一種3D噴射列印裝置及其列印方法與流程
2023-06-04 19:37:18 1
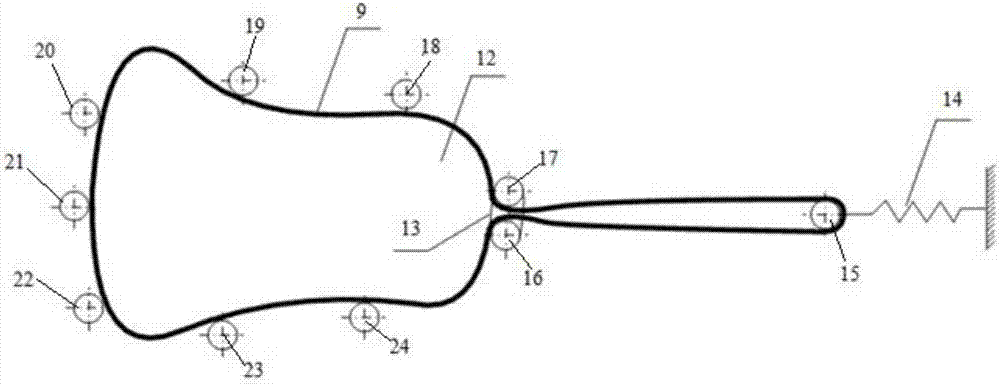
本發明屬於快速成型設備技術領域,具體涉及一種3d噴射列印裝置及其列印方法。
背景技術:
3d列印技術又稱為三維列印技術,是以數字模型文件為基礎,採用列印頭、噴嘴或其他列印技術逐層列印的方式來構造物體的技術。3d列印的設計過程是:先通過計算機創建三維模型,再將三維模型「分區」成逐層的截面,即將3d數字模型轉化成2d數字模型,最後控制印表機逐層列印。該技術的缺點是製成零件的強度低、「臺階效應」導致精度偏差大、材料的局限性及效率低。
噴射成型是把金屬熔融、液態金屬霧化、快速凝固、噴射沉積成形集成一個冶金操作流程中製成金屬材料產品的新工藝技術。該技術對於發展新材料、改革傳統工藝、提升材料性能都有重大作用。傳統噴射技術的缺點是對液體衝擊力大,容易促使液體偏移、固化劑滲透等問題,導致成型模型的精度質量差,而不能被廣泛的應用。
技術實現要素:
為了克服現有3d列印技術存在產品強度較差、精度較低及效率低的不足,本發明提出了一種列印出的產品強度好、精度較高及效率高的3d噴射列印裝置及其列印方法。
為了達到上述目的,本發明的技術方案如下:
本發明提供一種3d噴射列印裝置,包括:
三維建模模塊,用於建立三維模型;
模型輪廓成型模塊,根據三維模型提取三維模型的數據設定模具界限特徵;
數字霧化金屬滴液模塊,包括數字流體發生器和數字噴射控制模塊,數字噴射控制模塊的輸出端與數位化噴射液流霧化模塊的輸入端連接用於驅動數位化噴射液流霧化模塊按照設定的順序與方向噴射,數字流體發生器根據三維模型的數據產生滴液;
成型模塊,成型模塊設有成型內腔,成型模塊由不浸滴液的纖維布製備而成的,成型模塊的表面設有高強度超疏液塗層;
計算機控制模塊,其與三維建模模塊、模型輪廓成型模塊、數字霧化金屬滴液模塊、成型模塊控制連接。
優選的,三維建模模塊通過計算機建模軟體建立三維模型或通過多維度掃描三維物體獲得三維模型。
優選的,還設有金屬液供料機構,包括坩堝和上通棒,上通棒豎直貫通設置於坩堝內。
優選的,數字流體發生器設置於坩堝的下方且其進料口與坩堝的出料口連接,數字流體發生器內設有數字流體導流管,數字流體導流管的底部設有噴嘴。
優選的,成型模塊包括工作檯、基材和模具體,模具體設有成型內腔,模具體內且位於成型內腔的周向設有小擋板,基材套設於模具體上,基材上設形態定位銷軸、擋板定位銷軸、彈簧和連接銷軸,形態定位銷軸均勻分布於成型內腔周向,擋板定位銷軸設置於小擋板的兩側,連接銷軸連接設置於彈簧上且設置於小擋板的外側。
本發明還提供一種3d噴射列印方法,包括以下步驟:
s1、創建3d噴射列印所需要的三維模型;
s2、根據步驟s1中獲得的三維模型的提取模型輪廓數據;
s3、根據步驟s2中獲得的模型輪廓數據設計噴射路徑;
s4、驅動數字流體發生器霧化產生一定尺寸的液滴,並根據步驟s3中的噴射路徑控制數字流體發生器向成型模塊的成型內腔內噴射;
s5、完成零件成型。
優選的,步驟s1中通過計算機建模軟體建立三維模型或通過多維度掃描三維物體獲得三維模型。
優選的,噴射路徑為計算機軟體計算模擬噴射路徑或自主設計模擬噴射路徑。
有益效果:本發明按照噴射成型工藝將金屬液霧化成細小顆粒,藉助成型模塊把金屬液霧化的小顆粒噴射到成型內腔中,最終形成所需的實體模型,運用計算機控制噴射路徑,保證噴射液流不會發生較大的偏移,提高了實體零件精度、強度及生產效率。
附圖說明
圖1為本發明的整體結構示意圖。
圖2為本發明的成型模的結構示意圖。
圖3為本發明的控制模塊示意圖。
圖4為本發明的列印方法的工藝流程圖。
具體實施方式
下面結合附圖詳細說明本發明的優選實施方式。
為了達到本發明的目的,如圖1至圖3所示,在本發明的其中一種實施方式中提供一種3d噴射列印裝置,包括:
三維建模模塊,用於建立三維模型;
模型輪廓成型模塊,根據三維模型提取三維模型的數據設定模具界限特徵;
數字霧化金屬滴液模塊,包括數字流體發生器3和數字噴射控制模塊,數字噴射控制模塊的輸出端與數位化噴射液流霧化模塊的輸入端連接用於驅動數位化噴射液流霧化模塊按照設定的順序與方向噴射,數字流體發生器根據三維模型的數據產生滴液;
