一種鋅鐵氧體的製備方法與流程
2023-07-30 08:23:46
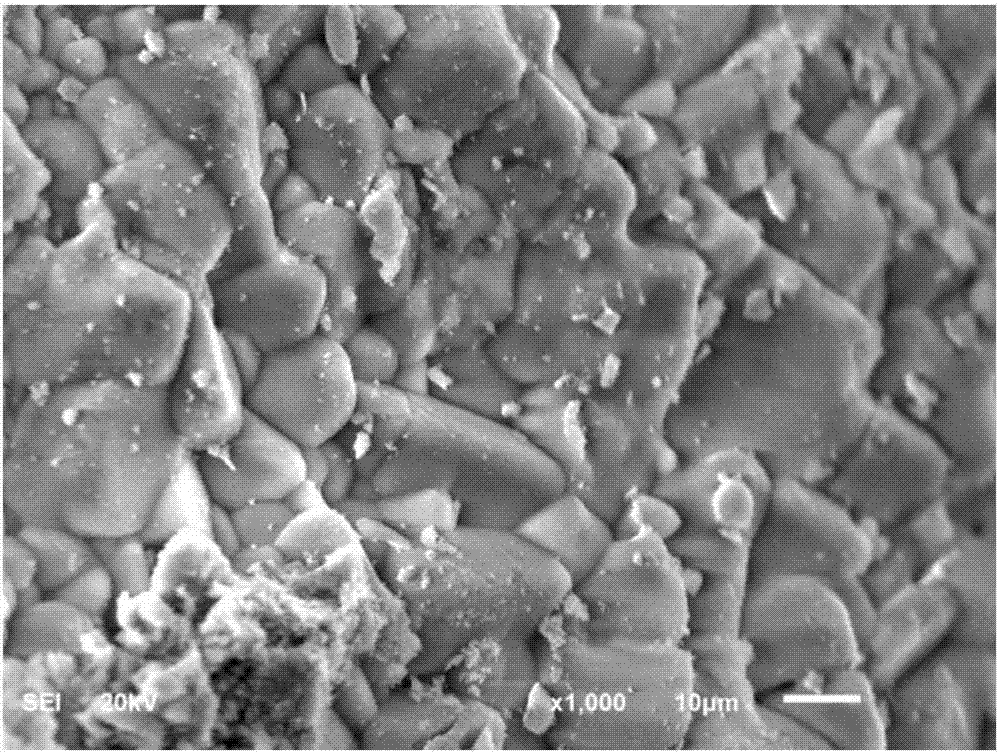
本發明屬於鋅鐵氧體材料製備技術領域,涉及一種鋅鐵氧體的製備方法,特別涉及一種利用電爐煉鋼粉塵製備鋅鐵氧體的方法。
背景技術:
鋅鐵氧體(znfe2o4)屬正尖晶石結構,是一種重要的功能材料,因具有優異的磁學性能、電特性、吸波和光催化性能,而被廣泛應用於磁存儲,生物醫學,光催化,氣敏傳感,電化學等領域。
目前,鋅鐵氧體的製備方法主要有:化學共沉澱法、溶膠-凝膠法、水熱法、高能球磨法、自蔓延高溫合成法、模板法等。
共沉澱法是將沉澱劑加入含zn2+、fe3+金屬鹽溶液中進行共沉澱處理,得到產品的前驅體,再對前驅體進行熱處理得到鋅鐵氧體。其優點在於:操作方便、設備簡單、易控制粒度等;缺點在於:反應原料的配比、反應溫度和氧化時間對鋅鐵氧體的影響較大。
溶膠-凝膠法是通過將含zn2+、fe3+金屬有機鹽或無機鹽水解製成溶膠,再將溶膠縮聚、蒸發形成凝膠,之後將凝膠體煅燒即可得到鋅鐵氧體。其優點在於:工藝過程溫度低,產品純度高,產物粒徑小,分散均勻;缺點在於:工藝條件不易控制,處理時間長,有機物原料對人體有害。
水熱法是製備結晶良好的鋅鐵氧體主要方法之一。與其它溼化學方法相比,水熱法的優點是粒子純度高、分散性好、晶形好且可控制,生產成本低,用水熱法製備的粉體一般無需燒結,這就可以避免在燒結過程中晶粒會長大而且雜質容易混入等缺點;但存在設備要求高、技術難度大、成本高、安全性能差等缺點。
高能球磨法是以金屬氧化物fe2o3和zno為原料,按照一定比例放入球磨機中充分球磨得到鋅鐵氧體的一種方法。高能球磨法具有產量高、工藝簡單、化學成分易控制等優點,但是存在耗能大、反應時間長、容易引入雜質、分散性較差等不足之處。
自蔓延高溫合成法即燃燒合成法,是利用反應過程中產生的較高熱量來維持反應持續進行的一種鋅鐵氧體的合成方法。其優點是工藝簡單,產物純度高、反應時間短、能耗低;缺點是反應條件苛刻、難以規模化生產。
模板法是以特定結構的基質作為模板來合成具有特定形貌尺寸的鋅鐵氧體的新方法。其優點是尺寸形態可控、成品粒度分布均勻;缺點是工藝複雜、易於引入雜質。
微乳液法是製備鋅鐵氧體材料的方法之一,在表面活性劑作用下,溶劑形成粒徑為納米級的微結構,從根本上限制了晶核的生長,因而更容易製備出鋅鐵氧體顆粒。該方法的優點是粒徑分布窄、設備簡單、能耗低、成品性能突出;缺點是成本高、後續處理困難。
目前鋅鐵氧體的各種製備方法多以純度較高的含鋅化合物和含鐵化合物為原料,這無疑增加了生產成本。
電爐煉鋼粉塵中不僅含有大量的鐵、碳元素,還含有鋅、鉛、錳等少量有用元素。目前,處理電爐煉鋼粉塵的主要方法是:
(1)將電爐煉鋼粉塵固化填埋、露天堆放或者低價出售。該方法主要問題是對生態環境造成了破壞,且有價金屬資源沒有得到回收利用。
(2)將電爐煉鋼粉塵經過燒結後返回高爐重新利用。該方法雖然有效回收了fe元素,但對於其他元素未能得到回收,而是在煙塵中富集,造成了資源的浪費,部分元素特別是zn在高爐煙道的富集還會引起高爐結瘤,影響高爐的使用壽命。
