用於確定氧氣吹煉過程中的點火時間點的方法和設備與流程
2023-08-07 09:58:26 1
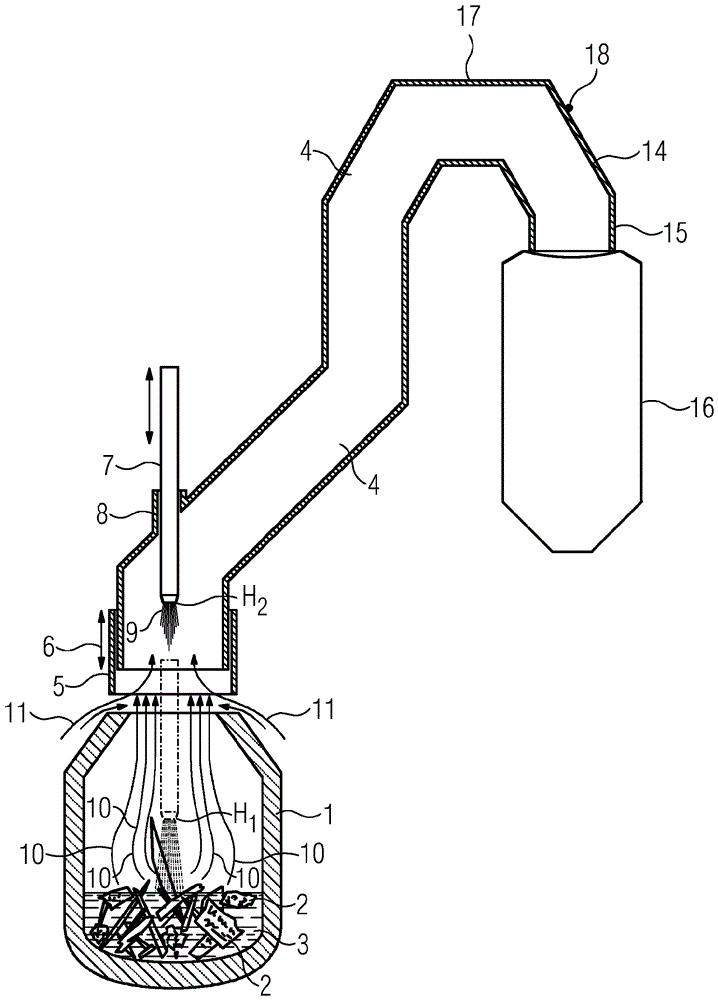
本發明涉及一種用於確定氧氣煉鋼過程中,特別是LD方法中的轉爐中的點火時間的方法,其中確定氧氣量值和排氣溫度值,以及對應的設備。
鋼生產的目的是製造鋼,換句話說,製造具有低碳含量和所需特性例如硬度、防鏽性或可成形性的鐵合金。
在吹煉過程中,生鐵用氧氣精煉。減少碳成分(精煉)的氧化過程在該方法中帶來足夠的熱量以保持鋼熔化,因此在轉爐中不需要外部供熱。吹煉過程可以再分為氧氣煉鋼過程和底吹過程。底吹過程包括Bessemer方法、Thomas方法、熟鐵和早期高爐。最知名的氧氣煉鋼過程是LD方法。
在Linz-Donawitz方法(簡稱LD法)中,將金屬廢料和熔融生鐵倒入LD轉爐中,並加入成渣組分。通過噴槍將氧氣吹到熔體上。在該過程中,不希望的伴隨元素如硫,磷,碳等在鋼中燃燒並進入煙道氣或爐渣中。由於與燃燒相關的巨大的熱產生,所添加的廢金屬被熔化和/或可以減少生鐵的使用,並且通過添加廢金屬和礦石來冷卻熔體。鼓風時間為10至20分鐘,並且被選擇為使得實現所需的脫碳和不期望的雜質的燃燒和期望的最終溫度。通過將轉爐容器傾倒入鋼包內來出成品鋼。首先,含鐵浴在超過1600 的溫度下通過出鋼孔被排到鋼包中,然後從轉爐邊緣上將渣倒出。
轉爐可以被安裝在具有滑動門的轉爐殼體(「狗窩」)中,並且轉爐殼體的任務是保護周圍環境免受來自轉爐的噴射以及將在轉爐出口和排氣冷卻罩之間的氣體浪湧引導到冷卻罩中或者引導到二次氣體提取中。赤鐵礦板主要用作火側襯裡;某些區域接收耐火搗固,或者在柔性頂板的區域中還接收耐熱鋼板。
然而,轉爐中的燃燒並不是在氧氣最先被噴入時就立即開始,而是通常被延遲幾秒到高達90秒後在不可預先確定的時間自發地開始。對於精確的點火時間的了解是非常重要的,因為氧氣僅僅從此時與熔體反應,並且該反應的實際持續時間對於過程控制和鋼的品質,特別是其碳含量是決定性的。與其它參數一起,點火時間使得能夠從開始到結束地控制吹煉過程。通過精確地知道點火時間,可以提高鋼的品質,並且不再需要重新噴入氧氣(後吹)或重新滲碳(與進一步使用硫相關)。提高了吹煉過程的可重複性,這也對工藝鏈的進一步的步驟產生積極的影響,例如二次冶金。
當前採用的方法基於不是完全可靠的手動輸入或自動化系統。到現在為止,點火時間由操作者通過觀察轉爐來確定,因此在過程控制系統中手動輸入點火時間。然而,強煙和粉塵的形成損害操作者的明確的點火識別,就像操作者缺乏經驗或任何不注意一樣。然而,該方法與實際點火時間和點火時間的記錄之間的幾秒、經常高達30秒的時間延遲相關聯。但是,點火時間的這種延遲確定對於過程控制是不利的。此外,回想起來不能精確地確定點火時間,而僅僅近似地確定。
噴槍頭部中的熱膨脹也可以用於確定點火時間(通過應變計)。然而,這需要相當多的技術開支並且僅能夠實現點火時間的延遲確定。
