基巖段不良含水層定位靶向注漿立井井壁結構、施工裝置及方法與流程
2023-12-04 19:08:46 2
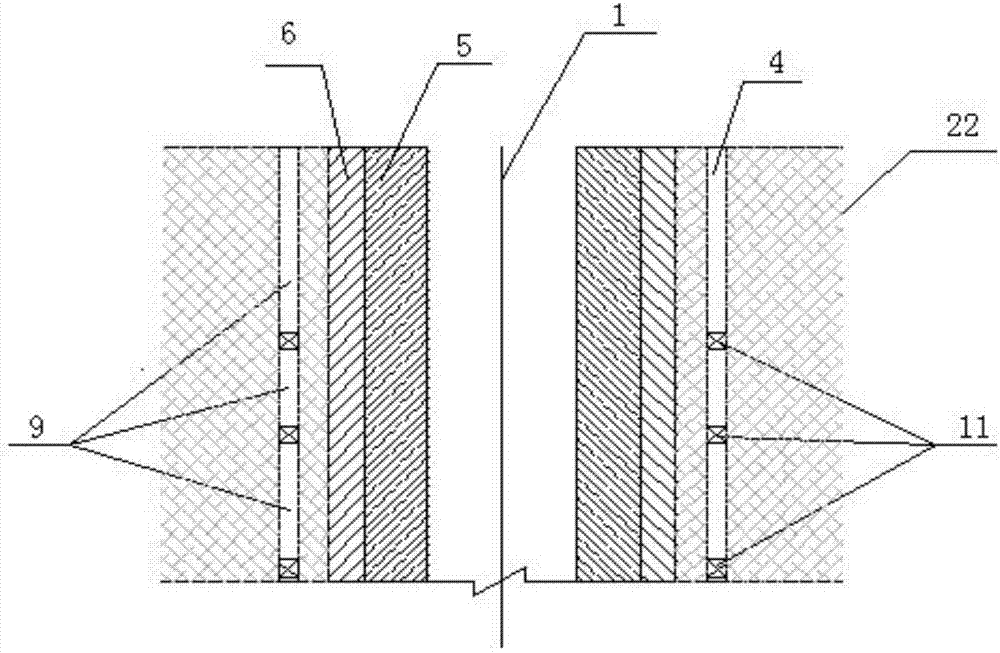
技術領域:
本發明屬於礦井立井建設技術領域,尤其涉及不良地層的立井井壁結構及施工方法。
背景技術:
立井是地下採礦聯繫地下與地表的重要提升、通風、運輸、排水及人員安全通道,井筒與地表直接相連,直接承受井筒提升設施的全部荷載,為此,必須確保立井井筒結構具有足夠的承載力和抗變形能力。
隨著採礦業的迅速發展,地下採礦所佔的比例越來越大,立井越來越深、穿過的地層越來越複雜,尤其是立井井筒基巖段處於不良含水層為強風化層、中風化層和富水層,其中,強風化層和中風化層屬於弱含水層,裂隙發育程度存在差異,下部為強含水層。不良含水層原巖成分以凝灰質為主,受強風化作用多變化為高嶺土等黏土礦物,呈鬆散土狀或呈殘塊狀,見空氣或遇水則解體呈鬆散狀,裂隙透水,湧水量大,井筒無法下掘、支護。
現在,立井井筒基巖段處於不良含水層的常規方法為冷凍法或井筒工作面注漿法。冷凍法是從地表鑽一圈或兩圈凍結孔至穩定巖層或井筒底部10m~20m,在凍結孔內全孔設置凍結鋼管,在地表布置冷凍站,通過凍結鋼管將製冷液循環輸送至凍結孔底,從而達到凍結井筒周身圍巖,達到防滲水加固圍巖的目的。存在缺陷是,該方法冷凍系統裝備工期長、造價高、耗電量大。井筒工作面注漿法,是井筒工作面快接近不良含水層時,停止掘進,留10m左右止漿巖冒或澆築混凝土止漿墊,在井筒工作面內布置鑽孔,進行工作面注漿。存在缺陷是,該方法採用的注漿泵功率小,注漿能力低,注漿材料消耗少,很難堵住裂隙通道裡的水,井筒開挖後,湧水量仍然很大,裂隙湧水帶動圍巖坍塌,造成災害。實踐表明,該兩種方法均存在缺陷,無法滿足井筒掘砌和承載力的要求。因此,尋求更為合理的一種基巖段不良含水層定位靶向注漿立井井壁結構及施工方法迫在眉睫。
技術實現要素:
為克服現有技術的缺陷,本發明的目的是提供一種基巖段不良含水層定位靶向注漿立井井壁結構及施工方法,該結構簡單、穩定、可靠、施工快速,能保證立井井筒的穩定性。
基巖段不良含水層定位靶向注漿立井井壁結構,包括在不良含水層中設置的井筒,其特點是,所述的井筒周圍設置定位靶向注漿鑽孔、孔口管、注漿段、外壁和內壁;所述的定位靶向注漿鑽孔,以井筒中心為圓心沿井筒荒徑線圓周2m外成對均勻布置並垂直地面,全井至少設置8個定位靶向注漿鑽孔;所述的孔口管設置在定位靶向注漿鑽孔內,水泥漿液由靶向注漿鑽孔注入,擴充至鑽孔周圍5~10m基巖段裂隙發育的不良含水層中,凝固成注漿段,注漿段分層設置在基巖段所處的不良含水層內,堵住裂隙,加固圍巖;所述的外壁為不小於300mm厚的鋼筋混凝土,內壁為不小於600mm厚的鋼筋混凝土。
