一種重油加氫催化劑及其製備方法與流程
2023-09-21 00:47:35 3
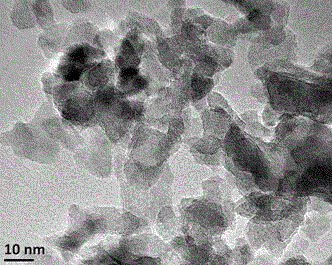
本發明涉及一種重油加氫催化劑及其製備方法。
背景技術:
隨著原油的日益重質化、劣質化,煉油企業面臨大量的重、渣油加工利用問題。重、渣油分子具有複雜的三維結構,含硫稠環芳烴側鏈常常形成空間位阻,妨礙五、六元環中的硫原子被催化劑活性中心吸附。在催化加氫過程中,重油大分子吸附並沉積在催化劑的表面或孔口,使反應內擴散阻力增大,造成催化劑的表觀活性下降。同時,重、渣油中含有較多的焦炭前驅物,它們在一定條件下會生成焦炭並沉積在孔內導致催化劑的活性中心中毒。催化劑內擴散成為重、渣油催化加氫過程的控制因素,因此重、渣油的催化加氫需要大孔催化劑,並具有較大的孔徑和孔容,以便容納更多的積炭、金屬沉積物等,減少大分子反應遇到的擴散阻力。催化劑的大孔徑和孔容主要依託於相應大孔徑大孔容的載體。
催化劑的孔道來源於載體,獲得不同孔道特徵的催化劑,首先是從催化劑載體入手。良好的大孔載體在孔徑分布上,除應具有較為集中的10-20nm的孔徑分布外,還應具有適量的大於50nm的大孔分布,以延緩大分子在催化劑中孔口的堵塞和容納更多的積炭、金屬沉積物等。因此,採用大小孔徑並存的雙孔徑分布的載體製成的催化劑,具有優越的性能。然而,通常用於製備加氫處理催化劑的氧化鋁的孔徑較小,不能滿足製備重油、渣油加氫脫金屬催化劑的需要。因此必須在製備過程中採用擴孔的辦法來得到大孔。常用的擴孔方法是在擬薄水氧化鋁幹膠粉混捏、擠條等成型過程中加入各種類型的擴孔劑。目前用到的物理擴孔劑有碳黑、碳纖維、糖類等有機物質。
US4448896以碳黑為擴孔劑,將其與擬薄水鋁石混捏成可塑體並擠條成型。在載體焙燒過程中,擴孔劑經氧化、燃燒,逐步以氣態物逸出,在載體中形成空洞,從而構成較大的孔道。但是該專利所用碳黑量較大,一般達到20wt%以上,所得載體的機械強度較低才,孔分布較為彌散。英國專利EP237240採用碳纖維為擴孔劑製備大孔氧化鋁,但同樣存在擴孔劑用量大及載體強度低等不足。
CN96103297.9通過在擬薄水鋁石幹膠粉中加入物理擴孔劑如炭黑及化學擴孔劑如磷化物,通過混捏法成型,所得載體可幾孔直徑為10~20nm。因而當反應所需催化劑要求載體具有雙重孔道且要有較高機械強度時,此種載體就受到了一定限制。
上述專利所面臨的共同問題還有,所用的碳黑、活性碳纖維或其它有機物質需要通過專門的工藝來製備。比如,碳黑粉的來源主要有槽法碳黑、高耐磨碳黑及乙炔法碳黑。使用這種經特殊工藝製備的擴孔劑無形中增加了大孔氧化。
此外,對於工業催化劑的設計而言,還應具有較高的比表面積,以便使催化劑的活性位的濃度較大。然而比表面積孔徑大小常常是矛盾的。為了抑制沉積物對孔口的沉積作用,需要較大的孔隙進行擴散,然而較大的孔隙通常意味著較低的比表面積。
技術實現要素:
針對現有技術的不足,本發明提供一種重油加氫催化劑及其製備方法。本發明重油加氫催化劑的催化劑,具有貫穿的大孔結構,較高的孔隙率,集中的介孔分布,傳質擴散性能優異,用於重、渣油加氫催化脫硫、脫氮和脫金屬能力較強。
