鍋爐主蒸汽溫度多參量智能控制系統的製作方法
2023-09-19 04:03:55
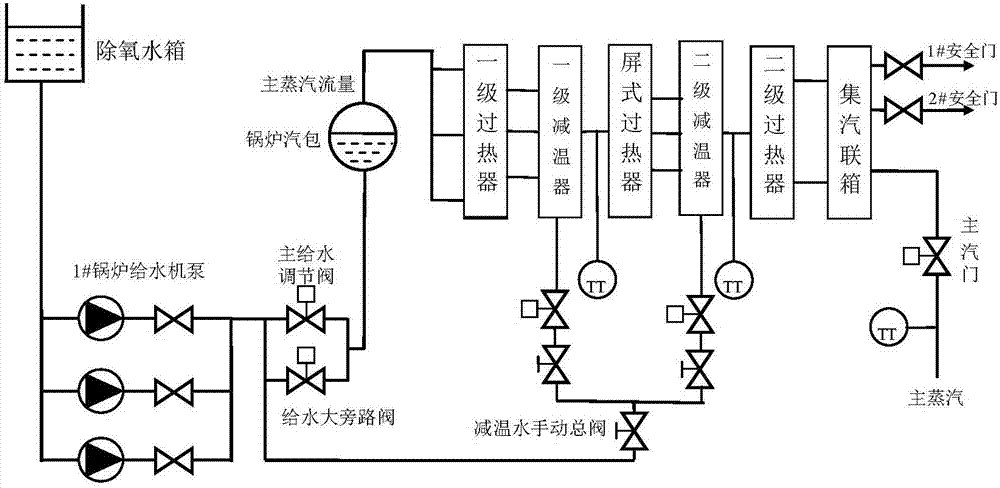
本發明涉及火力發電鍋爐主蒸汽溫度控制技術領域,具體的說是一種鍋爐主蒸汽溫度多參量智能控制系統。
背景技術:
鍋爐作為火力發電過程中的三大重要設備(鍋爐、汽輪機、發電機)之一,是最重要的生產設備,在電廠運行過程中,是為汽輪機提供動力的關鍵。
在發電過程中,鍋爐過熱器末級出口的主蒸汽(又稱為過熱蒸汽)溫度是鍋爐機組的重要控制參數,其控制品質的好壞直接影響整個機組的安全和經濟運行。由於電廠鍋爐過熱器在運行過程中,其溫度已接近過熱器金屬最高承受溫度,蒸汽溫度過高會使過熱器管道強度降低,使用壽命減少,長期超溫10~20℃運行,其壽命將縮短一半,長期處在超溫下會造成過熱器變形而爆管,影響其安全;蒸汽溫度過低,整個機組循環熱效率隨之降低,通常蒸汽溫度每降低5~10℃,其效率降低約1%。對汽輪機而言,過高的主蒸汽溫度會造成汽輪機高壓缸渦輪受到的熱應力過大而損壞;過低的主蒸汽溫度會使通過汽輪機最後幾段葉片蒸汽的溼度增加,造成葉片磨損。此外,溫度波動會導致鍋爐和汽輪機的金屬管道及零部件產生金屬疲勞,也會導致渦輪缸和轉子的脹差變化,甚至產生嚴重震動,危及機組的安全運行。因此過熱器出口的最終主蒸汽溫度必須嚴格地控制在規定的範圍內。通常要求不超過額定值的-10~+5℃,長時間運行偏差波動範圍不超過±5℃。主蒸汽的額定運行溫度通常在500℃以上。
從圖1可以看出,包含給水系統和主蒸汽系統,所述主蒸汽系統包括依次連接的鍋爐汽包、一級過熱器、一級減溫器、屏式過熱器、二級減溫器、二級過熱器和集汽聯箱。兩級減溫器位於兩級過熱器之間,其目的是保證各級蒸汽溫度在正常範圍內,保證蒸汽管道不被損壞,並使最終的主蒸汽溫度參數達到要求的值。從汽包出來的飽和蒸汽先經過一級過熱器,再經過兩級減溫器減溫,最終從二級過熱器輸出得到所需的主蒸汽。通過調節兩級減溫器的減溫水流量實現對各減溫器出口蒸汽溫度的獨立控制,兩級減溫器的減溫水來自給水母管。由於鍋爐汽包液位採用調節主給水閥的開度進行控制,鍋爐給水泵在工頻狀態下定量供水,此方式下能保證給水母管水壓波動較小,對減溫水流量的幹擾也小,兩級減溫器出口蒸汽溫度能滿足控制要求,並使最終的主蒸汽溫度偏差不大,從而間接實現對主蒸汽溫度的控制。但在這種工作方式下,因為鍋爐產生的最大蒸汽量約為220t/h,每臺鍋爐給水泵功率約為1000kw,當主給水調節閥不全開時,會在閥前後產生較大壓差,導致節流損失太大。
為響應國家節能降耗的要求,現在國內許多鍋爐逐步在進行變頻節能改造,即向給水泵增加變頻器裝置,然後將主給水調節閥全開,通過檢測汽包液位,根據液位偏差通過變頻器自動調節給水泵頻率控制給水量從而控制汽包液位。但這種改造後的運行方式帶來了新的問題,調節過程中,母管水壓會隨鍋爐蒸汽量的變化而出現波動,減溫水閥流量幹擾也會隨之變大,導致各減溫器出口蒸汽溫度控制精度變差。由於目前的這種控制方式並沒有將所需的主蒸汽溫度直接納入控制系統中,這樣各控制段蒸汽溫度偏差累積最終會造成出口主蒸汽溫度偏離所需溫度值。