進一步改進,所述的定位靶向注漿鑽孔,是利用鑽機從地面往下垂直鑽成,深度應穿過不良含水層下端10m厚度,孔口管段鑽孔直徑不小於250mm、下部鑽孔直徑不小於133mm。
進一步改進,所述的孔口管採用異徑結構形式,其中垂深0~10m段,管材規格為φ219×6mm;垂深10~30m段,管材規格為φ159×5mm。
進一步改進,所述的注漿段的注漿材料根據地層的圍巖破碎程度、裂隙發育情況及用水量選擇黏土水泥漿液/超細水泥漿;注漿壓力為所在高度位置靜水壓力的2.5~4倍;段高30m~50m,根據揭露地層情況而定。
進一步改進,所述的黏土水泥漿液水灰的重量比取值範圍為1.2~1.5,超細水泥漿水灰重量比取值範圍為0.8~1.0;所述的超細水泥漿由水泥加水、食鹽、三乙醇胺配製而成,三乙醇胺加入量為水泥重量的0.5‰,食鹽加入量為水泥重量的5‰;所述的水泥為普通矽酸鹽p·o42.5;水玻璃為28~40be;黏土的含砂量小於5%。
進一步改進,所述的注漿材料通過8個定位靶向注漿鑽孔在基巖段不良含水層向荒徑外擴散5~10m,堵住裂隙水,加固圍巖。
進一步改進,所述的外壁混凝土為標號不小於c30,混凝土內布置雙層鋼筋,受力筋直徑不小於20mm,沿井筒周邊布置,間距300mm;分部筋直徑不小於20mm,沿井筒中心線方向布置,間距300mm。
進一步改進,所述的內壁混凝土為標號不小於c30,混凝土內布置單層鋼筋,受力筋直徑不小於20mm,沿井筒周邊布置,間距300mm;分部筋直徑不小於20mm,沿井筒中心線方向布置,間距300mm。
基巖段不良含水層定位靶向注漿立井井壁結構施工裝置,其特點是包括原漿池、貯漿池、清水池、水玻璃池和成對設置的水泥罐、泥漿泵、一級攪拌罐、二級攪拌罐、高壓注漿泵,就近設在井筒附近;原漿池和貯漿池管道直接;一級攪拌罐進料口由管道與水泥罐連接,由管道、泥漿泵連接貯漿池,由管道與清水池連接,配入適量的水泥、泥漿和清水;二級攪拌罐進料口與一級攪拌罐出料口管道連接,由管道與水玻璃池連接,一級攪拌罐的水泥漿再加入水玻璃,在二級攪拌罐中繼續攪拌,二級攪拌罐出料口與高壓注漿泵、定位靶向注鑽孔管道相連接,高壓注漿泵將水泥漿高壓注入鑽孔內。
基巖段不良含水層定位靶向注漿立井井壁結構施工方法,按如下步驟進行:
1、標定定位靶向注漿立井井壁結構施工線按照設計坐標在地表標定出井筒中心點,根據井筒中心點和設計的井筒淨直徑和支護厚度標定出井筒淨徑線和荒徑線;沿井筒荒徑線外2m圓周至少對稱均勻布置8個垂直地面的定位靶向注鑽孔,鑽孔直徑不小於250mm,深度應穿過不良含水層厚度下端10m,連續編號為1#、2#、3#、4#、5#、6#、7#、8#,將8個孔分成兩組,第一組為1#、3#、5#、7#,第二組為2#、4#、6#、8#;先施工第一組鑽孔,根據場地大小,同時施工2/4個鑽孔;