例如,在狗窩打開時,操作人員可立即看到反應並識別點火時間。然而,一個打開的狗屋總會帶來巨大的安全風險。因此,點火時間可以通過按下按鈕手動設置。操作人員還可以通過安裝的攝像機在監視器上跟隨反應。
自動光學方法是將攝像機記錄連結到分析攝影材料的評估系統,從而將點火時間自動地中繼到過程模型。然而,具有錄像攝像機的解決方案導致大量的安裝費用,因為攝像機必須相應地被冷卻,並且必須保證不會被汙染的小孔,換句話說,轉爐出口的無障礙觀察。
在氧氣煉鋼過程的背景下,從DE 10 2012 224 184 A1公開了記錄多個運行參數並且通過關聯所述運行參數確定運行的目標變量。要記錄的運行參數包括排氣組成、排氣溫度和轉爐火焰的輻射功率等。指定的目標變量是最終的碳含量、溫度和熔體的組成。
WO 2007/109 850 A1公開了在氧氣高爐運行的背景下,通過感光元件確定排氣組成並且在高爐運行期間考慮該組成。
從專利說明書AT 299 283B中已知通過光電池,換句話說是廣義上的電子管測量火焰亮度以確定精確的點火時間。光電池根據AT 299 283B布置的,其光軸水平地在轉爐出口的上邊緣上方約10cm,使得當防火罩打開時,其檢測發射到轉爐出口的上邊緣和防火罩(萃取器罩)的下邊緣之間的輻射。現在調節光電池,使得其控制電流在大於約1100,優選約1200的目標反應氣體的溫度下發生,並由此描述點火時間。光電池的控制電流觸發預定的「冶金」氧氣量的測量。
AT 299 283 B的方法的缺點在於,這僅提供單個數據值,這樣的值經常不足以用於氧氣煉鋼過程的可靠的點火識別。光電池還可以由一次性故障觸發,例如,靠近光電池的單個火花,雖然氧氣的實際點火還沒有發生。
在AT 509 866 A4中,最早從氧氣鼓風或達到一定的O2流量開始,藉助於CCD圖像傳感器記錄轉爐出口和萃取器罩之間的區域的多個按時間順序的圖像,基於由該傳感器測量的輻射強度,隨著時間的流逝確定輻射強度的進程,並且將實現預定輻射強度或輻射強度預定增加的時間作為點火時間。
因此,本發明的一個目的是詳細說明一種允許可靠且冗餘地確定點火時間的方法。第二個目的是公開一種特別適合於執行該方法的設備。
與該方法相關的目的通過公開一種用於確定在轉爐中的氧氣煉鋼過程中,特別是LD方法中的點火時間的方法來實現,其中,確定頂吹氧氣量的氧氣量值和由於氧氣煉鋼過程產生的排氣中的當前排氣溫度的排氣溫度值,並且同時達到所述氧氣量的預定氧氣閾值值和排氣中的預定排氣溫度閾值值的時間被設定為點火時間。
與設備相關的目的通過公開一種用於確定氧氣煉鋼過程,特別是LD方法中的點火時間的設備來實現,包括用於注入氧氣的轉爐,其中,確定頂吹氧氣量的氧氣量值並且確定由於氧氣煉鋼過程產生的排氣中的當前排氣溫度的排氣溫度值,並且同時實現氧氣量的預定氧氣閾值值和排氣中的預定排氣溫度閾值值的時間可以被建立為點火時間。
