一種製備氧化石墨烯的方法及其裝置與流程
2023-06-09 20:43:17 1
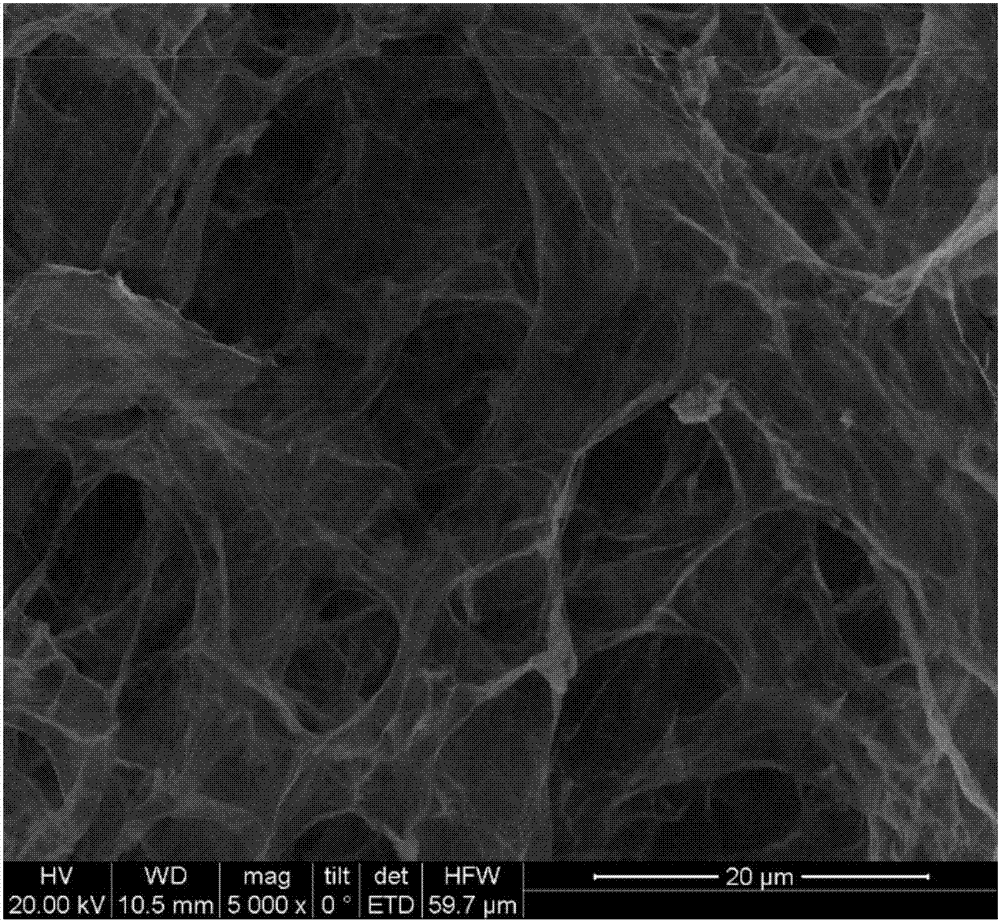
本發明涉及氧化石墨烯製備領域,特別是一種製備氧化石墨烯的方法及其裝置。
背景技術:
石墨烯是一種由單層碳原子堆積而成的二維蜂窩狀晶格結構新型碳材料。因其具有高比表面積(2600m2/g)、高熱導率(4800~5300W/(m·K))和高電子遷移率(15000cm2/(V·s))等性能,在複合材料、儲能材料和太陽能電池等領域有著廣泛的應用。
石墨烯的宏量製備是實現其諸多應用的前提。目前石墨烯的製備主要有以下方法:1)化學氣相沉積法;2)微機械剝離石墨法;3)金屬表面外延法;4)氧化還原法等。其中,氧化還原法是目前最為簡便的方法,成本較低,能夠實現大規模生產。因此,氧化石墨烯不僅是氧化還原法製備石墨烯的重要中間體,其自身所具有的特殊性質也使其在生物醫學、改性聚合物材料等方面有著廣泛的應用。
由於石墨天然的惰性,其氧化過程必須在較為苛刻的化學環境中完成,主要包括以下四種方法:1)Brodie法:該法採用發煙硝酸和氯酸鉀作為強酸和強氧化劑,需重複氧化步驟才能提高氧化程度,另外氯酸鉀的使用也有一定的危險性;2)Staudenmaier法:該法利用濃硫酸和發煙硝酸組成的混酸體系進行反應,以氯酸鉀為強氧化劑,氧化程度可由攪拌時間來控制,但該方法嚴重地破壞了氧化石墨烯的碳層,且氯酸鉀的使用也具有一定的危險性;3)Hummers法:該法採用濃硫酸和硝酸鈉體系,以高錳酸鉀為強氧化劑,產物氧化程度高、結構規整且易於在水中溶脹而層離得到單層氧化石墨烯,但硝酸鈉的使用會產生有毒的氮氧化物,汙染環境;4)改進的Hummers法:Kovtyukhova課題組將石墨在過硫酸鉀和五氧化二磷的濃硫酸溶液中進行預氧化,再用高錳酸鉀進行氧化,反應過程使用硝酸鈉,可避免氮氧化物的產生,產物氧化程度也較高,但產生的廢酸較多,操作也較為繁瑣。CN103382028A中公布了一種分別以濃硫酸和高錳酸鉀為強酸和強氧化劑製備氧化石墨烯的方法,但濃硫酸和高錳酸鉀混合後會產生高活性的七氧化二錳,在傳統的釜式反應器中進行該類反應需嚴格控制反應溫度,否則容易引起安全事故。另外,通過釜式反應製備氧化石墨烯還存在物料攪拌不均勻、高錳酸鉀利用率不高、需控溫防止衝料但過低的反應溫度並不利於反應快速進行等缺點。
技術實現要素:
本發明為了克服上述技術問題的不足,提供了一種製備氧化石墨烯的方法,可以完全解決上述技術問題。
解決上述技術問題的技術方案如下:
一種製備氧化石墨烯的方法,包括以下步驟:
(1)將石墨、酸和氧化劑按比例加入到混料釜內,在低溫下充分混合;
(2)將上述混合物輸入至第一管道反應器中,在一定溫度下進行反應1~4h;
(3)向步驟(2)所得的反應混合物中加入一定量的溶劑和還原劑混合均勻後,輸入至第二管道反應器中,在一定溫度下進行反應1~50h;
(4)將步驟(3)的反應混合物經後處理得到氧化石墨烯。
進一步地,步驟(1)中所述的石墨的粒徑為200微米以下,所述的酸為硫酸、硝酸、磷酸或乙酸的一種或多種,所述的氧化劑為高錳酸鉀、氯酸鉀、過硫酸鉀或過硼酸鈉的一種或多種,所述的氧化劑的粒徑為200微米以下,所述的石墨、酸和氧化劑的質量比為1:10~100:1~20,所述的低溫為-15~10℃。
