一種適用於小排量內燃機的機械諧振複合增壓系統的製作方法
2023-05-27 01:58:06 1
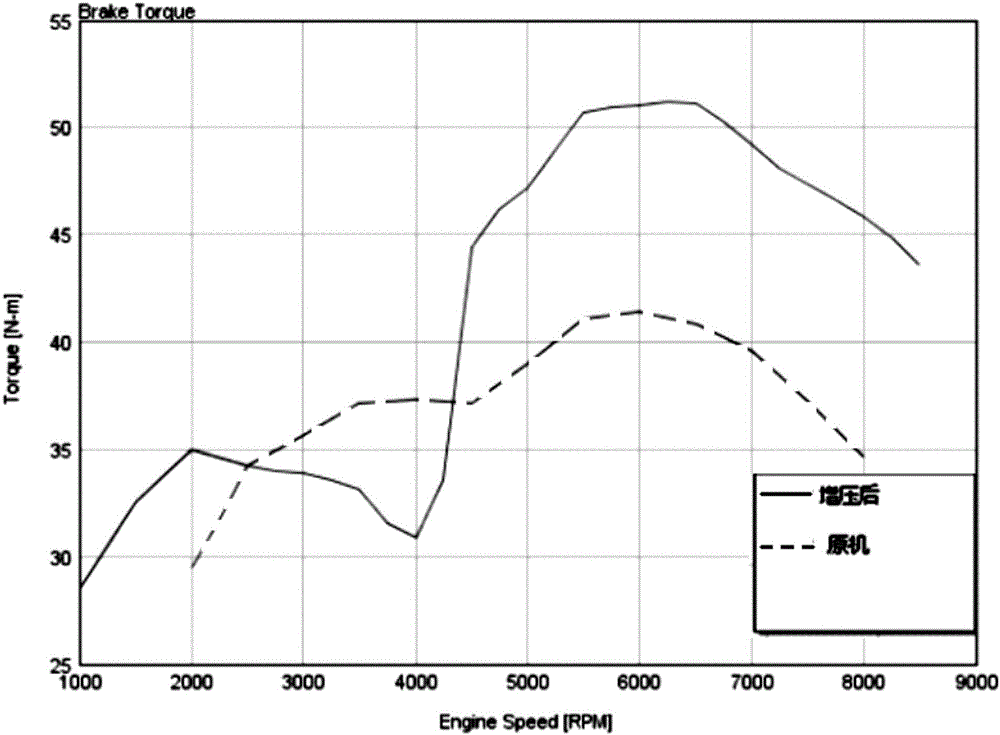
本實用新型涉及內燃機工程領域,尤其涉及一種適用於小排量內燃機的機械諧振複合增壓系統。
背景技術:
增壓是目前比較成熟的內燃機強化技術,增壓已經成為降低內燃機排放水平,提高內燃機升功率,改善內燃機燃油經濟性的重要手段。在高原環境,由於空氣稀薄,內燃機進氣質量減少,內燃機動力輸出與燃油經濟性大幅度降低,排氣汙染嚴重,增壓也是目前解決上述問題最為有效的方法。
內燃機進氣壓力的增加可以通過增壓器來實現。根據增壓器能量的來源,內燃機增壓技術可分為廢氣渦輪增壓、機械增壓、電動增壓以及諧振增壓等幾類。廢氣渦輪增壓是將具有一定能量的由發動機排出的廢氣引入渦輪機,利用廢氣能量推動渦輪機旋轉,由此驅動與渦輪同軸連接的增壓器實現增壓。廢氣渦輪增壓回收了具有一定壓力能的內燃機排氣的能量,目前該技術已經能實現高達十幾萬轉每分鐘的增壓器轉速,因而增壓效率較高。機械增壓是通過皮帶輪或齒輪方式從內燃機旋轉軸上取力,同樣可以實現高的增壓器轉速,效率也比較可觀。電動增壓通常是在柴油機轉速低於最大扭矩轉速的加速工況的初期進行工作,因此工作時間較短,其工作的目的是提高柴油機加速初期的空氣進氣量,解決柴油機低速加速不良及冒黑煙的問題。諧振增壓是諧振進氣系統利用系統中的不穩定流動,通過合適的諧振管長、諧振箱容積產生諧振作用,提高進氣門關閉前的進氣管壓力及充量係數,改善燃燒過程,降低油耗率並減少汙染。
對於單缸小排量內燃機,單純的機械增壓雖然具有動力輸出平順、響應速度快遞的優點,但是機械增壓消耗自身動力輸出,小排量動力冗餘低,對發動機動力消耗大,不利於有效提高單缸小排量內燃機經濟性。機械增壓技術還沒有在單缸小排量內燃機上推廣應用。
技術實現要素:
本實用新型的目的在於克服上述現有技術的缺點和不足,提供一種適用於小排量內燃機的機械諧振複合增壓系統。
本實用新型通過下述技術方案實現:
一種適用於小排量內燃機的機械諧振複合增壓系統,包括空濾器1、增壓器3、節氣門5、諧振腔6、氣缸9;
所述空濾器1通過進氣管2連接增壓器3;所述增壓器3通過擴散管4依次連接節氣門5、諧振腔6的入口;所述諧振腔6的出口通過諧振腔管11連接氣缸9。
所述諧振腔6上安裝有一級噴油嘴7,所述諧振腔管11的管尾安裝有二級噴油嘴8。
所述增壓器3採用無中冷器方式,由曲軸通過皮帶輪帶動,皮帶輪的轉動由汽車的水泵軸驅動。
所述擴散管4各管段的尺寸不同,即在增壓器3與節氣門5之間的管段內徑為20mm,在節氣門5與諧振腔6之間的管段內徑為40mm。
所述增壓器3與節氣門5之間的擴散管4上安裝有洩壓閥10。
所述諧振腔6的容積為3~4VL。
所述諧振腔管11的內徑為45mm,長度為230mm。
所述二級噴油嘴8通過噴油器支座安裝在諧振腔管11的管尾,噴油器支座的入口直徑為38mm~45mm。
本實用新型相對於現有技術,具有如下的優點及效果:
