一種氣缸停缸時停止活塞運動的機構的製作方法
2023-05-29 10:27:46 3
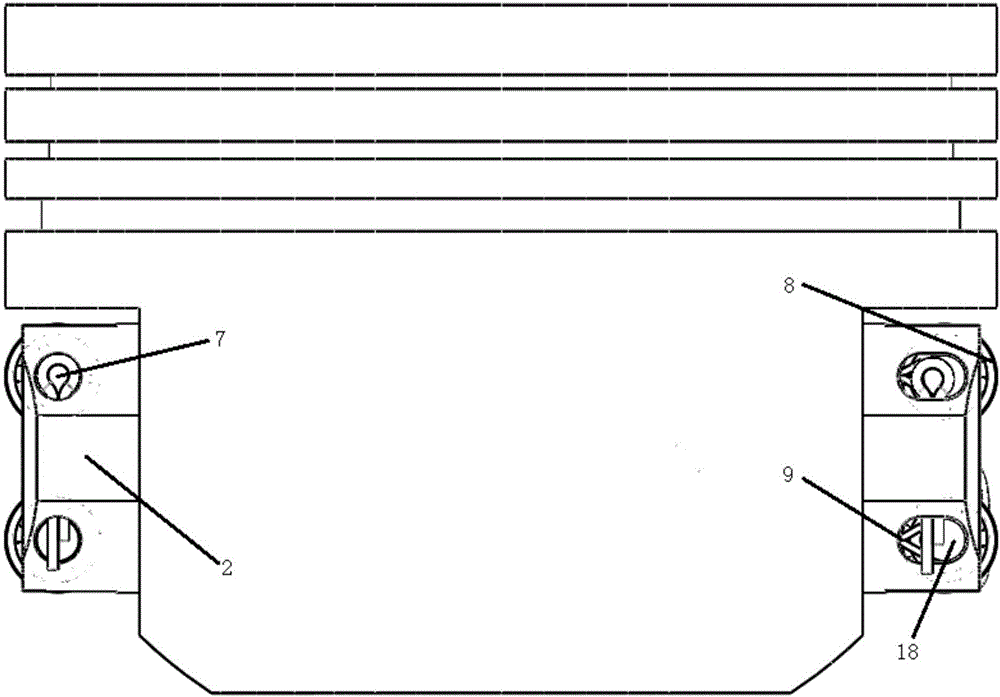
本發明涉及往復活塞式發動機,尤其涉及一種氣缸停缸時停止活塞運動的機構。
背景技術:
往復活塞式發動機的停缸技術通常採用停止氣門運動的方式來實現,氣門停止運動後活塞仍在往復運動,產生額外的摩擦損失。通常,在發動機摩擦損失中,活塞-連杆-曲軸機構所產生的摩擦佔有最大份額。
對於大排量發動機,例如V6、V8、V12,應用進排氣門停止機構可將發動機的工作氣缸數減半或者其他數量。例如,奔馳S500V8發動機在發動機轉速1000-3500rpm、自動變速器檔位在3、4、5檔時關閉4個氣缸,對應的車速為40-160km/h。本田V-6、3.5L發動機可在3缸、4缸、6缸中切換,3缸應用於低負荷工況,如巡航,4缸用於緩加速工況和3缸不能勝任的高轉速工況,6缸應用於更高負荷的工況。對於小排量發動機,大眾首先在四缸機上應用停缸技術,其車型Polo Blue GT上的1.4TSI發動機的停缸工況可覆蓋1400-4000rpm、25-100Nm區間,模式切換的響應時間在180°凸輪軸轉角之內。大眾公司宣稱在歐洲測試循環試驗中,在中低負荷下關閉第2、3缸進排氣門的停缸策略將降低油耗0.4L/60miles。
現有一種活塞止動機構在曲軸連杆系中應用四桿機構實現停止活塞運動的功能,如圖8和圖9所示,其中的四桿機構中有一桿可調整,用於實現活塞的運動和停止。
對於已在量產車中應用的氣門停止機構,停缸時活塞仍在往復運動,產生摩擦能量損失;對於可調四桿機構,其機構相對複雜,對原發動機的改動較大。因此,本領域的技術人員致力於開發一種氣缸停缸時停止活塞運動的機構,應用在帶有氣門停止機構的發動機上,當氣門停止運動後,活塞也停止運動,避免摩擦損失,與此同時,只對活塞和活塞銷稍作修改,即可實現停止活塞運動的功能,避免了四桿機構的複雜性。
技術實現要素:
有鑑於現有技術的上述缺陷,本發明所要解決的技術問題是如何在帶有氣門停止機構的發動機上,應用簡單設計,當氣門停止運動後,活塞也停止運動,避免摩擦損失。
為實現上述目的,本發明提供了一種氣缸停缸時停止活塞運動的機構,包括活塞銷(2),所述活塞銷(2)的兩端各裝有兩個與缸套表面接觸的軸承;所述活塞銷(2)的下部開放且上方有一螺紋孔,所述螺紋孔上裝有帶楔形槽的螺柱(10);活塞銷(2)包括電機(14)驅動的螺旋傳動機構,所述螺旋傳動機構包括兩個由螺旋傳動機構驅動的圓柱形滑塊(12),一滑塊內有壓縮式彈簧(11)和帶內螺紋的方形滑塊(13),另一滑塊內裝有驅動電機(14);所述螺旋傳動機構還包括為可伸縮電線(5)和電線(17),所述可伸縮電線(5)和所述電線(17)兩線相連;所述螺旋傳動機構被配置為檢測曲軸位置的控制器為電機(14)提供動作信號,控制電機改變兩個圓柱形滑塊(12)的位置。
進一步地,所述方形滑塊(13)與驅動電機(14)輸出軸螺紋套(16)配合形成螺旋傳動,驅動兩個圓柱形滑塊(12)相互遠離或接近。
