射出成型機及其熔膠螺杆的製作方法
2023-06-03 07:22:06
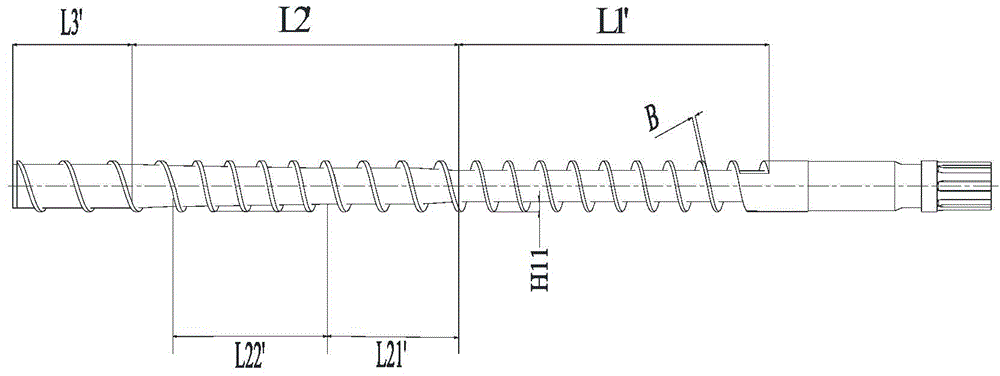
本發明涉及成型設備,尤其涉及一種射出成型機及其熔膠螺杆。
背景技術:
目前,常用的熔膠螺杆為傳統的三段式單螺紋螺杆,通用型變距螺杆,屏障型高混煉螺杆,分離型雙螺紋螺杆。
如圖1所示,其為傳統的三段式單螺紋螺杆。該三段式單螺紋螺杆包括螺紋部分和聯接部分,螺紋部分包括進料段L1'、壓縮段L2'和均化段L3'。進料段L1'由深為H11的平直牙底外螺紋構成,壓縮段L2由傾斜牙底的外螺紋構成,均化段L3由深為H12的平直牙底外螺紋構成。其工作原理是:塑料原料通過料筒入口進入進料段L1',螺杆受馬達驅動旋轉,使原料由螺旋輸送。輸送過程中受料筒壁預熱,經壓縮段L2因牙底變淺影響而受到強烈擠壓塑化(註:不同的塑料受到不同的壓縮比限制,壓縮比等於H11/H12)。塑化的塑料熔體進入均化段進一步熔融。為了保證產量需要增大H12和縮短均化段L3,這往往導致熔融塑化不徹底而含有未熔融的固相,削弱了均化段的職能。尤其在螺杆提高轉速之後更加明顯。為了充份熔融和提高混合效果,必須減小H12和增大均化段L3,但其結果剪切速率增大,熔體溫升提高,產量減小和能量消耗增大。高溫的熔體對於熱敏性塑料有可能造成熱分解。所以傳統的三段式單螺紋螺杆,塑化效果較差,為提高塑化效果會劇烈降低塑化效率。另外傳統三段式單螺紋螺杆,塑化過程固相固體床破碎之後,料筒內壓力呈不規則變化,螺杆受力不均勻容易產生掃膛現象,使螺稜側面沒有足夠的熔體對螺杆螺稜頂面和機筒之間進行充份潤滑,因而易產生磨損。
如圖2所示為通用型變距螺杆。變距螺杆在壓縮段L2起始和收尾採用了螺紋牙變距結構,包括第一牙距變化段L21和第二牙距變化段L22。這種螺杆均化段L3牙距以熔體輸送最佳升角(接近30°)確定,通常是進料段L1'牙距的1.5倍。變化的牙距解決了兩個問題:相同的壓縮比可以把均化 段L3'深度做小,增大剪切提高塑化效果,同時把進料段L1'深度H11做大,能提高塑化效率;當熔料自進料段L1'末進入壓縮段,受變距作用會減小壓縮比例,使熔料有一個平緩的壓縮切換點,壓縮過程也可以通過變距平緩吸收剪切熱能,防止溫升。所以變距螺杆比傳統螺杆提高了塑化效果的同時也可以提高塑化效率。但變距螺杆減小了均化段的有效牙數,減少了塑料在料筒中的駐留時間,熔體沿螺杆軸向溫差較大,因而對塑化效果的提高是有限的,實踐中對一些難熔或混色要求較高生產情況不能滿足。
如圖3所示,其為屏障型高混煉螺杆。該屏障型高混煉螺杆與傳統的三段式單螺紋螺杆相比,多了一個屏障段L4。在L4的外徑上交替開出數量相等的進、出料槽。按螺杆轉動方向,進入出料槽前面的凸稜比螺杆外半徑小一徑向間隙值,這是每一對進、出料槽的唯一通道。這條凸稜稱為屏障稜。當物料從壓縮段進入均化段後,含有未熔融固體顆粒的熔料流到屏障型混煉段時,被分成若干股料流進入屏障段的進料槽,熔料和粒度小於屏障間隙的固態小顆粒料越過屏障稜進入出料槽。未塑化的小顆粒料在屏障間隙受到了剪切作用,大量的機械能轉變為熱能,使小顆粒料熔融。屏障型螺杆解決了普通螺杆塑化品質難提高的問題,其熔體溫度相對均勻,相同產量下熔體質量高。但是屏障型螺杆產量與屏障間隙值的3次方成正比,因此小的屏障間隙值也使螺杆產量降低。
