脫除廢棄拋光粉中矽鋁雜質的方法與流程
2023-08-08 18:36:16 2
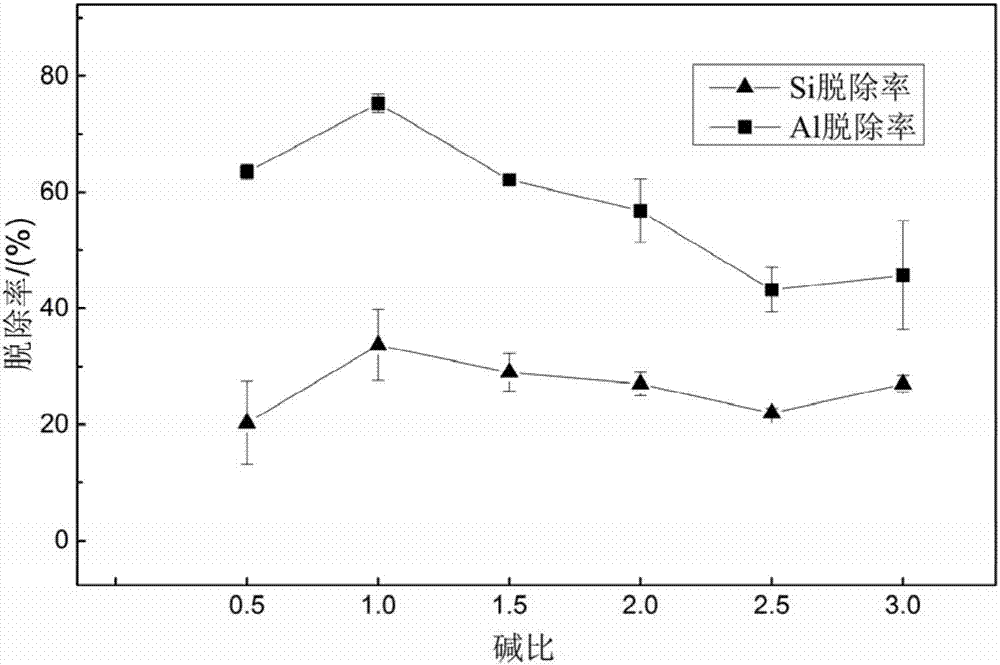
本申請涉及固廢處理技術領域,尤其涉及一種脫除廢棄拋光粉中矽鋁雜質的方法。
背景技術:
稀土拋光粉由於其理想的拋光效果,廣泛應用於一些光學玻璃器件的拋光及精密儀器的精磨等方面。在拋光磨削的過程中,被加工部件的表面磨削下來的玻璃顆粒、石英、金屬材料等進入到拋光粉中,而使得拋光粉的性能減弱而失效。隨著拋光粉用量的增加,大量的稀土拋光粉作為固體廢棄物堆存下來。稀土資源不可再生,且地殼中含量不集中,導致其加工成本高。在歐盟、美國和日本,稀土資源目前已被列為「緊缺」資源。雖然中國的稀土資源位居世界前列,但其作為重要的戰略資源以及其不可替代性,稀土資源越來越受到人們的重視。通過廢棄拋光粉的再利用,不僅可以回收稀土,而且還可以減弱廢棄拋光粉對環境的影響。
從廢棄拋光粉中沉澱分離稀土元素時,廢棄拋光粉中的主要雜質si和al會影響分離效果。因此,有必要先將廢棄拋光粉中的si和al雜質脫除。針對矽鋁雜質的脫除,傳統技術有採用物理化學法去除廢舊稀土螢光粉中的玻璃雜質,包括前段300-800℃焙燒,後續熱鹼浸出矽鋁的工藝。傳統技術還有預先高溫處理(950℃),再進行低溫鹼浸實驗使粉煤灰中矽和鋁雜質分步溶出。傳統技術還有採用了中溫(250℃)鹼浸並添加激發劑的方法回收矽鋁,平均溶出率為88.70%。傳統技術有利用低溫鹼浸的方式處理廢棄拋光粉,得到新生拋光粉。上述這些方法均存在高溫焙燒工序或反應溫度條件較高,或其反應溶劑對環境影響較大,而且矽鋁脫除效果有待進一步提高。
技術實現要素:
基於此,有必要針對上述技術問題,提供一種反應溫度較低,且對環境影響小,矽鋁脫除效果好的脫除廢棄拋光粉中矽鋁雜質的方法。
一種脫除廢棄拋光粉中矽鋁雜質的方法,包括:
提供含有矽鋁雜質的廢棄拋光粉;
提供濃度為0.25摩爾/升至1.75摩爾/升的鹼溶液,並將所述廢棄拋光粉加入所述鹼溶液中進行浸出反應,浸出反應時間為65分鐘至105分鐘,浸出反應溫度為85攝氏度至95攝氏度,所述鹼溶液中的鹼與所述廢棄拋光粉的質量比為0.75~1.5;
將浸出反應後的混合液降溫至室溫,從而獲得反應後的浸出液;以及
對所述浸出液進行過濾處理,過濾得到脫除出所述矽鋁雜質的廢棄拋光粉。
在其中一個實施例中,所述提供含有矽鋁雜質的廢棄拋光粉包括:
提供含有矽鋁雜質的稀土拋光粉;
在80攝氏度至110攝氏度乾燥處理所述含有矽鋁雜質的稀土拋光粉以去除水分;
對乾燥處理後的所述含有矽鋁雜質的稀土拋光粉進行研磨以及過篩處理從而獲得所述含有矽鋁雜質的廢棄拋光粉。
在其中一個實施例中,在所述提供含有矽鋁雜質的稀土拋光粉之後,所述方法進一步包括:對所述矽鋁雜質的稀土拋光粉進行破碎處理。