在吹煉過程中,將氧氣吹到液態金屬熔體上。這種累積的、吹入的O2量通過例如體積流量測量傳感器測量並且與當前測量的排氣溫度值一起例如被中繼到計算機系統。已經認識到,一旦發生點火,就可以建立排氣溫度值的增加。如果該值在可獲得一定頂吹O2量的同時超過預設閾值值,則可以斷定實現點火。換句話說,通過O2和溫度條件的與關聯,例如,以O2量>270Nm3且溫度>500的形式,產生非常魯棒且可再現的點火條件,這使得操作者的相對不可靠的點火識別被淘汰。
本發明實現了可靠的自動點火識別。本發明還使得能夠更精確地獲得過程模型的目標值。減少後吹例行程序也是可能的,並且可以節省吹煉過程所需的O2。根據本發明,現在可以產生可再現的鋼品質。此外,如果已經存在O2體積流量測量,則可以實現成本有效的實施。如果不存在這種測量,則安裝這種測量的更新操作也是成本有效的。本發明能夠最大限度地使用轉爐氣體,因為該氣體可以通過氣量計中的初級除塵被可靠地供給。通過二級除塵也可以獲得由於過晚檢測到O2吹氣過程的點火而導致的爆炸危險的降低。通過本發明,有利地可以產生被更好調節的過程模型,並且因此可以產生更好的鋼品質。簡單的實施也是有利的。
在從屬權利要求中列出了其它有利的措施,這些措施可以根據需要彼此組合以實現其他優點。
在一個有利的實施例中,在排氣煙道上記錄排氣溫度值,特別是在排氣煙道的垂直部分上或者在以流體技術的方式布置在蒸發冷卻器進口前面的部分上。也可以在蒸發冷卻器的蒸發冷卻器進口處記錄排氣溫度值。在那裡溫度的測量特別簡單和/或測量裝置的安裝特別容易。
優選地,連續地確定氧氣量值和排氣溫度值。一旦氧氣的頂吹開始和/或在頂吹期間和/或在頂吹過程期間,也可以連續地確定氧氣量值和排氣溫度值。可以通過更少的測量值來實現該方法的簡化。然而,其他位置也是可以想到的。
在優選實施例中,氧氣量值藉助於體積流量測量傳感器來確定。氧氣通過噴槍吹入轉爐中,其中噴槍通過閥連接到氧氣源。優選地,氧氣量值現在由安裝在所述閥的區域中,特別是安裝在所述閥上的體積流量測量傳感器確定。在那裡可以特別簡單地確定氧氣量值。
優選地,氧氣閾值量值和/或排氣溫度值是憑經驗確定的。也就是說,用於用信號通知點火的閾值值是憑經驗確定的,例如基於測量結果系列。這些可以變化,例如,取決於轉爐和轉爐內容物。閾值值可以存儲在資料庫中。這些也可以以一定間隔更新。
優選地,當前測量的排氣溫度值和氧氣量值被中繼到計算單元。在優選實施例中,計算單元包括分析算法,所述分析算法至少將當前測量的排氣溫度值和氧氣量值與排氣溫度值和氧氣閾值量值進行比較。
優選地,分析算法在計算單元中直到氧氣鼓風開始時才被激活。然而,分析算法只能在氧氣鼓風期間在計算單元中被激活。在吹煉過程中,將氧氣吹到液態金屬熔體上。這種累積的、吹入的O2量通過例如體積流量測量傳感器測量並且與當前測量的排氣溫度值一起被中繼到計算機系統。分析算法在計算機系統上運行。分析算法現在基於以下相關性:如果已經發生點火,則可以建立排氣溫度值的增加。如果在存在一定頂吹O2量的同時該值超過預設的閾值值,則可以斷定點火已經發生。通過來自當前進展中的過程階段的反饋,可以激活與其相關的評估。因此,分析算法可以在裝料、後吹、分離等期間不被使用,但在鼓風循環開始時被使用。
