一種活性炭吸收塔及氣體淨化裝置的製作方法
2023-09-23 00:47:10 2
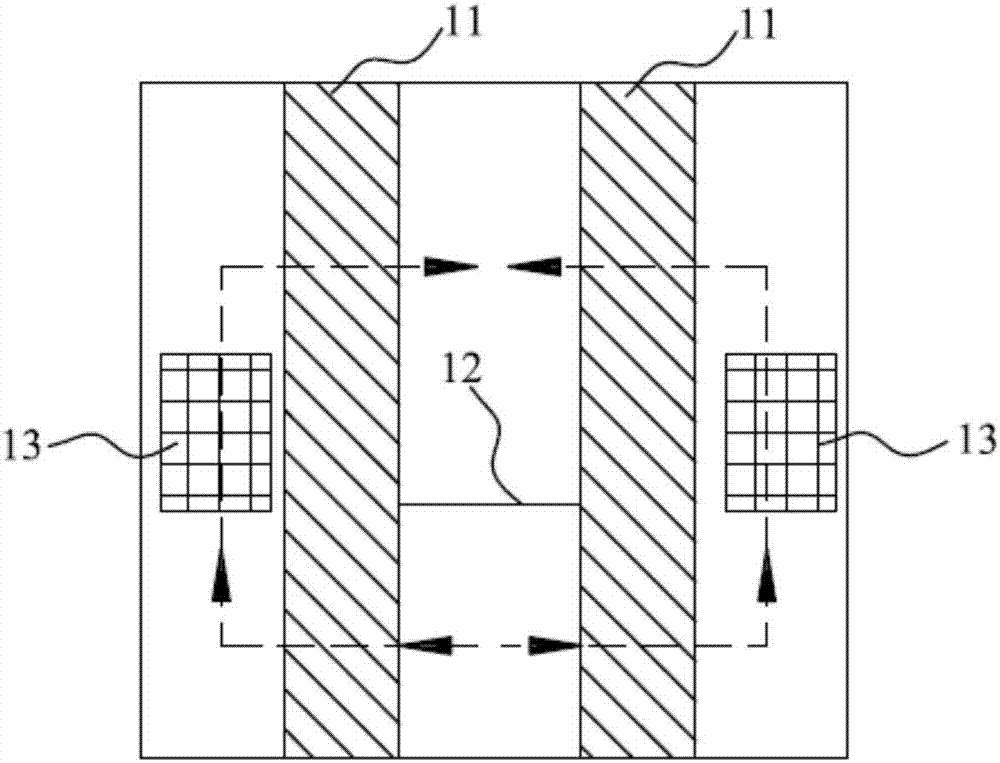
本發明涉及氣體淨化技術領域,尤其涉及一種活性炭吸收塔及氣體淨化裝置。
背景技術:
活性炭法脫除煙氣中汙染物技術作為一種固相吸附脫除技術,可實現一體化脫除so2、nox、有機物、重金屬和粉塵;脫硫率可達95%以上,脫硝率可達80%以上,通過吸附劑再生回收了硫資源,極大限度的控制了汙染物的排放,且無其他廢棄物產生,降低了二次汙染,同時一體化的工藝還縮短了工業流程。
活性炭吸收塔是整個淨化工藝的核心設備,在吸收塔上應用較多的是固定床和移動床。固定床由於間歇式的操作方式因而不能適用大煙氣量的工況,移動床可連續運行、適合各種工況,在工業上得到了廣泛的應用。按照煙氣和活性炭的運動方向,移動床可分為錯流式和逆流式,錯流式中氣體和固體的流路分離,便於氣固相分離處理,其氣固接觸面積大、處理氣量大、結構較簡潔且活動部件少維護方便。
專利號為jp2001038141a的日本專利「活性炭系吸收塔」中公開了一種錯流式移動床活性炭廢氣吸收塔,其特徵是塔內分布的若干出氣支管與吸收塔出氣口相連,且出氣支管的四周均由活性炭層包裹,這樣的設計儘可能增大了與煙氣的接觸面積,使流動的活性炭吸附劑層整體得到有效的利用。但該專利公布的吸收塔工藝複雜,氣流場分布也不均勻,阻力較大。
專利號為jp2942567b2的日本專利「圓筒形移動床氣體處理裝置及其廢氣脫硝脫硫裝置」中公開了一種錯流式圓通形移動床脫硫脫硝裝置,其特徵是同心的內外筒組成垂直雙重圓筒,在內外筒之間設置了多組長方形的活性炭移動層,煙氣在內外筒之間與活性炭接觸得以淨化,該裝置佔地面較小,處理氣量大,但是其結構複雜,製造成本高。
專利號為jp1994170164a的日本專利「活性炭脫硝裝置」中公開了一種錯流移動床脫硝裝置,其特徵是脫硫脫硝一體化布置,裝置先用石灰石法脫除so2,再通過噴氨氣或氨水用活性炭脫除nox,其脫硝效率較高,但工藝是兩種方法疊加而成,非真正意義上的一體化脫除技術。
目前採用交錯式移動床的活性炭吸收塔普遍具有活性炭利用率低,雜質的脫除效率低,且吸收塔的機構複雜,氣體流動阻力大等問題。
技術實現要素:
本發明的第一目的在於提出一種活性炭吸收塔,氣體與活性炭多次接觸,提高活性炭的利用率,且活性炭吸收塔的結構簡單,氣體的流動阻力小,可以顯著提高脫硫、脫硝效率。
為達此目的,本發明採用以下技術方案:
一種活性炭吸收塔,包括吸收塔主體、設置於所述吸收塔主體的進氣口和出氣口,所述吸收塔主體內設置有活性炭通道、隔擋板以及連通所述進氣口和所述出氣口的氣流通道,所述氣流通道被所述隔擋板分隔成u型或蛇形,且所述氣流通道分別從相反的方向穿過同一所述活性炭通道至少一次,所述活性炭通道內設置有流動的活性炭,所述活性炭通道的通道壁上開設有用於連通兩側的所述氣流通道的氣孔。
其中,所述氣流通道為多個,每個所述氣流通道均與至少一個所述活性炭通道對應,且分別從相反的方向穿過對應的所述活性炭通道至少一次。
其中,所述氣流通道中氣體首次經過所述活性炭通道後流入的區域設置有噴氨格柵。
其中,所述活性炭通道將所述吸收塔主體分隔成兩部分,所述隔擋板位於所述活性炭通道與所述吸收塔主體的內壁之間,將所述氣流通道為分隔形成所述u型通道,所述進氣口和所述出氣口位於所述活性炭通道的同一側且分別位於所述隔擋板的兩側。