如圖4所示為屏障螺杆的一個變種,屏障段L4為三角槽型的混煉段,進料槽寬度從寬變窄,出料槽從窄變寬。對進入的物料起壓縮作用,越過屏障稜之後起膨脹作用,有利於混合和塑化。此變種還增加了由螺旋短齒構成的混合段。這種屏障螺杆不僅提高了熔融品質,還提高了對色粉的混合能力。但是這種螺杆也受屏障間隙值限制,產量相對受限。
如圖5所示為屏障螺杆的另一個變種,在傳統三段式螺杆均化段L3增加了一段副螺紋,副螺紋與主螺紋有屏障間隙,作用及優缺點與進、出料槽屏障相同。
如圖6所示為目前應用廣泛的分離型雙螺紋螺杆。雙螺紋螺杆主要在壓縮段自進料段L1'末設置一條起屏障作用的副螺紋,將熔融段的螺槽分開為固相槽和液相槽。設置的副螺紋外徑小於主螺紋,副螺紋與料筒內壁有間 隙。當進料段L1'末端的料筒內壁開始出現熔膜,螺稜推進面也開始出現熔料時,固體床迫使熔池中的熔料通過副螺紋頂端的間隙進入液相槽。雙螺紋螺杆因為固液兩相分開,已熔融的熔體及時從固相槽通過副螺稜間隙流入液相槽,新熔化的熔體和未完全塑化的小顆粒在副螺稜間隙中受到剪切作用而塑化。固相槽末端被封死,液相槽中沒有殘留固相,因而塑化品質比普通螺杆高、穩定。但是普通雙螺紋螺杆固相槽的寬度越來越窄,固相與料筒壁接觸面越來越來越小,即熱交換面積越來越小,不利於熔融;而液相槽的寬度越來越寬,熔料反而與機筒內壁的熱交換面積越來越大,不利於降低熔料溫度。所以一些對溫度敏感材料如PC、PVC等適用性不好。
以上六種不同結構的熔膠螺杆,雖然可以在提高塑化品質或者提高塑化效率方面有片面的優勢,但均未完整、很好地解決生產效率、塑化效果、防止溫升缺陷,減少磨損的綜合特性優勢。
技術實現要素:
本發明提出一種射出成型機及其熔膠螺杆,解決現有技術中因傳統的單螺紋熔膠螺杆及常用的幾款或變距或屏障或分離型螺杆不能完整解決生產效率、塑化效果及溫升等性能,以及不能獲得優良綜合性能的問題,使得本發明射出成形機的熔膠螺杆具有更廣泛的適應性。
為解決上述技術問題,本發明提出一種熔膠螺杆,用以將塑料在射出成型機中塑化為熔體的部件,所述熔膠螺杆包括相互連接的螺紋部分和聯接部分,所述螺紋部分設有主外螺紋,所述螺紋部分包括進料段和塑化段。
所述進料段的一端與所述聯接部分連接;塑化段與所述進料段的另一端連接,所述塑化段還設有副外螺紋,所述副外螺紋將所述主外螺紋的螺紋槽分成液相槽和固相槽,所述液相槽和固相槽分別沿螺旋方向貫通,其中,所述液相槽的深度和寬度呈漸深漸寬結構,用以傳送液相塑料;所述固相槽的深度和寬度呈漸淺漸窄結構,用以傳送固相塑料;所述副外螺紋螺稜的外徑小於所述主外螺紋螺稜的外徑,且所述副外螺紋螺稜的外徑呈逐漸變大結構;所述塑化段沿螺紋旋轉方向依次分為第一壓縮段、第二壓縮段、第三壓縮段和第四壓縮段,用以對塑料進行階段性塑化為熔體。