進一步地,步驟(2)中所述的第一管道反應器的管道為盤管、連續S型管或者連續U型管,第一管道反應器的長徑比為50~80,所述的溫度為20~150℃。
進一步地,步驟(3)中所述的還原劑為雙氧水,所述的溶劑為水、乙二醇、N,N-二甲基甲醯胺(DMF)、N-甲基吡咯烷酮(NMP)、四氫呋喃(THF)中的一種或多種,所述的還原劑、溶劑與石墨的質量比為1~40:10~100:1,所述的第二管道反應器的管道為盤管、連續S型管或者連續U型管,第二管道反應器的長徑比為50~80,所述的溫度為20~200℃。
更進一步地,步驟(4)中所述的後處理為過濾、離心、洗滌、超聲、透析、凍幹的一種或多種組合。
同時,本發明還提供了一種實現上述製備方法的專用裝置,包括混料釜、第一管道反應器、第二管道反應器、混料器、冷凝器和後處理系統,所述的混料釜的輸出端和第一管道反應器的輸入端通過第一導管連接,第一導管上設置有第四計量泵,所述的第一管道反應器的輸出端與混料器的輸入端通過第二導管連接,所述的混料器的輸出端通過第三導管與第二管道反應器的輸入端連接,所述的第二管道反應器的輸出端與冷凝器的輸入端通過第四導管連接,冷凝器的輸出端與後處理系統連接。
進一步地,所述的混料釜、第一管道反應器和第二管道反應器均帶有控溫夾套。
進一步地,所述的混料釜的輸入端還與設置在混料釜的上遊端的第一固體加料器和第二固體加料器相連,所述的混料釜的上遊端還設置有第一貯存器,所述的第一貯存器與混料釜相連接的導管上依次設置有第一截止閥和第一計量泵。
進一步地,所述的混料器的輸入端還分別與第二貯存器和第三貯存器相連,所述的第二貯存器和第三貯存器與混料器相連接的導管上分別依次設置有第二截止閥和第二計量泵,第三截止閥和第三計量泵。
更進一步地,所述的後處理系統包括過濾系統、離心系統、洗滌系統、超聲系統、透析系統或者凍干係統中的任意一種或幾種。
本發明的有益效果在於:本發明通過管道控制物料的混合及反應方式,克服了傳統的釜式反應器一鍋煮的方式帶來的缺陷,生產過程安全、高效,產品質量較為穩定,保證了反應過程中物料的連續化,物料混合均勻,氧化劑高錳酸鉀的利用率較高,而且產物的氧化程度較高,有益於工業化生產。
附圖說明
下面結合附圖和具體實施方式對本發明作進一步詳細的說明。
圖1為本發明裝置的結構示意圖;
圖2為實施例1製備的氧化石墨烯的掃描電鏡SEM圖片;
圖3為實施例1製備的氧化石墨烯的元素分析EDAX圖譜;
圖中,1為第一固體加料器,2為第二固體加料器,3為第一貯存器,4為第二貯存器,5為第三貯存器,6為第一截止閥,7為第二截止閥,8為第三截止閥,9為第一計量泵,10為第二計量泵,11為第三計量泵,12為第四計量泵,13為混料器,14為混料釜,15為第一管道反應器,16為第二管道反應器,17為混料釜控溫夾套,18為第一管道反應器控溫夾套,19為第二管道反應器控溫夾套,20為冷凝器,21為第一導管,22為第二導管,23為第三導管,24為第四導管。
具體實施方式
實施例1:
一種製備氧化石墨烯的專用裝置(如圖1所示),包括混料釜14、第一管道反應器15、第二管道反應器16、混料器13、冷凝器20和後處理系統,所述的混料釜14的輸出端和第一管道反應器15的輸入端通過第一導管21連接,第一導管21上設置有第四計量泵12,所述的第一管道反應器15的輸出端與混料器13的輸入端通過第二導管22連接,所述的混料器13的輸出端通過第三導管23與第二管道反應器16的輸入端連接,所述的第二管道反應器16的輸出端與冷凝器20的輸入端通過第四導管24連接,冷凝器20的輸出端與後處理系統連接。