進一步地,所述驅動電機(14)由可伸縮電線(5)提供驅動信號。
進一步地,所述兩個圓柱形滑塊(12)分別由兩個圓柱端緊定螺釘(15)限制其繞自身軸線的旋轉運動,並被限制在一定距離內的軸向移動。
進一步地,所述活塞銷(2)被配置為分離時的上止點為排氣上止點,結合時為壓縮上止點或排氣上止點。
進一步地,所述上止點判斷和曲軸位置判斷由原發動機控制系統提供。
進一步地,所述活塞銷(2)的分離和結合依靠電機(14)在合適的曲軸轉角位置時驅動兩圓柱形滑塊(12)的移動實現。
進一步地,所述兩個圓柱形滑塊(12)開始接近時,氣缸(4)處於膨脹或排氣衝程,所述兩個圓柱形滑塊(12)開始遠離時,氣缸(4)處於進氣、壓縮、膨脹或者排氣中的任一衝程中。
進一步地,所述軸承為滾動軸承(8)或直線軸承。
進一步地,在活塞銷(2)兩端各安裝兩個滾動軸承(8),其中一側的滾動軸承支撐軸(18)配有弓形彈簧(9)。
本發明所述的一種可以在往復活塞式發動機運轉過程中實現活塞(1)和活塞銷(2)分離和結合的機構,它包括:兩端各有至少2個滾動軸承的活塞銷(2);活塞銷孔下部開放、上方有一螺紋孔(活塞頂為向上方向),孔上裝有帶楔形槽的螺柱(10);一套電機(14)驅動的螺旋傳動機構,包括2個由螺旋傳動機構驅動的圓柱形滑塊(12),一滑塊內有壓縮式彈簧(11)和帶內螺紋的方形滑塊(13),另一滑塊內裝有電機(14),該滑塊與電機固聯;為電機提供控制信號的可伸縮電線(5)和電線(17),兩線相連;檢測曲軸位置的控制器為電機(14)提供動作信號,控制電機改變兩個圓柱形滑塊(12)的位置,決定滑塊是否進入螺柱(10)上與滑塊形狀對應的楔形槽,從而決定活塞(1)與活塞銷(2)在上止點時分離或結合。
活塞銷(1)兩端各裝有2個與缸套表面接觸的滾動軸承(8),保證活塞銷(2)保持正常運動軌跡,並且不發生繞自身軸線的旋轉運動。在合適的曲軸轉角時,活塞銷(2)內的電機(14)(輸出軸裝有螺紋套(16))和方形滑塊(13)(中部有內螺紋孔)驅動的螺旋傳動機構推拉圓柱形滑塊(2)。本發明中包括2個帶楔形端的圓柱形滑塊(2),相應地,安裝活塞上的螺柱(10)上有楔形凹槽可與之配合,滑塊退出凹槽或進入凹槽分別對應活塞和活塞銷分離或結合。
活塞1和活塞銷2分離時的上止點為排氣上止點,以確保活塞在活塞環與缸套間摩擦力的作用下更易保持在上止點。結合時為壓縮上止點或排氣上止點。上止點判斷和曲軸位置判斷由原發動機控制系統提供。
為實現活塞1和活塞銷2在排氣上止點處分離,在該上止點前的某一曲軸轉角位置(540°曲軸轉角之內,即壓縮、膨脹、排氣衝程的任一位置),圓柱形滑塊12在電機14驅動下開始被預先收回,在排氣上止點時實現分離;為實現結合,當活塞銷不處於上止點時,圓柱形滑塊被推出,當活塞銷到達上止點時,與圓柱形滑塊相連的壓縮式彈簧11完成一次快速的壓縮和恢復過程,將兩圓柱形滑塊12及時彈入螺柱10上的楔形槽,結合完成。結合過程中活塞1頂部與汽缸蓋接觸,限制活塞1在結合過程中移動。由於結合過程在上止點,運動的活塞銷2在上止點處速度為零,不會衝擊靜止的活塞1。
