表層套管固井居中方法與流程
2023-12-10 12:20:27 2
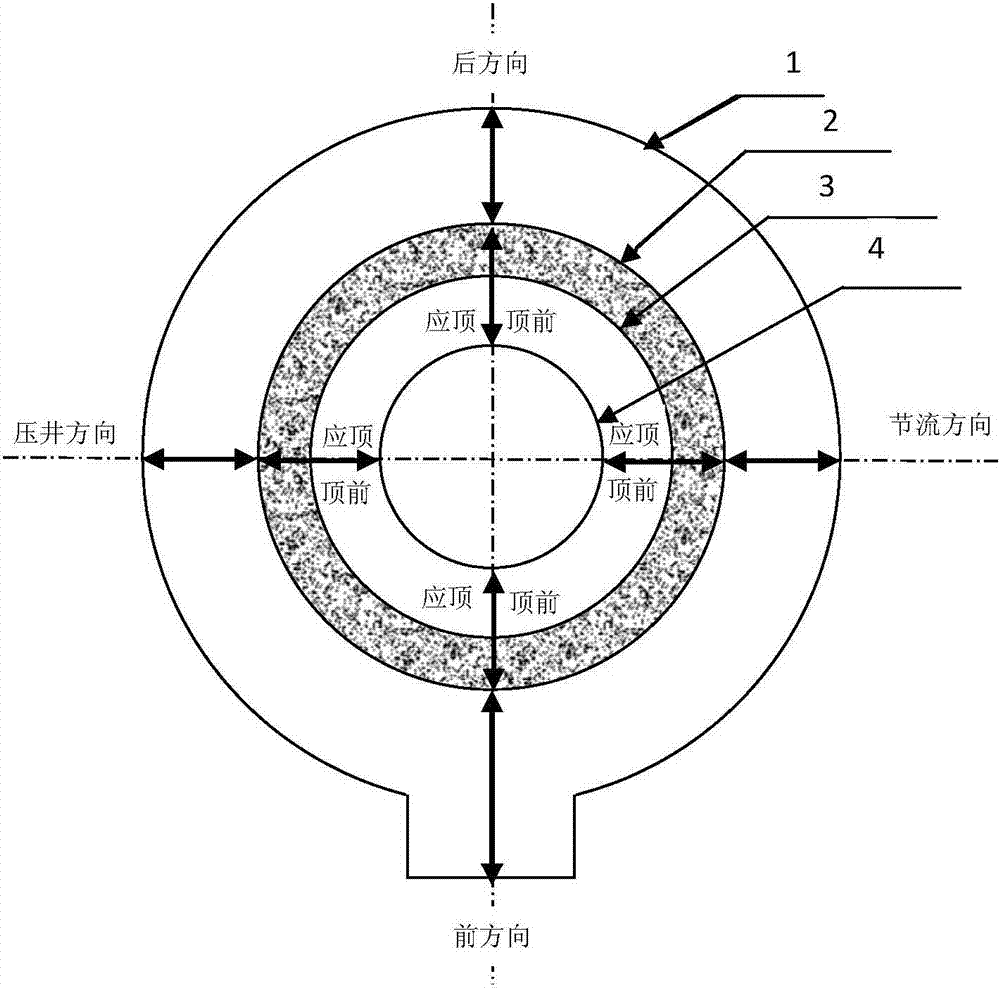
本發明涉及鑽井的固井及井控安全領域,尤其涉及一種表層套管固井居中方法。
背景技術:
鑽井作業中,若表層套管不居中,則會導致在後期的鑽井作業或井下其它作業過程中,位於近井口的技術套管與井口偏磨、破裂,從而給鑽井和安全生產過程中的井控安全埋下隱患。其中,套管居中指的是天車、轉盤中心、套管中心呈一條直線。
目前,國內外現有技術針對套管防磨損主要是針對鑽井工具、鑽井工藝採用技術措施,或在套管內進行塗層減輕磨損,以及在鑽井液等方面進行改進,以減少套管磨損;但上述措施均未從導致套管磨損的主要因素,即表層套管不居中而造成井口不正,進行有效地改進。因此,亟需一種可以從根本上解決井口不正造成井控裝備(如鑽頭)和技術套管偏磨這一問題的方法。
技術實現要素:
本發明提供一種表層套管固井居中方法,可實現表層套管準確居中,從本質上解決因井口不正帶來的井控裝備和技術套管偏磨等問題,具有很大的實用價值,易推廣。
本發明提供一種表層套管固井居中方法,包括:
在鑽井內的導管的周向邊沿套設一導管法蘭,所述導管法蘭具有與所述導管法蘭的軸線相垂直的第一圓形橫截面;
將轉盤中心投影到所述第一圓形橫截面上,形成第一投影點;
測量所述第一投影點與所述導管法蘭外徑之間在0度、90度、180度、270度四個方向上的距離,得到第一組校正數據;其中,所述0度為所述導管的後方;所述90度為節流壓井方向;所述180度為所述導管的前方;所述 270度為壓井管匯方向;
所述導管內設置有表層套管;根據所述第一組校正數據以及所述表層套管的半徑,對所述表層套管的中心位置進行校正,以使所述表層套管的中心與所述轉盤中心重合。
可選的,所述根據所述第一組校正數據以及所述表層套管的半徑,對所述表層套管的中心位置進行校正之前,還包括:
在所述四個方向上,穿過所述導管分別設置一個頂絲,以使所述頂絲牴觸所述導管內的所述表層套管的外壁;
相應的,所述根據所述第一組校正數據以及所述表層套管的半徑,對所述表層套管的中心位置進行校正,包括:
計算所述第一組校正數據與所述表層套管的半徑的差值,得到所述表層套管邊緣在所述四個方向上與所述導管法蘭外徑之間的標準距離值;根據所述標準距離值,調整所述四個方向上的所述頂絲,所述頂絲推動所述表層套管移動,以使所述表層套管移動到所述轉盤中心與所述表層套管中心重合的位置。
可選的,所述對所述表層套管的中心位置進行校正,以使所述表層套管的中心與所述轉盤中心重合之後,還包括:
對所述轉盤中心與所述表層套管中心是否重合進行檢測,得到所述轉盤中心與所述表層套管中心的偏距值;
其中,所述對所述轉盤中心與所述表層套管中心是否重合進行檢測包括:
將轉盤中心投影到第二圓形橫截面上,形成第二投影點;所述第二圓形橫截面為與所述表層套管的軸線相垂直的圓形橫截面;
在任一所述第二圓形橫截面上,測量所述第二投影點與所述表層套管中心點之間的距離,得到所述偏距值。
可選的,所述得到所述偏距值之後,還包括:
若所述偏距值小於等於預設偏距閾值,將所述頂絲與所述導管焊接固定;若所述偏距值大於所述預設偏距閾值,調整所述四個方向上的所述頂絲,所述頂絲推動所述表層套管移動,以使所述表層套管移動到所述轉盤中心與所述表層套管中心重合的位置。
可選的,所述預設偏距閾值為10mm。
可選的,所述根據所述第一組校正數據以及所述表層套管的半徑,對所述表層套管的中心位置進行校正之前,還包括:
將強行扶正卡盤設置在所述表層套管的上部,以對所述表層套管進行位置固定。
可選的,所述導管的管壁厚9mm;所述導管法蘭的壁厚300mm。
可選的,所述對所述表層套管的中心位置進行校正,以使所述表層套管的中心與所述轉盤中心重合之後,還包括:
在所述表層套管與所述導管的間隙空間中填充固定材料,以使所述表層套管相對於所述導管的位置固定。
本發明提供的表層套管固井居中方法,通過在鑽井內的導管的周向邊沿套設一導管法蘭,導管法蘭具有與導管法蘭的軸線相垂直的第一圓形橫截面;將轉盤中心投影到第一圓形橫截面上,形成第一投影點;測量第一投影點與導管法蘭外徑之間在0度、90度、180度、270度四個方向上的距離,得到第一組校正數據;其中,0度為導管的後方;90度為節流壓井方向;180度為導管的前方;270度為壓井管匯方向;導管內設置有表層套管;根據第一組校正數據以及表層套管的半徑,對表層套管的中心位置進行校正,以使表層套管的中心與轉盤中心重合。實現表層套管居中並實現其居中固井,從本質上解決了因井口不正帶來的井控裝備和技術套管偏磨等問題,具有很大的實用價值,易推廣。
附圖說明
圖1a為本發明表層套管固井居中方法的實施例一的流程圖;
圖1b為圖1a所示實施例的一結構示意圖;
圖2為本發明表層套管固井居中方法的實施例二的流程圖。
具體實施方式
為使本發明實施例的目的、技術方案和優點更加清楚,下面將結合本發明實施例,對本發明實施例中的技術方案進行清楚、完整地描述。需要說明的是,在附圖或說明書中,相似或相同的元件皆使用相同的附圖標記。
圖1a為本發明表層套管固井居中方法的實施例一的流程圖,如圖1a所 示,本實施例的方法包括:
步驟101、在鑽井內的導管的周向邊沿套設一導管法蘭。
具體的,通常來說,鑽井內的導管,其導管的壁厚較薄,例如,9mm壁厚的導管;以導管作為調整表層套管的支撐,導管強度有限,若在表層套管固井居中的作業過程中導管壁變形,則易導致對表層套管是否居中的檢測造成誤差,影響表層套管居中的效果;同時,導管還存在管壁橫截面不均勻的情況,若以導管作為校正表層套管居中的基準會產生偏差。因此,為了彌補導管的上述兩個缺陷,通常可以在安裝表層套管頭的導管的斷面之上300~400mm的位置處焊接導管法蘭,為保證校正過程中的導管法蘭的強度,該導管法蘭的厚度可以為300mm。從而以套設了導管法蘭後的導管作為測量和調整表層套管的基準,方便作業且提高了表層套管居中校準的可靠性。