實際過程中,各控制段採用的是簡單的常規pid控制,當主蒸汽溫度偏離所需溫度值範圍時,通過人工觀察最終主蒸汽溫度的值,由人工手動分段設定各減溫器出口蒸汽溫度的控制值,來間接控制最終主蒸汽溫度,因此對操作人員的要求很高,不僅需要豐富的相關專業知識,而且還必須具備熟練的操控水平,如果控制不及時,也很難在短時間內將主蒸汽溫度穩定在所需的溫度範圍內,顯然這種控制方式難以達到對主蒸汽溫度的精確控制。通過查閱大量相關文獻資料,目前國內的鍋爐主蒸汽溫度基本都是採用這種控制方式,即現在的控制方式不能滿足精確自動控制的要求。
由於鍋爐主蒸汽溫度控制過程中還存在被控對象慣性和延遲性較大,以及蒸汽流量、煙氣熱量、減溫水流量波動等各種幹擾影響,這些因素共同作用更加降低了對主蒸汽溫度的可控性指數。基於上述系統及缺陷,又不能對該系統的結構進行大的變動,無法對鍋爐汽包和一級減溫器、二級減溫器進行獨立供水,鍋爐主蒸汽溫度控制缺陷無法得到改變。
要想確保主蒸汽溫度的控制達到安全穩定,對其進行自動化控制越來越重要。為此,如何實現蒸汽生產過程中主蒸汽溫度的穩定,提高主蒸汽溫度控制質量具有重要的現實意義和實用價值。
技術實現要素:
針對上述問題,本發明提供了一種鍋爐主蒸汽溫度多參量智能控制系統,控制迅速,主蒸汽溫度穩定,溫度誤差小,可靠性高。
為達到上述目的,本發明採用的具體技術方案如下:
一種鍋爐主蒸汽溫度多參量智能控制系統,包括給水系統和主蒸汽系統,所述主蒸汽系統設置有鍋爐汽包,以及鍋爐汽包輸出蒸汽氣路上依次設置的一級過熱器、一級減溫器、屏式過熱器、二級減溫器、二級過熱器和集汽聯箱,在所述一級減溫器的蒸汽輸出口處設置有第一溫度監測器,在所述二級減溫器的蒸汽輸出口處設置有第二溫度監測器,所述二級過熱器蒸汽輸出口設置有第三溫度監測器,所述給水系統包括水箱,所述水箱中的水經給水機泵輸送到所述鍋爐汽包,所述水箱中的水還經給水機泵、一級減溫水流量閥輸送到一級減溫器,所述水箱中的水還經給水機泵、二級減溫水流量閥輸送到所述二級減溫器,其關鍵在於:
所述主蒸汽系統還設置有主蒸汽控制系統,所述主蒸汽控制系統包括內模控制器、減溫控制模塊、第三幹擾模塊和內部模型模塊;所述內模控制器獲取第一差值信號δt1並輸出主蒸汽溫度控制信號t1;所述減溫控制模塊根據所述主蒸汽溫度控制信號t1逐級對所述一級減溫器、二級減溫器的減溫過程進行控制,從而改變所述二級過熱器輸出蒸汽的二級過熱蒸汽溫度值t3;所述第三幹擾模塊採集第三幹擾驅動信號d0並輸出第三幹擾信號g,該第三幹擾信號g與所述二級過熱蒸汽溫度值t3作差後得到所述主蒸汽實際溫度信號t0;所述內部模型模塊獲取所述主蒸汽溫度控制信號t1並輸出跟蹤溫度信號t0』;所述主蒸汽實際溫度信號t0和所述跟蹤溫度信號t0』作差後得到第二差值信號δt2,該第二差值信號δt2與主蒸汽設定溫度信號t作差後得到所述第一差值信號δt1。
通過上述設計,為了實現對最終主蒸汽溫度的直接控制,通過擬合計算得到其內部模型,根據內模控制原理減小由於主蒸汽溫度傳輸過程中形成的純滯後對控制效果的影響,使溫度調節響應更及時。減小控制過程中時滯的影響,上述方案在主迴路中採用內模控制方式將最終主蒸汽溫度納入控制系統中,對主蒸汽溫度進行穩定。並對主蒸汽溫度進行幹擾控制,提高主蒸汽溫度穩定性。累積誤差小,控制可靠,魯棒性強。