其中,第一管道反應器15的管長為30m,管道直徑為6mm;第二管道反應器16的管長為30m,管道直徑為8mm。第一管道反應器15和第二管道反應器16的管道均為盤管。
混料釜14的釜體外部設置有混料釜控溫夾套17、第一管道反應器15的外部設置有第一管道反應器控溫夾套18,第二管道反應器16設置有第二管道反應器控溫夾套19。
混料釜14的輸入端還與設置在混料釜14的上遊端的第一固體加料器1和第二固體加料器2相連,所述的混料釜14的上遊端還設置有第一貯存器3,所述的第一貯存器3與混料釜14相連接的導管上依次設置有第一截止閥6和第一計量泵9。
混料器13的輸入端還分別與第二貯存器4和第三貯存器5相連,所述的第二貯存器4和第三貯存器5與混料器13相連接的導管上分別依次設置有第二截止閥7和第二計量泵10,第三截止閥8和第三計量泵11。
使用該裝置製備氧化石墨烯時,將粒徑在200微米以下的石墨粉和高錳酸鉀分別置於第一固體加料器1中和第二固體加料器2中,將98%濃硫酸置於第一貯存器3中,利用混料釜控溫夾套17將混料釜14降溫至0℃,利用第一管道反應器控溫夾套18將第一管道反應器15升溫至80℃,利用第二管道反應器控溫夾套19將第二管道反應器16升溫至130℃,通過第一計量泵9將濃硫酸連續輸入至混料釜14內,開啟第一固體加料器1和第二固體加料器2,並控制加料速度,使得石墨粉、高錳酸鉀和濃硫酸的質量比為1:3:40,在混料釜14中混合均勻後,通過第四計量泵12輸送至第一管道反應器15中,在第一管道反應器15中進行氧化反應,反應1小時。
將水置於第二貯存器4中,將30%雙氧水置於第三貯存器5中,分別通過第二計量泵10和第三計量泵11控制,使得水、雙氧水和第一管道反應器15中的氧化反應液同時輸入至混料器13中,控制流速使得進入混料器13的水、雙氧水和氧化反應液的質量比為100:7:1,在混料器13中混合後輸入至第二管道反應器16中進行分散和還原,反應1小時。
最後,將分散還原液輸入至冷凝器20中冷卻後再經超聲處理得到亮黃色氧化石墨烯分散液。
圖2和圖3分別顯示了氧化石墨烯的掃描電鏡SEM圖片和元素分析EDAX圖譜,從SEM圖可以看出,製備的氧化石墨烯材料形貌比較蓬鬆,片層比較纖薄,另從EDAX圖譜可以看出,製備的氧化石墨烯含氧元素比較多。
實施例2
一種製備氧化石墨烯的專用裝置,包括混料釜14、第一管道反應器15、第二管道反應器16、混料器13、冷凝器20和後處理系統,所述的混料釜14的輸出端和第一管道反應器15的輸入端通過第一導管21連接,第一導管21上設置有第四計量泵12,所述的第一管道反應器15的輸出端與混料器13的輸入端通過第二導管22連接,所述的混料器13的輸出端通過第三導管23與第二管道反應器16的輸入端連接,所述的第二管道反應器16的輸出端與冷凝器20的輸入端通過第四導管24連接,冷凝器20的輸出端與後處理系統連接。
其中,第一管道反應器15的管長為30m,管道直徑為6mm;第二管道反應器16的管長為30m,管道直徑為10mm。第一管道反應器15和第二管道反應器16的管道均為連續S型管。
混料釜14的釜體外部設置有混料釜控溫夾套17、第一管道反應器15的外部設置有第一管道反應器控溫夾套18,第二管道反應器16設置有第二管道反應器控溫夾套19。
