一種細紗機組合式微孔導紗鉤的製作方法
2023-07-24 07:42:46 3
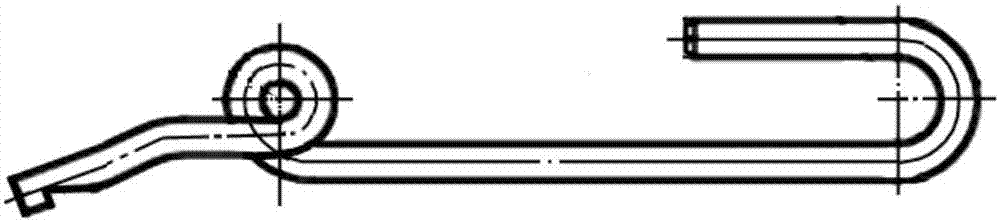
本實用新型屬於環錠紡紗技術領域,具體涉及一種細紗機組合式微孔導紗鉤。
背景技術:
導紗鉤是環錠紡細紗機不可缺少的紡紗器材,現有環錠紡細紗機所用的導紗鉤(如圖1和圖2所示)分A、B兩種類型,均固裝在葉子板2-1前端使用,位於前羅拉的下前方(如圖3所示)。由前羅拉鉗口2-3輸出的紗條2-2經導紗鉤1後,被鋼領2-4和鋼絲圈2-5加捻成紗線並卷繞在紗管2-7上。上述的導紗鉤由硬鋼絲材料製成,導紗鉤的孔徑較小,一般只有2.0mm~3.5mm,且均為螺旋開口孔。使用時要求導紗孔內表面光滑、耐磨,加工時導紗孔的成型、內表面的拋光和表面處理技術是關鍵。小孔徑導紗鉤有利於減少細紗毛羽,但成型、表面處理和拋光難度制約了導紗鉤導紗孔徑的進一步縮小。
紗線3mm以上的長毛羽為有害毛羽,長毛羽會使漿紗分絞困難,並造成織造時經紗開口不清,從而出現斷頭、停車和織疵。紗線毛羽產生於紡紗過程中,在絡紗過程中大量增加,因此,在紡紗過程中控制毛羽的產生是關鍵。紡紗過程中毛羽主要產生於三個環節:第一個環節是前羅拉輸出鉗口的加捻三角區,處於加捻三角區邊緣的纖維控制較弱,纖維的頭、尾端不能被完全卷捻入紗線體內,露在紗線體外的纖維頭、尾端就形成了毛羽。第二個環節是導紗鉤,紗線在經過導紗鉤時,和導紗鉤有一段接觸包圍弧,隨著氣圈紗2-6的迴轉和紗線的卷繞,紗線和導紗鉤有兩種滑動摩擦,第一種是隨氣圈紗迴轉而產生的與導紗孔周邊水平方向的滑動摩擦,這種滑動摩擦由於相對速度較高和摩擦動程較長而劇烈,以18000r/min錠速計,氣圈紗迴轉速度(忽略鋼絲圈卷繞的轉速差)約300r/s。A型導紗鉤的導紗孔周長約11mm(3.5mm×π),A型導紗鉤的第一種滑動摩擦相對速度約為3300mm/s=3.3m/s(π×3.5mm/r×300r/s),氣圈紗迴轉一周的摩擦動程即為導紗孔周長11mm,氣圈紗每秒摩擦動程高達3.3m;B型導紗鉤的導紗孔周長約6.3mm(2mm×π),第一種滑動摩擦相對速度約為1890mm/s=1.89m/s(π×2mm×300r/s),氣圈紗迴轉一周的摩擦動程和每秒的摩擦動程分別為6.3mm和1.89m。導紗鉤處第二種滑動摩擦是隨著紗線的卷繞而產生的從導紗孔周邊垂直向下的滑動摩擦,這種滑動摩擦由於相對速度較低和摩擦動程較短而較緩,以前羅拉直徑為27mm和轉速為250r/min計,紗條輸出速度(忽略捻縮,約等於紗線卷繞速度)約為13345mm/min=222.4mm/s=0.2224m/s(π×27mm/r×250r/min÷60s/min),垂直向下的摩擦動程約2mm。此兩種滑動摩擦均會使露出紗線體的毛羽加長,或使卷捻入紗線體內不緊密的纖維頭、尾端暴露出紗線體外而形成新的毛羽,顯然,第一種水平方向的滑動摩擦產生毛羽的作用要比第二種垂直方向滑動摩擦產生毛羽的作用大得多。第三個產生毛羽的環節是鋼絲圈,紗線經過鋼絲圈時也有一段包圍弧,隨著紗線的卷繞,紗線在鋼絲圈的紗線通道處與鋼絲圈產生滑動摩擦,此種滑動摩擦與導紗鉤處的第二種滑動摩擦相同,相對較緩。