進一步地,所述第三幹擾驅動信號d0為流經所述鍋爐汽包輸出的蒸汽流量信號。
採用上述方案,利用外環主迴路將主蒸汽溫度直接納入了控制系統中,減小了各控制段獨立控制情況下的偏差累積。通過外環主迴路對主蒸汽溫度進行直接控制。
再進一步描述,所述減溫控制模塊包括第一減溫控制模塊和第二減溫控制模塊,所述第一減溫控制模塊獲取所述主蒸汽溫度控制信號t1,並對所述一級減溫器的減溫過程進行控制,從而改變所述一級減溫器輸出蒸汽的第一減溫溫度值t1,所述第一減溫控制模塊還根據第一減溫溫度值t1生成第一減溫蒸汽溫度信號t3;所述第二減溫控制模塊獲取所述第一減溫蒸汽溫度信號t3,並對所述二級減溫器的減溫過程進行控制,從而改變所述二級減溫器輸出蒸汽的第二減溫溫度值t2,進而改變所述二級過熱蒸汽溫度值t3,所述第二減溫控制模塊還根據所述二級過熱蒸汽溫度值t3生成所述主蒸汽實際溫度信號t0。
通過上述設計,將對一級減溫器、二級減溫器的控制作為單獨的控制系統進行控制,分別用來快速穩定兩級減溫器出口蒸汽溫度,二級減溫器的蒸汽溫度設定值由一級減溫器輸出的蒸汽溫度給定,一級減溫器溫度設定值由主控制器隨動給定。累積誤差小,控制可靠。
再進一步描述,所述第一減溫控制模塊包括第一減溫控制器、第一補償模塊和第一幹擾模塊,所述第一減溫控制器獲取第三差值信號δt3並輸出第一減溫控制信號a,所述一級減溫水流量閥根據所述第一減溫控制信號a來改變閥門開度,從而改變一級減溫水流量,進而改變所述第一溫度監測器採集的所述第一減溫溫度值t1;所述第一幹擾模塊獲取第一幹擾驅動信號,並輸出第一幹擾信號d,所述第一蒸汽監測溫度與所述第一幹擾信號d作差後得到所述第一減溫蒸汽溫度信號t3;所述第一補償模塊獲取第一補償驅動信號,並輸出第一補償信號c,所述主蒸汽溫度控制信號t1與所述第一減溫蒸汽溫度信號t3、第一補償信號c依次作差後得到所述第三差值信號δt3。
採用上述方案,當第一幹擾信號d和第一補償信號c對一級減溫器作用時,第一減溫控制器迅速作出反應,並且內模控制器、第二減溫控制模塊也作出對應的響應,使得兩級減溫器出口蒸汽溫度快速穩定在同一溫度。削弱了一級減溫器減溫過程對主蒸汽溫度的影響。
再進一步描述,所述第一幹擾驅動信號或為相鄰兩個時刻所述一級減溫器蒸汽輸出口的蒸汽流量信號差值,或為相鄰兩個時刻流經所述一級減溫水流量閥的水流量信號差值;所述第一補償驅動信號或為相鄰兩個時刻所述一級減溫器蒸汽輸出口的蒸汽流量信號差值,或為相鄰兩個時刻流經所述一級減溫水流量閥的水流量信號差值。
採用上述方案,針對不同的實際情況,避免流經一級減溫水流量閥的水流量信號差值或者一級減溫器蒸汽輸出口的蒸汽流量信號差值對減溫過程造成的波動,當存在水流量差值或者蒸汽量差值時,對一級減溫器的減溫過程進行適當的補償和幹擾,增強一級減溫器的減溫控制穩定性。