其中,所述隔擋板和所述活性炭通道的接觸點分別到所述活性炭通道的兩端的距離的比例為1:1~1:4。
其中,所述活性炭通道的兩側分別到同側的所述吸收塔主體的內壁之間的距離的比例為4:1~1:1。
其中,所述活性炭通道內沿所述活性炭通道設置有將所述活性炭通道分為多層的有氣孔的隔板或網狀隔板。
其中,每層所述活性炭通道的兩端均設置有活性炭料倉以及開關閥,每層所述活性炭通道的下端還設置有控制器,所述控制器控制所述活性炭的流動速度。
其中,所述進氣口內設置有導流板,所述氣流通道內設置有氣流均布器。
本發明的第二目的在於提出一種氣體淨化裝置,該裝置中的活性炭吸收塔中氣體與活性炭多次接觸,提高活性炭的利用率,且活性炭吸收塔的結構簡單,氣體的流動阻力小,可以顯著提高脫硫、脫硝效率。
為達此目的,本發明採用以下技術方案:
一種氣體淨化裝置,包括上述的活性炭吸收塔。
有益效果:本發明提供了一種活性炭吸收塔及氣體淨化裝置。活性炭吸收塔包括吸收塔主體、設置於所述吸收塔主體的進氣口和出氣口,所述吸收塔主體內設置有活性炭通道、隔擋板以及連通所述進氣口和所述出氣口的氣流通道,所述氣流通道被所述隔擋板分隔成u型或蛇形,且所述氣流通道分別從相反的方向穿過同一所述活性炭通道至少一次,所述活性炭通道內設置有流動的活性炭,所述活性炭通道的通道壁上開設有用於連通兩側的所述氣流通道的氣孔。通過u型或蛇形的氣流通道,使氣體多次穿過活性炭,提高活性炭的利用率,且活性炭吸收塔的結構簡單,氣體的流動阻力小,可以顯著提高脫硫、脫硝效率。
附圖說明
圖1是本發明實施例1提供的一種活性炭吸收塔的內部結構示意圖;
圖2是本發明實施例1提供的另一種活性炭吸收塔的內部結構示意圖;
圖3是本發明實施例1提供的另一種活性炭吸收塔的結構示意圖;
圖4是本發明實施例2提供的活性炭吸收塔的內部結構示意圖;
圖5是本發明實施例3提供的一種活性炭吸收塔的內部結構示意圖;
圖6是本發明實施例3提供的另一種活性炭吸收塔的內部結構示意圖;
其中:
1、吸收塔主體;11、活性炭通道;12、隔擋板;13、噴氨格柵;2、進氣口;3、出氣口;4、活性炭料倉。
具體實施方式
為使本發明解決的技術問題、採用的技術方案和達到的技術效果更加清楚,下面結合附圖並通過具體實施方式來進一步說明本發明的技術方案。
實施例1
本實施例提供了一種活性炭吸收塔,如圖1-圖3所示,包括吸收塔主體1、設置於吸收塔主體1的進氣口2和出氣口3,吸收塔主體1內設置有活性炭通道11、隔擋板12以及連通進氣口2和出氣口3的氣流通道,氣流通道被隔擋板12分隔成u型,且氣流通道分別從相反的方向穿過同一活性炭通道11至少一次,活性炭通道11內設置有流動的活性炭,活性炭通道11的通道壁上開設有用於連通兩側的氣流通道的氣孔。
本實施例中的活性炭吸收塔採用的是錯流式移動床吸附工藝,相對於現有技術,本實施例中的活性炭吸收塔的氣流通道為u型,如圖1所示,氣體在氣流通道中的流動採取的是折返式流動方式,即氣體分別從相反的方向穿過同一活性炭通道11,增加了活性炭的吸附次數,使氣體和活性炭充分接觸,提高活性炭的利用率,並且活性炭吸收塔的結構簡單,氣體流動阻力小,可顯著提高脫硫和脫硝的效率。