混料釜14的輸入端還與設置在混料釜14的上遊端的第一固體加料器1和第二固體加料器2相連,所述的混料釜14的上遊端還設置有第一貯存器3,所述的第一貯存器3與混料釜14相連接的導管上依次設置有第一截止閥6和第一計量泵9。
混料器13的輸入端還分別與第二貯存器4和第三貯存器5相連,所述的第二貯存器4和第三貯存器5與混料器13相連接的導管上分別依次設置有第二截止閥7和第二計量泵10,第三截止閥8和第三計量泵11。
使用該裝置製備氧化石墨烯時,將粒徑在200微米以下的石墨粉和氯酸鉀分別置於第一固體加料器1中和第二固體加料器2中,將濃硝酸置於第一貯存器3中,利用混料釜控溫夾套17將混料釜14降溫至-15℃,利用第一管道反應器控溫夾套18將第一管道反應器15升溫至20℃,利用第二管道反應器控溫夾套19將第二管道反應器16升溫至20℃,通過第一計量泵9將濃硝酸連續輸入至混料釜14內,開啟第一固體加料器1和第二固體加料器2,並控制加料速度,使得石墨粉、氯酸鉀和濃硝酸的質量比為1:8:30,在混料釜14中混合均勻後,通過第四計量泵12輸送至第一管道反應器15中,在第一管道反應器15中進行氧化反應,反應4小時。
將乙二醇置於第二貯存器4中,將30%雙氧水置於第三貯存器5中,分別通過第二計量泵10和第三計量泵11控制,使得乙二醇、雙氧水和第一管道反應器15中的氧化反應液同時輸入至混料器13中,控制流速使得進入混料器13的乙二醇、雙氧水和氧化反應液的質量比為10:2:1,在混料器13中混合後輸入至第二管道反應器16中進行分散和還原,反應50小時。
最後,將分散還原液輸入至冷凝器20中冷卻後再過濾,濾餅用3%鹽酸洗滌三次,再分散於去離子水中,超聲處理,離心分離,取下層深色液體,凍幹,得到氧化石墨烯產物。
實施例3
一種製備氧化石墨烯的專用裝置,包括混料釜14、第一管道反應器15、第二管道反應器16、混料器13、冷凝器20和後處理系統,所述的混料釜14的輸出端和第一管道反應器15的輸入端通過第一導管21連接,第一導管21上設置有第四計量泵12,所述的第一管道反應器15的輸出端與混料器13的輸入端通過第二導管22連接,所述的混料器13的輸出端通過第三導管23與第二管道反應器16的輸入端連接,所述的第二管道反應器16的輸出端與冷凝器20的輸入端通過第四導管24連接,冷凝器20的輸出端與後處理系統連接。
其中,第一管道反應器15的管長為20m,管道直徑為6mm;第二管道反應器16的管長為20m,管道直徑為8mm。第一管道反應器15和第二管道反應器16的管道均為連續U型管。
混料釜14的釜體外部設置有混料釜控溫夾套17、第一管道反應器15的外部設置有第一管道反應器控溫夾套18,第二管道反應器16設置有第二管道反應器控溫夾套19。
混料釜14的輸入端還與設置在混料釜14的上遊端的第一固體加料器1和第二固體加料器2相連,所述的混料釜14的上遊端還設置有第一貯存器3,所述的第一貯存器3與混料釜14相連接的導管上依次設置有第一截止閥6和第一計量泵9。
混料器13的輸入端還分別與第二貯存器4和第三貯存器5相連,所述的第二貯存器4和第三貯存器5與混料器13相連接的導管上分別依次設置有第二截止閥7和第二計量泵10,第三截止閥8和第三計量泵11。