(3)將電爐煉鋼粉塵經過環形爐、迴轉窯或轉底爐等高溫還原後得到金屬化球團和含氧化鋅、氧化鉛煙塵。該方法設備投資較大,金屬化球團需要一定的機械強度和合適的金屬化率。此外,該方法只達到了對電爐煉鋼粉塵中的鋅和鐵分離和富集的目的,產品工業附加值低。
(4)將電爐煉鋼粉塵經過酸法或鹼法溼法工藝得到金屬鋅或鋅化合物。這些方法僅對粉塵中的鋅進行回收,資源綜合利用率低,處理粉塵的經濟效益差。
技術實現要素:
本發明的目的是為了克服上述鋅鐵氧體的製備方法和電爐煉鋼粉塵的處理方法存在的問題和不足,提供一種原料來源方便,資源綜合利用率高,原料成本低,設備簡單,操作方便的鋅鐵氧體的製備方法。
為了達到上述目的,本發明實現目的所採取的技術方案是:
一種鋅鐵氧體的製備方法,其步驟是:
1、往電爐煉鋼粉塵中加入hcl溶液,在50~70℃溫度下攪拌浸出;
2、過濾後,按h2o2與fe2+摩爾比為1~3:1向濾液中加入h2o2,再將氟化鹽按溶液中物質的量濃度比f+:ca2+=2.5~3.5:1.0加入到上述氧化後液中,淨化除雜後,補加含鋅物質,將淨化後液中鋅鐵物質的量濃度比控制在zn:fe=0.5~0.6:1.0,加入無機鹼,將溶液ph值調到8~11,進行沉鋅鐵,得到含鋅鐵沉澱物;
3、過濾並洗滌步驟2得到的含鋅鐵沉澱物,烘乾後,於600~700℃煅燒6~8小時,得到按質量百分比,其成分含量為:zn27.09~27.11,fe46.16~46.20,o26.66~26.73,k0.0011~0.0015,ca0.011~0.012,na0.0014~0.0018,al0.0152~0.0157的鋅鐵氧體粉體產物。
進一步的,步驟1所述的浸出的工藝條件是:液固比為4~7:1,hcl的濃度為3~4mol/l,浸出時間為1.5~2.5小時。
進一步的,步驟2所述的氟化鹽為naf、kf、nh4f中的一種。
進一步的,步驟2所述的無機鹼為nh3·h2o、(nh3)2co3、nh3hco3、na2co3、nahco3、naoh、koh中的一種。
進一步的,步驟2所述的含鋅物質為znco3、zn2(oh)2co3、zn(oh)2、zno、zncl2、zn(no3)2、金屬zn中的一種。
進一步的,步驟2所述的淨化除雜的條件是:淨化溫度為50~70℃,攪拌時間為0.5~1.5小時。
進一步的,步驟2所述的沉鋅鐵的條件是:溫度為65~80℃,攪拌時間為0.5~1.5小時。
本發明的一種利用電爐煉鋼粉塵製備鋅鐵氧體材料的方法,具有的有益效果和特點主要是:
(1)與現有的鋅鐵氧體的製備方法相比較,本發明不以純度較高的含鋅化合物和含鐵化合物為原料,而是直接以電爐煉鋼粉塵為原料製備鋅鐵氧體,原料來源方便,且原料成本低。採用溶液浸出、氧化和中和等常規溼法冶金方法製備鋅鐵氧體,設備簡單,操作方便。
(2)與現有的電爐煉鋼粉塵的處理方法相比較,本發明將電爐煉鋼粉塵以hcl溶液浸出、fe2+氧化、氟化鹽淨化除雜和鹼中和共沉澱,鋅和鐵最終以鋅鐵氧體產品形式回收,產品附加值高,有利於提高企業經濟效益。電爐煉鋼粉塵中的鋅和鐵等資源得到充分利用,資源綜合利用率高。
附圖說明
圖1為本發明的工藝流程圖。