本發明的重油加氫催化劑,包括片狀多晶γ-氧化鋁組成的氧化鋁載體和加氫活性金屬;其中片狀多晶γ-氧化鋁的性質如下:粒徑尺寸為100-600nm,厚度為40-100nm,片狀多晶γ-氧化鋁顆粒由5-40nm的γ-氧化鋁晶粒組成。
所述的重油加氫催化劑,具有如下性質:孔隙率為70%-90%,孔容為0.8-2.0cm3/g,比表面積為200-400m2/g,介孔分布為5-50nm,分布集中度為70%-90%。
所述的加氫活性金屬為VIB或VIII族金屬元素,第VIB族金屬優選為鉬和/或鎢,第VIII族的金屬優選為鈷和/或鎳。以催化劑的重量為基準,VIB族金屬的含量以氧化物計為5.0wt%-25.0wt%,VIII族金屬的含量以氧化物計為1.0-5.0%。
本發明的重油加氫催化劑的製備方法,包括如下內容:
將片狀γ-多晶氧化鋁原粉加入粘結劑、助擠劑混捏、成型、乾燥和焙燒,得到氧化鋁載體;採用常規的方法在所得的氧化鋁載體上負載活性金屬;
其中片狀γ-多晶氧化鋁的製備方法,包括如下步驟:
(1)無機鋁鹽、低碳醇和/或水、低碳環氧烷烴混合均勻,形成凝膠,然後將凝膠進行老化;
(2)將步驟(1)得到的凝膠用低碳醇浸泡,然後乾燥、焙燒;
(3)步驟(2)得到的物料浸入氨水中進行密閉水熱處理,固液分離,乾燥,得到片狀γ-多晶氧化鋁原粉。
步驟(1)中,所述的無機鋁鹽為水溶性無機鋁鹽,選自氯化鋁、硝酸鋁和硫酸鋁中的一種或多種,優選為氯化鋁;低碳醇為C5以下的醇,選自甲醇、乙醇、正丙醇和異丙醇中的一種或多種,更優選為乙醇和/或丙醇;低碳醇可以與水以任意比例混合,優選為水/低碳醇的質量比為0.5-2.0。
步驟(1)中,所述的低碳環氧烷烴的碳數為2-4,優選為環氧乙烷和/或環氧丙烷。
步驟(1)中,步驟(1)混合物中各組分含量,以質量百分計:無機鋁鹽10%-60%,優選為20%-35%,水和/或低碳醇的總含量為30%-70%,其餘物料為低碳環氧烷烴。低碳環氧烷烴與無機鋁鹽滿足下述關係:以摩爾量計,低碳環氧烷烴/Al3+為2.5-9,優選為3.5-7.0。
步驟(1)中,所述的老化溫度為20-90℃,優選30-60℃,老化時間為1-72小時,優選12-60小時。
步驟(2)中,所述的低碳醇為C5以下的醇,優選為甲醇、乙醇、正丙醇和異丙醇中的一種或多種,優選為乙醇和/或丙醇。
步驟(2)中,所述的浸泡條件為:溫度20-80℃,優選為30-60℃,時間1-72小時,優選為12-60小時。
步驟(2)中,所述的乾燥溫度不大於200℃,優選為不大於120℃。
步驟(3)中,所述的氨水濃度為0.01-0.5mol/L,以摩爾量計,氨水/Al3+比值0.5-20,優選為1.0-5.0;氨水的體積至少能夠將所處理的物料完全浸沒。
步驟(3)中,所述的密閉水熱條件為:130-180℃下水熱處理1-12小時。
步驟(3)中,所述的乾燥溫度不大於200℃,優選為不大於120℃,乾燥程度:在此溫度下物料恆重。