在其中一個實施例中,所述鹼溶液為氫氧化鈉溶液、氫氧化鉀溶液中的一種或多種。
在其中一個實施例中,所述將所述經乾燥處理的廢棄拋光粉加入所述鹼溶液中進行浸出反應的步驟包括:
提供反應容器,將濃度為0.25摩爾/升至1.75摩爾/升的鹼溶液以及廢棄拋光粉加入所述反應容器中,所述鹼溶液中的鹼與所述廢棄拋光粉的質量比為0.75~1.5;
加熱所述反應器使得所述反應器內的溫度為85攝氏度至95攝氏度,使所述反應容器中發生浸出反應,浸出反應時間為65分鐘至105分鐘。
在其中一個實施例中,所述浸出反應過程中,所述鹼溶液中的鹼與所述廢棄拋光粉的質量比為0.75-1.25,所述浸出反應時間為80分鐘至100分鐘,所述鹼溶液的濃度為1摩爾/升至1.25摩爾/升。
在其中一個實施例中,所述浸出反應過程中,所述鹼溶液中的鹼與所述廢棄拋光粉的質量比為1,所述浸出反應溫度為90攝氏度,所述浸出反應時間為90分鐘,所述鹼溶液的濃度為1摩爾/升。
在其中一個實施例中,所述將浸出反應後的混合液降溫至室溫,從而獲得反應後的浸出液包括:
提供溫度為0攝氏度至10攝氏度的清洗水;
將所述清洗水通入所述反應容器中,以將浸出反應後的混合液降溫至室溫從而獲得反應後的浸出液。
在其中一個實施例中,所述所述將浸出反應後的混合液降溫至室溫,從而獲得反應後的浸出液中,所述浸出反應後的混合液在5分鐘至10分鐘內降溫至室溫。
在其中一個實施例中,所述對所述浸出液進行過濾處理,過濾得到脫除所述含矽鋁雜質的廢棄拋光粉包括:
提供離心裝置和真空抽濾裝置;
將所述反應後的浸出液倒入所述離心裝置中,對所述反應後的浸出液進行離心處理;以及
將離心處理後的所述浸出液倒入所述真空抽濾裝置中,對所述浸出液進行抽濾處理。
本申請提供的脫除廢棄拋光粉中矽鋁雜質的方法,通過浸出反應來脫除矽鋁雜質。通過提供濃度為0.25摩爾/升至1.75摩爾/升的鹼溶液,並將所述廢棄拋光粉加入所述鹼溶液中進行浸出反應,浸出反應時間為65分鐘至105分鐘,浸出反應溫度為85攝氏度至95攝氏度,所述鹼溶液中的鹼與所述廢棄拋光粉的質量比為0.75~1.5。上述方法在較低的溫度下通過將所述廢棄拋光粉加入所述鹼溶液中進行浸出反應,從而脫除廢棄拋光粉中的矽鋁雜質。由於沒有引入反應溶劑,從而具有反應溫度條件低,且對環境影響小,矽鋁脫除效果好的的優點。
附圖說明
圖1為本申請一個實施例中的脫除廢棄拋光粉中矽鋁雜質的方法的流程圖;
圖2為本申請一個實施例中的脫除廢棄拋光粉中矽鋁雜質的方法中鹼比對脫除雜質的影響圖;
圖3為本申請一個實施例中的脫除廢棄拋光粉中矽鋁雜質的方法中浸出時間對脫除雜質的影響圖;
圖4為本申請一個實施例中的脫除廢棄拋光粉中矽鋁雜質的方法中溫度對雜質脫除的影響圖;
圖5為本申請一個實施例中的脫除廢棄拋光粉中矽鋁雜質的方法中鹼濃度對雜質脫除的影響圖。
具體實施方式