使用該裝置製備氧化石墨烯時,將粒徑在200微米以下的石墨粉、過硫酸鉀和過硼酸鈉按照質量比為1:1的混合物分別置於第一固體加料器1中和第二固體加料器2中,將乙酸置於第一貯存器3中,利用混料釜控溫夾套17將混料釜14降溫至10℃,利用第一管道反應器控溫夾套18將第一管道反應器15升溫至150℃,利用第二管道反應器控溫夾套19將第二管道反應器16升溫至200℃,通過第一計量泵9將乙酸連續輸入至混料釜14內,開啟第一固體加料器1和第二固體加料器2,並控制加料速度,使得石墨粉、氧化劑和乙酸的質量比為1:20:100,在混料釜14中混合均勻後,通過第四計量泵12輸送至第一管道反應器15中,在第一管道反應器15中進行氧化反應,反應2小時。
將DMF置於第二貯存器4中,將30%雙氧水置於第三貯存器5中,分別通過第二計量泵10和第三計量泵11控制,使得DMF、雙氧水和第一管道反應器15中的氧化反應液同時輸入至混料器13中,控制流速使得進入混料器13的DMF、雙氧水和氧化反應液的質量比為100:40:1,在混料器13中混合後輸入至第二管道反應器16中進行分散和還原,反應25小時。
最後,將分散還原液輸入至冷凝器20中冷卻後再經超聲處理得到亮黃色氧化石墨烯分散液。
實施例4
一種製備氧化石墨烯的專用裝置,包括混料釜14、第一管道反應器15、第二管道反應器16、混料器13、冷凝器20和後處理系統,所述的混料釜14的輸出端和第一管道反應器15的輸入端通過第一導管21連接,第一導管21上設置有第四計量泵12,所述的第一管道反應器15的輸出端與混料器13的輸入端通過第二導管22連接,所述的混料器13的輸出端通過第三導管23與第二管道反應器16的輸入端連接,所述的第二管道反應器16的輸出端與冷凝器20的輸入端通過第四導管24連接,冷凝器20的輸出端與後處理系統連接。
其中,第一管道反應器15的管長為30m,管道直徑為6mm;第二管道反應器16的管長為30m,管道直徑為8mm。第一管道反應器15的管道為盤管,第二管道反應器16的管道為連續U型管。
混料釜14的釜體外部設置有混料釜控溫夾套17、第一管道反應器15的外部設置有第一管道反應器控溫夾套18,第二管道反應器16設置有第二管道反應器控溫夾套19。
混料釜14的輸入端還與設置在混料釜14的上遊端的第一固體加料器1和第二固體加料器2相連,所述的混料釜14的上遊端還設置有第一貯存器3,所述的第一貯存器3與混料釜14相連接的導管上依次設置有第一截止閥6和第一計量泵9。
混料器13的輸入端還分別與第二貯存器4和第三貯存器5相連,所述的第二貯存器4和第三貯存器5與混料器13相連接的導管上分別依次設置有第二截止閥7和第二計量泵10,第三截止閥8和第三計量泵11。
使用該裝置製備氧化石墨烯時,將粒徑在200微米以下的石墨粉和過硼酸鈉分別置於第一固體加料器1中和第二固體加料器2中,將磷酸置於第一貯存器3中,利用混料釜控溫夾套17將混料釜14降溫至-10℃,利用第一管道反應器控溫夾套18將第一管道反應器15升溫至30℃,利用第二管道反應器控溫夾套19將第二管道反應器16升溫至80℃,通過第一計量泵9將磷酸連續輸入至混料釜14內,開啟第一固體加料器1和第二固體加料器2,並控制加料速度,使得石墨粉、過硼酸鈉和磷酸的質量比為1:18:50,在混料釜14中混合均勻後,通過第四計量泵12輸送至第一管道反應器15中,在第一管道反應器15中進行氧化反應,反應3小時。