兩個圓柱形滑塊12分別由兩個圓柱端緊定螺釘15限制其繞自身軸線的旋轉運動,並被限制在一定距離內的軸向移動。緊定螺釘前端面未與圓柱形滑塊10接觸,它的緊固是由於活塞銷2上與其配合的螺紋孔螺紋較淺實現的。
本發明中,考慮到氣缸4的響應特性很可能無法滿足在活塞銷2經過上止點的那一極短時間內即可將圓柱形滑塊12推出完成活塞1和活塞銷2的結合動作,圓柱形滑塊12內的壓縮式彈簧11是必需的,這樣在活塞銷2達到上止點和活塞1結合之前,電機14就將圓柱形滑塊12提前推出等待即將到來的活塞銷2,等活塞銷2達到上止點時,在壓縮式彈簧11的作用下圓柱形滑塊12被快速推入楔形槽完成結合。
驅動電機14工作的電線5在本發明中被設計為螺旋可伸縮的形式,以滿足活塞高頻高速往復運動的要求。可伸縮電線5一端固定於活塞銷,一端固定於曲軸箱機體。可伸縮電線5與電機控制線17連接。
兩個圓柱形滑塊12的相互遠離和接近動作依靠螺旋傳動方式實現,但利用發動機潤滑油通過液壓傳動也可能實現,因此液壓傳動是替代方案。使用類似電磁閥的機構驅動兩圓柱形滑塊12接近或原理也是替代方案。
活塞銷2兩端的滾動軸承8與氣缸4缸壁接觸,形成阻力小的滾動摩擦,但直線軸承中的結構也可能應用到活塞銷2與氣缸4缸壁的接觸處,形成滾動摩擦,因此在活塞銷兩端應用直線軸承是替代方案。
考慮到可伸縮電線可能會在活塞銷高頻往復運動的情況下發生失效,某些無線電力傳輸方案,例如磁耦合諧振(resonant coupling transfer)是替代方案。
本發明在現有的常規活塞和活塞銷產品的基礎上對其結構做出少量修改,在確保結構強度、剛度等滿足要求的前提下,使該發明的應用不必以大幅度地修改原來的活塞和活塞銷結構為代價。現有的量產車型上應用的停缸技術一般只涉及到停止氣門運動,活塞仍在往復運動,活塞裙部、活塞環與缸壁摩擦產生摩擦損失,該機構可以消除這一部分的摩擦損失。
以下將結合附圖對本發明的構思、具體結構及產生的技術效果作進一步說明,以充分地了解本發明的目的、特徵和效果。
附圖說明
圖1是本發明的一個較佳實施例的總體圖示圖;
圖2是本發明的一個較佳實施例的活塞和活塞銷結合狀態示意圖(正視);
圖3是本發明的一個較佳實施例的活塞和活塞銷結合狀態示意圖(仰視);
圖4是本發明的一個較佳實施例的活塞銷內布置示意圖;
圖5是本發明的一個較佳實施例的圓柱端緊定螺釘布置示意圖;
圖6是本發明的一個較佳實施例的活塞銷內部布置透視圖(結合狀態);
圖7是本發明的一個較佳實施例的活塞銷內部布置透視圖(分離狀態);
圖8是現有技術的四桿機構的活塞處於往復運動的狀態;
圖9是現有技術的四桿機構的活塞處於停止運動的狀態;
其中,1-活塞;2-活塞銷;3-連杆;4-氣缸;5-伸縮電線;6-曲軸;7-開口銷;8-滾動軸承;9-弓形彈簧;10-帶楔形槽螺柱;11-壓縮式彈簧;12-圓柱形滑塊;13-
方形滑塊;14-電機;15-圓柱端緊定螺釘;16-電機輸出軸螺紋套;17-電機控制線;18-滾動軸承支撐軸;21-活塞連杆;22-曲軸;23-連件;24-連杆擴展;25-主連杆;26-振子;27-調節器。