此外,可以提供在計算單元中的對溫度升高與氧氣量值之間的關係的監測。如果不發生這種關係,特別是如果不發生溫度升高,則優選地可以發出警報。還可以提供警報系統和/或用戶界面(HMI =人機界面系統)和/或多媒體設備,警報被中繼到此。
警報系統然後可以首先將警報中繼到用戶界面(HMI =人機界面系統)和/或多媒體設備。由於溫度升高和O2濃度之間的關係是吹煉過程的典型特徵,這同樣可以由計算機系統監測。如果這種關係在足夠長的時間之後不發生,則可以假定吹煉過程中存在問題。該警報可以被提供給警報系統,或者通過用戶界面(HMI)或其他移動可視化設備被信號通知給操作人員。
還可以提供具有包含多個光電二極體的傳感器的攝像機,優選具有CCD圖像傳感器,其中攝像機的光軸與轉爐出口和萃取器罩之間的間隙對準,以及用於評估攝像機的圖像的計算機,其中計算機被編程使得由於從傳感器接收的輻射強度,該計算機確定輻射強度隨時間的變化過程。最早(因為否則不是來自點火的其他火焰可能仍然在明亮地燃燒)開始於氧氣鼓風(例如,在達到一定的氧氣流量時),通過包含多個光電二極體的傳感器記錄在轉爐出口和萃取器罩之間的同一區域的多個按時間順序的圖像,其中每個光電二極體對應於一個像素,優選地通過CCD圖像傳感器,基於由光電二極體測量的輻射強度確定輻射強度隨時間的變化過程,並且將達到預定輻射強度或輻射強度的預定增加的時間確定為點火時間。這兩種設備/方法也可以被關聯以確定點火時間。關聯這兩種方法提供了點火時間的更好結果。
根據本發明的方法和根據本發明的設備實現了可靠的自動點火識別。觸發時間的精度也可以進一步提高。還可以實現潛在過程模型的目標值的更精確的實現和後吹例行程序的減少。有利地,也節省了在吹煉過程中所需的O2。可靠的自動點火識別保證生產可重複的鋼品質。換句話說,更好地調整後過程模型使得生產更好的鋼品質成為可能。
由於過晚檢測到O2吹煉過程的點火導致的二級除塵中的爆炸風險的降低是特別有利的。方法和/或設備的成本有效的實施也是可能的,因為O2體積流量測量容易安置。轉爐氣體的最大使用也是可能的,因為這可以通過在氣量計中的初級除塵來可靠地控制。本發明還可以被成本有效地結合到現有的狀態監測系統中。
本發明的附加特徵、特性和優點將從以下參考附圖的描述中顯現。附圖示出了圖解視圖:
圖1:根據本發明的具有傳感器的轉爐的截面側視圖,
圖2:該方法的圖解視圖。
雖然通過優選的示例性實施例更詳細地示出和描述了本發明,但是本發明不限於所公開的示例。本領域技術人員可以在不脫離由所附權利要求限定的本發明的範圍的情況下推導出其變型。