進一步地,所述第一壓縮段為分離型雙壓縮段,用以將塑料平緩塑化; 所述第一壓縮段的主外螺紋的牙距呈逐漸加大結構,所述第一壓縮段的主外螺紋的始端牙距大致等於螺杆直徑,所述第一壓縮段的主外螺紋尾端的牙距為所述螺杆直徑的1.5~1.9倍;所述第一壓縮段的副外螺紋牙距不變且為所述螺杆直徑的1.6~2.0倍。
進一步地,所述第一壓縮段的液相槽的始端深度為2~3mm且呈逐漸變深的結構;所述第一壓縮段固相槽自始端深度開始呈逐漸變淺的結構,所述第一壓縮段固相槽的始端深度符合公式:
其中,所述第一壓縮段固相槽的始端深度為H1,所述螺杆直徑為D;所述第一壓縮段的長度為所述螺杆直徑的3~5倍。
進一步地,所述第二壓縮段為分離型等距壓縮段,用以減少塑料壓縮和剪切,增加固相熱交換和液相混合,使熔料順暢;所述第二壓縮段的主外螺紋牙距和第二壓縮段的副外螺紋牙距均為所述螺杆直徑的1.5~1.9倍。
進一步地,所述第三壓縮段為分離型雙壓縮段,用以將塑料加速塑化為熔體;所述第三壓縮段的主外螺紋的牙距為所述螺杆直徑的1.5~1.9倍;所述第三壓縮段的副外螺紋牙距大致等於螺杆直徑的2.0倍;其中,所述第三壓縮段的副外螺紋牙距大於所述第一壓縮段的副外螺紋牙距,且所述第一壓縮段的副外螺紋牙距大於所述第二壓縮段的副外螺紋牙距。
進一步地,所述第四壓縮段為分離型壓縮收尾段;所述第四壓縮段主外螺紋牙距為所述螺杆直徑的1.5~1.9倍,所述第四壓縮段副外螺紋牙距為所述螺杆直徑的3~7倍;所述第四壓縮段的液相槽深度逐漸變尾端深度,所述第四壓縮段的尾端深度符合公式:
其中,所述第四壓縮段的尾端深度為H22,總壓縮比為i,總壓縮比取值範圍在2~2.5之間;所述第四壓縮段的的長度為所述螺杆直徑的0.5倍。
進一步地,所述副外螺紋螺稜的外徑與所述主外螺紋螺稜的外徑的差值由1~3mm逐漸變為0.3~0.7mm;所述主外螺紋的牙寬為所述螺杆直徑的0.1倍;所述副外螺紋的牙寬為所述螺杆直徑的0.05~0.07倍之間。
進一步地,所述進料段的末尾位置設有副外螺紋,所述塑化段的副外螺紋延續至所述進料段的副外螺紋且所述進料段的副外螺紋與所述塑化段的副外螺紋續接;所述進料段末尾位置的副外螺紋的起點位置距所述進料段與所述聯接部分連接端7~10倍螺杆直徑長度;所述進料段的副外螺紋牙距大於所述主外螺紋牙距。
本發明還提供一種射出成型機,包括如上所述的熔膠螺杆。
進一步地,所述熔膠螺杆沿圓周180度陣列,形成雙頭四螺紋熔膠螺杆。
與現有技術相比,本發明至少具有如下有益效果:本發明的熔膠螺杆在塑化塑料時不僅對塑料熔體進行固、液相分離,使熔融的熔體及時從固相槽通過副外螺紋的螺稜間隙流入液相槽,新熔化的熔體和未完全熔化的小顆粒在副外螺紋的螺稜間隙受到剪切作用塑化和混合;同時,具有長線程的液相槽,相當於比普通螺杆更長的均化段,減少各種波動和提高混合作用,提供穩定的料筒內腔壓力,減少掃膛、磨損。