本實用新型所述空濾器1通過進氣管2連接增壓器3;所述增壓器3通過擴散管4依次連接節氣門5、諧振腔6的入口;所述諧振腔6的出口通過諧振腔管11連接氣缸9,並在諧振腔6上安裝了一級噴油嘴7,在諧振腔管11的管尾安裝了二級噴油嘴8。本實用新型在機械增壓的基礎上,加裝了諧振增壓裝置,並自行設計了兩級噴油嘴,使發動機在不同轉速下都能保持有力穩定的輸出。
本實用新型一級噴油嘴安裝在諧振腔上,二級噴油嘴連同支座安裝在諧振腔管的尾部。一級噴油器保證高功率下的燃油霧化,降低燃油溫度,二級噴油器保證發動機低速時的快速響應。同時,雙噴油嘴能互為備份,提高系統冗餘度,即使一個噴油嘴由於堵塞或線束脫落故障,另一個噴油嘴也能保證發動機的正常運行。
本實用新型整體結構緊湊,布局合理,複合增壓系統使小排量發動機發揮出比自然吸氣狀態下更好的動力性,無論最大扭矩還是最大功率,最低都有超過25%的增幅,總體而言,這套複合增壓系統極大彌補了小排量發動機動力不足的缺點,動力性能與原機對比均有顯著提高。
附圖說明
圖1為本實用新型適用於小排量內燃機的機械諧振複合增壓系統。
圖2為增壓前後扭矩比較曲線圖。
圖3為增壓前後功率比較曲線圖。
具體實施方式
如圖1至3所示。本實用新型公開了一種適用於小排量內燃機的機械諧振複合增壓系統,包括空濾器1、增壓器3、節氣門5、諧振腔6、氣缸9;所述空濾器1通過進氣管2連接增壓器3;所述增壓器3通過擴散管4依次連接節氣門5、諧振腔6的入口;所述諧振腔6的出口通過諧振腔管11連接氣缸9。
所述諧振腔6上安裝有一級噴油嘴7,所述諧振腔管11的管尾安裝有二級噴油嘴8。在內燃機正常轉速下,一級噴油嘴7足以提供所需燃料,二級噴油嘴8主要起輔助作用,加速加濃,而且距離氣缸9近,提高響應。
所述增壓器3採用無中冷器方式,由曲軸通過皮帶輪帶動,皮帶輪的轉動由汽車的水泵軸驅動。
所述擴散管4各管段的尺寸不同,即在增壓器3與節氣門5之間的管段內徑為20mm,在節氣門5與諧振腔6之間的管段內徑為40mm。
所述增壓器3與節氣門5之間的擴散管4上安裝有洩壓閥10。
所述諧振腔6的容積為3~4VL(VL為發動機排量)。
所述諧振腔管11的內徑為45mm,長度為230mm。
所述二級噴油嘴8通過噴油器支座安裝在諧振腔管11的管尾,噴油器支座的入口直徑為38mm~45mm。
利用機械諧振複合增壓系統對一臺自然吸氣的單缸汽油機進行改造。
下面以一款自然吸氣單缸汽油機為例,對本實用新型作進一步具體詳細描述。
一款自然吸氣單缸汽油機,缸徑為96mm,行程為62.1mm,排量為0.449L,標定功率為28kw(7500r/min)。
根據經驗,車用增壓發動機一般選擇最大轉速的50~60%的全負荷工況作為匹配工況點。對於本實用新型,發動機最大轉速為8500r/min,因此設置5000r/min為匹配工況點。由計算公式可知,該匹配點空氣品質流量為25.57g/s;增壓比為1.47。同時由選定的機械增壓器MAP可知,此時對應增壓器轉速為140000r/min。此時增壓器與發動機間傳動比為28。
綜合基礎發動機本體的考慮,決定在發動機水泵處使用皮帶傳動機構為機械增壓器提供動力。增壓器內部行星齒輪變速器的傳動比為12.52。當選擇基礎傳動比28時,皮帶傳動機構的傳動比為2.24。由於一般增壓器所能提供的最小被動皮帶輪直徑為60mm,故換算出水泵處主動皮帶輪直徑為134mm左右,這會十分容易讓皮帶傳動系統和發動機本體產生幹涉。最終選擇傳動比為27,小傳動比帶來的小主動皮帶輪直徑,能有效避免幹涉問題。