為減少細紗毛羽,近年來,國內導紗鉤的孔徑有減小的趨勢,如B型導紗鉤國內有些企業已能生產1.8mm孔徑的了,但是,還是不能很好的滿足細紗機的紡紗需求。
技術實現要素:
本實用新型的目的在於克服上述現有技術中的不足,提供一種細紗機組合式微孔導紗鉤,能明顯縮短導紗鉤處形成毛羽時第一種滑動摩擦的摩擦動程,並降低該種滑動摩擦的相對滑動摩擦速度,從而明顯降低第一種滑動摩擦的劇烈程度,使導紗鉤處形成的毛羽數大大減少;可改善細紗的毛羽指標,提高細紗質量;同時結構簡單、設計合理、加工難度小、使用方便、而且耐磨,除能減少細紗毛羽和提高耐磨性外,還能縮短紡紗時接頭操作時間,具有提高紡紗效率、減少人力資源消耗、降低紡紗成本的特點。
為實現上述目的,本實用新型採用的技術方案是:一種細紗機組合式微孔導紗鉤,其特徵在於:包括上導紗片、下導紗片和支撐杆,所述上導紗片設置在支撐杆的前端上側,所述下導紗片設置在支撐杆的前端下側,所述上導紗片的一端開有第一連接孔,所述下導紗片的一端開有第二連接孔,所述上導紗片與下導紗片經穿過第一連接孔和第二連接孔的緊固件固定連接,所述上導紗片與下導紗片之間形成過紗間隙,所述上導紗片的另一端設置有上導紗槽,所述下導紗片的另一端設置有下導紗槽,所述上導紗槽與下導紗槽之間形成合成導紗孔。
上述的一種細紗機組合式微孔導紗鉤,其特徵在於:所述上導紗槽和下導紗槽的形狀均為V字形。
上述的一種細紗機組合式微孔導紗鉤,其特徵在於:所述上導紗槽和下導紗槽的底部均為圓角結構。
上述的一種細紗機組合式微孔導紗鉤,其特徵在於:所述上導紗槽的槽口向細紗機內側方向設置,所述下導紗槽的槽口向細紗機外側方向設置。
上述的一種細紗機組合式微孔導紗鉤,其特徵在於:所述合成導紗孔的形狀為橢圓形。
上述的一種細紗機組合式微孔導紗鉤,其特徵在於:所述合成導紗孔的短軸長度為0.1mm~0.5mm。
上述的一種細紗機組合式微孔導紗鉤,其特徵在於:所述支撐杆的前端向斜下方伸出。
上述的一種細紗機組合式微孔導紗鉤,其特徵在於:所述支撐杆的前端端部設置有擒紗槽。
上述的一種細紗機組合式微孔導紗鉤,其特徵在於:所述支撐杆的前端設置有用於固裝上導紗片和下導紗片的前U形彎,所述上導紗片設置在前U形彎的上側,所述下導紗片設置在前U形彎的下側;所述緊固件為緊固螺栓,所述緊固件依次穿過第二連接孔、前U形彎和第一連接孔,所述緊固件的端部設置有鎖緊螺母。
上述的一種細紗機組合式微孔導紗鉤,其特徵在於:所述上導紗片和下導紗片均為碳化鎢硬質合金導紗片。
本實用新型與現有技術相比具有以下優點:
1、本實用新型結構簡單,設計合理,使用方便。