此外,由於固液相分開,固相槽中塑料所包含的氣體能順利從料鬥排出產生均勻溫度的高質熔體;由於塑化段的長線程設計,螺杆固、液相接近全程,受力均勻,壓力穩定,可減少螺杆與料筒刮磨振動,減少磨損。
再者,由於牙距的變化,形成固相寬度不變的第二壓縮段,改善了固相熱交換,並較大幅度提高了塑化過程固、液相輸送效率,穩定提高產量,防止熔膠過程中容易產生的溫度非受控升高、螺杆打滑、吃料慢等缺陷。長線程的漸變副外螺紋的螺稜,提升了屏障流通量,不僅允許螺杆以較傳統螺杆更高的轉速運行,還可以設置較普通螺杆深的第四壓縮段尾端深度尺寸,進一步提高產量,在不降低對任一塑料塑化性能的前提下,通用於高低粘度塑料。
附圖說明
圖1是現有技術的三段式單螺紋普通螺杆結構示意圖。
圖2是現有技術的變距螺杆結構示意圖。
圖3是現有技術的屏障型高混煉螺杆結構示意圖。
圖4是現有技術的屏障型高混煉螺杆一種變化結構示意圖。
圖5是現有技術的屏障型高混煉螺杆另一種變化結構示意圖。
圖6是現有技術的分離型雙螺紋螺杆結構示意圖。
圖7是本發明射出成型機的結構示意圖。
圖8是本發明射出成型機螺杆組件的結構示意圖。
圖9是本發明射出成型機熔膠螺杆的結構示意圖。
圖10是本發明射出成型機射膠部件的剖視圖。
圖11是本發明射出成型機熔膠螺杆分段示意圖。
其中,附圖標記說明如下:100、射出成型機;1、射膠部件;2、料管組;3、熔膠螺杆;4、螺桿頭部;5、止逆環;6、止推墊圈;7、料管;8、馬達;9、傳動系統;31、螺紋部分;32、聯接部分;311、主外螺紋;312、副外螺紋;313、進料段;314、塑化段;315、液相槽;316、固相槽;3131、起始段;3141、第一壓縮段;3142、第二壓縮段;3143、第三壓縮段;3144、第四壓縮段。
具體實施方式
為了進一步說明本發明的原理和結構,現結合附圖對本發明的優選實施例進行詳細說明。
參閱圖7至圖11,本發明提供一種射出成型機100,其包括一射膠部件1,該射膠部件1包括一料管組2,該料管組2包括一熔膠螺杆3,該熔膠螺杆3用以將塑料在射出成型機100中塑化為熔體。熔膠螺杆3通過傳動系統9與驅動馬達8連接,另一端安裝有止逆閥三小件,止逆閥三小件包括螺桿頭部4、止逆環5和止推墊圈6。
熔膠螺杆3包括相互連接的螺紋部分31和聯接部分32。該聯接部分32包括聯接鍵、槽、軸頸和定位安裝孔。
螺紋部分31為熔膠螺杆3的主體部分,包括進料段313和塑化段314,其中,進料段313的一端與聯接部分32連接,塑化段314與進料段313的另一端連接。螺紋部分31上設有主外螺紋311,主外螺紋311為右旋或左旋的螺紋,主外螺紋牙寬B為0.5倍螺杆直徑。
進料段313的主外螺紋311為深的平直牙底定距螺紋,進料段主外螺紋牙距P1大致等於螺杆直徑D,進料段主外螺紋牙底深度H1符合公式:
進料段313的長度L1由熔膠螺杆3的長徑比決定,熔膠螺杆3的長徑比由射出成型機100的機器參數決定,其中,熔膠螺杆3的長徑比範圍在18~25之間。本實施例中,進料段313的長度L1在螺杆直徑D的9~12倍範圍之間,對於大長徑比的熔膠螺杆,進料段313的長度L1取大值;對於小長徑比熔膠螺杆,進料段313的長度L1取小值。
進料段313的末端位置設置有副外螺紋312的起始段3131,該段的副外螺紋312的牙距S1在倍螺杆直徑D的1.6~2.0倍且大於進料段主外螺紋牙距P1,形成主外螺紋311的槽收窄,原料在該副外螺紋312的起始段3131開始受到容積壓縮。更優地,副外螺紋312的起始段3131設在距進料段313的螺杆直徑D的7~10倍位置處,即原料在此位置開始進入容積壓縮狀態。
塑化段314的主外螺紋311主要為傾斜牙底,該段上還包括與主外螺紋311螺旋方向相同的副外螺紋312,主外螺紋311和副外螺紋312的牙距漸變,塑化段314的副外螺紋312的牙寬b為螺杆直徑D的0.05~0.07倍之間,塑化段314的長度為L2。在塑化段314上,副外螺紋312將主外螺紋311的螺紋槽分成液相槽315和固相槽316,液相槽315和固相槽316分別沿螺旋方向貫通。液相槽315的深度和寬度呈漸深漸寬結構,用以傳送液相塑料;固相槽316的深度和寬度呈漸淺漸窄結構,用以傳送固相塑料;參見圖11,熔膠螺杆3的液相槽315深度變化K1逐漸變深,固相槽316深度變化K2逐漸變淺,其中該液相槽315的深度是指從主外螺紋牙頂T1至液相槽牙底T2的距離,該固相槽316的深度是指從主外螺紋牙頂T1至固相槽牙底T3的距離。
塑化段314沿螺紋旋轉方向依次分為第一壓縮段3141、第二壓縮段3142、第三壓縮段3143和第四壓縮段3144,用以對塑料進行階段性塑化為熔體。
請參閱圖11對上述四個壓縮段進行詳細闡述,第一壓縮段3141為分離型雙壓縮段,用以將塑料平緩塑化。第一壓縮段3141的主外螺紋311從始端到尾端的牙距P1逐漸變為牙距P2,牙距P2的範圍在螺杆直徑1.5~1.9倍之間;第一壓縮段3141的副外螺紋312牙距S1保持不變,且該段副外螺紋312延續自進料段313末開始的副外螺紋312。
第一壓縮段3141的液相槽315起始於塑化段314接近開始處,其始端深度H21為2~3mm且逐漸變深,初始寬度則儘可能小,以利於平緩順暢塑化;第一壓縮段3141的固相槽316自始端深度開始逐漸變淺,第一壓縮段3141 固相槽316的始端深度與進料段313的主外螺紋311牙底深度H1相同。
本實施例中,第一壓縮段3141的長度I1為螺杆直徑的3~5倍。由於第一壓縮段3141主外螺紋牙距增大,固、液相槽相對普通雙螺紋螺杆有逐漸增寬,因而相對舒緩了普通雙螺紋螺杆底徑和槽寬雙壓縮帶來的容積階躍,有利於順暢進料。
