加熱粘結式層疊芯製作裝置的製作方法
2024-03-24 15:41:05
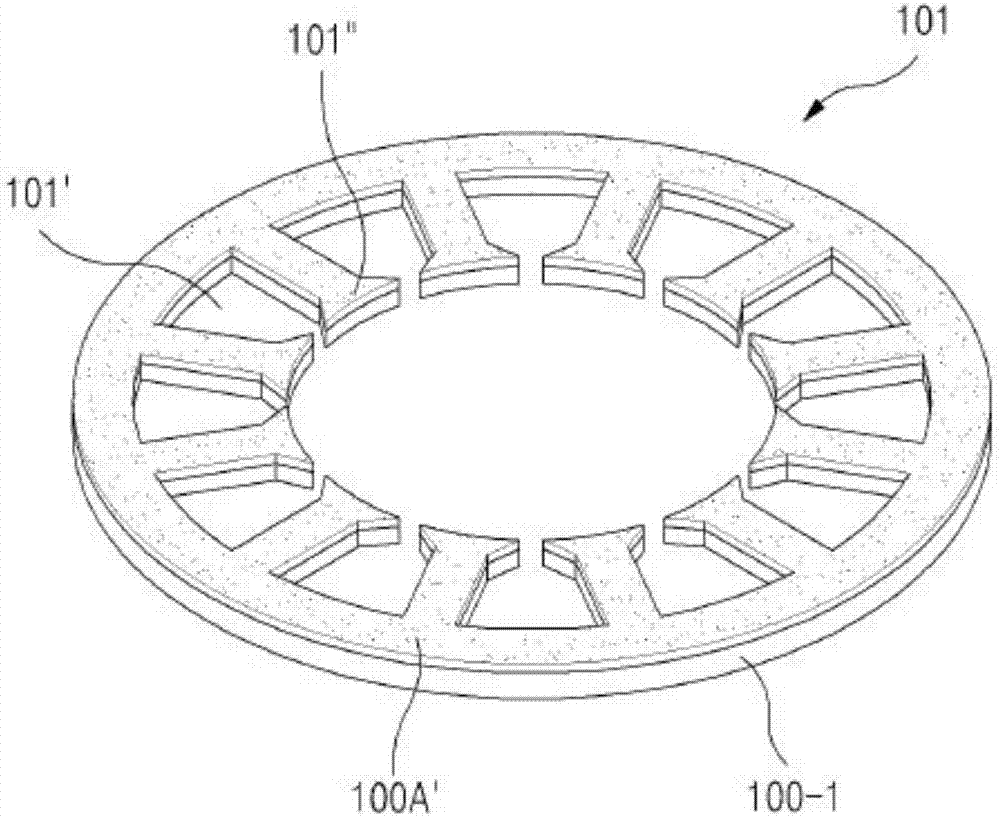
本發明涉及通過使薄片狀(laminar)部件層疊來製作的被用作馬達或發電機的定子或轉子的層疊芯的粘結式層疊芯製作裝置。更詳細地,涉及可通過使薄片狀部件連續層疊來輕鬆分離出1個芯產品的粘結式層疊芯製作裝置。
背景技術:
通常,疊加對條板進行衝孔工序及衝裁工序而得的薄片狀部件而成的層疊芯被用作馬達或發電機的定子或轉子,製作層疊芯的方法在本發明所屬技術領域中廣為熟知。
通過對供給到級進(progressive)模具裝置的條板依次進行用於形成槽部、齒部等的衝孔加工及衝裁加工來連續形成單張薄片狀部件,最終,按規定張數疊加外形被衝壓的單張薄片狀部件並使薄片狀部件固著,從而製作馬達層疊芯。
如在韓國公開專利公報第10-2005-0026882號等中公開的內容,單張薄片狀部件的固著方法有如下的所謂壓紋層疊方法,即,在各個單張薄片狀部件形成壓紋(embossing),當使薄片狀部件層疊時,以使壓紋被互相壓縮的方式使薄片狀部件互相結合。
在以如上所述的壓紋層疊方式製作的馬達芯中,因以強制扣入的方式使形成於母材的凹形突起部及凸形突起部的形狀緊固,因此起到如道路減速帶的作用並產生鐵損和磁通密度的損失。並且,存在空間係數降低、因共振現象而產生振動噪音的問題。
作為用於解決上述問題的粘結式層疊方法,韓國授權專利公報第10-0119014號中公開了馬達芯的層疊粘結裝置,上述馬達芯的層疊粘結裝置包括:模具,由下部模具支撐;衝頭,位於上述模具的上部,以進行上下運動的方式對供給到上述模具的上部表面的條板進行衝壓;衝頭支撐部,由上部模具支撐,在上述衝頭的外圍支撐衝頭;粘結劑供給單元,用於向上述條板的上側或側面供給粘結劑;層疊環,位於模具內部,藉助測壓型夾具支撐被衝壓的上述芯板,使上述芯板達到規定高度。
並且,在韓國授權專利公報第10-1164803號中公開了層疊芯的製作方法,在上述層疊芯的製作方法中,當衝壓模具運行時,通過與附著於模具的層疊分離模具相連接的管,向條板投入規定量的膠水,若達到所需的衝壓張數,則與衝壓模具相連接的層疊計數器使層疊分離模具從模具內瞬間上升,以便無法投入膠水,當重新開始進行衝壓時,使上升的層疊分離模具再次下降並再次投入膠水,通過反覆執行如上所述的過程,持續生產張數達到所需的衝壓張數的產品。
但是,在如上所述的以往的粘結式層疊方式中,在塗敷粘結劑的過程中採用單純從粘結劑供給單元向條板的上側或側面噴射粘結劑的方式或採用使粘結劑從與層疊分離模具相連接的軟管滴落的方式,因此塗敷粘結劑所消耗的時間長,不僅使層疊芯的生產率明顯下降,而且無法準確地在需要塗敷粘結劑的塗敷位置進行塗敷,不僅如此,還因粘結劑向周圍飛散而存在有可能對模具等產生不利影響的憂慮。
另一方面,以如下方式生產藉助上述現有技術製作完成的層疊芯,即,使薄片狀部件按規定張數壓紋層疊於上述模具裝置來生產張數被規定的層疊芯,向條板投入規定量的膠水,若達到所需的衝壓張數,則與衝壓裝置相連接的層疊計數器使層疊分離模具從模具內瞬間上升,以便無法投入膠水,從而製作張數被規定的層疊芯,前者中,在排出張數達到規定張數的層疊芯之後使模具裝置暫停,通過重新啟動模具裝置來接著生產下一個層疊芯,因此層疊芯生產率明顯下降,後者中,即使膠水未塗敷於計數的薄片狀部件也使薄片狀部件連續層疊於衝裁模具並向擠壓環排出,所層疊的塗敷膠水的薄片狀部件和未塗敷膠水的薄片狀部件有可能藉助膠水互相粘結,從而導致很難得到張數被規定的層疊芯,不僅如此,在迄今為止的粘結式層疊芯製作中,尚不存在使層疊芯相粘結並以規定張數連續排出的技術。
技術實現要素:
為了解決上述問題,本發明提出進一步得到改善的粘結式層疊芯製作裝置。
本發明的目的在於提供如下的馬達芯的粘結式層疊芯製作裝置及馬達的層疊芯,根據本發明的粘結式層疊芯製作裝置,通過採用加熱粘結方式來摒棄塗敷粘結劑的方式,可迅速完成更加堅固、穩定的粘結工序,根據本發明的馬達的層疊芯,不僅大幅度減少鐵損和磁通密度的損失,而且由於垂直度、平面度等的形狀公差良好、緊固強度優秀,因而使馬達的效率得到改善。
本發明的加熱粘結式層疊芯製作裝置包括模具裝置,上述模具裝置包括上部模具3和下部模具4,安裝於上部模具3的衝頭通過衝孔加工及衝裁加工來將在下部模具4的上部依次移送的蒸鍍有合成樹脂粘結膜100A′或塗敷有粘結用合成樹脂的條板100A製成單張薄片狀部件101,本發明的特徵在於,加熱粘結式層疊芯製作裝置還包括:擠壓環14,設置於下部模具4內,在按規定張數向擠壓環14推入被衝裁的單張上述薄片狀部件101並使多張薄片狀部件101緊貼之後排出被粘結的層疊芯100;以及層疊芯分離用突起形成裝置30,設置於上部模具3及下部模具4,工序上位於上述衝孔加工與上述衝裁加工之間。
優選地,在本發明中,加熱粘結式層疊芯製作裝置還包括:粘結加熱單元200,設置於上述擠壓環14的一側;以及磁場屏蔽單元300,設置於上述粘結加熱單元200的外側部,上述粘結加熱單元200採用高頻感應加熱方式,在擠壓環14外周面卷繞高頻感應線圈210,向上述高頻感應線圈210供給從控制裝置40內部的高頻振蕩器供給的高頻電流,藉助磁場使擠壓環14內部的層疊薄片狀部件101產生熱量,使得在各個薄片狀部件101的表面蒸鍍的合成樹脂粘結膜100A′或合成樹脂粘結塗層熔融,使薄片狀部件101之間互相粘結。
優選地,在本發明中,磁場屏蔽單元300為由鋁或銅形成的圓筒體,構成上述磁場屏蔽單元300的圓筒體310的內側面與構成粘結加熱單元200的高頻感應線圈210之間隔著間隔,上述圓筒體310的上部、下部與下部模具4相連接。
優選地,在本發明中,可在磁場屏蔽單元300的圓筒體310的內側部設置冷卻單元400,上述冷卻單元400形成冷卻水通道440,上述冷卻水通道(440)與冷卻蓄水罐410的供給管420及回收管430相連接。
優選地,在本發明中,層疊芯分離用突起形成裝置30包括:固定模具31,設置於上部模具3,具有凹入部31′;以及上下移動模具32,設置於下部模具4的與固定模具31相對應的位置,具有突出部32′。
優選地,在本發明中,層疊芯分離用突起形成裝置30包括:固定模具31,設置於上部模具3,具有突出部31A;以及上下移動模具32,設置於下部模具4的與固定模具31相對應的位置,具有凹入部32A。
優選地,在本發明中,藉助由層疊芯分離用突起形成裝置30形成的薄片狀部件101的分離用突起100-2使規定張數的層疊芯100之間相分離並向擠壓環14的外部排出。
優選地,在本發明中,粘結加熱單元200採用陶瓷加熱器加熱方式,在擠壓環14的外周面以相隔間距的方式設置正溫度係數(Positive Temperature Coefficien,PTC)加熱器220。
優選地,在本發明中,粘結加熱單元200採用陶瓷加熱器加熱方式,在擠壓環14的內周面設置正溫度係數加熱器220。
根據本發明,通過高頻感應加熱方式對層疊於擠壓環內部的多張薄片狀部件進行加熱,使塗敷於薄片狀部件表面的合成樹脂粘結塗層或蒸鍍的合成樹脂粘結膜熔融並使被熔融的上述合成樹脂膜或塗層粘結於上述薄片狀部件的背面部,使薄片狀部件與薄片狀部件之間的粘結穩定、堅固。
並且,在本發明中,迅速、穩定地進行層疊薄片狀部件的粘結工序
並且,本發明以使層疊芯和層疊芯輕鬆分離的方式生產,來大幅度節減馬達芯製作所需的製作時間及設備費用,並有效利用作業空間,不僅如此,進一步提高馬達的層疊芯生產率,具有降低成本的效果。