2、本實用新型上導紗片和下導紗片均固定安裝在支撐杆的前端的U形彎處,支撐杆固裝在葉子板前端,因此,無需改動葉子板,與現用導紗鉤互換性強,使用方便。
3、本實用新型組合導紗孔呈類似橢圓形孔形,合成類橢圓形導紗孔的短軸孔徑可在0.1mm~0.5mm之間依據對成紗毛羽的要求自由調控。同樣以18000r/min錠速為例,以合成導紗孔的短軸孔徑為0.25mm計,則導紗孔周長(即氣圈紗迴轉一周的摩擦動程)只有約1.6mm,第一種(水平方向)滑動摩擦的相對速度只有約480mm/s=0.48m/s(1.6mm×300r/s);當合成孔短軸孔徑為0.1mm時,合成導紗孔周長只有約1.0mm,此時第一種滑動摩擦的相對速度只有約300mm/s=0.3m/s。與現有導紗鉤相比,無論是A型還是B型,本實用新型均可大大降低氣圈紗與導紗鉤導紗孔水平方向滑動摩擦的速度和縮短氣圈紗與導紗孔水平方向滑動摩擦的動程,從而明顯減少導紗鉤處產生的細紗毛羽數,提高細紗成紗質量。同時,因為減輕了氣圈紗與導紗鉤的滑動摩擦,也減輕了導紗鉤的捻陷作用,使捻度更容易傳遞到紡紗段,有利於提高紡紗段紗線強力而減少斷頭。當合成孔短軸孔徑為0.1mm時,氣圈紗只在約0.5mm的微小的兩個弧段間滑動摩擦,由於上、下半孔導紗片中間有過紗間隙,並不在同一層面上,而且細紗機內側方向半孔在下,外側方向半孔在上,又由於從前鉗口到導紗鉤處紡紗段有約60°導紗角β存在,並不會增加紗線與導紗鉤的包圍弧長,所以,0.1mm短軸孔徑合成導紗孔仍能正常紡紗,且能最大限度地降低導紗鉤處產生的毛羽數。
4、本實用新型由上導紗片、下導紗片、支撐杆及緊固件等組合而成,上導紗槽和下導紗槽的槽底均為圓弧結構,內表面非常光滑;且小直徑半圓孔的加工比現用導紗鉤的螺旋導紗孔加工要容易,光潔度更高。水平方向摩擦動程縮短後,為防止導紗孔短時間磨出溝槽,本實用新型設計的上導紗片和下導紗片均採用碳化鎢硬質合金製作,所以具有非常高的耐磨性。
5、使用本實用新型進行接頭操作時,值車工無需像使用現用導紗鉤那樣,右手持紗掛上鋼絲圈後需沿導紗鉤平面繞導紗鉤一周(360°),而只需將紗線從下導紗片的V形槽口帶進,然後沿左前水平方向繞半周(180°)即可;而且使用本實用新型進行接頭操作時,值車工也無需像使用現用導紗鉤那樣,右手持紗繞過導紗鉤前端後,還須將紗頭提起並在垂直於導紗鉤平面的垂面內,由細紗機外側向內側方向繞過近180°角才能將紗頭接到前羅拉鉗口,而只需在垂面內繞約30°角即可將紗頭接到前羅拉鉗口,這樣可明顯節省接頭操作時間,從而節省人力資源和提高細紗機效率。
下面通過附圖和實施例,對本實用新型做進一步的詳細描述。
附圖說明
圖1為現有環錠紡細紗機所用A型導紗鉤的結構示意圖。
圖2為現有環錠紡細紗機所用B型導紗鉤的結構示意圖。
圖3為現有環錠紡細紗機所用導紗鉤的使用狀態圖。
圖4為本實用新型的結構示意圖。
圖5為本實用新型支撐杆的結構示意圖。
圖6為本實用新型下導紗片的結構示意圖。
