一種提高光纖水聽器一致性的光纖繞制方法及模具與流程
2023-10-18 06:46:49 4
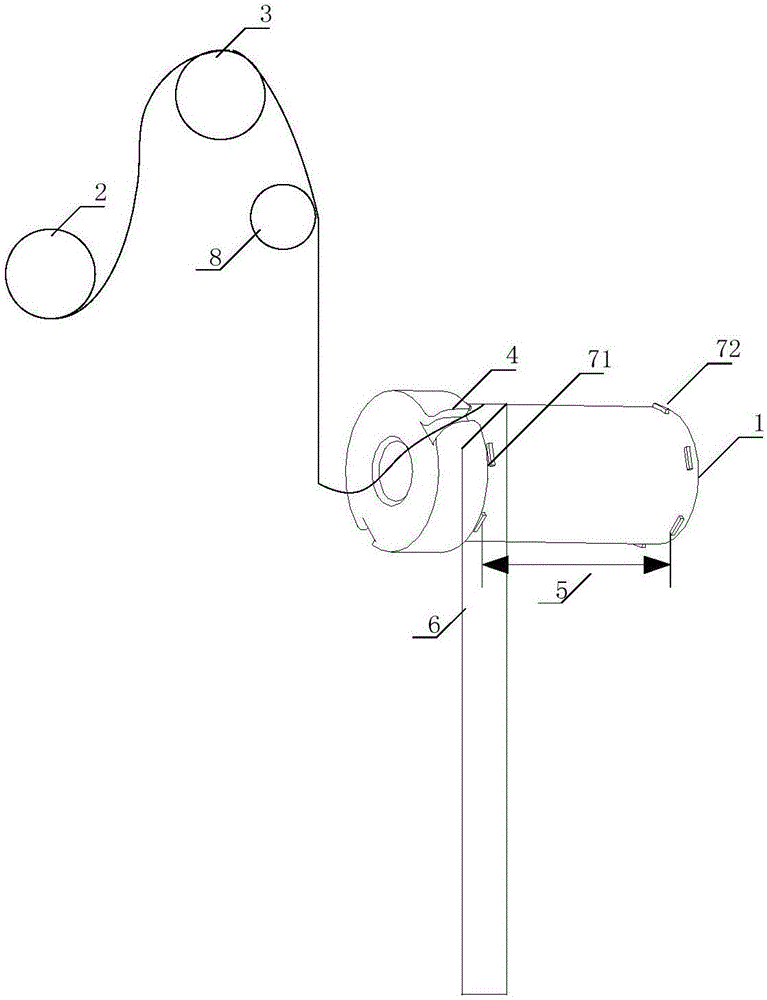
本發明涉及光纖傳感領域,尤其涉及一種提高光纖水聽器一致性的光纖繞制方法及模具。
背景技術:
基於光纖傳感原理的光纖水聽器作為一種新型水聲探測器件,與傳統的壓電水聽器相比,具有靈敏度高、頻響特性好、頻帶寬、「溼端」全光、抗電磁幹擾、傳輸距離遠以及便於大規模復用等優點,是現代聲納的一個重要發展方向。幹涉型光纖水聽器通過水下聲波對光纖的應力作用改變光纖纖芯的折射率或長度,從而引起在光纖中傳播光束的光程改變,導致相位發生變化,並得到有關水聲信息。因此,光纖環是光纖水聽器核心器件之一,它的穩定性直接影響光纖水聽器的性能,光纖環繞制的好壞對光纖水聽器頻響一致性有著很大的影響,光纖環的繞制技術是光纖水聽器的關鍵技術之一。光纖環的繞制是把一段完整的光纖通過膠粘劑繞在固定的彈性臂骨架上,這其中光纖的排布,張力的選取,塗膠的均勻性等都將成為影響光纖環因素的重要技術環節。在傳統的繞纖過程中,光纖排布間隙可能不盡相同,並且張力的選取也沒有明確的依據,塗膠過程中利用一直刷子將光纖表面塗均勻,然後將多餘的膠擦去,這種方式存在弊端:1.光纖如果排列不緊密,會導致繞第二層光纖時,存在搭纖的現象,導致整個光纖環上的光纖高低不平2.張力過小不能保證光纖與彈性筒的緊密耦合,張力過大,光纖在繞制過程中會被損壞3.人為利用刷子除去多餘的膠液時,由於不能保證膠液除去乾淨,造成光纖環表面不平整;4.只能將光纖繞制層表面的膠液去掉,不能將繞制層下面的多餘的膠液去掉,從而造成膠液堆積;5.工作時存在掉毛的風險,使光纖環內殘留雜物。
光纖水聽器是通過光纖環中光纖長度的變化來獲取聲信息的,經上述分析,按照傳統製作光纖環的方法會導致光纖水聽器獲取聲信息的能力不均勻,不穩定,導致整個水聽器頻響一致性的降低。
技術實現要素:
本發明解決的技術問題是:相比於現有技術,提供了一種提高光纖水聽器一致性的光纖繞制方法,使得光纖環上的光纖排列緊密,並且光纖的外表面塗膠均勻。
本發明目的通過以下技術方案予以實現:根據本發明一個方面,提供了一種提高光纖水聽器一致性的光纖繞制方法,所述方法包括以下步驟:
步驟一:測量光纖環的橫截面的直徑,根據所述直徑得出橫截面的周長,設定所繞光纖的匝數,根據橫截面的周長和所繞光纖的匝數得出所繞光纖的長度;
步驟二:根據光纖環的彈性壁壁厚和光纖長度確定光纖繞制張力;
步驟三:從載纖盤導出的具有步驟二中的光纖繞制張力的光纖繞於導纖輪,並通過導纖輪的導向經過進膠輪使得光纖的外表面塗覆有膠,然後進入光纖環芯軸的進纖槽;
