一種助力轉向電機殼體的專機裝置及其加工方法與流程
2023-09-23 22:52:20 4
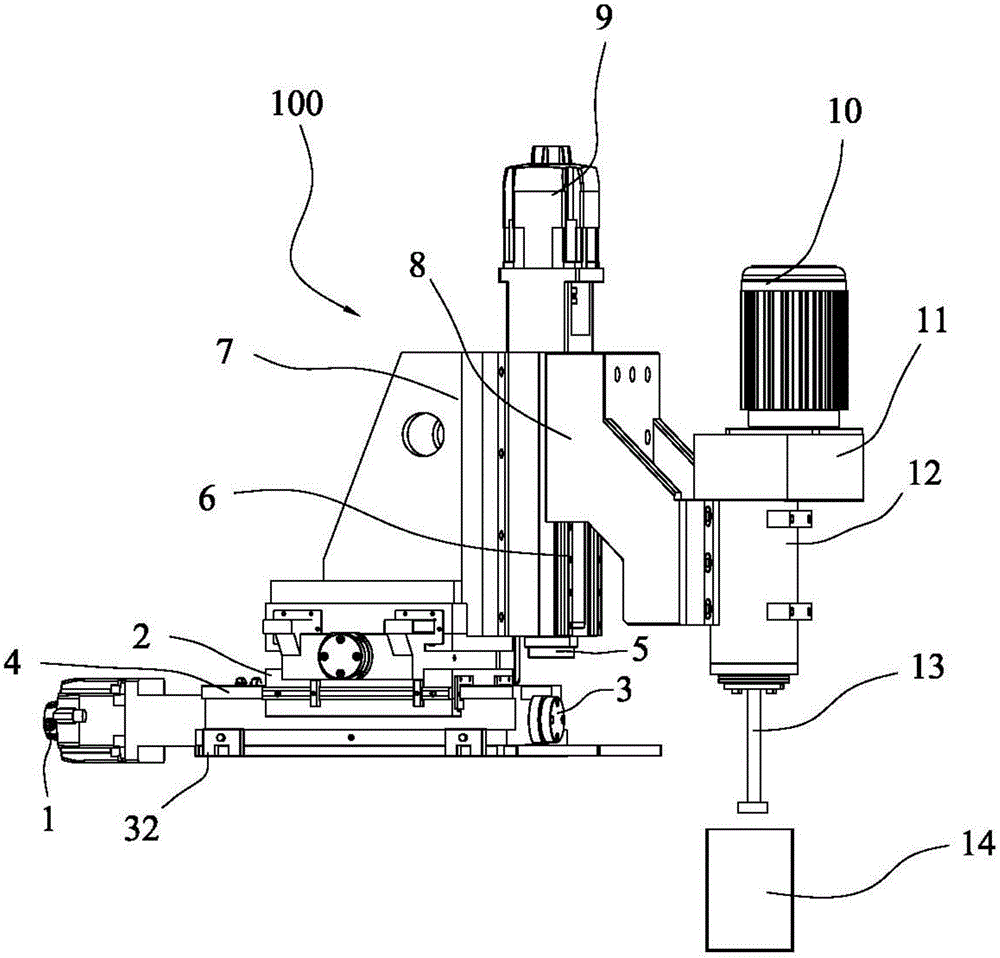
本發明屬於機械加工工具機技術領域,尤其涉及一種助力轉向電機殼體的專機裝置及其加工方法。
背景技術:
伴隨各種設備零部件的製造精度要求的日益提升,快速裝夾、多工位、多工序、以及低成本的機械加工手段已成為企業具備高競爭力的重要特性。
電動助力轉向系統(Electric Power Steering,縮寫EPS)是一種直接依靠電機提供輔助扭矩的動力轉向系統,與傳統的液壓助力轉向系統HPS(Hydraulic Power Steering)相比,EPS系統具有很多優點。EPS主要由扭矩傳感器、車速傳感器、電動機、減速機構和電子控制單元(ECU)等組成。
技術實現要素:
本發明的目的在於提供一種節約製造成本、提高產品的過程能力、改善產品質量的助力轉向電機殼體的專機裝置及其加工方法。
本發明提供一種助力轉向電機殼體的專機裝置,其包括:基座、設置在該基座上按順時針方向設置的9個工序、以及位於相鄰兩個工序之間的操作位置,其中,9個工序分別為:第一工序、第二工序、第三工序、第四工序、第五工序、第六工序、第七工序、第八工序、以及第九工序,所述操作位置位於第一工序和第九工序之間;其中,第一工序、第二工序和第三工序均設有下工位加工、中工位加工和上工位加工,第四工序、第五工序、第六工序、第七工序、第八工序和第九工序均設有下工位加工和上工位加工。
優選地,還包括與所述基座平行設置的中層基座、支撐該基座和中層基座的基板支撐柱、固定在中層基座上的轉塔、固定在該基座上且用於支撐轉塔的轉塔基座、以及位於中層基座上的工裝夾具,產品由所述工裝夾具夾緊,在某一工序上加工完成的產品由所述轉塔輸送至相鄰下一工序進行加工。
優選地,還包括位於對產品進行下工位加工的下工位、對產品進行上工位加工的上工位、以及對產品進行中工位加工的中工位;在第一工序、第二工序和第三工序中,下工位固定在基座上,中工位固定在下工位上,上工位固定在中層基座上;在第四工序、第五工序、第六工序、第七工序、第八工序和第九工序中,下工位固定在基座上,上工位固定在中層基座上。
優選地,所述上工位包括:固定在所述中層基座上的上工位墊板、第一異步電機、與該第一異步電機連接的第一齒輪變速箱,與該第一齒輪變速箱連接的第一動力頭、以及與該第一動力頭連接的上工位刀具,產品與該上工位刀具相對設置。
優選地,所述上工位還包括:安裝在所述上工位墊板上的上工位橫嚮導軌、安裝在該上工位橫嚮導軌上的上工位橫向滑座、與該上工位橫向滑座連接的上工位橫向絲軸、與該上工位橫向絲軸連接的第三伺服電機、與該上工位橫向滑座安裝的上工位導向基座、與該上工位導向基座安裝的上工位縱嚮導軌、與該上工位縱嚮導軌安裝的上工位縱向滑座、與該上工位縱向滑座連接的上工位縱向絲軸、與該上工位縱向絲軸連接的第一伺服電機;其中,所述第一動力頭安裝於所述上工位縱向滑座上。
優選地,所述中工位包括:第二伺服電機、第四伺服電機、中工位導軌、中工位滑座、中工位安裝基座、第二動力頭、以及中工位刀具;其中,所述中工位安裝基座安裝於所述下工位上;中工位滑座安裝於中工位導軌上;第四伺服電機與中工位滑座連接;第二伺服電機與第二動力頭連接;中工位刀具安裝於第二動力頭上。