2、設置注漿站在地面適當就近位置就近設置注漿站,共設兩套注漿系統,包括兩個水泥罐、一個原漿池、一個貯漿池、一個清水池、一個水玻璃池、兩個泥漿泵、兩個一級攪拌罐、兩個二級級攪拌罐、兩個注漿泵;
3、安裝鑽機按設計要求進行場平,在標定的孔位上方安裝工字鋼底盤,在底盤上安裝鑽機及鑽塔;
4、鑽孔及設孔口管採用φ250mm鑽頭向下鑽進40.5m,在鑽孔內下放設置長10m、直徑φ219×6mm和長30m、直徑φ159×5mm的異徑結構孔口管,向孔口管內注入水灰重量比為0.6:1的水泥漿,直至孔口返漿為止;經24小時養護,掃口至原來深度進行壓水試驗,檢查固結質量,如發現漏水現象,應再次進行注漿固結;
5、設置止漿塞採用φ133mm複合片鑽頭無芯向下鑽進至第一注漿段,在孔口管段設置kws型止漿塞;
6、壓水試驗通過鑽杆向鑽孔內注水,進行壓水試驗,符合設計標準後,方可進行高壓注漿;
7、高壓注漿按設計比例製備水泥黏土漿液,通過鑽杆向鑽孔內高壓注漿,達到注漿設定壓力,穩定時間20min,達到或接近設計注漿量後,該段注漿結束;
8、掃口,重複5、6、7步驟進入下一注漿段施工,kws型止漿塞設置在注漿段上部穩定巖層中;
9、開挖井筒在井筒設計的荒徑線範圍內自上而下逐次分段開挖井筒,每次開挖深度不大於4m;
10、澆築井筒外壁鋼筋混凝土自上而下澆築井筒外壁鋼筋外壁,直至注漿段底部;混凝土為標號不小於c30,混凝土內布置雙層鋼筋,受力筋直徑不小於20mm,沿井筒周邊布置,間距300mm;分部筋直徑不小於20mm,沿井筒中心線方向布置,間距300mm。
11、澆築井筒內壁鋼筋混凝土從注漿段底部自下而上連續澆築井筒內壁鋼筋混凝土,直至井口地表;混凝土為標號不小於c30,混凝土內布置雙層鋼筋,受力筋直徑不小於20mm,沿井筒周邊布置,間距300mm;分部筋直徑不小於20mm,沿井筒中心線方向布置,間距300mm;
12、拆除施工裝置,施工結束。
與現有技術相比,優點是構思新穎,結構簡單,穩定可靠,注漿段護衛基巖段井筒,承載力高,堵水效果好,施工快速,方便,能夠實現井筒快速掘砌,節省費用。
附圖說明
下面對照附圖對本發明作進一步說明。
圖1基巖段不良含水層定位靶向注漿立井井壁結構平面示意圖。
圖2是圖1之b-b剖面井壁結構示意圖
圖3是孔口管剖面示意圖。
圖4是圖1之施工裝置結構示意圖。
圖中:1、井筒中心2、淨徑線3、荒徑線4、鑽孔5內壁6、外壁7、孔口管8、水泥漿9、注漿段10鑽機11、止漿塞12、鑽杆13、原漿池14、貯漿池15、泥漿泵16、清水池17、水泥罐18、一級攪拌罐19、水玻璃池20、二級攪拌罐21、高壓注漿泵22、含水地層