步驟102、將轉盤中心投影到第一圓形橫截面上,形成第一投影點。
具體的,該導管法蘭具有與導管法蘭的軸線相垂直的第一圓形橫截面,導管法蘭為均勻的圓形環狀物體,其套設在導管外。優選的,導管的外徑等於導管法蘭的內徑,以使導管與導管法蘭緊密貼合。可以藉助鉛垂、十字線等測量工具,獲取得到轉盤中心在導管法蘭面也就是導管法蘭的第一圓形橫截面上的投影點,得到第一投影點。通常來說,鑽機及配套設備一旦安裝、調試完畢,不論轉盤位置可否調整,均認為是不可調整的。因此,以轉盤中心為基準得到其在導管法蘭面上的第一投影點,再以該第一投影點為基準,獲取其他基礎測量數據。
步驟103、測量第一投影點與導管法蘭外徑之間在0度、90度、180度、270度四個方向上的距離,得到第一組校正數據。
其中,0度為導管的後方;90度為節流壓井方向;180度為導管的前方;270度為壓井管匯方向。圖1b示出了圓井內壁1、導管法蘭外徑2、導管法蘭內徑3、表層套管外徑4的位置關係俯視圖以及對上述四個方向的界定。以第一投影點為基準獲取得到第一投影點在導管後方、前方、壓井管匯方、節流壓井方等四個方向上到導管法蘭外徑的距離,得到第一組校正數據。上述四個方向為鑽井作業中常用的基準方向,其分別代表了以導管中心為基準,過導管中心的十字垂直線與導管壁邊緣的交點的方向,即0度、90度、180度、270度四個方向。
步驟104、根據第一組校正數據以及表層套管的半徑,對表層套管的中心位置進行校正,以使表層套管的中心與轉盤中心重合。
具體的,導管內設置有表層套管,第一組數據中確定了轉盤中心到導管外導管法蘭外徑間的各個距離值,因此只要根據表層套管的半徑,可以計算得到表層套管中心與轉盤中心對正所需要的調整數據值,根據該調整數據值,對表層套管在導管內的位置進行調整,從而使表層套管的中心與轉盤中心重合,實現表層套管固井居中。
本實施例的表層套管固井居中方法,通過在鑽井內的導管的周向邊沿套設一導管法蘭,導管法蘭具有與導管法蘭的軸線相垂直的第一圓形橫截面;將轉盤中心投影到第一圓形橫截面上,形成第一投影點;測量第一投影點與導管法蘭外徑之間在0度、90度、180度、270度四個方向上的距離,得到第一組校正數據;其中,0度為導管的後方;90度為節流壓井方向;180度為導管的前方;270度為壓井管匯方向;導管內設置有表層套管;根據第一組校正數據以及表層套管的半徑,對表層套管的中心位置進行校正,以使表層套管的中心與轉盤中心重合。實現表層套管居中並實現其居中固井,從本質上解決了因井口不正帶來的井控裝備和技術套管偏磨等問題,具有很大的實用價值,易推廣。