圖7為本實用新型上導紗片的結構示意圖。
附圖標記說明:
1-1—上導紗片; 1-11—第一連接孔; 1-12—上導紗槽;
1-2—下導紗片; 1-21—第二連接孔; 1-22—下導紗槽;
1-3—支撐杆; 1-31—前U形彎; 1-4—緊固件;
1-5—擒紗槽; 1-6—合成導紗孔; 1-7—鎖緊螺母;
2-1—葉子板; 2-2—紗條; 2-3—前羅拉鉗口;
2-4—鋼領; 2-5—鋼絲圈; 2-6—氣圈紗;
2-7—紗管。
具體實施方式
如圖4至圖7所示,本實用新型包括上導紗片1-1、下導紗片1-2和支撐杆1-3,所述上導紗片1-1設置在支撐杆1-3的前端上側,所述下導紗片1-2設置在支撐杆1-3的前端下側,所述上導紗片1-1的一端開有第一連接孔1-11,所述下導紗片1-2的一端開有第二連接孔1-21,所述上導紗片1-1與下導紗片1-2經穿過第一連接孔1-11和第二連接孔1-21的緊固件1-4固定連接,所述上導紗片1-1與下導紗片1-2之間形成過紗間隙,所述上導紗片1-1的另一端設置有上導紗槽1-12,所述下導紗片1-2的另一端設置有下導紗槽1-22,所述上導紗槽1-12與下導紗槽1-22之間形成合成導紗孔1-6。
本實用新型細紗機組合式微孔高耐磨導紗鉤使用時,合成導紗孔1-6的中心必須位於錠子的中心線上。上導紗片1-1與下導紗片1-2之間形成過紗間隙,以便於細紗斷頭時接頭操作和開車時生頭操作。
本實施例中,所述上導紗槽1-12和下導紗槽1-22的形狀均為V字形。
本實施例中,所述上導紗槽1-12和下導紗槽1-22的底部均為圓角結構,內表面非常光滑,能進一步減少毛羽數,提高細紗質量。
本實施例中,所述上導紗槽1-12的槽口向細紗機內側方向設置,所述下導紗槽1-22的槽口向細紗機外側方向設置。
本實施例中,所述合成導紗孔1-6的形狀為橢圓形,或者為類橢圓形;所述合成導紗孔1-6的短軸長度為0.1mm~0.5mm,即可形成微孔結構,可根據對成紗毛羽的要求自由調控。
本實施例中,所述支撐杆1-3的前端向斜下方伸出。
如圖4所示,所述支撐杆1-3的前端端部設置有擒紗槽1-5,紡紗斷頭時,能擒住紗線頭,防止幹擾相鄰氣圈。
如圖4所示,所述支撐杆1-3的前端設置有用於固裝上導紗片1-1和下導紗片1-2的前U形彎1-31,所述上導紗片1-1設置在前U形彎1-31的上側,所述下導紗片1-2設置在前U形彎1-31的下側;所述緊固件1-4為緊固螺栓,所述緊固件1-4依次穿過第二連接孔1-21、前U形彎1-31和第一連接孔1-11,所述緊固件1-4的端部設置有鎖緊螺母1-7。
本實施例中,所述上導紗片1-1和下導紗片1-2均為碳化鎢硬質合金導紗片,具有非常高的耐磨性。
以上所述,僅是本實用新型的較佳實施例,並非對本實用新型作任何限制,凡是根據本實用新型技術實質對以上實施例所作的任何簡單修改、變更以及等效結構變換,均仍屬於本實用新型技術方案的保護範圍內。