晶片級封裝發光器件及其製造方法與流程
2023-08-03 18:16:16 1
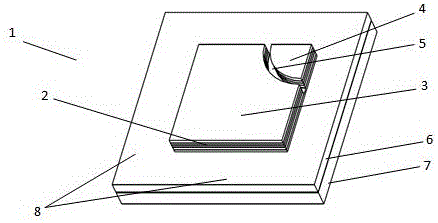
本發明涉及光電器件製造技術領域,具體涉及一種晶片級封裝發光器件及其製造方法。
背景技術:
晶片級封裝發光器件封裝體積小,封裝可靠性高,並且可以製作均勻的光轉換層,實現均勻光色特性,近年來得到了廣泛的應用。在中國臺灣、日韓、歐美等地的LED大公司紛紛發布了自己的晶片級封裝LED產品。白光晶片屬於晶片級尺寸水平封裝,配合白光晶片應用的二次光學元件的體積將大幅度縮小。綜合各企業產品,共同的特點是基於倒裝晶片的基礎上,使發光器件的封裝體積更小,光學、熱學性能更好,同時因省略了導線架與打線的步驟,使其後道工序更加便捷。但是目前的晶片級封裝發光器件的LED色溫還是不夠穩定,還存在很多缺點。同時其製造工藝也還存在很多缺點。
技術實現要素:
本發明的目的是解決現有技術的缺陷,提供一種晶片級封裝發光器件,採用的技術方案如下:
一種晶片級封裝發光器件,包括LED外延片,所述LED外延片包括正電極、負電極和電極溝道,所述正電極和負電極位於同一平面,所述電極溝道位於正電極與負電極之間,還包括石墨烯層和螢光粉薄層,所述石墨烯層分布於LED外延片的下方並與之連接,所述螢光粉薄層位於石墨烯層下方並與之連接。
作為優選,所述石墨烯層為平面形狀。
作為優選,所述LED外延片依次包括n型層、量子阱層、p型層和正電極層,將LED外延片與石墨烯層連接時,採用雷射剝離技術將藍寶石襯底全部剝離,使LED外延片的n型層直接與石墨烯層連接。
作為優選,所述石墨烯層的厚度為0.05mm~0.5mm,長寬均為2mm~3mm。
作為優選,所述螢光粉薄層選用Ce:YAG螢光粉材料與矽膠混合製成,通過噴塗方法噴塗於石墨烯層下方,其厚度為0.05mm~0.2mm。
作為優選,使用回流焊接爐對螢光粉薄層進行固化。
在石墨烯層的下方,選用Ce:YAG螢光粉材料與矽膠混合,採用噴塗方法製備螢光粉薄層,其螢光粉薄層厚度為0.05~0.2mm,再經過回流焊接爐對螢光粉薄層進行固化,螢光粉具有較薄厚度,固化時間比較短。
本發明的另一目的是解決現有技術的缺陷,提供一種晶片級封裝發光器件的製造方法,採用的技術方案如下:
一種晶片級封裝發光器件的製造方法,包括:
製備LED外延片陣列:採用MOCVD設備在藍寶石襯底上生長LED外延片陣列,然後用雷射剝離技術將藍寶石襯底全部剝離,使LED外延片的最底部是n型層;
採用離子體增強化學氣相沉積法製造平面形狀的石墨烯層陣列:將含碳的氣態物質在高溫和高真空的環境下,生成石墨烯薄膜,再用雷射切割技術將石墨烯薄膜切割成平面形狀的石墨烯層陣列;
選用Ce:YAG螢光粉材料與矽膠混合製成螢光粉,採用噴塗方法在石墨烯層陣列的背面噴塗螢光粉薄層陣列,並使用回流焊接爐對螢光粉薄層陣列進行固化;
利用銀獎膠,採用固晶技術方法或鍵合技術方法,將LED外延片的 n型層直接與石墨烯薄層陣列連接,構成發光器件陣列;
採用雷射切割方法將發光器件陣列切割成獨立的發光器件。