圖2為本發明表層套管固井居中方法的實施例二的流程圖,如圖2所示,在上述實施例一的基礎上,本實施例的方法包括:
步驟201、在鑽井內的導管的周向邊沿套設一導管法蘭。
步驟202、將轉盤中心投影到第一圓形橫截面上,形成第一投影點。
步驟203、測量第一投影點與導管法蘭外徑之間在0度、90度、180度、270度四個方向上的距離,得到第一組校正數據。
步驟204、在四個方向上,穿過導管分別設置一個頂絲,以使頂絲牴觸導管內的表層套管的外壁。
具體的,頂絲的一端用於連接旋擰工具,以調整頂絲插入在導管與表層套管之間的長度,具體到圖1b中,頂絲穿過導管法蘭內徑3對應的導管壁,頂在表層套管外徑4上。
步驟205、計算第一組校正數據與表層套管的半徑的差值,得到表層套管邊緣在四個方向上與導管法蘭外徑之間的標準距離值。
該標準距離值為表層套管的中心與轉盤中心重疊後,表層套管邊緣在前述四個方向上與導管法蘭外徑之間的距離。
步驟206、根據標準距離值,調整四個方向上的頂絲,頂絲推動表層套管移動,以使表層套管移動到轉盤中心與表層套管中心重合的位置。
步驟207、對轉盤中心與表層套管中心是否重合進行檢測,得到轉盤中心與表層套管中心的偏距值。
根據標準距離值對表層套管進行調整後,為了保證調整後的準確性,還需要對轉盤中心與表層套管中心是否重合進行檢測,以得到兩者中心的偏距值。偏距是指轉盤中心投影到表層套管中心平面上,並與表層套管中心的最大水平距離。具體檢測方法可以通過將轉盤中心投影到第二圓形橫截面上,形成第二投影點;其中,第二圓形橫截面為與表層套管的軸線相垂直的圓形橫截面。在任一第二圓形橫截面上,測量第二投影點與表層套管中心點之間的距離,得到偏距值。
步驟208、若偏距值小於等於預設偏距閾值,將頂絲與導管焊接固定;若偏距值大於預設偏距閾值,調整四個方向上的頂絲,頂絲推動表層套管移動,以使表層套管移動到轉盤中心與表層套管中心重合的位置。
具體的,偏距值的標準可以為:偏距值s≤6mm為優秀;偏距值6mm<s≤10mm為合格;偏距值s>10mm為不合格。預設偏距閾值為10mm。則當檢測得到偏距值s≤6mm,偏距值6mm<s≤10mm時,將頂絲與導管焊接固定,完成對表層套管的中心位置調整。若偏距值s>10mm,繼續調整四個方向上的頂絲,使頂絲推動表層套管移動,將表層套管移動到轉盤中心與表層套管中心重合的位置,直到偏距值在預設偏距閾值的範圍內。
進一步的,在對表層套管的中心位置進行校正之前,還可以包括:將強行扶正卡盤設置在表層套管的上部,以對表層套管進行位置固定。具體可以在最後一根表層套管下到位後,將強行扶正卡盤套在表層套管外部,使強行扶正卡盤在轉盤面上可以起到強行扶正表層套管的作用,以使表層套管在被調整的過程中保持穩定,不偏斜。具體過程為,首先使用強行扶正卡盤校正表層套管的上部,然後,根據開鑽前取的第1組校正數據,即轉盤中心垂直下去與壓井管匯方、節流管匯方、後方、前方導管法蘭外徑的距離及表層套管的半徑,計算好需調整的數據,調正套管下部。校正前 按圖1b所示標註頂正數據(即步驟205中得到的標準距離值),然後根據頂正數據將表層套管中心頂到與轉盤中心在此平面的投影,並帽並緊後點焊固定頂絲,從而將表層套管的下部校正。