第二壓縮段3142為分離型等距壓縮段,用以減少塑料壓縮和剪切,增加固相熱交換和液相混合,使熔料順暢,該段是塑化段314的主體部分。第二壓縮段3142的主外螺紋311的牙距和副外螺紋312牙距相同均為螺杆直徑的1.5~1.9倍。固相槽316沿第二壓縮段3142坡度逐漸變淺,液相槽315沿第二壓縮段3142坡度逐漸變深。第二壓縮段3142的結構相對於變窄變淺的傳統雙螺紋,因其不變的寬度和加深的液相槽更有利於固相自料筒吸熱及熔體越過副外螺紋的螺稜產生液相沿深度的變化改善液相熱交換和混合功能,防止熔膠過程中容易產生的溫度非受控升高、螺杆打滑、吃料慢等缺陷。第二壓縮段3142的長度I2符合公式:I2=L2-(5~7)D。
第三壓縮段3143為大導程副外螺紋的分離型雙壓縮段,用以將塑料加速塑化為熔體;第三壓縮段3143的主外螺紋311的牙距延續第二壓縮段3142的牙距P2,即1.5~1.9倍螺杆直徑;第三壓縮段3143的副外螺紋312牙距S2為2.0倍螺杆直徑或約2.0倍螺杆直徑,且同時保證S2>S1>P2,即第三壓縮段3143的副外螺紋312牙距大於第一壓縮段3141的副外螺紋312牙距,且第一壓縮段3141的副外螺紋312牙距大於第一壓縮段3141尾端的主外螺紋311牙距和第三壓縮段3143的主外螺紋311的牙距。該段的固相槽316繼續逐漸變淺,液相槽315逐漸變深至尾端深度H22。第三壓縮段3143液相槽315的尾端深度H22符合公式:
其中,總壓縮比為i,總壓縮比取值範圍在2~2.5之間。第三壓縮段3143已沒有固相的塑料,全部塑料都已軟化成粘度或高或低的不均勻熔體。該段取副外螺紋312牙距取大值即大致等於2.0倍螺杆直徑,不僅獲得最優熔體輸送螺旋升角約為30°,也使固相槽迅速收窄並逐漸變淺,以加速熔融,液 相槽逐漸變深,進一步均化,在塑化效率和品質上比普通雙螺紋螺杆都有改善。第三壓縮段3143的長度I3保證該段副螺紋牙距之外,其長度不受限制。
第四壓縮段3144為分離型壓縮收尾段;第四壓縮段3144主外螺紋311牙距繼續保持不變即為螺杆直徑的1.5~1.9倍,第四壓縮段3144副外螺紋312牙距為螺杆直徑的3~7倍。
固相槽316在該段約0.5倍螺杆直徑的長度位置牙底深度變為收尾深度H3,隨後漸變淺收窄消失,液相槽315擴展為整個牙槽,且延續第三壓縮段I3液相槽315的尾端深度H22。
第四壓縮段3144的的長度為螺杆直徑的0.5倍。第四壓縮段3144是一種雙螺紋固相槽快速收尾結構,使第四壓縮段3144的長度I4約為0.5倍螺杆直徑,至此所有固相塑料都已被壓縮剪切受熱塑化。
在本發明優選的實施例中,進料段313和塑化段314的副外螺紋312螺稜的外徑小於主外螺紋311螺稜的外徑,且副外螺紋312螺稜的外徑呈逐漸變大結構,也就是說副外螺紋312牙頂間隙σ是變化的,該副外螺紋312牙頂間隙σ是指主外螺紋牙頂T1至副外螺紋牙頂T4之間的距離。副外螺紋312螺稜的外徑與主外螺紋311螺稜的外徑的差值,即主外螺紋牙頂T1至副外螺紋牙頂T4之間的距離由1~3mm逐漸變為0.3~0.7mm。在進料段313末尾和塑化段314開始位置牙頂間隙σ在1~3mm之間,允許小的未熔顆粒越過副外螺紋螺稜進入液相槽。這樣就比一般屏障或傳統雙螺紋螺杆的間隙通道大,有利於提升效率。未熔顆粒越過副外螺紋螺稜時受到剪切作用,並在液相槽後續長行程中受混合與熱傳導作用充分塑化。牙頂間隙σ在塑化段末尾位置為0.3~0.7mm。塑化段末尾位置固相亦已塑化,極小的間隙才能對熔體進一步剪切混合,產生高質熔體;同時,當熔膠越過副外螺紋螺稜進入漸深的液相槽時,形成渦流,產生沿液相槽截面的渦卷流,不僅對熔體產生均勻混沌的混合,還能使熔體與料筒的熱交換更充份,產生均勻溫度的高質熔體。