作為優選,所述LED外延片包括正電極、負電極和電極溝道,所述正電極和負電極位於同一平面,所述電極溝道位於正電極與負電極之間。
作為優選,所述LED外延片依次包括n型層、量子阱層、p型層和正電極層。
作為優選,所述石墨烯層的厚度為0.05mm~0.5mm,長寬均為2mm~3mm,所述螢光粉薄層厚度為0.05mm~0.2mm。
與現有技術相比,本發明的有益效果:
1、石墨烯層具有很好的熱傳導性能,螢光粉薄層與石墨烯層直接接觸,能保證螢光粉薄層具有較低溫度,維持發光器件色溫穩定。
2、簡化了製造工藝,使用回流焊接爐對螢光粉薄層進行固化,與傳統在高溫烤箱中的固化流程相比節省了固化時間,降低了耗電。
附圖說明
圖1是本發明實施例的結構示意圖;
圖2是本發明實施例的LED外延片的結構示意圖;
圖3是本發明實施例發光器件焊接方法示意圖;
圖4是本發明實施例石墨烯陣列和螢光粉薄層陣列的結構示意圖;
圖5是本發明實施例發光器件陣列的結構示意圖。
具體實施方式
下面結合附圖和實施例對本發明做進一步詳細說明。
實施例:
如圖1所示,一種晶片級封裝發光器件,包括LED外延片2,所述LED外延片2包括正電極3、負電極4和電極溝道5,所述正電極3和負電極4位於同一平面,所述電極溝道5位於正電極3與負電極4之間,還包括平面形狀的石墨烯層6和螢光粉薄層7,所述石墨烯層6分布於LED外延片2的下方並與之連接,所述螢光粉薄層7位於石墨烯層6下方並與之連接。
如圖2所示,所述LED外延片依次包括n型層11、量子阱層10、p型層9和正電極層8,將LED外延片2與石墨烯層6連接時,使外延片n型層11直接與石墨烯層6連接。
所述石墨烯層6的厚度為0.05mm~0.5mm間,長寬尺寸均為2mm~3mm。
所述螢光粉薄層7選用Ce:YAG螢光粉材料與矽膠混合製成,通過噴塗方法噴塗於石墨烯層下方,其厚度為0.05mm~0.2mm。
使用回流焊接爐對螢光粉薄層7進行固化。
如圖3所示,本實施例發光器件焊接時,採用雙面鋁基電路板13,在電路板上製作正電極焊盤14、負電極焊盤15和石墨烯層焊接焊盤21,其厚度為0.05mm~0.1mm,保證LED外延片2的側面發光有效被阻擋或者反射到螢光粉薄層7中,使得石墨烯層6直接焊接到雙面鋁基電路板13,石墨烯層具有很好的熱傳導性能,螢光粉薄層與石墨烯層接觸,保證螢光粉具有較低溫度,維持發光器件色溫穩定。
本實施例的發光器件的製備方法如下:
製備LED外延片陣列:採用MOCVD設備在藍寶石襯底上生長LED外延片陣列,然後用雷射剝離技術將藍寶石襯底全部剝離,使LED外延片的最底部是n型層;
採用離子體增強化學氣相沉積法製造平面形狀的石墨烯層陣列16:將含碳的氣態物質在高溫和高真空的環境下,生成石墨烯薄膜,再用雷射切割技術將石墨烯薄膜切割成平面形狀的石墨烯層陣列16;
選用Ce:YAG螢光粉材料與矽膠混合製成螢光粉,採用噴塗方法在石墨烯層陣列的背面噴塗螢光粉薄層陣列17,並使用回流焊接爐對螢光粉薄層陣列17進行固化;
利用銀獎膠,採用固晶技術方法或鍵合技術方法,將LED外延片的 n型層直接與石墨烯薄層陣列16連接,構成發光器件陣列20;
採用雷射切割方法將發光器件陣列20切割成獨立的發光器件。