步驟四:將進纖槽的光纖引入到彈性壁一端設置的第一卡槽的槽內,轉動光纖環,光纖從彈性壁的一端向彈性壁的另一端並排繞設於彈性壁的光纖繞制區的外表面,形成第一光纖層,然後光纖經過彈性壁另一端設置的第二卡槽的槽繼續從彈性壁的另一端並排繞回到彈性壁的一端,依次循環纏繞,直到設定光纖的匝數繞完為止。
上述提高光纖水聽器一致性的光纖繞制方法中,在所述步驟二中,根據光纖環的彈性壁壁厚和光纖長度採用L4(3)正交試驗方法確定光纖繞制張力。
上述提高光纖水聽器一致性的光纖繞制方法中,在所述步驟三中,經過進膠輪後的光纖的外表面塗覆膠的厚度為0.5mm-1mm。
上述提高光纖水聽器一致性的光纖繞制方法中,在所述步驟三中,所述膠為紫外膠。
上述提高光纖水聽器一致性的光纖繞制方法中,在所述步驟四中,利用玻璃棒的一端將光纖引入到第一卡槽的槽內。
上述提高光纖水聽器一致性的光纖繞制方法中,在所述步驟四中,在光纖纏繞的過程中,玻璃棒的表面與正在纏繞的光纖相接觸。
上述提高光纖水聽器一致性的光纖繞制方法中,在所述步驟四中,在所述步驟四中,使用CCD觀測光纖的纏繞過程。
上述提高光纖水聽器一致性的光纖繞制方法中,在所述步驟四中,所述第一卡槽的數量為若干個,若干個第一卡槽沿著彈性壁一端的周向均勻分布。
上述提高光纖水聽器一致性的光纖繞制方法中,在所述步驟四中,所述第二卡槽的數量為若干個,若干個第二卡槽沿著彈性壁另一端的周向均勻分布。
根據本發明另一個方面,還提供了一種提高光纖水聽器一致性的光纖繞制模具,所述模具包括:光纖環、載纖盤、導纖輪和進膠輪;其中所述光纖環包括光纖環芯軸和彈性壁,其中,所述彈性壁套設於所述光纖環芯軸;所述光纖環芯軸的一端開設有進纖槽;所述彈性壁的一端設置有第一卡槽,第一卡槽的長度方向與彈性壁的軸向垂直;所述彈性壁的另一端設置有第二卡槽,第二卡槽的長度方向與彈性壁的軸向垂直。
上述提高光纖水聽器一致性的光纖繞制模具中,所述第一卡槽的數量為若干個,若干個第一卡槽沿著彈性壁一端的周向均勻分布;所述第二卡槽的數量為若干個,若干個第二卡槽沿著彈性壁另一端的周向均勻分布。
本發明與現有技術相比具有如下有益效果:
(1)本發明有效的控制了光纖環上光纖間隙的問題,既能滿足光纖緊密貼合,又不會出現搭線的現象;
(2)本發明有效的解決了由於機械加工精度及其它因素,每層繞纖開始時光纖與彈性壁緊密貼合較困難造成兩端的光纖高於其他部位的光纖的問題;
(3)本發明利用正交實驗的方法,選取彈性筒壁厚、光纖繞制張力、傳感光纖長度3個因素,採用L4(3)正交試驗確定合理張力,既保證了光纖與彈性壁的緊密耦合,又防止了製作過程中光纖張力過大容易損壞的問題;
(4)本發明解決了傳統的人為塗膠存在各種缺點:人為利用刷子除去多餘的膠液時,不能保證膠液除去乾淨,造成光纖環表面不平整,並且刷子掉毛的風險,使光纖環內殘留雜物;只能將光纖繞制層表面的膠液去掉,不能將繞制層下面的多餘的膠液去掉,從而造成膠液堆積。