為了使本申請的目的、技術方案及優點更加清楚明白,以下結合附圖對本申請的脫除廢棄拋光粉中矽鋁雜質的方法。應當理解,此處所描述的具體實施例僅僅用以解釋本申請,並不用於限定本申請。
請參見圖1,本申請實施例提供一種脫除廢棄拋光粉中矽鋁雜質的方法,包括:
s102,提供含有矽鋁雜質的廢棄拋光粉;
s104,提供濃度為0.25摩爾/升至1.75摩爾/升的鹼溶液,並將所述廢棄拋光粉加入所述鹼溶液中進行浸出反應,浸出反應時間為65分鐘至105分鐘,浸出反應溫度為85攝氏度至95攝氏度,所述鹼溶液中的鹼與所述廢棄拋光粉的質量比為0.75~1.5;
s106,將浸出反應後的混合液降溫至室溫,從而獲得反應後的浸出液;
s108,對所述浸出液進行過濾處理,過濾得到脫除出所述矽鋁雜質的廢棄拋光粉。
步驟s102中,所述含有矽鋁雜質的廢棄拋光粉可以直接從拋光工廠獲得。所述含有矽鋁雜質的廢棄拋光粉中的矽來自於拋光過程中,進入拋光粉中的微細玻璃粉末。廢棄拋光粉中的鋁則是來自拋光過程中加入的沉澱劑氯化鋁的水解產物氫氧化鋁。具體地,所述含有矽鋁雜質的廢棄拋光粉中,除含有矽鋁雜質外,還含有一定比例的稀土元素。可以理解,所述矽鋁雜質的廢棄拋光粉可以是塊材也可以是粉狀,還可以是液態的漿料。
步驟s104中,所述廢棄拋光粉加入所述鹼溶液中進行浸出反應,從而使得所述廢棄拋光粉中的矽鋁雜質溶於所述鹼溶液中。所述鹼溶液可以是氫氧化鉀或氫氧化鈉溶液中的一種,或者兩者的混合。
步驟s106中,所述將浸出反應後的混合液降溫至室溫的方式不限。當所述浸出反應在較大體積的反應器中進行時,可以通過向所述反應器中通入冷水的方式使得浸出反應後的混合液降溫。當所述浸出反應在較小體積的反應器中進行時,也可以通過直接給所述反應器的外壁衝冷水以給所述浸出反應後的混合液降溫。
步驟s108中,通過對所述浸出液進行過濾處理,可以得到脫除出矽鋁雜質的廢棄拋光粉。由於矽鋁雜質已經溶解在所述浸出液中,過濾後的所得到的固態物質就是去除矽鋁雜質的拋光粉。可以理解,本發明的脫除廢棄拋光粉中矽鋁雜質的方還可以用於廢棄拋光粉的回收利用。
本實施例中,通過提供濃度為0.25摩爾/升至1.75摩爾/升的鹼溶液,並將所述廢棄拋光粉加入所述鹼溶液中進行浸出反應,浸出反應時間為65分鐘至105分鐘,浸出反應溫度為85攝氏度至95攝氏度,所述鹼溶液中的鹼與所述廢棄拋光粉的質量比為0.75~1.5。上述方法在較低的溫度下通過將所述廢棄拋光粉加入所述鹼溶液中進行浸出反應,從而脫除廢棄拋光粉中的矽鋁雜質。由於沒有引入反應溶劑,從而具有反應溫度條件低,且對環境影響小,矽鋁脫除效果好的的優點。
在一個實施例中,所述步驟s102還可以包括以下步驟:
s202,提供含有矽鋁雜質的稀土拋光粉;
s202,在80攝氏度至110攝氏度乾燥處理所述含有矽鋁雜質的稀土拋光粉以去除水分;以及
s202,對乾燥處理後的所述含有矽鋁雜質的稀土拋光粉進行研磨以及過篩處理從而獲得所述含有矽鋁雜質的廢棄拋光粉。
