薄膜體聲波諧振器及其加工方法與流程
2023-05-27 13:21:56 5
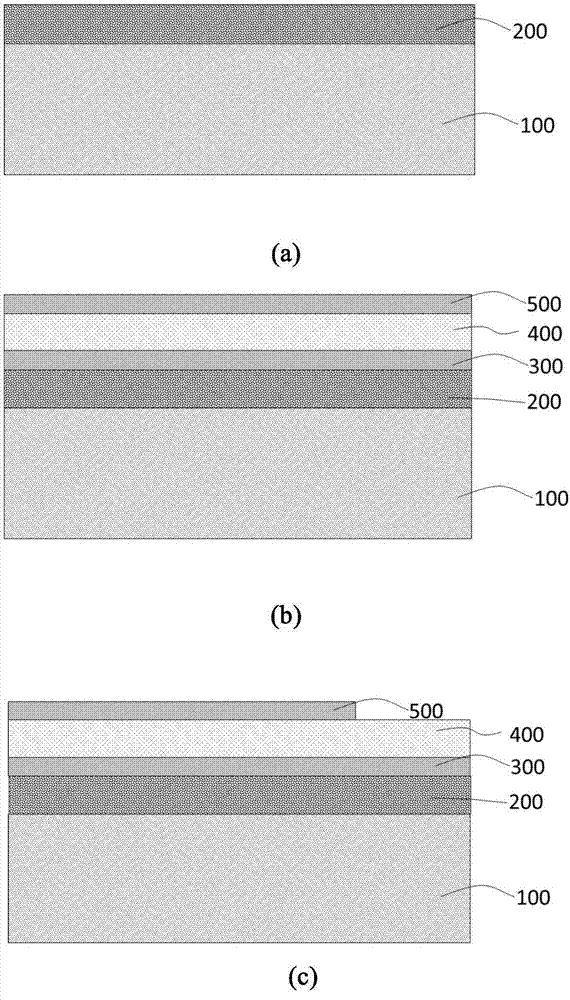
本發明涉及一種薄膜體聲波諧振器,特別是涉及一種採用鍵合工藝實現的薄膜體聲波諧振器及其加工方法。
背景技術:
隨著無線通訊應用的發展,人們對於數據傳輸速度的要求越來越高。在移動通信領域,第一代是模擬技術,第二代實現了數位化語音通信,第三代(3g)以多媒體通信為特徵,第四代(4g)將通信速率提高到1gbps、時延減小到10ms,第五代(5g)是4g之後的新一代移動通信技術,雖然5g的技術規範與標準還沒有完全明確,但與3g、4g相比,其網絡傳輸速率和網絡容量將大幅提升。如果說從1g到4g主要解決的是人與人之間的溝通,5g將解決人與人之外的人與物、物與物之間的溝通,即萬物互聯,實現「信息隨心至,萬物觸手及」的願景。
與數據率上升相對應的是頻譜資源的高利用率以及通訊協議的複雜化。由於頻譜有限,為了滿足數據率的需求,必須充分利用頻譜;同時為了滿足數據率的需求,從4g開始還使用了載波聚合技術,使得一臺設備可以同時利用不同的載波頻譜傳輸數據。另一方面,為了在有限的帶寬內支持足夠的數據傳輸率,通信協議變得越來越複雜,因此對射頻系統的各種性能也提出了嚴格的需求。
在射頻前端模塊中,射頻濾波器起著至關重要的作用。它可以將帶外幹擾和噪聲濾除以滿足射頻系統和通訊協議對於信噪比的需求。隨著通信協議越來越複雜,對頻帶內外的要求也越來越高,使得濾波器的設計越來越有挑戰。另外,隨著手機需要支持的頻帶數目不斷上升,每一款手機中需要用到的濾波器數量也在不斷上升。
目前射頻濾波器最主流的實現方式是聲表面波濾波器和基於薄膜體聲波諧振器技術的濾波器。聲表面波濾波器由於其自身的局限性,在1.5ghz以下使用比較合適。然而,目前的無線通訊協議已經早就使用大於2.5ghz的頻段,這時必須使用基於薄膜體聲波諧振器技術的濾波器。
薄膜體聲波諧振器的結構和製備方式已經有很多。在以往的結構和製備方式中,主要採用氮化鋁、氧化鋅、pzt等壓電薄膜作為壓電材料,而製備高質量的壓電薄膜材料一直是該領域的重點與難點。傳統製備壓電薄膜的方法是首先沉積底電極材料,然後對其刻蝕形成所需的底電極形狀,在此基礎上再沉積壓電層。由於壓電層的沉積質量(比如晶向,表面平整度等)很大一部分依賴於底電極的品質,尤其是刻蝕所造成的底電極邊緣殘留、毛刺等缺陷將嚴重影響高質量的壓電層生長,從而影響最終薄膜體聲波諧振器的性能。
技術實現要素:
本發明的目的是針對現有技術的缺陷,提出了一種採用鍵合方式實現的薄膜體聲波諧振器及其製備方法。通過將頂電極、壓電材料、底電極依次沉積為壓電薄膜堆疊結構,然後將底電極刻蝕後與帶有空腔的基片鍵合,最後再對頂電極金屬進行刻蝕形成所需的電極形狀。具體地,本發明的方案如下:
一種薄膜體聲波諧振器的製備方法,其特徵在於,包括以下步驟:
在襯底材料上製備壓電三明治堆疊結構,所述壓電三明治堆疊結構包括第一電極、壓電材料、第二電極,所述第一電極位於所述壓電材料上表面;
圖形化所述第一電極;
在所述壓電材料表面沉積第一金屬薄膜,並圖形化形成第一金屬材料層;
製備帶有空氣隙的基片;
在所述基片上沉積第二金屬薄膜,並圖形化形成第二金屬材料層;
將所述第一金屬材料層和所述第二金屬材料層進行鍵合,使得製備有壓電三明治堆疊結構的襯底材料與帶有空氣隙的基片形成整體;
去除所述襯底材料。
進一步地,所述去除所述襯底材料包括剝離步驟。
進一步地,包括在所述襯底材料上沉積用於剝離的薄膜材料層的步驟。
進一步地,鍵合後,所述第一電極與所述基片完全接觸。
進一步地,還包括圖形化所述壓電材料層、並引出所述第一電極的步驟。
進一步地,還包括在所述壓電材料層表面形成互連的步驟。
進一步地,所述薄膜材料層為易與所述襯底材料剝離的材料,包括二氧化矽、氮化矽、磷矽玻璃。
進一步地,所述剝離步驟包括溼法腐蝕。
本發明還提出一種薄膜體聲波諧振器,由本發明的製備方法所製備。
本發明還提出一種濾波器,包括薄膜體聲波諧振器。
本發明所提出的技術方案具有以下幾個優點:首先,通常壓電薄膜的生長依賴於其下方的電極材料和形狀,比如常用的c軸擇優的氮化鋁壓電薄膜一般在鉬電極、鎢電極和鉑金電極上生長比較好,比如在電極邊緣生長的壓電薄膜性能往往較差,因此薄膜體聲波諧振器和濾波器的性能往往與壓電薄膜下方的電極材料和形狀有很大關係。採用本發明的方案,由於能避免底電極刻蝕工藝造成的電極邊緣粗糙對壓電材料生長的影響,從而能更有效的獲得高質量的壓電薄膜;其次,由於採用預先刻蝕好的空腔鍵合工藝,能有效的避免傳統加工方法造成的犧牲層釋放不徹底和粘連問題,或者是背部刻蝕所造成的器件應力問題。
附圖說明
圖1為本發明的一種薄膜體聲波諧振器剖面結構圖;
圖2為本發明的一種薄膜體聲波諧振器的製備工藝流程圖。
具體實施方式
下面通過附圖和實施例,對本發明的技術方案做進一步的詳細描述。
實施例1
圖1為本發明實施例的一種薄膜體聲波諧振器的剖面結構圖,該薄膜體聲波諧振器包括基片700、基片700例如為矽片;基片700上包括空氣隙800;鍵合層600(900)、鍵合層例如為金等;在空氣隙800上方包括壓電三明治結構,其中500為壓電三明治結構的第一電極,材料為鉬等;400為壓電三明治結構的壓電層,材料為壓電單晶,比如壓電石英、鉭酸鋰、鈮酸鋰或四硼酸鋰等;300為壓電三明治結構的第二電極,材料為鉬等;互連金屬120將壓電三明治結構的第一電極引出到400表面形成焊點或互連點,材料為金或鎢等。
實施例2
圖2為本發明實施例的一種薄膜體聲波諧振器的製備工藝流程圖,該製備流程包括:
(a)準備單面或雙面拋光的矽片100,其中拋光面向上,進行標準清洗。
(b)沉積一層後續用於剝離的薄膜材料200,該材料可以是二氧化矽、氮化矽、磷矽酸玻璃等容易與矽襯底剝離的材料。