具體實施方式
由圖1、圖2、圖3可以看出,基巖段不良含水層定位靶向注漿立井井壁結構,包括在不良含水層中設置的井筒,井筒1周圍設置定位靶向注漿鑽孔4、孔口管7、注漿段9、外壁6和內壁5;定位靶向注漿鑽孔,以井筒中心1.1(圖中未標註)為圓心沿井筒荒徑線3圓周2m外成對均勻布置並垂直地面,全井至少設置8個定位靶向注漿鑽孔;所述的孔口管設置在定位靶向注漿鑽孔內,水泥漿液由靶向注漿鑽孔注入,擴充至鑽孔周圍8m基巖段裂隙發育的不良含水層中,凝固成注漿段,注漿段分層設置在基巖段所處的不良含水層22內,堵住裂隙,加固圍巖;所述的外壁為350mm厚的鋼筋混凝土,內壁為700mm厚的鋼筋混凝土。
由圖1、圖2、圖3可以看出,所述的定位靶向注漿鑽孔,是利用鑽機10從地面往下垂直鑽成,深度應穿過不良含水層下端10m厚度,孔口管段鑽孔直徑350mm、下部鑽孔直徑145mm。
由圖1、圖2、圖3可以看出,所述的孔口管採用異徑結構形式,其中垂深0~10m段,管材規格為φ219×6mm;垂深10~30m段,管材規格為φ159×5mm。
由圖1、圖2、圖3可以看出,所述的注漿段的注漿材料根據地層的圍巖破碎程度、裂隙發育情況及用水量選擇黏土水泥漿液/超細水泥漿;注漿壓力為所在高度位置靜水壓力的3倍;段高45m,根據揭露地層情況而定。
由圖1、圖2、圖3可以看出,所述的黏土水泥漿液水灰重量比取值範圍為1.3,超細水泥漿水灰重量比取值範圍為0.9;所述的超細水泥漿由水泥加水、食鹽、三乙醇胺配製而成,三乙醇胺加入量為水泥重量的0.5‰,食鹽加入量為水泥重量的5‰;所述的水泥為普通矽酸鹽p·o42.5;水玻璃為28~40be;黏土的含砂量小於5%。
由圖1、圖2、圖3可以看出,所述的注漿材料通過8個定位靶向注漿鑽孔在基巖段不良含水層向荒徑外擴散8m,堵住裂隙水,加固圍巖。
由圖1、圖2、圖3可以看出,所述的外壁混凝土標號c30,混凝土內布置雙層鋼筋,受力筋直徑25mm,沿井筒周邊布置,間距300mm;分部筋直徑22mm,沿井筒中心線方向布置,間距300mm。
由圖1、圖2、圖3可以看出,所述的內壁混凝土標號不小於c30,混凝土內布置單層鋼筋,受力筋直徑25mm,沿井筒周邊布置,間距300mm;分部筋直徑22mm,沿井筒中心線方向布置,間距300mm。
由圖1、圖2、圖3可以看出,基巖段不良含水層定位靶向注漿立井井壁結構施工裝置,其特點是包括原漿池13、貯漿池14、清水池16、水玻璃池19和成對設置的水泥罐17、泥漿泵15、一級攪拌罐18、二級攪拌罐20、高壓注漿泵21,就近設在井筒附近;原漿池和貯漿池管道直接;一級攪拌罐進料口由管道與水泥罐連接,由泥漿泵連接貯漿池,由管道與清水池連接,配入適量的水泥、泥漿和清水;二級攪拌罐進料口與一級攪拌罐出料口管道連接,由管道與水玻璃池連接,一級攪拌罐的水泥漿再加入水玻璃,在二級攪拌罐中繼續攪拌,二級攪拌罐出料口與高壓注漿泵、定位靶向注鑽孔管道相連接,高壓注漿泵將水泥漿高壓注入鑽孔內。