優選地,所述下工位包括:固定在基座上的下工位墊板、第二異步電機、第五伺服電機、第六伺服電機、下工位滑座、第一下工位導軌基座、第二下工位導軌基座、第三動力頭、下工位導軌、第二齒輪變速箱31、以及下工位刀具,其中,第一下工位導軌基座安裝於下工位墊板上;第二下工位導軌基座安裝於第一下工位導軌基座上;第五伺服電機與第一下工位導軌基座連接;第一下工位導軌基座與下工位導軌連接;第六伺服電機與下工位導軌;第三動力頭安裝於下工位滑座上;第二齒輪變速箱安裝連接與第三動力頭上;第二異步電機與第二齒輪變速箱連接安裝;下工位刀具安裝於第三動力頭上。
優選地,所述中工位安裝基座安裝於所述下工位的下工位導軌上。
本發明還提供一種加工方法,包括如下步驟:
第一步:操作人員站在操作位置;
第二步:產品依次放入各個工序,產品經工裝夾具夾緊;
第三步:產品抵達第一工序的位置;
第三步,具體如下步驟:
A、下工位的第五伺服電機驅動下工位滑座移動至設定坐標,此時,第二異步電機啟動,通過第二齒輪變速箱傳遞一定轉速至第二動力頭,下工位刀具加工產品內腔;
B、中工位的第四伺服電機使中工位滑座沿中工位導軌移動至設定坐標,第二伺服電機傳遞一定轉速至第二動力頭,中工位刀具加工產品側面;
C、上工位的第三伺服電機和第一伺服電機分別驅動上工位橫向滑座和上工位縱向滑座至設定坐標位置,第一異步電機輸入一定轉速至第一齒輪變速箱,第一齒輪變速箱輸出一定轉速至第一動力頭,第一動力頭帶動上工位刀具,上工位刀具加工產品上面;
第四步:至此完成第一工序的加工,磚塔轉動將第一工序的完成的產品送至第二工序位置,同時第九工序結束加工,成品出來。
優選地,所述第三步的每一工序的工位均為同時進行,即,以上A、B、C動作均同時進行。
本發明對加工薄壁鋁壓鑄產品製造過程的一次性能&效益的提升,本發明該具有節約製造成本、提高產品的過程能力、改善產品質量等3項技術優勢;本發明縮短產品CNC加工時間;提升成品的合格率;減少產品裝夾時間。
附圖說明
圖1為助力轉向電機殼體的專機裝置的結構示意圖;
圖2為圖1所示專機裝置的上工位的結構示意圖;
圖3為圖1所示專機裝置的中工位的結構示意圖;
圖4為圖1所示專機裝置的下工位的結構示意圖;
圖5為圖2至圖4所示上工位、中工位和下工位組裝的結構示意圖。
具體實施方式
下面結合附圖和實施例對本發明進行進一步說明。
本發明一種助力轉向電機殼體的專機裝置,為一種用於筒狀形狀的特殊產品所涉及的一款多工位、多主軸、多工序同步進行的高精度加工製造設備。本專機裝置與普通加工工具機相比,其在加工循環時間上能夠節省90%的工作時間,每班能夠連續產出4800pcs成品件。
薄壁產品指的是薄壁鋁壓鑄產品,如筒狀的電動助力轉向的電機殼體。
本發明屬於電腦數字控制(CNC)機械加工工具機/薄壁鋁壓鑄零部件加工製造工藝。
如圖1所示,本專機裝置包括基座51、設置在該基座51上按順時針方向設置的9個工序、以及位於相鄰兩個工序之間的操作位置43,其中,9個工序分別為:第一工序44、第二工序、第三工序、第四工序、第五工序、第六工序、第七工序、第八工序、以及第九工序42,操作位置43位於第一工序44和第九工序42之間。
