一種熔融鹽中催化裂解甲烷製備氫氣的方法及實現該方法的裝置與流程
2023-06-10 18:39:01 2
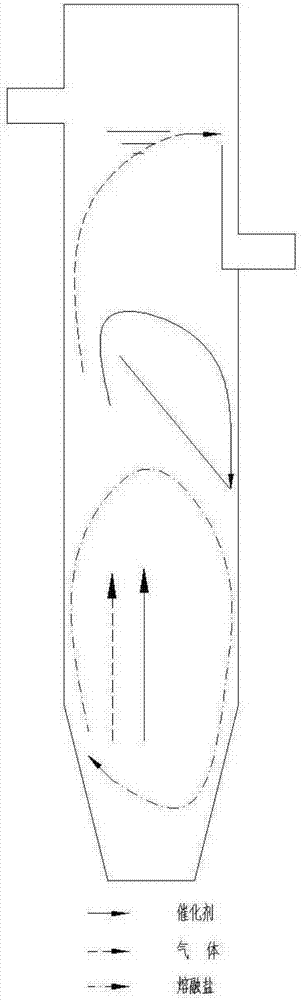
技術領域:
本發明屬於能源利用技術領域,具體涉及一種熔融鹽中催化裂解甲烷製備氫氣的方法及實現該方法的裝置。
背景技術:
:
氫作為一種清潔的能源,有望成為21世紀的主要能源之一。目前全世界大約96%的氫能是通過化石燃料(天然氣、煤炭、石油等)的水蒸氣催化氣化、部分氧化的方法製備。
熔融鹽是指鹽的熔融態液體,通常說的熔融鹽是指無機鹽的熔融體。目前使用較多的高溫熔融鹽為鹼金屬(li、na、k等)的碳酸鹽、硝酸鹽、氯化物等。研究結果表明熔融鹽對ch4裂解效果較差。中國專利zl201110166589.9一種基於熔融鹽特性的粗合成氣淨化提質新方法。該發明公開了一種基於熔融鹽特性的粗合成氣淨化提質新方法,包括以下步驟:1)高溫顆粒物脫除;2)烴類臨氧脫除3)氣體汙染物脫除及調質等步驟將粗合成氣烴類選擇性轉化、焦油裂解、h2s、hcl脫除和h2/co比值調質放在同一個反應器內完成;該方法通過臨氧轉化的方法將烴類(包含甲烷)轉化為合成氣。中國專利zl201210332772.6一種利用熔融鹽製備氫氣的方法,該發明公開了一種利用熔融鹽製備氫氣的方法,包括以下步驟:1)熔融鹽反應制氫:將經過預處理的含碳原料以及氧化劑通入熔融鹽介質中,在熔融鹽反應爐內反應制氫;2)氣體分離:將步驟(1)得到的富氫氣通入氣體分離裝置,分離其中的雜質氣體,得到氫氣;3)雜質氣體回用。該方法所指的含碳燃料是指液體或在固體燃料,同時該方法會產生部分的烴類氣體,並且不能轉化該部分氣體,需要通過步驟2)對該部分氣體進行分離。
以甲烷為原料製取氫氣是目前工業上常用的制氫方法之一,有兩種主流的工藝路線。
1)通過氣化,將甲烷先轉化為合成氣(主要成分是h2、co),然後通過分離或者轉化將合成氣中的co去除從而得到純氫。氣化過程可以採用甲烷水蒸氣重整(srm)、甲烷部分氧化(pom)、自熱重整(atr)、二氧化碳重整等工藝;
2)採用甲烷催化裂解實現炭黑和氫氣的聯產,中國專利zl201510358286.5公開了一種鎳基催化劑及其製備方法與甲烷催化裂解生產氫氣的方法。改發明利用甲烷催化裂解生產氫氣的方法包括:使包括甲烷的原料氣在高密度循環流化床反應器中與催化劑接觸並發生催化裂解反應,得到包括氫氣的生成氣和失活的催化劑,在沉降器中分離後,催化劑攜帶積炭進入再生器再生,得到包括co或合成氣的再生煙氣,再生後的催化劑重新進入反應器。再生產生的熱量用來提供整個系統的能量需要,實現自熱操作。
上述專利均未涉及採用流化床反應器在熔融鹽中利用催化劑催化裂解天然氣製備氫氣的裝置及方法。
技術實現要素:
:
本發明的目的在於提供一種熔融鹽中催化裂解甲烷製備氫氣的方法及實現該方法的裝置,其不需要後續的氣體分離工序,可以直接在熔融鹽中產生氫氣,工藝流程緊湊簡單,易於放大,解決了現有技術中存在的問題。
