基於雷射納米加工技術的埋置晶片互連方法與流程
2024-01-22 03:52:15 1
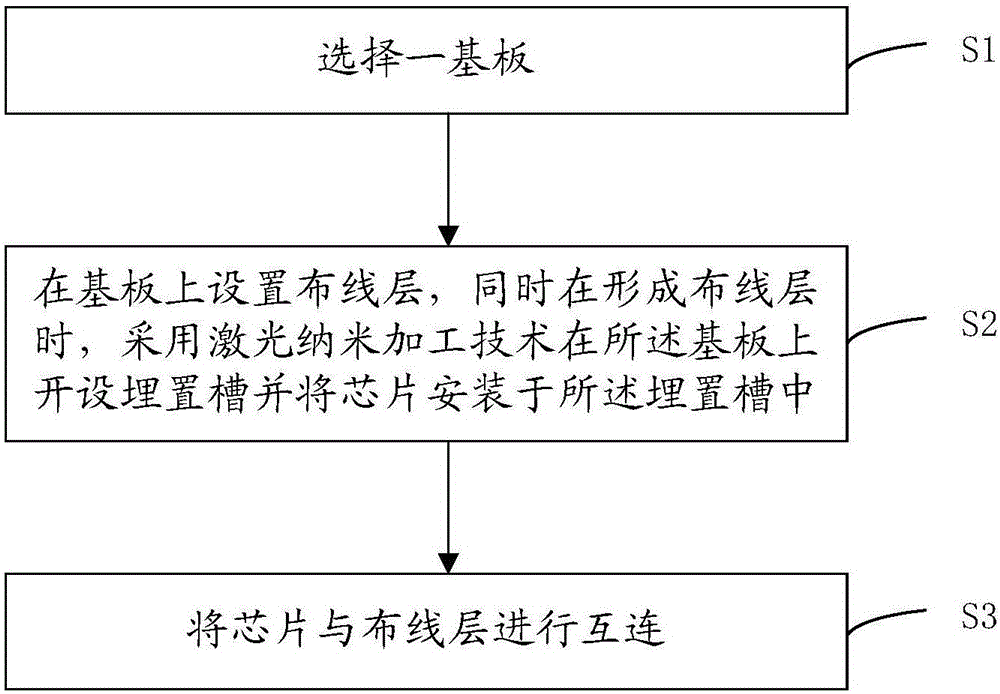
本發明涉及電子封裝技術領域,特別涉及一種基於雷射納米加工技術的埋置晶片互連方法。
背景技術:
在「遵循摩爾定律」和「超越摩爾定律」的驅動下,微電子封裝向著高集成密度、高功率密度、高可靠、低成本的方向發展,越來越多的多功能和小型化需求給封裝和基板都帶來了新的挑戰,促使電子封裝向三維封裝方向發展。將晶片器件埋入基板內部的埋入式封裝技術是實現三維封裝的方法之一,同時可有效地縮短晶片器件與封裝基板的連接距離,為高頻、高速信號傳輸提供有力的保證。
晶片埋置包括晶片先置型埋入技術、晶片中置型埋入技術和晶片後置型埋入技術。晶片先置型埋入技術是指先將晶片埋入到各類基板中,然後在晶片和基板上進行後續的多層互連布線,此方法提高了基板縱向空間的利用率。晶片中置型埋入技術是指將晶片埋入到布線層中間,然後在晶片和基板上進行後續的布線,與先置型埋入技術特點相似。晶片後置型埋入技術是指在疊層基板製作完成之後在基板上開腔,然後將晶片埋入該腔體而形成的封裝結構,此方法晶片散熱性好,可返工。埋置晶片互連方法可消除傳統的晶片與基板金屬焊區的各類焊接點,而且器件的製造過程不需要焊料,與焊料以及回流有直接或者間接關係的大量缺陷將會消失,從而提高電子產品的可靠性。
晶片先置型埋入方法需直接在基板上開槽,對於通用的Si基板,常採用幹法刻蝕或溼法腐蝕工藝,幹法刻蝕定位精度高,但成本較高。溼法腐蝕時形成倒梯形結構,需考慮腔體底部尺寸與晶片尺寸的匹配問題,晶片定位精度較低。同時Si材料的機械強度低,埋置晶片互連時會因澱積金屬層和介質層後,而產生較大的彎曲和翹曲問題,影響產品可靠性。對於散熱性高、翹曲小的金屬基板,氧化法周期長。晶片後置型埋入方法需在介質層和基板上開槽,多層基板層間介質多樣,結構複雜,通過化學方法開槽困難,效率低,成本高。
技術實現要素:
本發明的目的在於提供一種基於雷射納米加工技術的埋置晶片互連方法,以解決現有的埋置晶片互連方法中化學方法成本高、周期長、實現難度大等問題。
為實現上述目的,本發明提供了一種基於雷射納米加工技術的埋置晶片互連方法,包括以下步驟:
S1:選擇一基板;
S2:在所述基板上通過介質層光刻及金屬化布線實現多層電路的連接形成布線層,在形成布線層時,根據晶片在所述布線層中的預設位置,採用雷射納米加工技術在所述基板上的相應位置處開設埋置槽,並將晶片安裝於所述埋置槽中;
S3:將晶片與布線層進行互連。
較佳地,所述基板的材料為金屬或由金屬與非金屬的混合物構成的合金。