再進一步描述,所述第二減溫控制系統包括第二減溫控制器、第二補償模塊和第二幹擾模塊,所述第二減溫控制器獲取第四差值信號δt4並輸出第二減溫控制信號b,所述二級減溫水流量閥根據所述第二減溫控制信號b來控制閥門開度,從而改變二級減溫水流量,進而改變所述第二溫度監測器採集的所述第二減溫溫度值t2;所述第二幹擾模塊獲取第二幹擾驅動信號,並輸出第二幹擾信號f,所述第二減溫溫度值t2與所述第二幹擾信號f作差後得到所述第二減溫蒸汽溫度信號t4;所述第二補償模塊獲取第二補償驅動信號,並輸出第二補償信號h,所述第一減溫蒸汽溫度信號t3與所述第二減溫蒸汽溫度信號t4、第二補償信號h依次作差後得到所述第四差值信號δt4。
當第二幹擾信號f和第二補償信號h對二級減溫器作用時,第二減溫控制器迅速作出反應,並且內模控制器、第一減溫控制器也作出對應的響應,使得兩級減溫器出口蒸汽溫度快速穩定在同一溫度。削弱了二級減溫器減溫控制過程對主蒸汽溫度的影響。
再進一步描述,所述第二幹擾驅動信號或為相鄰兩個時刻所述二級減溫器蒸汽輸出口的蒸汽流量信號差值,或為相鄰兩個時刻流經所述二級減溫水流量閥的水流量信號差值;所述第二補償驅動信號或為相鄰兩個時刻所述二級減溫器蒸汽輸出口的蒸汽流量信號差值,或為相鄰兩個時刻流經所述二級減溫水流量閥的水流量信號差值。
針對不同的實際情況,避免流經二級減溫水流量閥的水流量信號差值或者二級減溫器蒸汽輸出口的蒸汽流量信號差值對減溫過程造成的波動,當存在水流量差值或者蒸汽量差值時,對二級減溫器的減溫過程進行適當的補償和幹擾,增強二級減溫器的減溫控制穩定性。
再進一步描述,所述主蒸汽系統還設置有自適應pid修正模塊,所述自適應pid修正模塊以輸入溫度偏差e和偏差變化率ec作為輸入,所述自適應pid控制器輸出參數增量信號δk至所述內模控制器;
所述輸入溫度偏差e為所述主蒸汽設定溫度信號t與所述主蒸汽實際溫度信號t0的差值;所述偏差變化率
通過上述設計,實現主迴路控制器參數的在線實時修正。通過引入模糊智能在線修正單元,對主蒸汽溫度偏差進行分析,當機組運行工況變化使主蒸汽溫度偏離設定值範圍時,通過模糊智能在線修正單元給出相應的控制器參數修正值,並與主控制器原有的基本參數設定值疊加後得到新的控制器動態設定值,從而實現對控制器參數的動態修正。經過參數修正後的控制器根據輸入偏差運算後輸出合適的控制量給執行機構,以此對主蒸汽溫度進行控制,從而改善常規控制方式在工況變化時,固定的控制器參數不能較好地控制主蒸汽溫度的缺點,使系統具有更好的適應調節能力。
本發明的有益效果:
採用兩級控制,將對一級減溫器、二級減溫器的控制作為兩單內環控制迴路,分別用來快速穩定兩級減溫器出口蒸汽溫度,二級減溫器的蒸汽溫度設定值由一級減溫器出口蒸汽溫度給定,一級減溫器溫度設定值由內模控制器隨動給定。能快速消除減溫水流量波動等幹擾因素引起的主蒸汽溫度波動,使系統快速穩定。保證了兩控制段噴水減溫器有效配合。
通過外環主迴路將主蒸汽溫度直接納入了控制系統中,減小了各控制段獨立控制情況下的偏差累積。
主迴路採用內模控制方式,將兩單內環迴路等效為廣義的被控對象,通過擬合計算得到其內部模型,根據內模控制原理減小由於主蒸汽溫度傳輸過程中形成的純滯後對控制效果的影響,使溫度調節響應更及時。