圖1示出了轉爐1,其中有待精煉的承諾,即廢金屬和塊狀生鐵2和熔融生鐵3。排氣煙道4布置在轉爐出口上方,轉爐1朝著煙道向上逐漸變細。這可以分為多個部分並且以流體技術的方式連接到蒸發器冷卻器16。可以沿著雙箭頭6下降和/或升高的萃取器罩5圍繞排氣煙道4。它用於密封轉爐出口並在精煉期間收集新鮮氣體。可以提升和降低的噴槍7通過排氣煙道4的孔8插入到轉爐1中。
噴槍7從位置H2被下降到操作位置H1,在位置H2中噴槍7以連續衝程被拉出並且氧氣源尚未打開。在到達操作位置H1之前不久,打開氧氣源並釋放吹煉所需的氧氣9。噴槍7進一步被降低,同時氧氣9從出口被釋放,直到其到達操作位置H1,其由點劃線示出。一旦達到操作位置H1,如果沒有點火延遲,則應該立即發生點火。然而,如果點火被突出的廢金屬或類似物延遲,則一定量的氧氣逸出,其不參與精煉反應並且必須被考慮。
如果發生點火,則主要包括一氧化碳(CO)的反應氣體10從轉爐1上升。然後,如圖1所示,萃取器罩5打開,使得所謂的漏風11通過萃取器罩5和轉爐1和/或其轉爐出口之間的間隙流入。反應氣體10的一氧化碳與空氣燃燒。鼓風氧氣與來自生鐵的碳在點火時開始的燃燒產生明亮的白色火焰和/或氣體。
在氧氣煉鋼過程中,在高壓(高達12巴)下將氧氣吹送到熔融金屬浴上。在劇烈反應中,氧將鐵氧化成氧化鐵和將碳氧化成一氧化碳(CO),其中氧化鐵立即將氧轉移到伴隨的元素。在反應的中心,即焦點處,溫度為2500至3000,並且出現猛烈的、翻滾的沸騰,這在該過程期間將所述浴的尚未被精煉的部分帶到所述焦點。
精確識別點火時間對於通過過程模型的精確過程控制是非常重要的。從這時起,由鼓風噴槍頂吹的O2開始與液態金屬熔體反應。如果這個時間未被正確識別,則其可能具有諸如例如過程模型的目標值的不精確實現的後果。也可能需要後吹例行程序。
作為「後吹」的結果,也可能發生增加的O2消耗。作為不精確檢測的時間的另一結果,也可能產生不可再現的鋼品質。該過程產生的CO氣體也不能使用-它被完全燃燒。
當可燃性氣體通過袋式過濾器系統被進給時,還可能存在增加的二級除塵的爆炸風險。此外,當前使用的方法基於不是完全可靠的手動輸入或自動化系統。
因此,在LD過程中與操作者的視覺點火識別相關的困難是眾所周知的:可再現性差或不可能,需要有經驗的坩堝司機,狗窩必須在吹煉階段開始時打開,造成潛在的安全風險,等等。如果沒有操作者方面的點火信號,則這可能導致排氣煙道4的負載增加。在一些系統中,然後在足夠長的時間之後自動產生點火信號,包括與實際點火時間相比顯著延遲的信號。
現在通過本發明避免了這些問題。
所提出的方法和/或設備是基於對與排氣中的排氣溫度值相關的氧氣量值,即累積的吹入O2量的分析。這兩個參數具有明確的關係,由此實現點火識別。
圖2在圖解視圖中示出了所述方法。
根據本發明,確定頂吹氧氣量的氧氣量值110,並且確定由於氧氣煉鋼過程產生的排氣中的當前排氣溫度的排氣溫度值20,其中同時達到所述氧氣量的預定氧氣閾值值和排氣中的預定排氣溫度閾值值時的時間被建立為點火時間。
