連接,上層滑軌結構與下層滑軌結構在空間上相對垂直。
進一步地,在定位板10上沿滑槽9滑動的方向設置有u形開口7,所述u形開口7面向衝壓臺13的方向,u形開口7的開口端兩側相對側壁的下表面均設置有向內凹陷的空腔6。
進一步地,所述動力機構採用衝壓氣缸8,所述固定板11的一端通過防撞塊25與衝壓臺13具有臺階狀的側壁相連,另一端與衝壓氣缸8的活塞杆固定連接。
進一步地,所述衝壓裝置還包括推動機構,所述推動機構包括伸縮氣缸1、位於伸縮氣缸1下方並與伸縮氣缸1的活塞杆連接的推動氣缸2,與推動氣缸2的活塞杆固定連接的推板5。
進一步地,所述衝壓裝置還包括收集裝置,所述收集裝置位於衝壓臺13的下料區17,所述衝壓頭4上設有用於統計衝壓次數的計數器或傳感器。
本發明還提供一種用於對片狀零件進行組裝的衝壓方法,其特殊之處在於:根據本發明提供的衝壓裝置對待衝壓的片狀零件進行衝壓,具體過程如下:
步驟1,推動機構將待衝壓的片狀零件推動至預設地點,具體過程如下:
步驟11、推動機構內伸縮氣缸1的活塞杆伸出帶動伸縮氣缸1下方的推動氣缸2降落至旋轉裝置的旋轉臺上,
步驟12、推動氣缸2的活塞杆固定連接有推板5,推動氣缸2的活塞杆伸出,推板5沿定位板10的u形開口7推動待衝壓片狀零件前進至衝壓臺13上;
步驟2、位於衝壓臺13上方的衝壓頭4對待衝壓的片狀零件進行衝壓動作,當衝壓完成後,動力機構帶動定位機構離開預設地點,推動機構繼續推動衝壓後的片狀零件離開衝壓臺13;
步驟3,根據衝壓臺13的衝壓次數統計實現對待衝壓片狀零件數的統計,當衝壓完成,衝壓臺13與定位機構相連的一側壁設置有下料區17,所述下料區17位於緩衝區15的下方,推動機構內的推板5在動力機構的帶動下推動衝壓後的片狀零件離開衝壓區16,沿著緩衝區15進入下料區17;
步驟4、衝壓後的片狀零件從衝壓臺13進入收集裝置,按照次序排放。
進一步地,動力機構為衝壓氣缸8,當定位機構與衝壓臺13一側壁相貼時所到達的位置為步驟1中的預設地點,此時,定位機構中定位板10的u形開口7搭放在衝壓臺13上方。
進一步地,在步驟2中,定位機構到達預設地點之後推動機構執行動作之前,所述定位機構根據待衝壓片狀零件在預設地點上的位置進行微調工作,具體過程為:
定位機構到達預設地點之後,若定位板10的u形開口7不在衝壓臺13的衝壓區16上方,則調整限位塊12在滑槽9中的位置來滿足定位板10的u形開口7在衝壓區16上方;
根據待衝壓片狀零件在預設地點上的位置,分別利用定位機構內的上層滑軌結構實現橫向調整,下層滑軌機構實現縱向調整,滿足待衝壓片狀零件與定位板10的u形開口7在同一前進方向。
本發明與現有技術相比,其有益之處在於:
本發明高度自動化、提高生產效率以及生產精度,利用衝壓裝置對需要衝壓的待衝壓片狀零件流水線作業,並且衝壓速度提高,每分鐘可以衝壓零件個數為60-120個,,衝壓後的片狀零件裝配牢固,定位精度高,誤差小。
附圖說明
圖1是本發明的衝壓裝置結構示意圖;
圖2是本發明的衝壓臺結構示意圖;
圖3是本發明的衝壓頭結構示意圖;
圖4是本發明的電腦移圈針結構示意圖。
標記說明:1、伸縮氣缸,2、推動氣缸,3、安裝槽,4、衝壓頭,5、推板,6、空腔,7、u形開口,8、衝壓氣缸,9、滑槽,10、定位板,11、固定板,12、限位塊,13、衝壓臺,14、衝壓板,15、緩衝區,16、衝壓區,17、下料區,18、第一滑塊,19、第一滑軌,20、第二滑塊,21、第二滑軌,22、底板,23、定位氣缸,24、底座,25、防撞塊,26、凹槽,27、腿部,28、本體,29、簧片。