附圖說明
圖1為本發明實施例的條板的立體圖。
圖2為本發明實施例的對條板進行衝壓加工及衝裁加工而成的薄片狀部件的立體圖。
圖3為本發明實施例的層疊芯的立體圖。
圖4為本發明實施例的層疊芯製作裝置的剖視圖。
圖5為本發明實施例的粘結加熱單元及磁場屏蔽單元的部分剖視圖。
圖6為示出本發明實施例的磁場屏蔽單元的剖視圖。
圖7為示出本發明再一實施例的粘結加熱單元及磁場屏蔽單元的剖視圖。
圖8為本發明還有一實施例的粘結加熱單元及磁場屏蔽單元的截取剖視圖。
圖9為作為本發明實施例的圖4中的再一實施例的層疊芯製作裝置的剖視圖。
圖10為作為本發明實施例的圖4中的還有一實施例的層疊芯製作裝置的剖視圖。
圖11為作為本發明實施例的圖10中的實施例的層疊芯製作工序圖。
圖12為作為本發明實施例的圖11中的實施例的層疊芯製作工序圖。
具體實施方式
以下,參照附圖,詳細說明本發明的製作由1個以上的單位層疊體組成的層疊芯的層疊芯製作裝置的優選實施例。
圖1為本發明實施例的條板100A的立體圖,圖2為本發明實施例的對條板進行衝壓加工及衝裁加工而成的薄片狀部件的立體圖,圖3為本發明實施例的層疊芯的立體圖,圖4為本發明實施例的層疊芯製作裝置的剖視圖。
參照圖1,例如,本發明的條板100A為在由薄板形成的呈帶形狀的鋼板100-1表面蒸鍍有合成樹脂粘結膜100A'或塗敷有粘結用合成樹脂塗層的條板。本發明的一目的在於在沒有如上所述的通過用於粘結的塗敷裝置所進行的粘結作業的情況下使用上述條板100A生產層疊粘結芯。
參照圖2,示出了藉助後述的模具裝置1對上述條板100A進行衝壓加工及衝裁加工而成的薄片狀部件101,圖3示出按規定張數粘結上述薄片狀部件101而成的層疊芯100。
上述層疊芯100呈蒸鍍於薄片狀部件101表面的合成樹脂膜100A'被熔融並粘結於上述薄片狀部件101的背面金屬面的狀態。在圖1至圖3中,條板100A和薄片狀部件101在鋼板100-1的上部面形成粘結膜100A',實際上,粘結膜可同時蒸鍍於鋼板100-1的上部面及下部面,或者粘結膜僅蒸鍍於鋼板100-1的下部面。無論是哪一種情況,均可適用於本發明,在本說明書中,以圖1至圖3所示的形態進行說明,但是,本發明包括粘結膜100A'形成於鋼板100-1的上部面及下部面的情況或者粘結膜100A'形成於鋼板100-1的上部面和下部面中的一面的情況等所有情況。
通過對向圖4所示的模具裝置1供給的蒸鍍有合成樹脂粘結膜100A'或塗敷有粘結用合成樹脂的條板100A依次進行衝壓加工及衝裁加工,使上述薄片狀部件101具有槽部101'、齒部101"等,從而連續形成單張薄片狀部件101,最終,按規定張數疊加外形被衝壓的單張薄片狀部件101並使薄片狀部件101固著,從而製作馬達的層疊芯100。
尤其,本發明提供如下的加熱粘結式層疊芯裝置,即,本發明的加熱粘結式層疊芯裝置通過使用蒸鍍有合成樹脂粘結膜100A'或塗敷有粘結用合成樹脂的芯用條板100A來生產粘結的層疊芯,本發明的加熱粘結式層疊芯裝置並不採用迄今為止周知的通過粘結劑塗敷裝置所進行的粘結方式,而是採用在層疊模具內進行加熱的粘結方式。
具體地,參照圖4進行說明,本發明實施例的層疊芯製作裝置採用在依次移動的蒸鍍有合成樹脂粘結膜100A'或塗敷有粘結用合成樹脂的條板100A上連續進行作業的衝壓加工方式,上述層疊芯製作裝置可使用模具裝置1。
優選地,本發明中的模具裝置1為級進模具裝置,上述模具裝置1包括上部模具3和下部模具4。上部模具3配置於下部模具4的上側,並朝向下部模具4沿著升降方向v進行運動。通過上部模具3安裝於壓力機,並隨著啟動壓力機,上部模具3進行運動。在下部模具4的上部,條板100A沿著前進方向f移動。