附圖說明
圖1示出了本發明實施例提供的提高光纖水聽器一致性的光纖繞制方法的示意圖;
圖2示出了本發明實施例提供的光纖環的結構示意圖。
具體實施方式
下面結合附圖對本發明作進一步詳細說明:
圖1示出了本發明實施例提供的提高光纖水聽器一致性的光纖繞制方法的示意圖。提高光纖水聽器一致性的光纖繞制方法包括以下步驟:
步驟一:測量光纖環1的橫截面的直徑,根據所述直徑得出橫截面的周長,設定所繞光纖的匝數,根據橫截面的周長和所繞光纖的匝數得出所繞光纖的長度;
步驟二:根據光纖環1的彈性壁12壁厚和光纖長度確定光纖繞制張力;
步驟三:從載纖盤2導出的具有步驟二中的光纖繞制張力的光纖繞於導纖輪3,並通過導纖輪3的導向經過進膠輪8使得光纖的外表面塗覆有膠,然後進入光纖環芯軸11的進纖槽4;
步驟四:將進纖槽4的光纖引入到彈性壁12一端設置的第一卡槽71的槽內,轉動光纖環1,光纖從彈性壁12的一端向彈性壁12的另一端並排繞設於彈性壁12的光纖繞制區5的外表面,形成第一層光纖,然後光纖經過彈性壁12另一端設置的第二卡槽72的槽繼續從彈性壁12的另一端並排繞回到彈性壁12的一端,依次循環纏繞,直到設定光纖的匝數繞完為止。
在步驟一中,如圖1和2所示,光纖環1的橫截面為圓,用卡尺精確測量光纖環1的橫截面的直徑,計算出橫截面的周長,設定好光纖環1上所繞光纖的匝數,以此精確計算光纖環1上光纖的長度,從而保證每個光纖環1上所繞光纖的總長度一致。
在步驟二中,選取彈性壁12的壁厚、光纖繞制張力、光纖長度3個因素,採用L4(3)正交試驗方法確定合理的光纖繞制張力,既保證了光纖與彈性壁12的緊密耦合,又防止了製作過程中光纖張力過大容易損壞的問題。
在步驟三中,如圖1和圖2所示,從載纖盤2上緩慢抽出部分光纖,通過導纖輪3後,與光纖環1的軸向成垂直角度,緩慢旋轉載纖盤2使得光纖稍稍繃緊,然後到達進膠輪8,調整進膠輪8與光纖接觸面積,保證膠在光纖的外表面塗覆均勻,從而降低了後續的光纖環1由於膠量不均勻導致的應力。光纖經過進膠輪8後進入光纖環芯軸11的進纖槽4,通過進纖槽4能夠利於光纖纏繞,並且保持光纖的張力。
在步驟四中,如圖1和圖2所示,用玻璃棒6的一端緩慢撥起引入進纖槽4的光纖,將光纖引入第一卡槽71的槽內,使光纖與第一卡槽71緊密貼合,使光纖稍稍承力,避免光纖環1上的光纖過於鬆散導致排列不緊密;設定低轉速,使光纖環1非常緩慢的轉動,光纖從彈性壁12的左端開始向彈性壁12的右端無間隙的並排纏繞,同時用玻璃棒6一直擋著所繞的光纖,使光纖與彈性壁12起始端(圖1所示的左端)緊密貼合,其中,在彈性壁12起始端開始緩慢繞過幾圈光纖後,逐步提高光纖環1的轉速,同時繼續用玻璃棒6輕輕地擋著正在繞制的光纖,避免由於光纖環1的轉動,導致光纖排布時出現較大的縫隙,同時通過CCD觀測,保證光纖緊密排布,又不能由於排布過密出現搭纖的現象,直到纏繞到彈性壁12的末端(圖1所示的右端),形成第一光纖層,再次降低轉速,用玻璃棒6將光纖引入到彈性壁12另一端設置的第二卡槽72的槽內,然後將光纖從彈性壁12的右端向彈性壁12的左端並排纏繞於第一光纖層的外表面,直到光纖再次引入第一卡槽71的槽內,依次循環纏繞,直到設定光纖的匝數繞完為止。