本發明的重油加氫催化劑,載體由片狀多晶γ-氧化鋁組成,片狀多晶γ-氧化鋁為γ-氧化鋁二次顆粒具有片狀形貌,γ-氧化鋁二次顆粒由γ-氧化鋁一次小晶粒組成,形成多晶γ-氧化鋁,因此可以保持傳統多晶不規則氧化鋁顆粒的活性。同時,本發明的片狀多晶γ-氧化鋁,在載體顆粒中無序排列,形成連續且較大的孔隙率,有利於重油大分子尤其是渣油中膠質、瀝青質的傳質過程。同時,片狀氧化鋁晶粒在形貌和尺寸上統一性相對較高,能夠顯著提高載體材料中由二次粒子形成的孔隙尺寸分布的集中性,從而改善催化劑的催化性能。本發明的重油加氫催化劑應用於重、渣油加氫反應,具有很強的加氫催化脫硫、脫氮和脫金屬能力。
附圖說明
圖1為本發明實施例1製備的片狀γ-氧化鋁的掃描電鏡照片。
圖2為本發明實施例1製備的片狀γ-氧化鋁的透射電鏡照片。
圖3為本發明實施例1製備的片狀γ-氧化鋁的X射線衍射(XRD)譜圖。
圖4為本發明實施例1製備的片狀γ-氧化鋁的孔結構分布圖。
具體實施方式
下面結合實施例對本發明作進一步詳細說明。以壓汞法測試大孔氧化鋁的孔隙率。比表面積採用BET法測定,介孔分布集中度採用峰面積積分法測定。片狀γ-氧化鋁顆粒尺寸根據掃描電鏡圖像測量。組成片狀顆粒的小晶粒通過透射電鏡觀察,觀察其尺寸範圍。晶型採用X射線衍射表徵。
本發明氧化鋁載體中片狀γ-多晶氧化鋁,具體的製備方法如下:
(1)無機鋁鹽、低碳醇和/或水、低碳環氧烷烴混合均勻,形成凝膠,然後將凝膠進行老化;
所述的無機鋁鹽為水溶性無機鋁鹽,選自氯化鋁、硝酸鋁和硫酸鋁中的一種或多種,優選為氯化鋁;低碳醇為C5以下的醇,選自甲醇、乙醇、正丙醇和異丙醇中的一種或多種,更優選為乙醇和/或丙醇;低碳醇可以與水以任意比例混合,優選為水/低碳醇的質量比為0.5-2.0;所述的低碳環氧烷烴的碳數為2-4,優選為環氧乙烷和/或環氧丙烷;混合物中各組分含量,以質量百分計:無機鋁鹽10%-60%,優選為20%-35%,水和/或低碳醇的總含量為30%-70%,其餘物料為低碳環氧烷烴。低碳環氧烷烴與無機鋁鹽滿足下述關係:以摩爾量計,低碳環氧烷烴/Al3+為2.5-9,優選為3.5-7.0;所述的老化溫度為20-90℃,優選30-60℃,老化時間為1-72小時,優選12-60小時;
(2)將步驟(1)得到的凝膠用低碳醇浸泡,然後乾燥、焙燒;
所述的低碳醇為C5以下的醇,優選為甲醇、乙醇、正丙醇和異丙醇中的一種或多種,優選為乙醇和/或丙醇;所述的浸泡條件為:溫度20-80℃,優選為30-60℃,時間1-72小時,優選為12-60小時;所述的乾燥溫度不大於200℃,優選為不大於120℃。
(3)步驟(2)得到的物料浸入氨水中進行密閉水熱處理,固液分離,乾燥,得到片狀γ-多晶氧化鋁原粉;
所述的氨水濃度為0.01-0.5mol/L,以摩爾量計,氨水/Al3+比值0.5-20,優選為1.0-5.0;氨水的體積至少能夠將所處理的物料完全浸沒;所述的密閉水熱條件為:130-180℃下水熱處理1-12小時;步驟(3)中,所述的乾燥溫度不大於200℃,優選為不大於120℃,乾燥程度:在此溫度下物料恆重。