上部模具3可包括:衝孔衝頭5、6、7、8及衝裁衝頭9,用於對條板100A進行衝壓;衝頭板17,用於安裝上述衝頭;以及衝頭支撐部19,用於在上部支撐上述衝頭板17。此時,圖4示出4個衝孔衝頭5、6、7、8,根據所要製作的芯的形態或大小等,可隨意變更上述衝孔衝頭的數量或形狀,而且基於搭載於控制裝置40內部的微處理器的控制程序依次對條板100A執行衝壓及衝裁。
並且,上部模具3可包括:衝頭墊板18,用於在衝頭支撐部19與衝頭板17之間支撐上述衝頭;以及脫料板20,引導衝頭向準確的位置移動,並用於去除進行衝壓時所扣入的條板100A。
下部模具4可包括:模具支撐部16,安裝於壓力機,用於把持下部模具4的整體重心;模具板13,安裝於上述模具支撐部16的上部;模具墊板15,位於模具支撐部16與模具板13之間,用於承受向模具板13施加的壓力。
並且,在下部模具4內安裝圓桶形狀的衝裁模具11,上述衝裁模具11在與衝裁衝頭9相對應的位置形成有中空。衝裁模具11使在被衝裁衝頭9衝壓後從條板100A分離的作為單張芯的薄片狀部件101向下部排出,所排出的薄片狀部件101在通過設置於上述衝裁模具11下部的擠壓環14的過程中被加熱並使薄片狀部件101之間互相粘結。
根據上述擠壓環14,在按規定張數向擠壓環14的底部推入被衝裁模具11衝壓並堆積在衝裁模具11內部的薄片狀部件101來使薄片狀部件101互相緊貼之後,藉助後述的粘結加熱單元200進行加熱處理,使薄片狀部件101與薄片狀部件101互相緊貼,經過粘結處理的層疊芯100藉助公知技術以自動或半自動的方式向外部排出,上述公知技術有擠壓環14的支撐力解除、設置於擠壓環14外周面的旋轉模具的旋轉及基於層疊芯重量傳感器檢測的重量排出等。
利用如上所述的本發明的模具裝置1的層疊芯製作工序包括衝孔(piercing)工序、在上述衝孔工序與衝裁工序之間執行的層疊芯分離用突起形成工序、衝裁(blanking)工序及層壓(laminating)工序。其中,優選地,層壓工序為加熱與層疊同時進行的工序。
在上述衝孔工序中,在條板100A上形成除芯外形之外的槽部101'、齒部101"、軸孔等的基本形狀。此時,條板100A在模具裝置1內依次移動1個間距(pitch),並藉助安裝於上部模具3並沿著上下方向移動的衝孔衝頭5、6、7、8進行衝孔加工。
若結束衝孔工序,則可執行後述的用於使規定張數的層疊芯100和規定張數的層疊芯100互相分離並排出的層疊芯分離用突起形成工序。
如圖9所示,本發明的設置於上部模具3和下部模具4的用於執行層疊芯分離用突起形成工序的工序上位於衝孔加工與衝裁加工之間的層疊芯分離用突起形成裝置30包括:固定模具31,設置於上部模具3,具有凹入部31′;以及上下移動模具32,設置於下部模具4的與固定模具31相對應的位置,具有突出部32′。具有如上所述的結構的層疊芯分離用突起形成裝置30在經過衝孔加工後移送的條板100A形成1個以上的分離用突起100-2,通過油壓氣缸等促動器40A使上述上下移動模具32進行升降,如圖11所示,可通過使分離用突起100-2在條板100A向上突起,來使層疊芯100和層疊芯100分離。另一方面,可通過上部模具3和下部模具4的運行來執行分離用突起100-2形成作業,無需運行促動器40A。
並且,圖10所示的本發明另一實施例的設置於上部模具3和下部模具4的工序上位於衝孔加工與衝裁加工之間的層疊芯分離用突起形成裝置30包括:固定模具31,設置於上部模具3,具有突出部31A;以及上下移動模具32,設置於下部模具4的與固定模具31相對應的位置,具有凹入部32A,如圖12所示,可在條板100A形成1個以上向下突出的分離用突起100-2,由此使位於具有分離用突起100-2的薄片狀部件正上方的薄片狀部件並不附著於具有分離用突起100-2的薄片狀部件而分離。當然,上述突起形成裝置30可通過改變衝裁衝頭的形狀來使用,而並非單獨的裝置,可在薄片狀部件101形成1個以上的向下突出的突起。