本實施例中第一卡槽71和第二卡槽72使光纖稍稍承力,避免光纖環1上的光纖過於鬆散導致排列不緊密。
本實施例有效的控制了光纖環上光纖間隙的問題,既能滿足光纖緊密貼合,又不會出現搭線的現象;並且本實施例通過卡槽和玻璃棒有效的解決了由於機械加工精度及其它因素,每層繞纖開始時光纖與彈性壁緊密貼合較困難造成兩端的光纖高於其他部位的光纖的問題;並且本實施例利用正交實驗的方法,選取彈性筒壁厚、光纖繞制張力、傳感光纖長度3個因素,採用L4(3)正交試驗確定合理張力,既保證了光纖與彈性壁的緊密耦合,又防止了製作過程中光纖張力過大容易損壞的問題;並且本實施例解決了傳統的人為塗膠存在各種缺點:人為利用刷子除去多餘的膠液時,不能保證膠液除去乾淨,造成光纖環表面不平整,並且刷子掉毛的風險,使光纖環內殘留雜物;只能將光纖繞制層表面的膠液去掉,不能將繞制層下面的多餘的膠液去掉,從而造成膠液堆積。
上述實施例中,在所述步驟三中,經過進膠輪8後的光纖的外表面塗覆膠的厚度為0.5mm-1mm。具體的,通過進膠輪8將光纖的外表面塗覆膠的厚度選擇為0.5mm-1mm,從而使得即保證光纖在有效的與光纖環粘接,又不會使得膠過量而使得光纖層下面有多餘的膠。
上述實施例中,在步驟三中,所述膠為紫外膠。具體的,紫外膠物理性能均勻穩定,頻率響應均勻,有利於光纖水聽器一致性的提高。
上述實施例中,在步驟四中,在光纖纏繞的過程中,玻璃棒6的表面與正在纏繞的光纖相接觸。具體的,玻璃棒6的內表面始終緊貼住正在纏繞的光纖,即玻璃棒6的內表面與彈性壁12之間的距離大約等於光纖直徑,從而避免由於光纖環1的轉動,導致光纖排布時出現較大的縫隙,保證光纖緊密排布,又不能由於排布過密出現搭纖的現象。
上述實施例中,在步驟四中,使用CCD觀測光纖的纏繞過程。具體的,從光纖開始從彈性壁12纏繞的時刻開始直至結束,始終利用CCD觀測,保證光纖緊密排布,又不能由於排布過密出現搭纖的現象。
上述實施例中,在步驟四中,第一卡槽71的數量為若干個,若干個第一卡槽71沿著彈性壁12一端的周向均勻分布。具體的,如圖2所示,在彈性壁12的左端設置有多個凸起的第一卡槽71,多個第一卡槽71沿著彈性壁12的左端的周向均勻分布,由於光纖的循環纏繞,從而保證光纖在到達彈性壁12的左端時能夠相對應的進入第一卡槽71內,利於光纖的纏繞,並且還保證了光纖的纏繞張力。