通過對所述含有矽鋁雜質的稀土拋光粉進行乾燥處理,可以脫除所述含有矽鋁雜質的稀土拋光粉中的水分。當所述含有矽鋁雜質的稀土拋光粉的水分被脫除後,就可以避免所述含有矽鋁雜質的稀土拋光粉由於含水量大易於結團。通過對所述乾燥後的含有矽鋁雜質的稀土拋光粉進行研磨以及過篩處理,可以獲得粒度分布相對均勻的稀土拋光粉,並且細粒有利於後續與溶液充分接觸,確保反應更徹底。由於所述含有矽鋁雜質的稀土拋光粉具有較小的且分布均勻的粒徑,所述含有矽鋁雜質的稀土拋光粉可以與所述鹼溶液充分接觸以及反應,從而提高了反應的效率,進一步可以提高矽鋁雜質的脫除效率。上述的研磨處理,可以通過各種方式進行。所述過篩處理可以採用30~60目篩進行。
可以理解,當所述矽鋁雜質的稀土拋光粉中包括較大的顆粒時,所述步驟s202之後,還可以包括對所述矽鋁雜質的稀土拋光粉進行破碎處理的步驟。經過破碎處理,可以使的脫水乾燥過程中水分脫除的更加徹底。
在一個實施例中,所述步驟s104可以包括以下步驟:
s302,提供反應容器,將濃度為0.25摩爾/升至1.75摩爾/升的鹼溶液以及廢棄拋光粉加入所述反應容器中,所述鹼溶液中的鹼與所述廢棄拋光粉的質量比為0.75~1.5;
s304,加熱所述反應器使得所述反應器內的溫度為85攝氏度至95攝氏度,使所述反應容器中發生浸出反應,浸出反應時間為65分鐘至105分鐘。
所述反應容器不限,可以根據實際反應的廢棄拋光粉的量選擇磁力攪拌恆溫加熱器。選擇具有加熱功能的反應容器,以便於加熱。
在一個實施例中,所述浸出反應過程中,所述鹼溶液中的鹼與所述廢棄拋光粉的質量比為0.75-1.25,所述浸出反應時間為80分鐘至100分鐘,所述鹼溶液的濃度為1摩爾/升至1.25摩爾/升。本實施例中,上述浸出反應過程中的參數選擇,可以使得本實施例中的脫除廢棄拋光粉中矽鋁雜質的方法具有較高的矽鋁脫除率。
在一個實施例中,所述步驟s106可以通過通入冷水的方式給所述浸出反應後的混合液降溫。當所述浸出反應在反應容器中發生時,所述步驟s106包括以下步驟:
s402,提供溫度為0攝氏度至10攝氏度的清洗水;
s404,將所述清洗水通入所述反應容器中,以將浸出反應後的混合液降溫至室溫從而獲得反應後的浸出液。
所述清洗水優選為去離子水,或者自來水,避免引入鋁離子,影響了矽鋁雜質的脫除效率。所述清洗水通入所述反應容器中,可以快速將所述浸出反應後的混合液降溫。優選地,控制所述浸出反應後的混合液在5分鐘至10分鐘內降溫至室溫。在反應溫度較高的情況下(90℃左右),隨時間的增長,矽鋁會發生「二次沉澱」反應。因此,通過控制所述浸出反應後的混合液降溫的時間在5分鐘至10分鐘內,可以避免溶液中的矽鋁再次結合生成矽鋁沉澱,從而提高矽鋁的脫除效率。可以理解,在給所述浸出反應後的混合液降溫時,可以先停止對所述反應容器加熱。