參照圖9和圖11具體說明藉助如上所述的層疊芯分離用突起形成裝置30執行的工序上位於衝孔加工與衝裁加工之間的層疊芯分離用突起形成工序和層疊芯分離過程。
在藉助搭載於後述的控制裝置40內部的驅動程序製作例如由15張薄片狀部件層疊而成的層疊芯100的情況下,在對第16張條板100A(圖11中的步驟(a))進行上述衝孔工序後,通過使具有凹入部31'的固定模具31和突出部32'的上下移動模具32相嚙合,來在所移送的上述條板100A向上突出形成1個以上的突起100-2(圖11的步驟(b)),在上述突起100-2突出形成的條板100A衝壓出芯的外形,從而執行製作出薄片狀部件101的衝裁工序(圖11中的步驟(c))。
通過反覆的衝裁工序使沒有衝壓出突起100-2的15張薄片狀部件101層疊來形成層疊芯,使通過上述步驟(b)形成的具有突起100-2的薄片狀部件層疊於由15張薄片狀部件101形成的層疊芯的上部(圖11中的步驟(d))。
接著,在具有突起100-2的薄片狀部件101的上部繼續層疊沒有突起100-2的薄片狀部件101(圖11中的步驟(e))。具有突起100-2的薄片狀部件101藉助其上部的薄片狀部件101按壓的力量來受到來自其上部及下部的薄片狀部件的壓力。藉助該壓力,朝向上方的突起100-2的形狀變形成類似朝向下方的褶皺狀。藉助這種變形,具有突起100-2的薄片狀部件不與其下部的薄片狀部件相接觸而分離(圖11的步驟(f))。
經過如上所述的步驟,可獲得從擠壓環14脫離的具有15張薄片狀部件的單獨的層疊芯,即最終產品。
即,若藉助粘結加熱單元200使層疊於擠壓環14內部的層疊芯100以後述的方式得到加熱,各個合成樹脂粘結膜100A'被熔融,並與各個薄片狀部件101的背面金屬面相粘結。在最初由15張薄片狀部件101形成的層疊芯100的最上方的薄片狀部件101的上部面,後續由其他15張薄片狀部件101層疊而成的層疊芯100的最下方的薄片狀部件101的分離用突起100-2變形並處於面接觸狀態,因此,即使薄片狀部件101藉助上述粘結加熱單元200產生熱量,蒸鍍於由15張薄片狀部件101形成的層疊芯100的最上方的薄片狀部件101上部面的合成樹脂粘結膜100A'面與向後續由其他15張薄片狀部件101層疊而成的層疊芯100的最下方的薄片狀部件101的下方突出的分離用突起100-2之間的接觸面積僅達到變形的上述分離用突起100-2的面積的程度,因此所形成的粘結部的粘結力非常脆弱。因此,粘結力脆弱的後續層疊的分離用突起100-2向下突出的薄片狀部件101與最初由15張薄片狀部件101形成的上述層疊芯100因上述粘結部的粘結力脆弱而互相分離,從而從擠壓環14排出由15張薄片狀部件101粘結而成的層疊芯100。
換句話講,由15張薄片狀部件101形成的層疊芯100的各個薄片狀部件101與合成樹脂粘結膜100A'的粘結面積非常寬,因而藉助粘結加熱單元200被加熱並穩定、均勻地形成粘結,在之後的由15張薄片狀部件101形成的層疊芯100的最下方的薄片狀部件101的背面突出的分離用突起100-2與之前由15張薄片狀部件101形成的層疊芯100的薄片狀部件101的上部合成樹脂粘結膜100A'之間的接觸面積非常窄,導致粘結力非常脆弱,因而每個由15張薄片狀部件101形成的層疊芯100之間的分離非常容易,當從擠壓環14排出層疊芯100時,可按每隔15張薄片狀部件101分離並排出層疊芯100。
參照圖10和圖12,具體說明本發明另一實施例的層疊芯分離過程。