基巖段不良含水層定位靶向注漿立井井壁結構施工方法,按如下步驟進行:
1、標定定位靶向注漿立井井壁結構施工線按照設計坐標在地表標定出井筒中心點,根據井筒中心線1.1和設計的井筒淨直徑和支護厚度標定出井筒淨徑線和荒徑線;沿井筒荒徑線外2m圓周至少對稱均勻布置8個垂直地面的定位靶向注鑽孔,鑽孔直徑不小於250mm,深度應穿過不良含水層厚度下端10m,連續編號為1#、2#、3#、4#、5#、6#、7#、8#,將8個孔分成兩組,第一組為1#、3#、5#、7#,第二組為2#、4#、6#、8#;先施工第一組鑽孔,根據場地大小,同時施工2/4個鑽孔;
2、設置注漿站在地面適當就近位置就近設置注漿站,共設兩套注漿系統,包括兩個水泥罐、一個原漿池、一個貯漿池、一個清水池、一個水玻璃池、兩個泥漿泵、兩個一級攪拌罐、兩個二級級攪拌罐、兩個注漿泵;
3、安裝鑽機按設計要求進行場平,在標定的孔位上方安裝工字鋼底盤,在底盤上安裝鑽機及鑽塔;
4、鑽孔及設孔口管採用φ250mm鑽頭向下鑽進40.5m,在鑽孔內下設置長10m,直徑φ219×6mm和長30m直徑φ159×5mm的異徑結構孔口管,向孔口管內注入水灰重量比為0.6:1的水泥漿,直至孔口返漿為止;經24小時養護,掃口至原來深度進行壓水試驗,檢查固結質量,如發現漏水現象,應再次進行注漿固結;
5、設置止漿塞採用φ133mm複合片鑽頭無芯向下鑽進至第一注漿段,在孔口管段設置kws型止漿塞;
6、壓水試驗通過鑽杆向鑽孔內注水,進行壓水試驗,符合設計標準後,方可進行高壓注漿;
7、高壓注漿按設計比例製備水泥黏土漿液,通過鑽杆向鑽孔內高壓注漿,達到注漿設定壓力,穩定時間20min,達到或接近設計注漿量後,該段注漿結束;
8、掃口,重複4、5、6、7步驟進入下一注漿段施工,kws型止漿塞設置在注漿段上部穩定巖層中;
9、開挖井筒在井筒設計的荒徑線範圍內自上而下逐次分段開挖井筒,每次開挖深度3.5m;
10、澆築井筒外壁鋼筋混凝土自上而下澆築井筒外壁鋼筋外壁,直至注漿段底部;混凝土為標號c30,混凝土內布置雙層鋼筋,受力筋直徑25mm,沿井筒周邊布置,間距300mm;分部筋直徑22mm,沿井筒中心線方向布置,間距300mm。
11、澆築井筒內壁鋼筋混凝土從注漿段底部自下而上連續澆築井筒內壁鋼筋混凝土,直至井口地表;混凝土為標號c30,混凝土內布置雙層鋼筋,受力筋直徑25mm,沿井筒周邊布置,間距300mm;分部筋直徑22mm,沿井筒中心線方向布置,間距300mm。
12、拆除施工裝置,施工結束。