在一個實施例中,所述步驟s108可以包括以下步驟:
s502,提供離心裝置和真空抽濾裝置;
s504,將所述反應後的浸出液倒入所述離心裝置中,對所述反應後的浸出液進行離心處理;以及
s506,將離心處理後的所述浸出液倒入所述真空抽濾裝置中,對所述浸出液進行抽濾處理。
所述離心裝置為低速離心分離機,用於將所述反應後的浸出液在低速離心機中,轉速3000-5000r/min進行離心處理10-15min,從而可以實現所述反應後的浸出液中的固液分離。所述真空抽濾裝置為真空泵與抽濾瓶相結合,用於對所述浸出液進行抽濾處理。所述反應後的浸出液先經過離心處理後,再進行抽濾處理可以提高所述矽鋁雜質的脫除效率。可以理解,在工業生產中,可以不經過離心,直接進行抽濾,或者輸送至板框壓濾機,濾去水分。
在一個實施例中,所述鹼溶液為氫氧化鈉溶液,所述廢棄拋光粉除了矽鋁雜質外,還含有一定比例的稀土元素。具體地,所述廢棄拋光粉的成分組成如下表:
圖2為本申請一個實施例中的脫除廢棄拋光粉中矽鋁雜質的方法中鹼比對脫除雜質的影響圖。圖2中的鹼比為鹼溶液中的鹼與所述廢棄拋光粉的質量比。圖2中,鹼濃度為2mol/l,反應溫度為60℃,反應時間為30min。當鹼比為1時,矽和鋁的脫除率均達到最大值,分別為33.66%和95.28%。鹼比過低時,溶液中的oh-不足以與樣品中的矽鋁反應。在鹼比為0.5時,矽鋁的脫除率僅為20.25%和63.46%。隨著鹼比的升高,oh-分別於矽鋁化合物進行充分反應,脫除率呈升高的趨勢,並在鹼比為1時達到最大值。鹼比為1時,溶解到溶液中al濃度較高,達到95.28%。鹼比繼續增加,矽、鋁脫除率均有下降趨勢,鋁脫除率的下降趨勢較為明顯。根據阿布拉莫夫的na2o-al2o3-cao-sio2-h2o系相圖可知,鋁的存在會影響矽的溶解度,導致矽的脫除率並不理想。同時鹼比增大,由相圖知,矽鋁會反應形成結晶,而使得兩者的脫除率均有所下降。因此,將鹼比設定為1,即能得到相對理想的脫除效果。
圖3為本申請一個實施例中的脫除廢棄拋光粉中矽鋁雜質的方法中浸出時間對脫除雜質的影響圖。圖3中,鹼濃度2mol/l,鹼比1,反應溫度90℃。由圖3可以得出,在鹼浸過程中,在10~90min反應時間內,隨反應時間延長,矽鋁脫除率變化趨勢相似,均不斷升高。在反應時間為90min時,廢棄拋光粉中的矽鋁雜質與氫氧化鈉的反應就已經接近平衡,矽鋁脫除率達到最大值(52.35%、76.85%)。繼續延長反應時間,矽鋁脫除率不再升高,且有下降的趨勢。在鹼比,溫度和鹼濃度不變的條件下,反應時間過長(超過90min),會使得矽鋁結合形成「二次沉澱」。因此,反應時間確定為90min較為適宜。