一般採用活性炭吸附方法吸收的氣體內的雜質為so2等硫化物以及nox,硫化物在氣體通過活性炭通道11時被活性炭吸附,nox需要與氨氣混合之後通過活性炭吸附。具體而言,活性炭通道11將吸收塔主體1分隔成兩部分,隔擋板12位於活性炭通道11與吸收塔主體1的內壁之間,將氣流通道為分隔形成u型通道,進氣口2和出氣口3位於活性炭通道11的同一側且分別位於隔擋板12的兩側。氣體從進氣口2流入氣流通道後,通過活性炭通道11的通道壁上開設的氣孔與活性炭接觸,活性炭吸附氣體內的so2等硫化物,之後與氣流通道內設置的噴氨格柵13噴出的氨氣混合均勻後,再次通過活性炭通道11,達到脫硝的效果。本實施例中氣流通道中氣體首次經過活性炭通道11後流入的區域內設置有噴氨格柵13,使氣體在通過一次活性炭通道11後吸收氣體內的硫化物,降低氣體內硫化物的濃度,方便噴氨格柵13噴出的氨氣與氣體內的nox充分混合反應,提高氨氣利用率以及脫硝效率,提高活性炭吸收塔的經濟效益。
本實施例中與進氣口2相對的部分活性炭通道11主要吸收氣體內的so2等硫化物,氣體經過一次活性炭之後與氨氣混合均勻,再次經過的活性炭通道11的部分主要吸收氣體中的氮氧化物,從而達到一體式脫硫、脫硝的效果。本實施例中的隔擋板12和活性炭通道11的接觸點分別到活性炭通道11的兩端的距離的比例可以為1:1~1:4,活性炭通道11的兩側分別到同側的吸收塔主體1的內壁之間的距離的比例可以為4:1~1:1。與進氣口相對的部分活性炭通道內的活性炭主要起到吸附氣體內硫化物的作用,氣體與氨氣混合後再次通過活性炭通道主要是為了吸收氣體內氮氧化物,因此上述比例是在綜合考慮氣體內不同的雜質的濃度比例確定的,可以在實際使用時根據待淨化氣體內硫化物或氮氧化物的濃度來調整,合理利用活性炭及氨氣等資源。
如圖2-圖3所示,本實施例中的氣流通道可以為多個,每個氣流通道均與至少一個活性炭通道11對應,且分別從相反的方向穿過對應的活性炭通道11至少一次。如圖2所示,兩個u型氣流通道的開口相對設置,進氣口2位於兩個活性炭通道11之間,氣體從進氣口2流入氣流通道後,分別穿過兩側的活性炭通道11,與氨氣混合後反方向再次穿過活性炭通道11與出氣口3相對的部分,之後經出氣口3流出。增加氣流通道可以提高活性炭吸收塔的一次性淨化的氣體容量,提高脫硫、脫硝效率。
為平衡氣體內so2等硫化物以及nox的濃度以及活性炭通道11內的活性炭利用率,活性炭佔吸收塔主體1內的空間比例在25%~63%之間比較適合,若活性炭佔吸收塔主體1內的空間過大,氣體的流入量較小,相對的帶吸附的so2等硫化物以及nox較少,並且活性炭在活性炭通道11內實時流動,會導致活性炭吸附飽和度較低,利用不充分,造成資源浪費;相反若活性炭的比例較小,而氣體的流入量較大,則會導致氣體內的so2等硫化物以及nox吸收不徹底。
活性炭通道11的厚度可以為0.8~2.5m,具體值可以根據實際使用時氣體內so2等硫化物以及nox的濃度以及活性炭流動速度等進行調整,使其在合理利用活性炭資源的前提下,提高脫硫率和脫硝率。
由於活性炭通道11內的活性炭是流動的,因此活性炭通道11的兩端還設置有活性炭料倉4以及開關閥,活性炭料倉4與活性炭通道11連通,開關閥控制活性炭流出或流入活性炭料倉4,並且開關閥的閥片邊緣可以由耐高溫的軟質材料製成,如摻雜金屬的石棉材料等,增加開關閥的密封性,耐高溫材料可以防止活性炭吸收塔內氣體與氨氣反應時溫度升高使閥片變形,避免在更換活性炭時汙染氣體洩漏。活性炭通道11的下端還設置有控制器,控制器可以控制活性炭通道11內活性炭的流動速度,活性炭的流動速度可以根據實際氣體中待吸附的物質的濃度及吸附速度進行調整。