在吹煉過程中,將氧氣吹到液態金屬熔體上。氧氣量值110,也被描述為吹入O2量110,例如通過體積流量測量傳感器測量並且與當前測量的排氣溫度值20一起被中繼到計算機系統40。分析算法30在計算機系統40上運行。例如在蒸發冷卻器進口15(圖1)上記錄排氣溫度值20。還可以在排氣煙道4(圖1)上記錄排氣溫度值20,特別是在排氣煙道4(圖1)的以流體技術方式緊接在蒸發冷卻器進口15(圖1)前面的部分14上。還可以在排氣煙道4(圖1)的豎直部分17(圖1)上記錄該溫度值。溫度傳感器18(圖1)的安裝在這些點處特別簡單。
氧氣量值110和排氣溫度值20可以連續地確定,或者在開始頂部吹氧之後和/或在頂吹期間連續地確定。其他排列也是可以想到的,只要它們實現它們的目的。
分析算法30現在基於以下關係:如果已經發生點火,則可以建立排氣溫度值20的增加。如果該排氣溫度值20超過預設的閾值值,同時存在一定的頂吹O2量110,則可以斷定點火已經發生。
根據本發明,O2和溫度條件的與關聯導致非常魯棒和可再現的點火條件,例如,以氧氣量值>270Nm3與排氣溫度值>500的形式,其使得操作者的相對不可靠的點火識別被淘汰。可以基於測量結果系列憑經驗確定要預先確定的氧氣量的氧氣閾值值和要預先確定的用於信號通知點火的排氣溫度閾值值。這些可以例如根據轉爐而變化。然而,也可以使用用於建立閾值值的其他數學方法。
通過來自當前被使用的過程階段50的反饋,可以激活對其其評估。因此,分析算法30可以在裝料、後吹、分離等期間不被使用,但在吹風循環開始時是被使用。
由於溫度升高和氧氣量值之間的關係是吹煉過程的典型特徵,這同樣可以由計算機系統40監測。如果這種關係在足夠長的時間之後不發生,則可以假設吹煉過程存在問題。該警報可以被提供給警報系統60,或者藉助於用戶界面(人機界面)70或另一個移動可視化設備80用信號通知操作人員。
所述設備尤其適合於執行根據本發明的方法。
本發明可以消除與點火識別相關的「人為不確定因素」,導致更高和/或更可再現產品品質。坩堝司機不再需要擔心點火識別和/或過程控制被簡化(節省了控制元件)。此外,可以增加安全性,因為狗窩不再需要在吹煉階段開始時打開。
附圖標記列表
1 轉爐,尤其是鋼轉爐
2 廢金屬和塊狀生鐵
3 熔融生鐵
4 排氣煙道
5 萃取器罩
6 萃取器罩5被降低和/或升高的方向
7 噴槍
8 噴槍7的孔
9 氧氣
10 反應氣體
11 漏風
14 排氣煙道斜向下的部分
15 蒸發冷卻器進口
16 蒸發冷卻器
17 排氣煙道的水平部分
18 溫度傳感器
20 排氣溫度值
30 分析算法
40 計算機系統
50 過程階段
60 警報系統
70 用戶界面(HMI=人界面系統)
80 多媒體設備
110 氧氣量值
H1噴槍7的操作位置
H2噴槍7的位置,其中氧氣源被打開。