較佳地,所述雷射納米加工技術具體為:採用雷射器在所述基板上的相應位置進行納米加工,埋置槽的尺寸與待埋置的晶片相匹配。
較佳地,所述雷射器所發射雷射的波長為355nm的全固態紫外雷射。
較佳地,納米加工時,控制雷射光斑通過振鏡形成環狀的旋轉軌跡,根據所述旋轉軌跡半徑以埋置槽邊緣為加工起點,通過調整光斑移動速度來控制單列刻蝕槽的環狀圖案重疊面積,以及通過控制光斑的圓心的移動路徑來控制刻蝕槽列與列之間的重疊,以實現開設出所述埋置槽。
較佳地,所述步驟S2中,在形成布線層時進行開設晶片埋置槽以及將晶片安裝於所述埋置槽中分為三種情況:
先置型晶片埋置:首先進行埋置槽加工並進行晶片埋置,然後進行布線層加工;
中置型晶片埋置:在形成布線層期間加工埋置槽並進行晶片埋置,然後繼續進行布線層加工;
後置型晶片埋置:形成布線層後再加工埋置槽並進行晶片埋置。
較佳地,進行所述先置型晶片埋置時,直接通過雷射在所述預設位置處進行雷射燒蝕獲得所述埋置槽,然後進行晶片埋置及後續的布線層加工,然後所述步驟S3中,通過介質層通孔將所述晶片與布線層連接。
較佳地,進行所述中置型晶片埋置時,在形成布線層期間,在已經進行部分布線的基板上根據晶片的埋置需要在布線層或布線層與基板上進行雷射燒蝕出所需深度與尺寸的所述埋置槽,然後進行晶片埋置及後續的布線層加工,然後所述步驟S3中,通過介質層通孔將所述晶片與布線層連接。
較佳地,進行所述後置型晶片埋置時,在形成了布線層的基板上的預設位置處,通過雷射燒蝕獲得埋置槽,進行晶片的埋置,然後所述步驟S3中,通過引線鍵合實現晶片與基板的電氣互連。
較佳地,所述介質層為液態或膠狀聚合物構成。
本發明方法具有以下有益效果:
(1)將雷射納米加工技術引入到埋置晶片封裝加工中,通過紫外雷射的「冷加工」精確的實現晶片先置型開槽及晶片後置型開槽,加工精準,效率高,加工過程簡單。
(2)基於金屬基板及低介電常數介質實現高效率、低成本的晶片器件埋入基板的三維封裝方法。
(3)通過雷射納米加工技術簡化了基板或布線層的開槽過程,可有效解決不同晶片尺寸的高精度共面埋置問題,並進一步提高封裝效率,降低成本。
(4)採用金屬或合金,例如鋁基金屬材料為基板襯底,滿足熱導率高[>150W/(m·K)]、成本低。
(5)相比化學加工方法,雷射加工工序簡單,成本低,精度高,而且整個基板封裝流程工藝簡單高效。
附圖說明
圖1為本發明提供的方法流程圖;
圖2為本發明具體實施例一提供的先置型埋置晶片互連結構示意圖;
圖3A為本發明具體實施例一的埋置槽加工過程示意圖;
圖3B為本發明具體實施例一的晶片埋置過程示意圖;
圖3C為本發明具體實施例一的布線層形成過程示意圖;