(c)在薄膜材料200上面依次沉積第二電極300,壓電材料400和第一電極500。其中,第一電極500和第二電極300包括鉬電極,壓電材料400包括氮化鋁(aln)、氧化鋅(zno)、鈮酸鋰(linbo3)、鉭酸鋰(litao3)之一或者組合。
(d)對第一電極500進行圖形化,形成如圖2(c)所示圖形。
(e)在壓電材料400表面沉積一定厚度的鉻金薄膜,經光刻圖形化後形成共熔鍵合的第一金屬材料層600,如圖2(d)所示。本實施例中採用連續沉積電極、壓電材料的方式形成壓電三明治堆疊結構,能避免底電極刻蝕工藝造成的電極邊緣粗糙對壓電材料生長的影響,從而能更有效的獲得高質量的壓電薄膜。
(f)準備單面或雙面拋光的矽片700,對其進行圖形化並刻蝕成空腔結構800,如圖2(e)所示;
(g)在前述矽片700表面沉積一定厚度的鉻金薄膜,經光刻圖形化後形成共熔鍵合的第二金屬材料層900,如圖2(f)所示。
(h)將前述沉積壓電和電極材料晶圓片100和矽片700進行共熔鍵合,使得前述共熔鍵合的第一金屬材料層600和第二金屬材料層900融為一體,形成600(900)。這樣鍵合後,沉積壓電和電極材料晶圓片100和矽片700形成一個整體。需要注意的是,鍵合後的薄膜體聲波諧振器第一電極500應保證與矽片700完全接觸,中間沒有間隙。如圖2(g)、圖2(h)所示。在整個晶片上,壓電三明治結構佔據的面積較小,而第一金屬層600和第二金屬層900佔據了較大面積。
(i)對前述形成一體結構中的晶圓片100進行剝離。本實施例中的剝離步驟通過溼法腐蝕薄膜材料200,從而將晶圓片100從鍵合形成的一體結構中剝離。如圖2(i)所示。
(j)將剝離後的基於矽片700的器件進行標準清洗,然後對第二電極300進行圖形化,形成如圖2(j)所示圖形。
(k)對壓電材料薄膜200進行圖形化,在預先設定好的位置開口露出第一電極500,形成如圖2(k)所示圖形。
(l)最後在前述圓片的表面沉積金屬,如金,經光刻圖形化後形成互連金屬120,其目的將薄膜體聲波諧振器的第一電極引出至壓電材料薄膜200的表面,形成焊點或互連點,方便薄膜體聲波諧振器的信號引出或與別的器件互連,如圖2(1)所示。
在本實施例中,製備壓電三明治結構與製備帶空腔的基片可以同時進行,並沒有嚴格的先後步驟要求。
本發明提供的製備方法中,壓電三明治結構逐層沉積之後再整體刻蝕,有效避免了沉積材料層的缺陷或者損害。其次,由於採用預先刻蝕好的空腔鍵合工藝,能有效的避免傳統加工方法造成的犧牲層釋放不徹底和粘連問題,或者是背部刻蝕所造成的器件應力問題。
最後所應說明的是,以上實施例僅用以說明本發明的技術方案而非限制,儘管參照較佳實施例對本發明進行了詳細說明,本領域的普通技術人員應當理解,可以對本發明的技術方案進行修改或者等同替換,而不脫離本發明技術方案的精神和範圍。