本發明的目的是提供一種熔融鹽中催化裂解甲烷製備氫氣的方法,包括如下步驟:包括如下步驟:制氫原料、氣化劑、熔融鹽從流化床反應器底部進入流化床反應器,流化床反應器內的催化劑與制氫原料反應產生固體產物和氣體產物,固體產物在熔融鹽及氣體產物共同作用下處於流態化狀態,並在流化床反應器中下部形成固體產物及催化劑的密相區,流化床反應器中上部為液態熔融鹽;進入流化床反應器的制氫原料在熔融鹽、催化劑、氣化劑共同作用下催化轉化為富氫氣體和固體碳,富氫氣體和固體碳從流化床反應器氣體出口流出,進入氣固分離器,經氣固分離器分離得到氫氣及固體碳;流化床反應器內含有催化劑、制氫原料反應產生的固體產物的熔融鹽經過液固分離後,一部分重新從流化床底部循環進入流化床反應器為流化床流態化提供動力;另一部分進入熔融鹽再生系統進行再生,然後重新從流化床底部循環進入流化床反應器為流化床流態化提供動力。在本發明中固體產物為碳,固體碳通入流化床反應器進行循環利用;通過對少量甲烷熱裂解產生的固體碳進行循環利用,可以提高制氫原料的利用率,提高氫氣產率。
熔融鹽再生系統所採用的熔融鹽再生方法為苛化法或其衍生工藝。通過該方法再生,在再生過程中可以去除混入熔融鹽中的灰分,s、cl等雜質元素,使熔融鹽恢復到初始狀態。
甲烷在催化劑和水蒸氣的共同作用下轉化為co、h2以及少量的c、co2。
然後產生的co、co2等在熔融鹽的作用下被吸收或轉化。
2moh+co2=m2co3+h2o
co+2moh=m2co3+h2總反應(其中m為k或者na)
通過上述過程每1mol的甲烷可以轉化為4mol的氫氣。
所述的熔融鹽為moh和m2co3的混合物,其中m為鹼金屬,moh的質量分數為60%~90%,所述的m為鉀或鈉。
所述的制氫原料為含碳燃料,優選的採用富含甲烷的氣體燃料,更為優選的可以採用天然氣或垃圾填埋氣。
所述的催化劑為甲烷催化裂解催化劑,優選的採用ni基的甲烷裂解催化劑。
因為顆粒狀的甲烷裂解催化劑在熔融鹽液體中處於流態化狀態,催化劑顆粒之間不斷的摩擦碰撞,可以有效防止顆粒表面積碳。同時熔融鹽是一種常用的催化劑表面處理劑及碳轉化催化劑。通過使催化劑顆粒在熔融鹽中流化狀態,可以有效延長催化劑使用壽命。
一種實現熔融鹽中催化裂解甲烷製備氫氣的方法的裝置,該裝置包括流化床反應器、氣固分離器、熔融鹽循環泵和熔融鹽再生系統,流化床反應器底部設置有制氫原料進口、氣化劑進口、循環熔融鹽進口及物料循環口,流化床反應器中上部設置有氣體產物出口和熔融鹽出口,流化床中部設置有傾斜的分隔板;熔融鹽再生系統和熔融鹽循環泵分別通過管道與熔融鹽出口相連;氣固分離器通過管道與氣體產物出口相連,氣固分離器固體出口通過管道與物料循環口相連。通過對少量甲烷熱裂解產生的固體碳進行循環利用,可以提高制氫原料的利用率,提高氫氣產率。
氣體產物出口的高度高於熔融鹽出口的高度,即流化床反應器中熔融鹽液面低於流化床反應器氣體出口,從而保證液態熔融鹽不會進入流化床反應器氣體出口及氣體管路,防止熔融鹽在上述位置冷凝堵塞管路。
優選地,所述的流化床反應器內設置有分隔板,所述的分隔板與水平面的夾角為45°~60°。在該角度範圍內分隔板可以對熔融鹽中的氣泡進行有效的阻擋,並且可以使得沉降在分隔板上的固體催化劑可以在重力左右下自動向下運動。在流化床反應器豎直壁面與分隔板傾斜向上的一端留有氣體通道,在流化床豎直壁面與分隔板傾斜向下的一端設置有固體顆粒通道。通過該分隔板的阻擋使流化床在的氣泡在上升過程中聚集到流化床豎直壁面與分隔板傾斜向上的一端,然後繼續在熔融鹽中上升。同時在分隔板阻擋下,在流化床內形成一個沒有氣泡並且熔融鹽流速較小的區域,實現熔融鹽中氣泡和固體催化劑的分離,並且使固體催化劑顆粒在該區域沉降下來,並通過流化床豎直壁面與分隔板傾斜向下的一端設置的固體顆粒通道返回到流化床底部,從而實現固體催化劑顆粒的循環。熔融鹽在該分隔板的阻擋作用下在熔融鹽底部也進行內循環流動。