具體實施方式
以下參照附圖,給出本發明的具體實施方式,用來對本發明做進一步說明。
實施例1
在本實施例中通過電腦移圈針作為待衝壓片狀零件進行說明,在本實施例中該待衝壓片狀零件包括兩個零部件,電腦移圈針有本體28及簧片29組成,在裝配是需要將簧片29安裝在本體28的凹槽26內,並通過衝壓將兩個零部件藉助衝壓力裝配在一起,通過本實施例提供的衝壓裝置極大地提高裝配效率及裝配精度。
在本實施例的衝壓裝置中,所述衝壓裝置包括動力機構、衝壓頭4、定位機構、衝壓臺13,所述衝壓頭4位於衝壓臺13上方,所述定位機構位於動力機構與衝壓臺13之間。對於本實施例的衝壓裝置作為自動生產線上的一部分,電腦移圈針來自上一工作位安裝槽3的傳送。
為了避免在衝壓過程中的強大衝擊力對整個自動生產線帶來磨損,衝壓臺13的兩側一側與定位機構相連,另一側設置有過渡臺,用來緩衝衝擊力,過渡臺承接上一工位傳送的需要進行衝壓的電腦移圈針。
所述推動機構包括伸縮氣缸1、位於伸縮氣缸1下方並與伸縮氣缸1的活塞杆連接的推動氣缸2,與推動氣缸2的活塞杆固定連接的推板5。在本實施例中衝壓頭4為∩形結構,其中∩形結構的兩個腿部27均為楔形狀;衝壓時,將衝壓頭4的腿部27橫跨在電腦移圈針的上方,將本體28與簧片29裝配在一起。
衝壓臺13頂部的臺面設置有衝壓區16、與衝壓區16銜接的緩衝區15;在衝壓區16設置有衝壓板14,衝壓臺13與定位機構相連的一側壁設置有下料區17,所述下料區17位於緩衝區15的下方。
衝壓區16為平面狀,所述緩衝區15為與衝壓區16形成彎折的斜面、在衝壓區16上設置有凹槽26,所述衝壓板14內嵌在凹槽26內,下料區17所在的衝壓臺13側壁設置成臺階狀,臺階狀的臺面為斜坡狀,所述衝壓臺13的頂部衝壓板14的上表面與過渡臺上表面位於同一平面;便於安裝槽3內的電腦移圈針平滑地移動至衝壓臺13上。
在本實施例中衝壓板14為硬度合金製成;用來增加衝壓臺13面的硬度,在衝壓頭4的強壓下不易順壞。
所述定位機構包括固定板11、定位板10、滑動結構,其中定位板10上設置有限位塊12,所述定位板10位於固定板11上方,且定位板10的中心開設有滑槽9,限位塊12位於滑槽9內;所述滑動結構為雙層滑軌結構,上層滑軌結構的第一滑塊18位於安裝在底板22上表面的第一滑軌19上方,在底板22的下表面安裝有下層滑軌結構的第二滑塊20,第二滑塊20下方設置第二滑軌21;固定板11的上表面與定位板10活動連接,固定板11的下表面與第一滑塊18固定連接,上層滑軌結構與下層滑軌結構在空間上相對垂直;在定位板10上沿滑槽9滑動的方向設置有u形開口7,所述u形開口7面向旋轉臺的方向,且開口的尺寸大於推動機構中推板5的尺寸,u形開口7的開口端兩側相對側壁的下表面均設置有向內凹陷的空腔6,待衝壓的電腦移圈針可以沿著空腔6前進至衝壓臺13的衝壓板14上。
利用雙層滑軌結構,可以在橫向或縱向來調整定位機構的位置,以滿足電腦移圈針與定位板10的空腔6在同一方向上,便於電腦移圈針沿著空腔6移動,當定位機構調整好後,推動機構並能夠將電腦移圈針推送至衝壓臺13上方,等待衝壓頭4降落對本體28和簧片29的裝配體進行衝壓。
在本實施例中動力機構採用衝壓氣缸8,所述固定板11的一端通過防撞塊25與衝壓臺13具有臺階狀的側壁相連,另一端與衝壓氣缸8的活塞杆固定連接。