具體實施方式
如圖1所示,本發明在現有活塞和活塞銷產品基礎上進行改造,改造後的活塞1的特徵是:活塞銷孔下方開放,以便活塞銷與活塞分離,活塞銷孔上方各安裝有帶楔形槽的螺柱10。如圖2和圖3所示,活塞銷2的特徵是:為保證活塞銷2分離後活塞銷仍可保持原運動軌跡運動,在活塞銷兩端各安裝兩個滾動軸承8,其中一側的滾動軸承支撐軸18配有弓形彈簧9,用於使滾動軸承緊貼氣缸4壁面。滾動支撐軸的軸向限位依靠開口銷7來實現。
如圖4、圖5和圖6所示,活塞銷2內部布置有電機14、圓柱形滑塊12、方形滑塊13、壓縮式彈簧11。電機14輸出軸上安裝有螺紋套16,方形滑塊13中部開有螺紋孔,從而電機輸出軸螺紋套16和方形滑塊13形成簡易螺旋傳動機構,電機軸轉動驅動方形滑塊移動,方形滑塊再進一步驅動圓柱形滑塊12移動。活塞銷2上安裝有兩顆圓柱端緊定螺釘15,圓柱形滑塊12上開槽圓柱端緊定螺釘15的圓柱形頭部進入槽內,但頭部端面不與槽底接觸,圓柱端緊定螺釘15對圓柱形滑塊12起限位作用,一方面限制圓柱形滑塊12的軸向移動範圍,一方面防止圓柱形滑塊12繞軸線轉動。
圓柱形滑塊12一端加工成與帶楔形槽螺柱10上的楔形槽對應的外形,以便圓柱形滑塊12與帶楔形槽螺柱10結合。圓柱形滑塊12與方形滑塊12之間安裝有壓縮式彈簧11,其作用是可確保活塞1與活塞銷2結合之前,圓柱形滑塊12可預先推出,等活塞銷2達到上止點時,在壓縮式彈簧11的作用下圓柱形滑塊12和帶楔形槽螺柱10結合,從而活塞1與活塞銷2結合。
活塞1與活塞銷2分離步驟為:在發動機某一氣缸的某個工作循環內(在該工作循環內,進排氣氣門在執行了此循環的工作動作後即將在下一工作循環停止運動,此功能由現有的氣門停止機構實現),發動機原傳感器和控制器系統檢測到該氣缸處於壓縮、膨脹或排氣衝程時,電機14接受到控制信號將方形滑塊13拉回,兩圓柱形滑塊12由此被拉回,相互接近,等該工作循環完成,活塞1與活塞銷2一同達到排氣上止點之後,由於圓柱形滑塊12已經被拉出帶楔形槽滑塊10的楔形槽,所以活塞銷2與活塞1無連接關係,活塞銷2離開排氣上止點,而活塞1則在摩擦力和燃燒室內外壓力差的作用下留在排氣上止點。如圖7所示,分離完成。
活塞1與活塞銷2結合步驟為:發動機原傳感器和控制器系統檢測到活塞銷處於非上止點位置時,電機14接收到控制信號將方形滑塊13推出,從而兩圓柱形滑塊12相互遠離,等活塞銷2到達上止點後,由於兩圓柱形滑塊12已被預先推出,在壓縮式彈簧11的作用下,兩圓柱形滑塊12端部嵌入帶楔形槽螺柱10的楔形槽內,活塞銷2與活塞1建立連接關係,活塞1開始與活塞銷2一同運動。如圖6所示,結合完成。
以上詳細描述了本發明的較佳具體實施例。應當理解,本領域的普通技術無需創造性勞動就可以根據本發明的構思作出諸多修改和變化。因此,凡本技術領域中技術人員依本發明的構思在現有技術的基礎上通過邏輯分析、推理或者有限的實驗可以得到的技術方案,皆應在由權利要求書所確定的保護範圍內。