圖4為本申請一個實施例中的的脫除廢棄拋光粉中矽鋁雜質的方法中溫度對雜質脫除的影響圖。圖4中,鹼濃度2mol/l,鹼比2,反應時間為30min。由圖4可知,在0-90℃範圍內,隨溫度升高,氫氧化鈉浸出液中離子運動加劇,對矽鋁脫除率有促進作用。反應溫度在90℃時,矽和鋁的脫除率達到最大值,分別為57.57%,75.10%。溫度繼續升高,矽鋁脫除率呈現下降趨勢。主要是由於,在100℃時,矽鋁雜質會與naoh生成類似於沸石的結構,導致廢棄拋光粉中的si和al脫除率降低。
sio2(s,非晶質)+2oh-(aq)→sio3-(aq)+h2o(l)(1)
根據溫元凱文算法,可以計算出不同溫度下相應反應的吉布斯能變。在30℃~130℃以上,矽鋁雜質與naoh的反應的吉布斯自由能變始終為負值。而反應(3)隨吉布斯自由能變會隨溫度升高而急劇減小,因此,較高的溫度會使溶液中的溶解的矽鋁化合物離子,又重新結合生成矽鋁復鹽。因此,在90℃浸出效果相對理想,溫度過高,不僅對設備要求高,而且增加能耗,經濟成本相應增加。基於上述理由,溫度在85℃~95℃範圍內最為合適。優選的溫度為90℃。
圖5為本申請一個實施例中的脫除廢棄拋光粉中矽鋁雜質的方法中鹼濃度對雜質脫除的影響圖。圖5中,反應時間為90min,鹼比為1,反應溫度為90℃。由圖5可知,當鹼濃度在0-0.5mol/l之間,隨著鹼濃度的升高,體系中oh-濃度增大,樣品與鹼接觸反應的機率就越大,矽鋁脫除率明顯升高。樣品中鋁雜質溶於鹼生成alo2-,廢棄拋光粉樣品中的矽以矽酸鈉形式進入溶液。當na2sio3濃度超過溶液的平衡濃度後,如果溶液中有足夠濃度的alo2-,就會生成水合鋁矽酸鈉結晶沉澱物,而使得矽鋁雜質的在溶液中溶解率下降。
na2o·nsio2+2naalo2+h2o→na2o·a2o3·nsio2+naoh(4)
在鹼濃度為0.5mol/l時,矽脫除率達到最大(98.71%)。鋁脫除率在鹼濃度為1mol/l時,達到最大值97.93%。為實現同樣理想的矽鋁脫除效果,將naoh濃度確定在1mol/l時,矽鋁脫除率分別達到95.37%、97.93%。
綜合以上內容,本發明一個實施例中的脫除廢棄拋光粉中矽鋁雜質的方法,所述浸出反應過程中,所述鹼溶液中的鹼與所述廢棄拋光粉的質量比為1,所述浸出反應溫度為90攝氏度,所述浸出反應時間為90分鐘,所述鹼溶液的濃度為1摩爾/升。在上述條件下,矽鋁脫除率分別為95.37%、97.93%。
以上所述實施例的各技術特徵可以進行任意的組合,為使描述簡潔,未對上述實施例中的各個技術特徵所有可能的組合都進行描述,然而,只要這些技術特徵的組合不存在矛盾,都應當認為是本說明書記載的範圍。
以上所述實施例僅表達了本申請的幾種實施方式,其描述較為具體和詳細,但並不能因此而理解為對本申請專利範圍的限制。應當指出的是,對於本領域的普通技術人員來說,在不脫離本申請構思的前提下,還可以做出若干變形和改進,這些都屬於本申請的保護範圍。因此,本申請專利的保護範圍應以所附權利要求為準。