在本實施例中的衝壓裝置還包括工作檯,在工作檯上設有底座24、及用於固定伸縮氣缸1頂部的支架,所述衝壓臺13的底部固定在底座24上,在底座24上還設有固定衝壓氣缸8的固定架,第二滑軌21固定在底座24上方。
在本實施例中待衝壓片狀零件為具有兩個零部件的電腦移圈針,對於本實施例的工作原理,仍利用電腦移圈針為例,待衝壓片狀零件為電腦移圈針,其包括兩個兩部件,一個為本體28,一個為簧片29,需要將簧片29嵌入在本體28的凹槽26內。
位於衝壓臺13上方的衝壓頭4對待衝壓的電腦移圈針進行衝壓動作,當衝壓完成後,定位氣缸23帶動定位機構離開衝壓臺13,推動機構繼續推動衝壓完成的電腦移圈針離開衝壓臺13,通過以下的具體自動化衝壓方法來完成。
步驟1,推動機構將待衝壓的電腦移圈針推動至預設地點,具體過程如下:
步驟11、推動機構內伸縮氣缸1的活塞杆伸出帶動伸縮氣缸1下方的推動氣缸2降落至旋轉裝置的旋轉臺上,
步驟12、推動氣缸2的活塞杆固定連接有推板5,推動氣缸2的活塞杆伸出,推板5沿定位板10的u形開口7推動待衝壓的電腦移圈針前進至衝壓臺13上。
步驟2、位於衝壓臺13上方的衝壓頭4對待衝壓的電腦移圈針進行衝壓動作,當衝壓完成後,動力機構帶動定位機構離開預設地點,推動機構繼續推動衝壓後的電腦移圈針離開衝壓臺13。
步驟3,根據衝壓臺13的衝壓次數統計實現對待衝壓的電腦移圈針零件數的統計,當衝壓完成,衝壓臺13與定位機構相連的一側壁設置有下料區17,所述下料區17位於緩衝區15的下方,推動機構內的推板5在動力機構的帶動下推動衝壓後的電腦移圈針離開衝壓區16,沿著緩衝區15進入下料區17。
在本實施例中動力機構為衝壓氣缸8,當定位機構與衝壓臺13一側壁相貼時所到達的位置為步驟1中的預設地點,此時,定位機構中定位板10的u形開口7搭放在衝壓臺13上方。
在步驟2中,定位機構到達預設地點之後推動機構執行動作之前,所述定位機構根據待衝壓的電腦移圈針在預設地點上的位置進行微調工作,具體過程為:
定位機構到達預設地點之後,若定位板10的u形開口7不在衝壓臺13的衝壓區16上方,則調整限位塊12在滑槽9中的位置來滿足定位板10的u形開口7在衝壓區16上方;
根據待衝壓的電腦移圈針在預設地點上的位置,分別利用定位機構內的上層滑軌結構實現橫向調整,下層滑軌機構實現縱向調整,滿足待衝壓的電腦移圈針與定位板10的u形開口7在同一前進方向。以後的每次衝壓均按照此次調整進行。
實施例2
在本實施例中的衝壓裝置結構整體與實施例1類似,
衝壓裝置還包括收集裝置,所述收集裝置位於衝壓臺13的下料區17,所述衝壓頭4上設有用於統計衝壓次數的計數器或傳感器。
對於本實施例的工作過程,步驟1-步驟3與實施例1相同,在步驟3完成後,執行步驟4、完成衝壓後的電腦移圈針進入收集裝置,按照次序排放,並根據衝壓臺13的衝壓次數統計衝壓次數,實現對組裝件個數的統計。
對於本領域技術人員而言,顯然本發明不限於上述示範性實施例的細節,而且在不背離本發明的精神或基本特徵的情況下,能夠以其他的具體形式實現本發明。因此,無論從哪一點來看,均應將實施例看作是示範性的,而且是非限制性的,本發明的範圍由所附權利要求而不是上述說明限定,因此旨在將落在權利要求的等同要件的含義和範圍內的所有變化囊括在本發明內。
此外,應當理解,雖然本說明書按照實施方式加以描述,但並非每個實施方式包含一個獨立的技術方案,說明書的這種敘述方式僅僅是為清楚起見,本領域技術人員應當將說明書作為一個整體,各實施例中的技術方案也可以經適當組合,形成本領域技術人員可以理解的其他實施方式。