一種鎂合金表面耐腐蝕高熵合金塗層及其製備方法與流程
2023-08-08 21:58:32 4
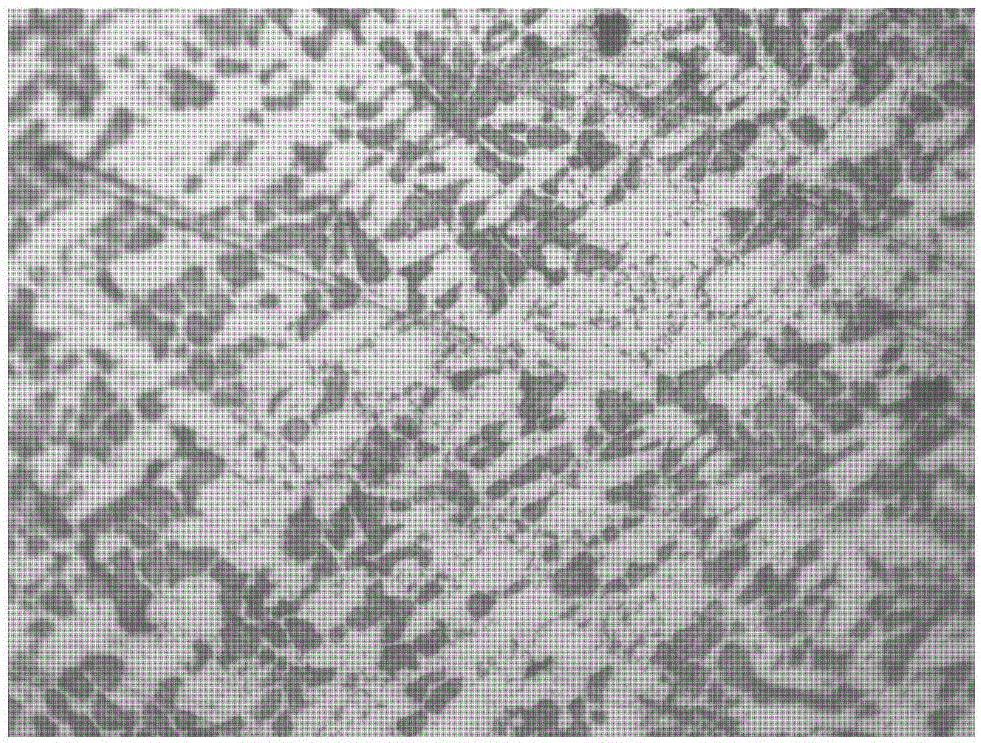
本發明涉及表面防護材料技術領域,更具體的涉及一種鎂合金表面耐腐蝕高熵合金塗層及其製備方法。
背景技術:
鎂合金材料比強度高,可回收利用且礦產資源豐富,在「海、陸、空、天」等許多工業領域都得到了廣泛應用。然而這些領域所需的構件結構複雜且需要適應各種服役環境。鎂合金材料性質活潑,特別是在腐蝕環境中很容易發生全面腐蝕或點蝕,形成的表面氧化膜疏鬆多孔緻密性差,很難對基體產生保護作用。因此,獲得鎂合金表面成分均勻,結構穩定,組織緻密,結合力強且耐腐蝕性能優良的保護塗層是提高基體鎂合金基體腐蝕性能的關鍵因素。
表面工程可通過表面塗覆、表面改性或多種表面技術複合處理,在保留鎂合金基體優異特性的同時,大幅提高鎂合金耐蝕性能,節能、節材、環保。目前,用於鎂合金表面腐蝕防護的方法主要有雷射熔敷、氣相沉積、微弧氧化、化學轉化、等離子處理、熱噴塗等。但上述方法存在膜層較薄、有環境汙染或不適合鎂合金這類高活性敏感基體等缺點。
技術實現要素:
本發明提供一種鎂合金表面耐腐蝕高熵合金塗層及其製備方法,採用磁控濺射技術在鎂合金基體上製備耐腐蝕高熵合金塗層,能夠形成與基材結合力強,孔隙率低和成分均勻的防護塗層。
具體的,鎂合金表面耐腐蝕高熵合金塗層,高熵合金塗層中包括Ti、Cr、Al、V和Si元素,所述Ti、Cr、Al、V和Si元素之間的摩爾比為1:1:1:1:1。
一種鎂合金表面耐腐蝕高熵合金塗層的製備方法,包括以下步驟:
S1、將摩爾比為1:1:1:1:1的Ti、Cr、Al、V和Si顆粒原料進行電弧熔煉,反覆電弧熔煉至少5次,使Ti、Cr、Al、V和Si顆粒原料均勻混煉,將混煉後的合金在模具中冷卻,將冷卻後的合金研磨加工後得到濺射靶材;
S2、清潔S1中得到的濺射靶材,去除靶材表面氧化物;
S3、使用超聲波清洗鎂合金基材,並將清洗後的鎂合金基材置於襯底託內放入進樣室,並對進樣室和濺射室內分別抽真空;
S4、將鎂合金基材襯底託放置在進樣室中的反濺射靶上,向進樣室中通入氬氣和氮氣,對鎂合金基材表面進行反濺射清洗;
S5、將鎂合金基材反轉180°,將鎂合金基材送入濺射室,調節濺射室真空度,利用清潔後的濺射靶材對鎂合金基材表面進行磁控濺射,使鎂合金基材表面完全覆蓋耐腐蝕高熵合金塗層。
優選的,步驟S1中,Ti、Cr、Al、V和Si顆粒原料的純度至少為99%。
優選的,步驟S1中,電弧熔煉前先抽取真空至0.01atm,再充入純氬氣至0.2atm,反覆抽氣充氣過程3次後進行電弧熔煉,電弧熔煉電流為500A。