本發明重油加氫催化劑的具體製備過程如下:
將片狀γ-多晶氧化鋁原粉加入粘結劑、助擠劑混捏、成型、乾燥和焙燒,得到氧化鋁載體;採用常規的方法在所得的氧化鋁載體上負載活性金屬;
所用的粘結劑是硝酸、磷酸、鋁溶膠、矽溶膠和檸檬酸中的一種或幾種;所述的助擠劑是幹澱粉、田菁粉和石墨中的一種或幾種;其中成型後載體的形狀包括但不限於球形、條形、圓柱形、三葉草、四葉草、齒球及其它異形;所述的成型為常規成型方法,如擠條成型等。所述的乾燥溫度不大於200℃,優選為不大於120℃,乾燥時間為5-24小時;所述的焙燒條件為:400-750℃焙燒1-12小時,優選500-650℃焙燒3-6小時;所述的載體原粉材料乾燥後,也可以不焙燒。
本發明催化劑活性金屬的負載,可採用現有技術中常規的負載方法,優選浸漬法,可以是飽和浸、過量浸或絡合浸,即用含有所需活性組分的溶液浸漬催化劑載體,浸漬後的載體在80℃~130℃乾燥1~12小時,然後在500℃~800℃焙燒2~7小時,製得最終催化劑。
實施例1
將水、無水乙醇、氯化鋁混合,再加入環氧丙烷混合均勻,混合物各組分以重量計,含量分別為:水23%,乙醇23%,氯化鋁20%,環氧丙烷34%。混合均勻後,所得凝膠於30℃下老化60小時,然後用乙醇浸泡老化後的凝膠, 30℃下浸泡60小時。完畢後除去液相,120℃下乾燥直至產物不再發生明顯的減重。然後在500℃下焙燒6小時,冷卻到室溫,再浸入到過量的至少將其完全淹沒的0.01M的氨水中(以摩爾量計,氨水/Al3+比值為5.0),然後密閉並升溫到135℃水熱處理12小時。將120℃下乾燥後的產物於650℃下焙燒3小時,冷卻後經掃描電鏡觀察可知,產物形貌表現為片狀,其尺寸為100-400nm,厚度為36nm。將樣品研磨並超聲分散後,用透射電鏡觀察可知,片狀顆粒由8-30nm的更小晶粒組成。由於簡單研磨和超聲處理不可能破壞單晶顆粒,故片狀顆粒並不是大單晶晶粒。產物的XRD結果表明,其為γ-氧化鋁。因此,片狀顆粒為多晶γ-氧化鋁。物理吸附測試表明,其具有8-20nm的較窄的介孔分布。
實施例2
室溫下,將水、無水乙醇、氯化鋁混合,再加入環氧丙烷混合均勻,混合物各組分以重量計,含量分別為:水15%,乙醇20%,氯化鋁35%,環氧丙烷30%。混合均勻之後,所得凝膠於40℃下老化48小時,然後用丙醇浸泡老化後的混合物,溫度為40℃,時間為48小時,完畢後除去液相,100℃下乾燥直至產物不再發生明顯的減重。然後在600℃下焙燒6小時,冷卻到室溫,再浸入到過量的至少將其完全淹沒的0.1M的氨水中(以摩爾量計,氨水/Al3+比值為2.0),然後密閉並升溫到150℃水熱處理5小時。將100℃下乾燥後的產物於550℃下焙燒5小時。冷卻後,掃描電鏡觀察可知,產物形貌為片狀,其尺寸為254nm,厚度為41nm。將樣品研磨並超聲分散後,用透射電鏡觀察可知,片狀顆粒由10-25nm的小晶粒組成。產物的XRD結果表明,其為γ-氧化鋁。所以,片狀顆粒為多晶γ-氧化鋁。物理吸附測試表明,其具有10-21nm的較窄的介孔分布。
實施例3