成型模塊,成型模塊設有成型內腔,成型模塊由不浸滴液的纖維布製備而成的,成型模塊的表面設有高強度超疏液塗層;
計算機控制模塊,其與三維建模模塊、模型輪廓成型模塊、數字霧化金屬滴液模塊、成型模塊控制連接。
本實施方式按照噴射成型工藝將金屬液霧化成細小顆粒,藉助成型模塊把金屬液霧化的小顆粒噴射到成型內腔中,最終形成所需的實體模型,運用計算機控制噴射路徑,保證噴射液流不會發生較大的偏移,提高了實體零件精度、強度及生產效率。同時,成型模塊由不浸滴液的纖維布製備而成,限定噴射滴液的界限,高強度超疏液塗層與金屬滴液不相容,在成型內腔內不會殘留金屬滴液,金屬滴液可以自由脫落。
其中,三維建模模塊通過計算機建模軟體建立三維模型或通過多維度掃描三維物體獲得三維模型。
另外,數字流體發生器根據三維模型的數據產生一定尺寸的滴液,若該三維模型的尺寸較大,為提高生產效率,計算機控制模塊可以驅動數字流體發生器產生直徑相對較大的液滴;若該三維模型的尺寸較小,並且精度要求較高,則計算機可驅動數字流體發生器產生直徑相對較小的液滴以滿足要求。所以,具體的液滴尺寸可根據模型自身的屬性及生產現狀決定。
如圖1所示,還設有金屬液供料機構,包括坩堝1和上通棒2,上通棒2豎直貫通設置於坩堝1內。
如圖1所示,數字流體發生器3設置於坩堝1的下方且其進料口與坩堝1的出料口連接,數字流體發生器3內設有數字流體導流管10,數字流體導流管的底部設有噴嘴4。
如圖1至圖2所示,成型模塊包括工作檯7、基材8和模具體9,模具體9設有成型內腔12,模具體9內且位於成型內腔12的周向設有小擋板13,基材8套設於模具體上,基材8上設形態定位銷軸5、擋板定位銷軸、彈簧14和連接銷軸15,形態定位銷軸5均勻分布於成型內腔12周向,擋板定位銷軸設置於小擋板13的兩側,連接銷軸15連接設置於彈簧14上且設置於小擋板13的外側。
擋板定位銷軸包括第一擋板銷軸16和第二擋板銷軸17,第一擋板銷軸16和第二擋板銷軸17設置於小擋板13的兩側;形態定位銷軸5包括第一定位銷軸18、第二定位銷軸19、第三定位銷軸20、第四定位銷軸21、第五定位銷軸22、第六定位銷軸23、第七定位銷軸24,是nurbs曲線形態控制的定位點,各點的位置隨著模型不同截面的變化而變化。
模具成型是通過計算機控制模塊獲得模型外輪廓,並控制成型模塊形成同樣的外輪廓,在形成後,模具可能會出現缺口,該缺口是由於「纖維布」的截面周長要比模型輪廓的周長要長,所以成型模具在形成外輪廓後,會多出一部分「纖維布」,該模具缺口很微小,通過固定小擋板可以消除模具缺口。
坩堝1裝有一定體積的熔體11,計算機控制模塊驅動數字流體發生器3霧化產生金屬液滴,通過數字流體導流管10及噴嘴4向成型內腔中噴射霧化液滴,最終固化成型。在樣件成型的過程中,當某一截面噴射完成後,工作檯7在計算機的控制下向下移動某一距離,然後成型模塊的「纖維布」的周長會自適應調整,噴嘴4會噴射金屬液滴,繼續下一個截面的成型工藝。這種模具隨實體的逐步堆積動態調整水平截面外輪廓形態,其調整的原理是基於nurbs曲線形態控制的。
如圖4所示,本實施方式還提供一種3d噴射列印方法,包括以下步驟:
s1、創建3d噴射列印所需要的三維模型;
s2、根據步驟s1中獲得的三維模型的提取模型輪廓數據;
s3、根據步驟s2中獲得的模型輪廓數據設計噴射路徑;
s4、驅動數字流體發生器霧化產生一定尺寸的液滴,並根據步驟s3中的噴射路徑控制數字流體發生器向成型模塊的成型內腔內噴射;
s5、完成零件成型。
為了進一步地優化本發明的實施效果,在本發明的另一種實施方式中,在前述內容的基礎上,步驟s1中通過計算機建模軟體建立三維模型或通過多維度掃描三維物體獲得三維模型。
為了進一步地優化本發明的實施效果,在本發明的另一種實施方式中,在前述內容的基礎上,噴射路徑為計算機軟體計算模擬噴射路徑或自主設計模擬噴射路徑。
以上所述的僅是本發明的優選實施方式,應當指出,對於本領域的普通技術人員來說,在不脫離本發明創造構思的前提下,還可以做出若干變形和改進,這些都屬於本發明的保護範圍。