優選地,所述的熔融鹽出口處設置有固液分離裝置,所述固液分離裝置分別與熔融鹽循環泵和分隔板再生系統連接。固液分離裝置可以是過濾式裝置,也可以是慣性分離式裝置。通過分離裝置將與熔融鹽混合在一起的催化劑、碳等固體組分保留在流化床反應器內,使得進入熔融鹽循環泵及熔融鹽再生系統的基本只有液態的熔融鹽。
本發明的有益效果是:
1)本發明提供的設備及方法裂解甲烷產生氫氣的理論產率為1mol甲烷可以產生4mol氫氣,遠高於傳統工藝1mol甲烷可以產生3mol氫氣的理論產率,氫氣產率可提高30%;
2)本發明提供的設備及方法不需要後續的氣體分離工序,可以直接在熔融鹽中產生氫氣,工藝流程緊湊簡單,易於放大;
3)本發明提供的設備及方法可以有效提高催化劑使用壽命。
附圖說明:
圖1是本發明熔融鹽中催化裂解甲烷製備氫氣的裝置示意圖;
圖2是本發明熔融鹽中催化裂解甲烷製備氫氣的裝置中氣-液-固流動示意圖;
圖中:1、流化床反應器;11、固液分離裝置;12、熔融鹽出口;13、分隔板;14、氣體產物出口;15、物料循環口;16、制氫原料進口;17、氣化劑進口;18、循環熔融鹽進口;2、氣固分離器;21、氣體出口;22、固體出口;3、熔融鹽循環泵;4、熔融鹽再生系統。
具體實施方式:
以下實施例是對本發明的進一步說明,而不是對本發明的限制。
除特別說明,本發明中的實驗材料和試劑均為本技術領域常規市購產品。
實施例1
參閱圖1及圖2:本發明提供一種熔融鹽中催化裂解甲烷製備氫氣的方法及實現該方法的裝置,其不需要後續的氣體分離工序,可以直接在熔融鹽中產生氫氣,工藝流程緊湊簡單,易於放大,解決了現有技術中存在的問題。
實現熔融鹽中催化裂解甲烷製備氫氣的方法的裝置,該裝置包括流化床反應器1、氣固分離器2、熔融鹽循環泵3、熔融鹽再生系統4。流化床反應器底部設置有制氫原料進口16、氣化劑進口17、循環熔融鹽進口18及物料循環口15,流化床反應器中上部設置有氣體產物出口14,流化床反應器中上部設置有熔融鹽出口12,流化床中部設置有傾斜的分隔板13;熔融鹽再生系統及熔融鹽循環泵分別通過管道與熔融鹽出口相連;氣固分離器通過管道與流化床氣體產物出口相連,氣固分離器固體出口22通過管道與物料循環口相連。氣固分離器的氣體出口21將得到的氫氣收集。通過對少量甲烷熱裂解產生的固體碳進行循環利用,可以提高制氫原料的利用率,提高氫氣產率。
熔融鹽出口處設置有固液分離裝置11,固液分離裝置分別與熔融鹽循環泵和分隔板再生系統連接。固液分離裝置可以是過濾式裝置,也可以是慣性分離式裝置。通過分離裝置將與熔融鹽混合在一起的催化劑、碳等固體組分保留在流化床反應器內,使得進入熔融鹽循環泵及熔融鹽再生系統的基本只有液態的熔融鹽。
一種熔融鹽中催化裂解甲烷製備氫氣的方法,包括如下步驟:將天然氣、150℃飽和水蒸氣及氧氣、熔融鹽從流化床底部進入流化床反應器,所採用的天然氣與氧氣的化學當量比為0.28,流化床反應器內的溫度為900℃,流化床反應器內的ni基的甲烷裂解催化劑與天然氣反應產生固體碳和富氫氣體,流化床反應器內的ni基的甲烷裂解催化劑及天然氣反應產生的固體碳在熔融鹽及富氫氣體共同作用下處於流態化狀態,並在熔融鹽反應器中下部形成一個催化劑及天然氣反應產生的固體產物的密相區,反應器中上部為液態熔融鹽。進入流化床反應器的天然氣在熔融鹽、催化劑、水蒸氣共同作用下催化轉化為富氫氣體和固體碳,富氫氣體、固體碳從流化床反應器氣體出口流出,進入氣固分離器,經氣固分離器分離得到氫氣及固體碳。流化床內含有催化劑、天然氣反應產生的固體碳的熔融鹽經過液固分離後,一部分直接重新從流化床底部循環進入流化床反應器為流化床流態化提供動力;一部分進入熔熔融鹽再生系統進行再生,然後重新從流化床底部循環進入流化床反應器為流化床流態化提供動力。固體碳通入流化床反應器進行循環利用;通過對少量甲烷熱裂解產生的固體碳進行循環利用,可以提高制氫原料的利用率,提高氫氣產率。