上述實施例中,在步驟四中,第二卡槽72的數量為若干個,若干個第二卡槽72沿著彈性壁12另一端的周向均勻分布。具體的,如圖2所示,在彈性壁12的右端設置有多個凸起的第二卡槽72,多個第二卡槽72沿著彈性壁12的右端的周向均勻分布,由於光纖的循環纏繞,從而保證光纖在到達彈性壁12的右端時能夠相對應的進入第二卡槽72內,利於光纖的纏繞,並且還保證了光纖的纏繞張力。
如圖1所示,本發明還提供了一種提高光纖水聽器一致性的光纖繞制模具,該模具包括:光纖環1、載纖盤2、導纖輪3和進膠輪8。具體的,載纖盤2和導纖輪3的設置位置可以根據人為設置在所需的位置,進膠輪8的右端可以與光纖環1的左端相對齊,從而使得經過進膠輪8的光纖走向與光纖環1的軸向相垂直
其中,光纖環1包括光纖環芯軸11和彈性壁12,其中,彈性壁12套設於光纖環芯軸11。具體的,彈性壁12套設於光纖環芯軸11的外表面,彈性壁12能夠圍繞光纖環芯軸11轉動。
光纖環芯軸11的一端開設有進纖槽4。具體實施時,進纖槽4的數量可以為若干個,若干個進纖槽4沿光纖環芯軸11的一端的周向均勻分布。
彈性壁12的一端設置有第一卡槽71,第一卡槽71的長度方向與彈性壁12的軸向垂直。具體實施時,彈性壁12的左端設置有第一卡槽71,第一卡槽71的數量為若干個,若干個第一卡槽71沿著彈性壁12左端的周向均勻分布。第一卡槽71的長度方向與彈性壁12的軸向垂直,使得光纖繞設在第一卡槽71的方向與彈性壁12的軸向垂直,從而便於纏繞。
彈性壁12的另一端設置有第二卡槽72,第二卡槽72的長度方向與彈性壁12的軸向垂直。具體實施時,彈性壁12的右端設置有第二卡槽72,第二卡槽72的數量為若干個,若干個第二卡槽72沿著彈性壁12右端的周向均勻分布。第二卡槽72的長度方向與彈性壁12的軸向垂直,使得光纖繞設在第二卡槽72的方向與彈性壁12的軸向垂直,從而便於纏繞。
本發明有效的控制了光纖環上光纖間隙的問題,既能滿足光纖緊密貼合,又不會出現搭線的現象;並且本發明通過卡槽和玻璃棒有效的解決了由於機械加工精度及其它因素,每層繞纖開始時光纖與彈性壁緊密貼合較困難造成兩端的光纖高於其他部位的光纖的問題;並且本發明利用正交實驗的方法,選取彈性筒壁厚、光纖繞制張力、傳感光纖長度3個因素,採用L4(3)正交試驗確定合理張力,既保證了光纖與彈性壁的緊密耦合,又防止了製作過程中光纖張力過大容易損壞的問題;並且本發明解決了傳統的人為塗膠存在各種缺點:人為利用刷子除去多餘的膠液時,不能保證膠液除去乾淨,造成光纖環表面不平整,並且刷子掉毛的風險,使光纖環內殘留雜物;只能將光纖繞制層表面的膠液去掉,不能將繞制層下面的多餘的膠液去掉,從而造成膠液堆積。
以上所述的實施例只是本發明較優選的具體實施方式,本領域的技術人員在本發明技術方案範圍內進行的通常變化和替換都應包含在本發明的保護範圍內。