將NMP置於第二貯存器4中,將30%雙氧水置於第三貯存器5中,分別通過第二計量泵10和第三計量泵11控制,使得NMP、雙氧水和第一管道反應器15中的氧化反應液同時輸入至混料器13中,控制流速使得進入混料器13的NMP、雙氧水和氧化反應液的質量比為50:10:1,在混料器13中混合後輸入至第二管道反應器16中進行分散和還原,反應15小時。
最後,將分散還原液輸入至冷凝器20中冷卻後再經透析處理得到氧化石墨烯產物。
實施例5
一種製備氧化石墨烯的專用裝置,包括混料釜14、第一管道反應器15、第二管道反應器16、混料器13、冷凝器20和後處理系統,所述的混料釜14的輸出端和第一管道反應器15的輸入端通過第一導管21連接,第一導管21上設置有第四計量泵12,所述的第一管道反應器15的輸出端與混料器13的輸入端通過第二導管22連接,所述的混料器13的輸出端通過第三導管23與第二管道反應器16的輸入端連接,所述的第二管道反應器16的輸出端與冷凝器20的輸入端通過第四導管24連接,冷凝器20的輸出端與後處理系統連接。
其中,第一管道反應器15的管長為30m,管道直徑為6mm;第二管道反應器16的管長為30m,管道直徑為8mm。第一管道反應器15的管道為連續S型管,第二管道反應器16的管道為連續U型管。
混料釜14的釜體外部設置有混料釜控溫夾套17、第一管道反應器15的外部設置有第一管道反應器控溫夾套18,第二管道反應器16設置有第二管道反應器控溫夾套19。
混料釜14的輸入端還與設置在混料釜14的上遊端的第一固體加料器1和第二固體加料器2相連,所述的混料釜14的上遊端還設置有第一貯存器3,所述的第一貯存器3與混料釜14相連接的導管上依次設置有第一截止閥6和第一計量泵9。
混料器13的輸入端還分別與第二貯存器4和第三貯存器5相連,所述的第二貯存器4和第三貯存器5與混料器13相連接的導管上分別依次設置有第二截止閥7和第二計量泵10,第三截止閥8和第三計量泵11。
使用該裝置製備氧化石墨烯時,將粒徑在200微米以下的石墨粉和高錳酸鉀分別置於第一固體加料器1中和第二固體加料器2中,將98%濃硫酸和乙酸(質量比為5:1)的混合物置於第一貯存器3中,利用混料釜控溫夾套17將混料釜14降溫至-5℃,利用第一管道反應器控溫夾套18將第一管道反應器15升溫至140℃,利用第二管道反應器控溫夾套19將第二管道反應器16升溫至190℃,通過第一計量泵9將酸連續輸入至混料釜14內,開啟第一固體加料器1和第二固體加料器2,並控制加料速度,使得石墨粉、高錳酸鉀和酸的質量比為1:3:100,在混料釜14中混合均勻後,通過第四計量泵12輸送至第一管道反應器15中,在第一管道反應器15中進行氧化反應,反應2.5小時。
將THF置於第二貯存器4中,將30%雙氧水置於第三貯存器5中,分別通過第二計量泵10和第三計量泵11控制,使得THF、雙氧水和第一管道反應器15中的氧化反應液同時輸入至混料器13中,控制流速使得進入混料器13的THF、雙氧水和氧化反應液的質量比為80:5:1,在混料器13中混合後輸入至第二管道反應器16中進行分散和還原,反應30小時。
最後,將分散還原液輸入至冷凝器20中冷卻後再經超聲處理得到亮黃色氧化石墨烯分散液。
以上所述,僅是本發明的較佳實施例,並非對本發明做任何形式上的限制,凡是依據本發明的技術實質上對以上實施例所作的任何簡單修改、等同變化,均落入本發明的保護範圍之內。