在藉助搭載於後述的控制裝置40內部的驅動程序製作例如由15張薄片狀部件層疊而成的層疊芯100的情況下,在對第15張條板100A(圖12中的步驟(a))進行上述衝孔工序後,通過使具有突出部31A的固定模具31和凹入部32A的上下移動模具32相嚙合,來在所移送的上述條板100A向下突出形成1個以上的突起100-2(圖12的步驟(b)),在上述突起100-2突出形成的條板100A衝壓出芯的外形,從而執行製作出薄片狀部件101的衝裁工序(圖12中的步驟(c))。
通過反覆的衝裁工序使沒有衝壓出突起100-2的14張薄片狀部件101層疊來形成層疊芯,使通過上述步驟(b)形成的具有突起100-2的薄片狀部件層疊於由14張薄片狀部件101形成的層疊芯的上部(圖12中的步驟(d))。
接著,在具有突起100-2的薄片狀部件101的上部繼續層疊沒有突起100-2的薄片狀部件101(圖12中的步驟(e))。具有突起100-2的薄片狀部件101藉助其上部的薄片狀部件101按壓的力量來受到來自其上部及下部的薄片狀部件的壓力。藉助該壓力,朝向下方的突起100-2的形狀變形成類似朝向上方的褶皺狀。藉助這種變形,具有突起100-2的薄片狀部件不與其上部的薄片狀部件相接觸而分離(圖12的步驟(f))。
經過如上所述的步驟,可獲得從擠壓環14脫離的具有15張薄片狀部件的單獨的層疊芯,即最終產品。
其中,雖然未在圖4中示出,但是本發明可包括旋轉驅動裝置(未圖示),在被衝壓的薄片狀部件101在衝裁模具11內粘結之前,旋轉驅動裝置使未圖示的旋轉模具沿著圓周方向旋轉規定角度。由此,可消除因有可能在各個薄片狀部件101之間產生的細微的厚度偏差而引起的影響。
以下,參照圖5及圖6,詳細說明擠壓環14、粘結加熱單元200及磁場屏蔽單元300,上述擠壓環14設置於下部模具4內,在按規定張數向上述擠壓環14推入單張薄片狀部件101並使多張薄片狀部件101緊貼之後排出被粘結的層疊芯100,上述粘結加熱單元200包括上述擠壓環14,上述磁場屏蔽單元300設置於上述粘結加熱單元200的外側部。
上述粘結加熱單元200採用高頻感應加熱方式,在擠壓環14外周面卷繞高頻感應線圈210,向上述高頻感應線圈210供給從設置於控制裝置40內部的高頻振蕩器供給的高頻電流,藉助磁場使擠壓環14內部的層疊薄片狀部件101產生熱量,使得在各個薄片狀部件101的表面蒸鍍的合成樹脂粘結膜100A'或合成樹脂粘結塗層熔融,使薄片狀部件101和薄片狀部件101互相粘結。
如上所述,若藉助控制裝置40內部的微處理器中所搭載的控制程序層疊的薄片狀部件101堆積在擠壓環14內部,則通過檢測上述情況向高頻感應線圈210供給高頻電流,藉助設置於粘結加熱單元200內部的未圖示的溫度傳感器檢測內部溫度並通過顯示窗口進行確認,由此可確認加熱溫度,或者可通過控制加熱時間或控制所選擇的合成樹脂粘結膜100A'的熔融溫度,控制粘結加熱單元200的加熱時間及加熱溫度等。
上述粘結加熱單元200將擠壓環14作為芯(卷繞筒),將層疊於擠壓環14內部的薄片狀部件101作為金屬導體,若使高頻電流在卷繞於擠壓環14外周面的高頻感應線圈210流通,則在層疊的上述薄片狀部件101的表面附近產生渦流,薄片狀部件101藉助上述渦流損耗的熱量被加熱。
因此,層疊於擠壓環14內部的薄片狀部件101和薄片狀部件101通過薄片狀部件101迅速產生熱量使合成樹脂粘結膜100A′迅速熔融,使被熔融的合成樹脂粘結膜100A′和薄片狀部件101的背面互相粘結,層疊於薄片狀部件101整體表面的合成樹脂粘結膜100A′全部被均勻地熔融,從而使薄片狀部件101以更加堅固的狀態粘結。