優選的,步驟S1中,研磨加工後得到濺射靶材直徑為57.16mm,厚度為5.68mm,且濺射靶材表面平整光亮呈銀白色。
優選的,步驟S2中,將濺射靶材預鍍10min進行表面氧化物的去除,預鍍射頻功率為100W,工作壓力為39.65Pa。
優選的,步驟S3中,進樣室和濺射室內分別抽真空至真空度低於20Pa。
優選的,步驟S4中,進樣室真空度為10-4Pa時,通入氬氣和氮氣,所述氬氣和所述氮氣的體積比為0.091:1,調節真空度為3-5Pa時,開始對鎂合金基材表面進行反濺射清洗,射頻功率為150W,工作壓力為90Pa,反濺射靶與鎂合金基材之間的距離為9cm。
優選的,步驟S5中,濺射室真空度為5×10-5Pa時,通入氬氣和氮氣,所述氬氣和所述氮氣的體積比為0.091:1,調節真空度為3-5Pa時,開始對鎂合金基材表面進行磁控濺射,射頻功率為150W,工作壓力為90Pa,濺射靶材與鎂合金基材之間的距離為9cm。
本發明具有以下有益效果:
本發明應用磁控濺射技術製備的鎂合金表面耐腐蝕高熵合金塗層具有塗層與基材結合力強,塗層緻密孔隙率低,成分均勻且容易控制的優點;可以避免因熱輸入產生的相變和氧化製備得到緻密厚塗層,低溫高速的特性適用於鎂合金等敏感基體的腐蝕防護和尺寸恢復;製備得到的鎂合金表面耐腐蝕高熵合金塗層能夠在電化學和中性鹽霧腐蝕環境中對鎂合金基體提供長效防護。
附圖說明
為了更清楚地說明本發明實施例或現有技術中的技術方案,下面將對實施例或現有技術描述中所需要使用的附圖作簡單地介紹,顯而易見地,下面描述中的附圖僅僅是本發明的一些實施例,對於本領域普通技術人員來講,在不付出創造性勞動的前提下,還可以根據這些附圖獲得其他的附圖。
圖1為本發明實施例1提供的鎂合金表面耐腐蝕高熵合金塗層示意圖;
圖2為本發明實施例1提供的鎂合金表面耐腐蝕高熵合金塗層的微觀組織圖;
圖3為本發明實施例1提供的鎂合金表面耐腐蝕高熵合金塗層表面SEM圖;
圖4為本發明實施例1提供的鎂合金表面耐腐蝕高熵合金塗層橫截面SEM圖。
具體實施方式
下面將結合本發明實施例中的附圖,對本發明實施例中的技術方案進行清楚、完整地描述,顯然,所描述的實施例僅僅是本發明一部分實施例,而不是全部的實施例。基於本發明中的實施例,本領域普通技術人員在沒有做出創造性勞動前提下所獲得的所有其他實施例,都屬於本發明保護的範圍。
實施例1
本發明實施例1提供一種鎂合金表面耐腐蝕高熵合金塗層,包括Ti、Cr、Al、V和Si元素,所述Ti、Cr、Al、V和Si元素之間的摩爾比為1:1:1:1:1。
具體的,鎂合金表面耐腐蝕高熵合金塗層的製備方法,包括以下步驟:
S1、將摩爾比為1:1:1:1:1的Ti、Cr、Al、V和Si顆粒原料進行混合,所使用的顆粒原料至少純度為99%,將混合後的顆粒原料置於水冷銅模上,抽取真空至0.01atm,然後充入純氬氣使真空度至0.2atm,重複抽氣充氣過程三次後進行電弧熔煉,其中,純氬氣能夠防止合金被氧化,電弧熔煉電流為500A,將溶解並冷卻的合金塊翻面再次進行電弧熔煉,反覆熔煉5次,確保所有合金元素均勻混煉後,將冷卻得到的合金塊研磨加工形成濺射靶材,濺射靶材直徑為57.16mm,厚度為5.68mm,且濺射靶材表面平整光亮,無斑點及針孔狀缺陷,呈銀白色;
S2、以100W的鍍射頻功率,39.65Pa的工作壓力下將S1中得到的濺射靶材預鍍10min,清潔濺射靶材,去除靶材表面氧化物;
S3、選用5mm厚度的AZ31鎂合金板材為鎂合金基材,並使用超聲波清洗鎂合金基材,將清洗後的鎂合金基材置於襯底託內放入進樣室,一次可放置6片鎂合金基材樣品;然後將進樣室門鎖緊,關閉濺射室閘板閥,打開進樣室閘板閥,打開機械泵,對進樣室抽氣,當真空度低於20Pa時,關閉進樣室閘板閥,打開濺射室閘板閥,濺射室內抽真空,使真空度低於20Pa;
S4、利用機械手將鎂合金基材襯底託放置在進樣室中的反濺射靶上,反濺射靶為專用清洗靶材,抽氣使進樣室的真空度為10-4Pa時,通入氬氣和氮氣,通過質量流量計調節氬氣和氮氣的體積比為0.091:1,當複合計熱偶規指針指到5Pa時,打開RF電源,調節匹配電容C1和C2,將反射功率調至最小,反濺射靶材表面起輝,開始對鎂合金基體表面反濺射清洗;
S5、反濺射清洗後,關閉RF電源,打開進樣室閘板閥繼續抽真空,當進樣室的真空度在10-4Pa時,打開閘板閥,將反濺射清洗過的樣品用磁力傳遞杆交接叉管取下後,將反濺射靶材降下,並將樣品翻轉180°,使樣品朝下,送入主濺射室,抽氣使濺射室的真空度為5×10-5Pa時,通入氬氣和氮氣,通過質量流量計調節氬氣和氮氣的體積比為0.091:1,當複合計熱偶規指針指到3Pa時,打開RF電源,調節匹配電容C1和C2,將反射功率調至最小,使得清潔後的濺射靶材表面起輝,對鎂合金基體表面進行磁控濺射,使鎂合金基材表面完全覆蓋耐腐蝕高熵合金塗層。
將本實施例1中製備的鎂合金表面耐腐蝕高熵合金塗層進行檢測,通過對塗層表面及橫截面的微觀組織進行觀察,如圖1-圖4所示,本實施例1中製備的鎂合金表面耐腐蝕高熵合金塗層與鎂合金基材結合狀況良好,並且塗層組織緻密孔隙率低,能夠對鎂合金基材提供有效的防護。
儘管已描述了本發明的優選實施例,但本領域內的技術人員一旦得知了基本創造性概念,則可對這些實施例作出另外的變更和修改。所以,所附權利要求意欲解釋為包括優選實施例以及落入本發明範圍的所有變更和修改。
顯然,本領域的技術人員可以對本發明進行各種改動和變型而不脫離本發明的精神和範圍。這樣,倘若本發明的這些修改和變型屬於本發明權利要求及其等同技術的範圍之內,則本發明也意圖包含這些改動和變型在內。