實現主迴路控制器參數的在線實時修正。通過引入自適應pid在線修正模塊,對主蒸汽溫度偏差進行分析,當機組運行工況變化使主蒸汽溫度偏離設定值範圍時,通過自適應pid在線修正模塊給出相應的控制器參數修正值,並與內模控制器原有的基本參數設定值疊加後得到新的控制器動態設定值,從而實現對控制器參數的動態修正。經過參數修正後的控制器根據輸入偏差運算後輸出合適的控制量給執行機構,以此對主蒸汽溫度進行控制,從而改善常規控制方式在工況變化時,固定的控制器參數不能較好地控制主蒸汽溫度的缺點,使系統具有更好的適應調節能力。
附圖說明
圖1是本發明的單座燃煤鍋爐主蒸汽生產工藝示意圖;
圖2是本發明的主蒸汽生成工藝流程圖;
圖3是本發明的內模控制系統框圖;
圖4是本發明內模控制原理圖;
圖5是本發明內模控制等效結構圖;
圖6是本發明的鍋爐主蒸汽溫度雙單內環串級控制系統框圖。
圖7是本發明自適應pid修正模塊組成框圖。
具體實施方式
下面結合附圖對本發明的具體實施方式以及工作原理作進一步詳細說明。
從圖1和圖2可以看出,一種鍋爐主蒸汽溫度多參量智能控制系統,包括給水系統和主蒸汽系統,所述主蒸汽系統設置有鍋爐汽包,以及鍋爐汽包輸出蒸汽氣路上依次設置的一級過熱器、一級減溫器、屏式過熱器、二級減溫器、二級過熱器和集汽聯箱。
從圖1還可以看出,在所述一級減溫器的蒸汽輸出口處設置有第一溫度監測器,在所述二級減溫器的蒸汽輸出口處設置有第二溫度監測器,所述二級過熱器蒸汽輸出口設置有第三溫度監測器,所述給水系統包括水箱,所述水箱中的水經給水機泵輸送到所述鍋爐汽包,所述水箱中的水還經給水機泵、一級減溫水流量閥輸送到一級減溫器,所述水箱中的水還經給水機泵、二級減溫水流量閥輸送到所述二級減溫器。
優選地,在鍋爐汽包蒸汽輸出口處設置有第一蒸汽流量計。在一級減溫器的蒸汽輸出口處設置有第二蒸汽流量計。在二級減溫器的蒸汽輸出口處設置有第三蒸汽流量計。
優選地,在一級減溫器的減溫水管道上設置有第一減溫水流量計。在二級減溫器的減溫水管道上設置有第二減溫水流量計。
從圖3可以看出,所述主蒸汽系統還設置有主蒸汽控制系統,所述主蒸汽控制系統包括內模控制器、減溫控制模塊、第三幹擾模塊和內部模型模塊;所述內模控制器獲取第一差值信號δt1並輸出主蒸汽溫度控制信號t1;所述減溫控制模塊根據所述主蒸汽溫度控制信號t1逐級對所述一級減溫器、二級減溫器的減溫過程進行控制,從而改變所述二級過熱器輸出蒸汽的二級過熱蒸汽溫度值t3;所述第三幹擾模塊採集第三幹擾驅動信號d0並輸出第三幹擾信號g,該第三幹擾信號g與所述二級過熱蒸汽溫度值t3作差後得到所述主蒸汽實際溫度信號t0;所述內部模型模塊獲取所述主蒸汽溫度控制信號t1並輸出跟蹤溫度信號t0』;所述主蒸汽實際溫度信號t0和所述跟蹤溫度信號t0』作差後得到第二差值信號δt2,該第二差值信號δt2與主蒸汽設定溫度信號t作差後得到所述第一差值信號δt1。
其中,結合圖4可知內模控制原理,將圖4作等效變換,得到等效結構圖。詳見圖5。
閉環系統有:
如果模型匹配,即gp(s)=gm(s)時,式(1)可簡化為:
y(s)=gc(s)gp(s)r(s)+[1-gc(s)gm(s)]gd(s)d(s)(2)
此時如果滿足則有:
公式(3)表明,內模控制器能夠實現對參考輸入的無偏差跟蹤。然而理想控制器特性是在存在且控制器gc(s)可以實現的條件下得到的。然而由於控制過程中時滯和慣性環節的存在,中將出現純超前和純微分環節,因此常規的內模控制器可按下列方法設計:
1)將gm(s)分為兩項,即:
gm(s)=gm+(s)gm-(s)(4)
其中:gm+(s)為模型中包含純滯後和不穩定零點的部分,gm-(s)為模型中的最小相位部分。
2)求取內模控制器:
gc(s)=f(s)/gm-(s)(5)
式中f(s)為低通濾波器,其形式為
其中λ濾波參數,是內模控制器僅有設計參數。
考慮一階時滯過程內模pid控制器的設計
被控對象傳遞函數模型:
取濾波器為:
由式(5)可得內模控制器為:
相應的反饋控制器為:
為使式(10)具有pid控制器的形式,用一階taylor級數逼近時滯項
e-τs=1-τs(11)
故可得內模pid控制器形式如下:
顯然式(12)具有pi控制器的形式。
在本實施例中,減溫控制模塊包括第一減溫控制模塊和第二減溫控制模塊,第一減溫控制模塊包括第一減溫控制器、第一補償模塊和第一幹擾模塊,所述第一減溫控制器獲取第三差值信號δt3並輸出第一減溫控制信號a,所述一級減溫水流量閥根據所述第一減溫控制信號a來改變閥門開度,從而改變一級減溫水流量,進而改變所述第一溫度監測器採集的所述第一減溫溫度值t1;所述第一幹擾模塊獲取第一幹擾驅動信號,並輸出第一幹擾信號d,所述第一蒸汽監測溫度與所述第一幹擾信號d作差後得到所述第一減溫蒸汽溫度信號t3;所述第一補償模塊獲取第一補償驅動信號,並輸出第一補償信號c,所述主蒸汽溫度控制信號t1與所述第一減溫蒸汽溫度信號t3、第一補償信號c依次作差後得到所述第三差值信號δt3。其中主蒸汽溫度控制信號t1作為被減數,第一減溫蒸汽溫度信號t3、第一補償信號c作為減數。
所述第二減溫控制系統包括第二減溫控制器、第二補償模塊和第二幹擾模塊,所述第二減溫控制器獲取第四差值信號δt4並輸出第二減溫控制信號b,所述二級減溫水流量閥根據所述第二減溫控制信號b來控制閥門開度,從而改變二級減溫水流量,進而改變所述第二溫度監測器採集的所述第二減溫溫度值t2;所述第二幹擾模塊獲取第二幹擾驅動信號,並輸出第二幹擾信號f,所述第二減溫溫度值t2與所述第二幹擾信號f作差後得到所述第二減溫蒸汽溫度信號t4;所述第二補償模塊獲取第二補償驅動信號,並輸出第二補償信號h,所述第一減溫蒸汽溫度信號t3與所述第二減溫蒸汽溫度信號t4、第二補償信號h依次作差後得到所述第四差值信號δt4。其中第一減溫蒸汽溫度信號t3作為被減數,第二減溫蒸汽溫度信號t4、第二補償信號h作為減數。
在本實施例中,第一幹擾驅動信號為相鄰兩個時刻所述一級減溫器蒸汽輸出口的蒸汽流量信號差值δd1。
在本實施例中,所述第一補償驅動信號為相鄰兩個時刻所述一級減溫器蒸汽輸出口的蒸汽流量信號差值δd1。
其中,一級減溫器蒸汽輸出口的蒸汽流量信號差值δd1=d1i-d1(i-1),其中d1i為時刻ti的一級減溫器蒸汽輸出口的蒸汽流量信號,d1(i-1)為時刻ti-1的一級減溫器蒸汽輸出口的蒸汽流量信號。
在本實施例中,第二幹擾驅動信號為相鄰兩個時刻所述二級減溫器蒸汽輸出口的蒸汽流量信號差值δd2。
在本實施例中,所述第二補償驅動信號或為相鄰兩個時刻所述二級減溫器蒸汽輸出口的蒸汽流量信號差值δd2。