增壓器出口為20mm,諧振腔進口為40mm,因此連接的擴散管管徑設計變化為20-40-40,增壓器的高速氣流在此減速擴散增壓,將動能轉變為靜壓能,且擴散管由鋁管拉伸而成,能有效傳熱降低氣體溫度,提高發動機性能。彎曲半徑設計為45mm,理論上設計半徑越大,發動機性能越佳,但在實際表現中,我們發現當半徑接近50mm時,節氣門出現偏流導致性能下降,因此設計為45mm。
在擴散管上安裝洩壓閥,洩壓閥是一個保護裝置,當從節氣門全開到接近全關的減速工況時,可以起到保護引擎及增壓器的作用。
根據經驗,諧振腔設計體積為3~4VL時性能(VL為發動機排量),大容積能提高扭矩,但對於加速響應不利,到1.5升左右,聯合運行線已經貼近阻塞線,再提升容積沒意義。我們在排量為450cc發動機上,選用容積為1.5L的諧振腔。
一級噴油嘴安裝在諧振腔上,二級噴油嘴連同支座安裝在諧振腔管的尾部。一級噴油器保證高功率下的燃油霧化,降低燃油溫度,二級噴油器保證發動機低速時的快速響應。同時,雙噴油嘴能互為備份,提高系統冗餘度,即使一個噴油嘴由於堵塞或線束脫落故障,另一個噴油嘴也能保證發動機的正常運行。
諧振腔管管徑為45mm,長度為230mm,因為該長度的諧振腔管能在5500r/min至6500r/min形成一個平坦的扭矩平臺,並且滿足最大功率設計目標。
噴油器支座入口直徑為45mm,管徑越大,對扭矩的提升越明顯,但是會降低響應速度,所以綜合考慮下採用45mm,經過優化,出口直徑為38mm。
按照以上參數,設計機械諧振複合增壓系統與發動機進行匹配,經測試動力性能與原機對比均有顯著提高。如圖3所示,複合增壓系統對內燃機最大功率的增加情況。如圖2所示,安裝複合增壓系統的內燃機與未安裝增壓系統的內燃機器扭矩的增加情況。
試驗結果表明:發動機在8500r/min運行時,最大功率增加40%左右,在6500r/min運行時,最大扭矩增加25%左右,有1000-2000的扭矩平臺,表明本機械諧振複合增壓系統的有效性。
常見的小型渦輪介入轉速在1500r/min左右,但由於轉子半徑小,增壓比低,增壓效果不明顯,大型渦輪增壓比高,但要3000-4000r/min以上才能有效發揮增壓作用。對於小型發動機而言,即使使用設計給乘用車使用的小型渦輪,轉子半徑相對仍然偏大,等待轉子加速過程中,遲滯嚴重。而本實用新型專為0.6L以下的小型發動機設計。機械增壓響應速度快,全程介入,響應性好,能提高駕駛感受;而諧振增壓,關鍵在於管路半徑長度,諧振腔開口邊界的設計,雖然簡單,但能提高特定轉速範圍內的性能。本機械諧振複合增壓系統匹配於5000r/min,而最終最大扭矩與出現於6500r/min-8500r/min的範圍,已達到設計目的。
如上所述,便可較好地實現本實用新型。
本實用新型的實施方式並不受上述實施例的限制,其他任何未背離本實用新型的精神實質與原理下所作的改變、修飾、替代、組合、簡化,均應為等效的置換方式,都包含在本實用新型的保護範圍之內。