熔融鹽再生系統所採用的熔融鹽再生方法為苛化法。通過該方法再生,在再生過程中可以去除混入熔融鹽中的灰分,s、cl等雜質元素,使熔融鹽恢復到初始狀態。
甲烷在催化劑和水蒸氣的共同作用下轉化為co、h2以及少量的c、co2。
然後產生的co、co2等在熔融鹽的作用下被吸收或轉化。
2naoh+co2=na2co3+h2o
co+2naoh=na2co3+h2總反應
熔融鹽為naoh和na2co3的混合物,在本實施例中,熔融鹽混合物中naoh的質量分數為90%,制氫原料為天然氣,,催化劑採用ni基的甲烷裂解催化劑。
因為顆粒狀的甲烷裂解催化劑在液態熔融鹽中處於流態化狀態,催化劑顆粒之間不斷的摩擦碰撞,可以有效防止顆粒表面積碳。同時熔融鹽是一種常用的催化劑表面處理劑及碳轉化催化劑。通過使催化劑顆粒在熔融鹽中流化狀態,可以有效延長催化劑使用壽命30%。
氣體產物出口的高度高於熔融鹽出口的高度,即流化床反應器中熔融鹽液面低於流化床反應器氣體出口,從而保證液態熔融鹽不會進入流化床反應器氣體出口及氣體管路,防止熔融鹽在上述位置冷凝堵塞管路。
熔融鹽出口處設置有固液分離裝置,固液分離裝置分別與熔融鹽循環泵和分隔板再生系統連接,為慣性分離式裝置。通過分離裝置將與熔融鹽混合在一起的催化劑、碳等固體組分保留在流化床反應器內,使得進入熔融鹽循環泵及熔融鹽再生系統的基本只有液態的熔融鹽。
通過上述過程,本發明所提供的工藝可以直接一步將1mol的甲烷轉化為4mol的氫氣。
將熔融鹽再生前後的組分做對比,如表1所示。
表1熔融鹽再生前後主要組成
由表1可以得出:通過熔融鹽再生系統再生,可以去除混入熔融鹽中的灰分,s、cl等雜質元素,使熔融鹽恢復到初始狀態,使熔融鹽可以循環使用。
作為本工藝流程的對比:天然氣採用部分氧化(pom)轉化工藝在1000℃附近進行甲烷轉化1mol甲烷可產生1mol的co及2mol的h2,然後再經過水氣平衡催化變換,可將產氣中的1molco轉化為1molh2,整個過程總的來說1mol甲烷可轉化為3mol的氫氣。
採用本項目的工藝,與傳統工藝相比,每1mol甲烷可以多生產1molh2。同時本發明提供工藝氣體分離工序,直接在熔融鹽中產生氫氣,並可提高催化劑使用壽命30%左右。
所製得的產氣中氫氣含量為99%。
實施例2
與實施例1相同,不同之處在於:
制氫原料為垃圾填埋氣,流化床反應器內溫度為800℃,氣化劑為空氣,催化劑為甲烷催化裂解用ni粉,熔融鹽為氫氧化鉀和碳酸鉀的混合物,其中氫氧化鉀的質量分數為60%。分隔板與水平面的夾角為60°。
所製得的產氣中氫氣含量為61%,其餘39%主要為氮氣。
實施例3
與實施例1相同,不同之處在於:
制氫原料為天然氣,流化床反應器內溫度為1000℃,氣化劑為氧氣,催化劑為甲烷催化裂解用ni粉,熔融鹽為氫氧化鉀和碳酸鉀的混合物,其中氫氧化鉀的質量分數為75%,分隔板與水平面的夾角為45°。
所製得的產氣中氫氣含量為99.5%。
以上對本發明提供的熔融鹽中催化裂解甲烷製備氫氣的方法及實現該方法的裝置進行了詳細的介紹,以上實施例的說明只是用於幫助理解本發明的技術方案及其核心思想,應當指出,對於本技術領域的技術人員來說,在不脫離本發明原理的前提下,還可以對本發明進行若干改進和修飾,這些改進和修飾也落入本發明權利要求的保護範圍內。