室溫下,將水、無水乙醇、氯化鋁混合,再加入環氧丙烷混合均勻,混合物各組分以重量計,含量分別為:水30%,乙醇23%,氯化鋁25%,環氧丙烷22%。混合均勻之後,所得凝膠於60℃下老化12小時,然後用乙醇60℃浸泡老化後的混合物24小時,之後除去液相,120℃下乾燥直至產物不再發生明顯的減重。然後在550℃下焙燒5小時,冷卻到室溫,再浸入到過量的至少將其完全淹沒的0.3M的氨水中(以摩爾量計,氨水/Al3+比值為3.0),然後密閉並升溫到165℃水熱處理9小時。將120℃下乾燥後的產物於500℃下焙燒8小時,冷卻後掃描電鏡觀察可知,產物形貌為片狀,尺寸為542nm,厚度為89nm。將樣品研磨和超聲分散後,用透射電鏡觀察可知,片狀顆粒由10-35nm的小晶粒組成。產物的XRD結果表明,其為γ-氧化鋁,因此片狀顆粒為多晶γ-氧化鋁。物理吸附測試表明,其具有35-47nm的較窄的介孔分布。
實施例4
採用實施例1的方法製備的片狀多晶γ-氧化鋁。將其與少量的田菁粉混合,以質量計,田菁粉含量為2.5%,其餘為片狀多晶γ-氧化鋁載體原粉,總重量為100g。以2%的硝酸溶液140克浸潤上述混合粉末,然後混捏擠條成圓柱形,120℃乾燥3小時,然後550℃焙燒5小時得到載體。配製鉬酸銨與硝酸鎳的混合水溶液,以浸漬法負載到上述載體上,120℃乾燥2小時,然後升溫到650℃焙燒4小時,得到氧化態催化劑。性質如表1所示。
所製備的重油加氫催化劑使用前需經預硫化,硫化後逐漸切換為原料油。所用重質柴油原料性質:相對密度0.898,硫含量6312μg/g,氮含量9104μg/g。反應條件:溫度350℃,壓力6MPa,空速1.0h-1,體積氫油比470。原料油經加氫反應後,性質如下:相對密度0.871,硫含量104μg/g,氮含量79μg/g。
實施例5
採用實施例3的方法製備的片狀多晶γ-氧化鋁。將其與少量的田菁粉混合,以質量計,田菁粉含量為2.5%,其餘為片狀多晶γ-氧化鋁載體原粉,總重量為100g。以2%的硝酸溶液140克浸潤上述混合粉末,然後混捏擠條成圓柱形,120℃乾燥3小時,然後550℃焙燒5小時得到載體。配製鉬酸銨與硝酸鎳的混合水溶液,以浸漬法負載到上述載體上,120℃乾燥2小時,然後升溫到700℃焙燒5小時,得到氧化態催化劑。性質如表1所示。
所製備的重油加氫催化劑使用前需經預硫化,硫化後逐漸切換為原料油。所用渣油原料性質:相對密度0.942,硫含量24217μg/g,氮含量3047μg/g。反應條件:溫度390℃,壓力15.4MPa,空速0.6h-1,體積氫油比1000。催化劑加氫性能如表1所示。原料油經加氫反應後,性質如下:相對密度0.869,硫含量2404μg/g,氮含量751μg/g。
對比例1
按照CN 96103297.9實施例1的方法製備大孔氧化鋁。按照本發明實施例5的方法負載活性金屬,使用相同的條件,並進行渣油脫硫反應。原料油經加氫反應後,性質如下:相對密度0.892,硫含量3576μg/g,氮含量1069μg/g。
表1 催化劑性質。
從表1可以看出,本發明催化劑較集中的孔分布和較大的孔隙率。