第一工序44、第二工序和第三工序均設有下工位加工、中工位加工和上工位加工,第四工序、第五工序、第六工序、第七工序、第八工序和第九工序42均設有下工位加工和上工位加工。
其中,本專機裝置還包括位於對產品進行下工位加工的下工位300、對產品進行上工位加工的上工位100、以及對產品進行中工位加工的中工位200。
如圖2所示為上工位100的結構示意圖,上工位100包括:上工位墊板32、第一異步電機10、第一伺服電機9、第三伺服電機1、上工位橫向滑座2、上工位橫向絲軸3、上工位橫嚮導軌4、上工位縱向絲軸5、上工位縱嚮導軌6、上工位導向基座7、上工位縱向滑座8、第一齒輪變速箱11、第一動力頭12、以及上工位刀具13,筒狀的電機殼體14與上工位刀具13相對設置。
上工位100的各部件的連接方式為:上工位墊板32使用螺絲連接於中層基板35上;上工位橫嚮導軌4安裝於上工位墊板32上;上工位橫向滑座2安裝於上工位橫嚮導軌4上;第三伺服電機1與上工位橫向絲軸3連接,以用於驅動;上工位橫向絲軸3與上工位橫向滑座2連接,上工位橫向絲軸3傳動,驅動上工位橫向滑座2移動;上工位導向基座7安裝於上工位橫向滑座2上;上工位縱嚮導軌6安裝於上工位縱向基座7上;第一伺服電機9與上工位縱向絲軸5連接;上工位縱向滑座8安裝於上工位縱嚮導軌6上,上工位縱向滑座8在上工位縱嚮導軌6上滑動;上工位縱向絲軸5連接於上工位縱向滑座8的底部,用於傳動;第一動力頭12安裝於上工位縱向滑座8上;第一齒輪變速箱11安裝連接與第一動力頭12上;第一異步電機10與第一齒輪變速箱11連接安裝;上工位刀具13安裝於第一動力頭12上;電機殼體14在工裝夾具33上定位夾緊。
其中,上工位100用於加工電機殼體14上面。
如圖3所示為中工位200的結構示意圖,中工位200包括:第二伺服電機19、第四伺服電機18、中工位導軌17、中工位滑座16、中工位安裝基座15、第二動力頭20、以及中工位刀具21,電機殼體14與中工位刀具21相對設置。
中工位200的各部件的連接方式為:中工位安裝基座15安裝於下工位的下工位導軌28上;中工位滑座16安裝於中工位導軌17上;第四伺服電機18通過絲軸(圖未示)與中工位滑座16連接;第二伺服電機19與第二動力頭20連接安裝;中工位刀具21安裝於第二動力頭20上;電機殼體14在工裝夾具33上定位夾緊。
如圖4所示為下工位300的結構示意圖,下工位300包括:下工位墊板38、第二異步電機30、第五伺服電機24、第六伺服電機23、下工位滑座22、第一下工位導軌基座25、第二下工位導軌基座27、第三動力頭26、下工位導軌28、第二齒輪變速箱31、以及下工位刀具29,電機殼體14與下工位刀具29相對設置。