圖2為採用本發明所製備的鋅鐵氧體形貌的掃描電子顯微鏡圖。
圖3為採用本發明所製備的鋅鐵氧體的x射線衍射圖。
具體實施方式
為了使本發明的目的、技術方案及優點更加清楚明白,以下結合附圖及實施例,對本發明進行進一步的詳細說明。應當理解,此處所描述的具體實施例僅僅用於解釋本發明,並不用於限定本發明。
實施例1
按圖1所示,取所述的電爐煉鋼粉塵10g,向其中加入4mol/lhcl溶液,在液固比為4:1,60℃溫度下攪拌浸出2小時,過濾後,按h2o2與fe2+摩爾比為2:1向濾液中加入h2o2,反應0.5小時後,將naf按溶液中物質的量濃度比f+:ca2+=2.5:1.0加入到上述氧化後液中淨化除雜,保持溫度60℃,攪拌1小時,過濾後,往濾液中補加zncl2,將淨化後液中鋅鐵物質的量濃度比控制在zn:fe=0.6:1.0,加入naoh溶液,將溶液ph值調到11,保持溫度75℃,攪拌時間1小時,過濾並洗滌含鋅鐵沉澱物,烘乾後,於700℃煅燒6小時,得到4.23g鋅鐵氧體粉體產物,其成分按質量百分比為:zn27.09,fe46.16,o26.73,k0.0011,ca0.012,na0.0014,al0.0055。
實施例2
按圖1所示,取所述的電爐煉鋼粉塵10g,向其中加入3mol/lhcl溶液,在液固比為5:1,70℃溫度下攪拌浸出2.5小時,過濾後,按h2o2與fe2+摩爾比為2:1向濾液中加入h2o2,反應0.5小時後,將nh4f按溶液中物質的量濃度比f+:ca2+=3.5:1.0加入到上述氧化後液中淨化除雜,保持溫度50℃,攪拌1.5小時,過濾後,往濾液中補加zno,將淨化後液中鋅鐵物質的量濃度比控制在zn:fe=0.55:1.0,加入nh3·h2o溶液,將溶液ph值調到9.5,保持溫度65℃,攪拌時間1.5小時,過濾並洗滌含鋅鐵沉澱物,烘乾後,於600℃煅燒8小時,得到4.05g鋅鐵氧體粉體產物,其成分按質量百分比為:zn27.11,fe46.20,o26.66,k0.0013,ca0.012,na0.0015,al0.0152。
實施例3
按圖1所示,取所述的電爐煉鋼粉塵10g,向其中加入3.5mol/lhcl溶液,在液固比為7:1,50℃溫度下攪拌浸出1.5小時,過濾後,按h2o2與fe2+摩爾比為2:1向濾液中加入h2o2,反應0.5小時後,將kf按溶液中物質的量濃度比f+:ca2+=3.0:1.0加入到上述氧化後液中淨化除雜,保持溫度70℃,攪拌1小時,過濾後,往濾液中補加znco3,將淨化後液中鋅鐵物質的量濃度比控制在zn:fe=0.5:1.0,加入na2co3溶液,將溶液ph值調到8,保持溫度75℃,攪拌時間1小時,過濾並洗滌含鋅鐵沉澱物,烘乾後,於650℃煅燒7小時,得到4.36g鋅鐵氧體粉體產物,其成分按質量百分比為:zn27.10,fe46.19,o26.68,k0.0015,ca0.011,na0.0018,al0.0157。
以上所述,僅為本發明較佳的具體實施方式。當然,本發明還可有其它多種實施例,在不背離本發明精神及其實質的情況下,任何熟悉本技術領域的技術人員,當可根據本發明作出各種相應的等效改變和變形,都應屬於本發明所附的權利要求的保護範圍。