而且,在上述粘結加熱單元200的外側部設置磁場屏蔽單元300,以便從採用高頻感應加熱方式的粘結加熱單元200產生的磁場不向外部洩漏,從而可防止設置於本發明的模具裝置1周圍的電子設備及裝置等因洩漏的電磁場而產生錯誤的現象。
優選地,上述磁場屏蔽單元300為由鋁或銅形成的圓筒體,構成上述磁場屏蔽單元300的圓筒體310的內側面與構成粘結加熱單元200的高頻感應線圈210之間隔著間隔,上述圓筒體310的上部、下部與下部模具4相連接,由此使洩漏的磁場通過圓筒體310向下部磨具4接地,從而防止磁場洩漏。
即,可通過由鋁或銅形成的圓筒體310使藉助粘結加熱單元200產生的磁場被抵消,為了進一步防止所產生的磁場向外部洩漏,維持圓筒體310與高頻感應線圈210之間的間隔,並通過圓筒體310使磁場向下部模具4旁通,從而防止磁場向磁場屏蔽單元300的外部洩漏。
而且,可在上述磁場屏蔽單元300的圓筒體310的內側部形成冷卻單元400,上述冷卻單元400形成與冷卻蓄水罐410的供給管420及回收管430相連接的冷卻水通道440。可在上述供給管420或回收管430設置啟動泵450。具有如上所述的結構的冷卻單元400防止因在粘結加熱單元200產生的高溫熱量向本發明的模具裝置1的外部傳遞而對周邊設備產生不利影響,在粘結加熱單元200的運行時間內或粘結加熱單元200運行之後的規定時間內,冷卻水可在冷卻水通道440進行循環。
當然,採用高頻感應加熱方式的本發明的粘結加熱單元200可通過在擠壓環14的內部產生熱量來可使高溫熱量無法直接向外部傳遞,但為了使穩定性達到更佳而設置冷卻單元400,根據需要,在無需設置冷卻單元400的情況下,可不設置冷卻單元400。
在具有如上所述的結構的本發明中,本發明的加熱粘結式層疊芯製作裝置包括模具裝置1,上述模具裝置1包括上部模具3和下部模具4,安裝於上部模具3的衝頭通過衝孔加工及衝裁加工來將在下部模具的上部依次移送的蒸鍍有合成樹脂粘結膜100A'或塗敷有粘結用合成樹脂的條板100A製成單張薄片狀部件101,本發明還包括:擠壓環14,設置於下部模具4內,在按規定張數向上述擠壓環14推入被衝裁的單張上述薄片狀部件101並使多張薄片狀部件101層疊之後排出層疊的層疊芯;粘結加熱單元200,包括上述擠壓環14;磁場屏蔽單元300,設置於上述粘結加熱單元200的外側部;以及層疊芯分離用突起形成裝置30,設置於上部模具3及下部模具4,工序上位於上述衝孔加工與上述衝裁加工之間。
在具有如上所述的結構的本發明中,利用蒸鍍有合成樹脂粘結膜100A'或塗敷有粘結用合成樹脂的條板100A,若通過對上述條板100A進行衝壓工序及衝裁工序而獲得的薄片狀部件101按規定張數位於擠壓環14的內部,則藉助採用高頻感應加熱方式的粘結加熱單元200使層疊於擠壓環14內部的薄片狀部件101迅速產生熱量,藉助產生熱量的薄片狀部件101來使在薄片狀部件101的表面蒸鍍的合成樹脂膜100A'或合成樹脂塗層熔融,使薄片狀部件101表面的被熔融的合成樹脂膜100A'和薄片狀部件101背面的金屬層堅固地粘結,從而製作由規定張數的薄片狀部件101粘結而成的層疊芯100,使得由規定張數的薄片狀部件101粘結而成的層疊芯100以薄片狀部件101的張數被固定的方式分離並被排出,加熱方式採用高頻感應加熱方式,因此,在沒有額外的粘結劑塗敷工序的情況下迅速完成粘結工序,使粘結更加堅固、穩定。尤其,本發明的層疊芯100並不通過如上所述的基於壓紋的層疊芯製作裝置製作,而是採用基於高頻感應線圈210的感應加熱方式,因此在各個薄片狀部件101所產生的熱量的溫度恆定,使得薄片狀部件101的膨脹係數達到恆定,因而不僅大幅度減少鐵損和磁通密度的損失,而且由於垂直度、平面度等的形狀公差良好、緊固強度優秀,因而本發明提供使馬達的效率得到改善的馬達的層疊芯100。