下工位300的各部件的連接方式為:下工位墊板38使用螺絲連接於基座51上;第一下工位導軌基座25安裝於下工位墊板38上;第二下工位導軌基座27安裝於第一下工位導軌基座25上;第五伺服電機24與第一下工位導軌基座25連接,驅動第一下工位導軌基座25移動;第一下工位導軌基座25與下工位導軌28連接;第六伺服電機23與下工位導軌28,驅動下工位導軌28移動;第三動力頭26安裝於下工位滑座22上;第二齒輪變速箱31安裝連接與第三動力頭26上;第二異步電機30與第二齒輪變速箱31連接安裝;下工位刀具29安裝於第三動力頭26上;電機殼體14在工裝夾具33上定位夾緊。
如圖5所示,本專機裝置還包括:基座51、與該基座51平行設置的中層基座35、支撐該基座51和中層基座35的基板支撐柱37、固定在中層基座35上的轉塔34、固定在該基座51上且用於支撐轉塔34的轉塔基座36、以及位於中層基座35上的工裝夾具33,電機殼體14由工裝夾具33夾緊,在某一工序上加工完成的產品由該轉塔34輸送至相鄰下一工序進行加工。
由於第一工序44、第二工序和第三工序均設有下工位加工、中工位加工和上工位加工,故在第一工序44、第二工序和第三工序中,下工位300固定在基座51上,中工位200固定在下工位300上,上工位100固定在中層基座35上,下工位300加工電機殼體14內腔,中工位200加工電極殼體14側面,上工位100加工電機殼體14上面。
由於第四工序、第五工序、第六工序、第七工序、第八工序和第九工序42均設有下工位加工和上工位加工,故在第四工序、第五工序、第六工序、第七工序、第八工序和第九工序42中,下工位300固定在基座51上,上工位100固定在中層基座35上,下工位300加工電機殼體14內腔,上工位100加工電機殼體14上面。
本發明加工方法,包括如下步驟:
第一步:操作人員站在操作位置43;
第二步:電機殼體14依次放入各個工序,電機殼體14經工裝夾具33夾緊;
第三步:電機殼體14抵達第一工序44的位置;
第三步,具體如下步驟:
A、下工位的第五伺服電機24驅動下工位滑座22移動至設定坐標,此時,第二異步電機30啟動,通過第二齒輪變速箱31傳遞一定轉速至第二動力頭26,下工位刀具29加工電機殼體14內腔;
B、中工位的第四伺服電機18驅動絲軸使中工位滑座16沿中工位導軌17移動至設定坐標,第二伺服電機19傳遞一定轉速至第二動力頭20,中工位刀具21加工電極殼體14側面;
C、上工位的第三伺服電機1和第一伺服電機9分別驅動上工位橫向滑座2和上工位縱向滑座8至設定坐標位置,第一異步電機10輸入一定轉速至第一齒輪變速箱11,第一齒輪變速箱11輸出一定轉速至第一動力頭12,第一動力頭12帶動上工位刀具13,上工位刀具13加工電機殼體14上面;
每一工序的工位均為同時進行,即,以上A、B、C動作均同時進行。
第四步:至此完成第一工序的加工,磚塔34轉動將第一工序的完成的產品送至第二工序位置,同時第九工序結束加工,成品出來。
經過第一工序至第九工序完成一件成品件的加工。
本發明對加工薄壁鋁壓鑄產品製造過程的一次性能&效益的提升,本發明該具有節約製造成本、提高產品的過程能力、改善產品質量等3項技術優勢;本發明縮短產品CNC加工時間;提升成品的合格率;減少產品裝夾時間。
以上詳細描述了本發明的優選實施方式,但是本發明並不限於上述實施方式中的具體細節,在本發明的技術構思範圍內,可以對本發明的技術方案進行多種等同變換,這些等同變換均屬於本發明的保護範圍。