為使活性炭吸收塔內的氣體分布均勻,進氣口2處還設置有導流板,引導氣體流入氣流通道,氣流通道內還設置有氣流均布器,使活性炭吸收塔內的氣體分布均勻,提高脫硫、脫硝效率。
本實施例中的活性炭吸收塔的結構簡單,氣體流動阻力較小,且活性炭通道11內活性炭流動順暢,一般氣體在活性炭內的停留時間為3~25s,顯著提高了脫硫、脫硝效率。
實施例2
與實施例1不同的是,本實施例中的隔擋板12將活性炭吸收塔內的氣流通道隔成蛇形,即類似s形蜿蜒折返的形式,如圖4所示,活性炭通道11兩側分別設置有一個隔擋板12,進氣口2和出氣口3分別位於活性炭通道11的兩側,且位於出氣口3一側的隔擋板12的位置高於位於進氣口2一側的隔擋板12的位置,氣體經進氣口2流入後穿過活性炭通道11,並與氨氣混合,之後兩次穿過活性炭通道11後經出氣口3流出,增加了活性炭的吸附次數,使氣體和活性炭充分接觸,提高活性炭的利用率,並且活性炭吸收塔的結構簡單,氣體流動阻力小,可顯著提高脫硫和脫硝的效率。
本實施例中的氣流通道也可以為多個,每個氣流通道均與至少一個活性炭通道11對應,且分別從相反的方向穿過對應的活性炭通道11至少一次。增加氣流通道可以提高活性炭吸收塔的一次性淨化的氣體容量,提高脫硫、脫硝效率。
實施例3
在上述實施例的基礎上,如圖5和圖6所示,活性炭通道11內沿活性炭通道11設置有將活性炭通道11分為多層的有氣孔的隔板或網狀隔板。每層活性炭的流動速度可以相同,也可以不同,其具體的流動速度可以根據活性炭吸附so2等硫化物以及nox速度確定,不同的物質吸附速度不一致,吸附速度比較慢時,活性炭的流動速度應較慢,以使活性炭有足夠的時間吸附,避免活性炭吸附濃度較低,造成活性炭浪費;當物質吸附速度快時,活性炭的流動速度若較慢,會造成活性炭中某一物質的濃度飽和,導致氣體淨化不徹底。
每層活性炭通道11的兩端可以共用一個活性炭料倉4,活性炭料倉4通過管道分別於每層活性炭通道11的兩端連通,也可以每層活性炭通道11分別設置一個活性炭料倉4,只要滿足管道的密封性,防止氣體洩漏即可。每層活性炭通道11的兩端均設置有開關閥,開關閥控制每層活性炭流出或流入活性炭料倉4,避免在更換活性炭或活性炭流入或流出時汙染氣體洩漏。每層活性炭通道11的下端分別設置有控制器,控制器可以控制活性炭通道11內活性炭的流動速度。活性炭的流動速度可以根據實際氣體中待吸附的物質的濃度及吸附速度進行調整。
當活性炭通道11內通過帶氣孔的隔板或是網狀隔板分為兩層時,兩層活性炭的厚度比可以為1:10~1:1;當活性炭通道11被分為三層時,每層活性炭的厚度比可以為1:10:15~1:1:1,其具體的比例可以根據實際通入的氣體中某一帶吸收物質的濃度來確定。
實施例4
本實施例提供了一種氣體淨化裝置,包括上述實施例中的的活性炭吸收塔。該活性炭吸收塔的氣流通道為u型或蛇形,氣體在氣流通道中的流動採取的是折流方式,即氣體分別從相反的方向穿過同一活性炭通道11至少一次,增加了活性炭的吸附次數,使氣體和活性炭充分接觸,提高活性炭的利用率,並且活性炭吸收塔的結構簡單,氣體流動阻力小,可顯著提高脫硫和脫硝的效率。
以上內容僅為本發明的較佳實施例,對於本領域的普通技術人員,依據本發明的思想,在具體實施方式及應用範圍上均會有改變之處,本說明書內容不應理解為對本發明的限制。