相鄰兩個時刻所述二級減溫器蒸汽輸出口的蒸汽流量信號差值δd2=d2i-d2(i-1),其中d2i為時刻ti的一級減溫器蒸汽輸出口的蒸汽流量信號,d2(i-1)為時刻ti-1的一級減溫器蒸汽輸出口的蒸汽流量信號。
在本實施例中,第三幹擾驅動信號d0為流經所述鍋爐汽包輸出的蒸汽流量信號。
從圖6可以看出,所述主蒸汽系統還設置有自適應pid修正模塊,所述自適應pid修正模塊以輸入溫度偏差e和偏差變化率ec作為輸入,所述自適應pid控制器輸出參數增量信號δk至所述內模控制器;
所述輸入溫度偏差e為所述主蒸汽設定溫度信號t與所述主蒸汽實際溫度信號t0的差值;所述偏差變化率
從圖6可以看出,自適應pid在線修正模塊的工作原理是:首先根據操作人員的經驗制定推理規則,然後將輸入蒸汽溫度偏差信號模糊化處理後,在模糊智能在線修正單元中依據該規則推理運算出相應的決策結果,並將該結果反模糊化等處理後得到所求參數修正值,即主迴路內模pid控制器的參數修正值,將該修正值與內模pid基本設定值疊加後作為內模pid新的動態設定值,從而完成對控制器參數的在線修正。參數修正的表達式如下
kp=k′p+δkp
ki=k′1+δki
kd=k′d+δkd
式中k′p、k′i、k′d為控制器基本設定值,δkp、δki、δkd為修正值,kp、ki、kd為修正後的控制器動態設定值。
其中,本方案設計的推理規則是:
1)當e為nb且ec也為nb時,即偏差為負大且有繼續偏大的趨勢,實測主蒸汽溫度高於設定值540℃且偏差繼續增大,為儘快消除已有負大偏差及變大的趨勢,需要增大控制器比例p的參數值,為防止積分飽和需減小積分i的值,為避免過大超調,微分d取較小值或零,即δkp為pb,δki為nb,δkd為ps,這樣使得控制器參數處在控制要求內,使得主蒸汽溫度快速穩定。
2)當e為zo且ec為ns時,即偏差為零且有增大趨勢,實測主蒸汽溫度等於設定值540℃但有上升趨勢,此時應增大控制器p的值提高響應速度,適當減小積分i的值提高系統穩定性能,微分環節取適當值減小穩定時的振蕩,即δkp為ps,δki為ns,δkd為ns。
3)當e為pb且ec也為pb時,即偏差為正大且有增大趨勢,實測主蒸汽溫度低於設定值540℃且有繼續減小趨勢。為消除已有的正大偏差並抑制偏差的進一步變大,需減小控制器p的值,並增大控制器積分和微分的值,使系統獲得較好的穩態性能,即δkp為nb,δki為pb,δkd為pb。
逐條分析各種情況,可得到控制器參數模糊智能在線修正單元的模糊規則表,如下表1~3所示:
表1δkp的模糊規則表
表2δki的模糊規則表
表3δkd的模糊規則表
在本方案中,e和ec為輸入溫度偏差和偏差變化率,e和ec為模糊化處理後的溫度偏差和偏差變化率。nb(負大,negativebig)、nm(負中,negativemedium)、ns(負小,negativesmall)、zo(零、zero)、ps(正小,postivesmall)、pm(正中,postivemedium)、pb(正大,postivebig)。
應當指出的是,上述說明並非是對本發明的限制,本發明也並不僅限於上述舉例,本技術領域的普通技術人員在本發明的實質範圍內所做出的變化、改性、添加或替換,也應屬於本發明的保護範圍。