此外,當應用於直徑為120mm及以上的中大型熔膠螺杆時,可以將本發明的熔膠螺杆結構按圓周180度陣列,形成雙頭四螺紋變徑變距熔膠螺杆,該雙頭四螺紋變徑變距熔膠螺杆更符合大型螺杆的低轉速工作特性,更有利於提高塑化能力,可獲得最優的塑化效率。
如圖10所示,當馬達8經傳動系統9驅動熔膠螺杆3旋轉,原料自螺杆進料段313入螺紋槽,受螺紋的旋轉輸送作用,向螺桿頭部4移動。這過程中原料受料管7傳遞熱量預熱。原料到達進料段313末的副螺紋起始段3131時,由於副外螺紋的螺旋升角影響受到初壓縮。到達第一壓縮段3141受底徑深度變淺、牙距變化、副外螺紋屏障及與料筒壁旋轉摩擦的影響,受到強列壓縮和剪切,釋放大量熱能,開始熔化塑料。已熔化的塑料及未熔小顆粒受固體床擠壓及時越過副外螺紋的螺稜進入液相槽。未熔塑料繼續行程到達等第二壓縮段3142受到平緩壓縮及改善的熱傳導,不斷熔融。熔膠受擠壓越過不斷減小的副外螺紋螺稜間隙σ獲得合適的剪切流入液相槽形成渦圈流被混合渾沌。當塑料進入第三壓縮段3143和第四壓縮段3144時,已基本塑化,此時較強的剪切有利於提高效率和塑化品質,產生高質熔體進入料筒熔池,為下一次注射作好準備。
本發明射出成型機及其熔膠螺杆具有如下技術效果:
1、通過在熔膠螺杆上設塑化段,採用變徑變距技術,以最優的螺旋升角和較深的液相通道快速輸送熔體,減少熔膠駐留時間,提高塑化能力。
2、在塑化段採用變距雙螺紋技術,使固相和液相塑料獲得合理的熱傳導、剪切量和混合過程,充份熔化原料,產生均勻溫度的混沌熔體。
3、熔膠螺杆只分為兩段,液相長度在10~15螺杆直徑之間,這是一個長程的均化過程,相對更穩定地輸送熔體,減少掃膛現象。同樣地,壓縮過程在10~15螺杆直徑之間,使塑化過程平緩穩定。固、液相分離,減少了液相受固相擠壓剪切發熱,使螺杆轉速可以提高,這也間接提高了熔膠螺杆的產量;長線程設計的漸變副外螺紋螺稜,提升了屏障流通量,不僅允許熔膠螺杆以較傳統螺杆更高的轉速運行,還可以設置較普通螺杆深的第四壓縮段尾端深度尺寸,進一步提高產量,在不降低對任一塑料塑化性能的前提下,通用於高低粘度塑料。
4、本發明的熔膠螺杆能夠實現塑化能力與熔體質量雙提高,避免了傳統螺杆中塑化品質、塑化效率與螺杆通用性三項指標不可兼得的缺陷,生產過程穩定,有效克服熔膠過程中容易產生的溫度非受控升高、螺杆打滑、吃料慢及容易磨損等缺點,是具有廣泛適用性的通用型優質螺杆。
以上僅為本發明的較佳可行實施例,並非限制本發明的保護範圍,凡運 用本發明說明書及附圖內容所作出的等效結構變化,均包含在本發明的保護範圍內。