另一方面,在本發明中,雖然藉助採用高頻感應加熱方式的粘結加熱單元200使層疊薄片狀部件101粘結,但如圖7及圖8中所示的實施例,可通過藉助採用陶瓷加熱器方式的粘結加熱單元實施的加熱粘結方法來實施本發明。
即,上述粘結加熱單元200採用陶瓷加熱器加熱方式,在擠壓環14的外周面隔著間隔設置正溫度係數陶瓷加熱器220(正溫度係數熱敏電阻),或可通過使用陶瓷加熱器來代替擠壓環14,上述陶瓷可使用由碳化矽或氮化矽形成的陶瓷。當然,使上述擠壓環14具有大內徑,可將上述正溫度係數陶瓷加熱器220接合在上述擠壓環的14內部壁面周圍來構成粘結加熱單元200,在此情況下,衝裁模具11的內徑和正溫度係數陶瓷加熱器220的內徑可相同。
在具有如上所述的結構的粘結加熱單元200中,正溫度係數陶瓷加熱器220隨著供電而迅速產生熱量,由此對擠壓環14進行加熱,並使聚集在擠壓環14內部的多張層疊薄片狀部件101導熱來使蒸鍍於各個薄片狀部件101表面的合成樹脂粘結膜100A'或合成樹脂粘結塗層熔融,從而使薄片狀部件101和薄片狀部件101互相粘結。
在對設置於擠壓環14內的正溫度係數陶瓷加熱器220進行加熱的情況下,藉助正溫度係數陶瓷加熱器220產生的熱量,可使在位於正溫度係數陶瓷加熱器220內周面的薄片狀部件101蒸鍍的合成樹脂粘結膜100A'熔融。
在如上所述的本發明中,提供由正溫度係數陶瓷加熱器220構成的粘結加熱單元200的原因如下,即,在供電的同時,正溫度係數陶瓷加熱器220迅速產生熱量,由此縮短粘結時間,以正溫度係數使溫度一直維持規定溫度,從而不僅可穩定地維持粘結程度,而且減少耗電量、消除高溫火災危險。
如上所述,若藉助搭載於未圖示的微處理器的控制程序檢測到以規定張數層疊的薄片狀部件101聚集在擠壓環14內部,則供給電流,即向正溫度係數陶瓷加熱器220供電,藉助設置於粘結加熱單元200內部的未圖示的溫度傳感器檢測內部溫度並通過顯示窗口進行確認,由此可確認加熱溫度,或者可通過控制加熱時間或控制所選擇的合成樹脂粘結膜100A′的熔融溫度,控制粘結加熱單元200的加熱時間及加熱溫度等。
因此,層疊於擠壓環14內部的薄片狀部件101和薄片狀部件101通過被正溫度係數陶瓷加熱器220加熱,使合成樹脂粘結膜100A′迅速熔融,使得薄片狀部件101和薄片狀部件101互相粘結,層疊於薄片狀部件101整體表面的合成樹脂粘結膜100A′全部被均勻地熔融,從而使薄片狀部件101以更加堅固的狀態粘結。
而且,以不存在磁場屏蔽單元300的方式在上述粘結加熱單元200的外側部設置呈圓筒體的絕熱壁400′,由此可防止在粘結加熱單元200產生的高溫熱量向本發明的模具裝置1的外部傳遞而對周邊設備產生不利影響。
上述絕熱壁400′可形成與冷卻蓄水罐410的供給管420及回收管430相連接的冷卻水通道440。可在上述供給管420或回收管430設置啟動泵450。具有如上所述的結構的絕熱壁400′防止因在粘結加熱單元200產生的高溫熱量向本發明的模具裝置1的外部傳遞而對周邊設備產生不利影響,在粘結加熱單元200的運行時間內或粘結加熱單元200運行之後的規定時間內,冷卻水可在冷卻水通道440進行循環。其中,絕熱壁400′需迅速吸收裝置內部的熱量並進行冷卻,因此,優選地,採用熱導率高的鋁或黃銅、青銅類的金屬材質。
在對本發明的說明過程中,通過結合對擠壓環14進行加熱的裝置來說明了分離型突起形成工序,但分離型突起形成工序並不局限於這種形態的裝置。分離型突起形成工序及其裝置方面的結構還可適用於現有的粘結式芯製作裝置,這是理所當然的。
以上,詳細說明了本發明,但本發明的範圍並不局限於上述說明。上述說明僅用於例示本發明,本發明的範圍由發明要求保護範圍所定義,在發明要求保護範圍內的簡單的變形或變更均屬於本發明的權利範圍。