進一步地,在表層套管的中心與轉盤中心重合後,還可以包括:在表層套管與導管的間隙空間中填充固定材料,以使表層套管相對於導管的位置固定。
具體的,作業過程中在固井完清理圓井內泥漿,根據表層套管頭安裝高度要求,畫線割斷導管,取出導管,若導管割口下水泥漿面空100mm以上,則用水泥填滿表層套管外環空,該表層套管外環空具體為在表層套管與導管的間隙空間中填充固定材料,該固定材料可以為水泥,以使表層套管相對於導管的位置固定,進一步保證表層套管中心位置不偏移轉盤中心的位置。
進一步地,還可以包括:測量第一投影點與井壁之間在前方、壓井管匯方向、節流壓井方向的距離,得到第二組校正數據;根據第二組校正數據以及表層套管的半徑,對表層套管的中心位置進行校正。
在表層套管固井居中的作業過程中,導管有可能會受到各種因素影響而導致位置發生移動,此時可以根據第二組校正數據對表層套管的中心位置進行校正。
進一步地,還可以以轉盤中心垂直下去,在井架底座基礎面上與壓井管匯方、節流壓井方、底座工字梁邊、後方或前方下工字梁的距離,以供老井加深、試油,或因基礎問題重新安井架或圓井坍塌時使用。
進一步地,在對表層套管的中心位置進行校正,以使表層套管的中心與轉盤中心重合之後,還可以包括:在表層套管上表面安裝表層套管頭;檢測表層套管頭上的法蘭面與水平面間的間距值,若間距值大於0.5mm,對與表層套管頭結合的表層套管的上表面進行打磨,以使間距值小於等於0.5mm。
具體的,在用水泥填滿表層套管外環空間且水泥凝固後,表層套管的中心位置已經固定,此時可以精割表層套管並打磨平斷面,割表層套管前大鉤放在離轉盤內表層套管母接箍以上3-5mm。套管精割後,在表層套管割口斷面上放置偏距檢驗盤,四方用三角尺檢驗表層套管中心與檢驗盤中心是否同心,從轉盤中心下放鉛垂線,在圓井接上鉛垂檢驗偏距。安裝表層套管頭,待表層套管頭安裝完後,檢驗表層套管頭上法蘭面水平面高、低差數據,高、 低之差小於0.5mm為合格,大於0.5mm為不合格。如果該井重新上鑽機作業時,可以以老井口中心為基準畫線、定位,確保偏距達到標準。
最後應說明的是:以上各實施例僅用以說明本發明的技術方案,而非對其限制;儘管參照前述各實施例對本發明進行了詳細的說明,本領域的普通技術人員應當理解:其依然可以對前述各實施例所記載的技術方案進行修改,或者對其中部分或者全部技術特徵進行等同替換;而這些修改或者替換,並不使相應技術方案的本質脫離本發明各實施例技術方案的範圍。