圖3D為本發明具體實施例一的晶片與布線層連接過程示意圖;
圖4為本發明具體實施例三提供的後置型埋置晶片互連結構示意圖;
圖5A為本發明具體實施例三的布線層形成過程示意圖;
圖5B為本發明具體實施例三的埋置槽加工過程示意圖;
圖5C為本發明具體實施例三的晶片與布線層連接過程示意圖;
圖6為本發明優選實施方式的雷射光斑加工路徑示意圖。
標號說明:101-鋁矽金屬基底;102-接地屏蔽層;103-晶片一;104-晶片電極金屬化布線;105-金屬化布線;106-介質層;107-晶片二;108-背面介質保護層;109-鍵合引線;110-晶片一埋置槽;111-光刻膠;112-雷射束;113-晶片二埋置槽;114-旋轉軌跡;115-移動起點;116-加工路徑。
具體實施方式
為更好地說明本發明,茲以一優選實施例,並配合附圖對本發明作詳細說明,具體如下:
如圖1所示,本實施例提供了一種基於雷射納米加工技術的埋置晶片互連方法,包括以下步驟:
S1:選擇一基板;
其中,基板的材料為金屬或由金屬與非金屬的混合物構成的合金(如鋁矽合金)。這種基板具有低成本、高導熱率及高強度的特點。基板可為金屬基板圓片,具體選用散熱性高、翹曲小的氮化鋁或鋁矽圓片,圓片表面採用機械或化學的方法拋光。
S2:在基板上設置布線層,同時在形成布線層時,採用雷射納米加工技術在所述基板上開設埋置槽並將晶片安裝於所述埋置槽中;
具體地,通過介質層光刻及金屬化布線實現多層電路的連接形成布線層,在形成布線層時,根據晶片在布線層中的預設位置,採用雷射納米加工技術在基板上的相應位置處開設埋置槽,並將晶片安裝於埋置槽中;
S3:將晶片與布線層進行互連。
上述的雷射納米加工技術具體為:採用雷射器在所述基板上的相應位置進行納米加工,埋置槽的尺寸與待埋置的晶片相匹配。
優選地,雷射器所發射雷射的波長為355nm的全固態紫外雷射。
進一步地,上述的步驟S2中,在形成布線層時進行開設晶片埋置槽以及將晶片安裝於所述埋置槽中分為三種情況:
先置型晶片埋置:首先進行埋置槽加工並進行晶片埋置,然後進行布線層加工;
中置型晶片埋置:在形成布線層期間加工埋置槽並進行晶片埋置,然後繼續進行布線層加工;
後置型晶片埋置:形成布線層後再加工埋置槽並進行晶片埋置。
具體實施例一:
本實施例通過圖2、圖3A至圖3D詳細說明先置型埋置晶片互連方法實施例。參見圖2,本實施例中提供的先置型埋置晶片互連結構包括:基板101、接地屏蔽層102、晶片一103、晶片電極金屬化布線104、金屬化布線105、介質層106、晶片二107、背面介質保護層108。
在對圖2中的結構進行先置型晶片埋置時,直接通過雷射在預設位置處進行雷射燒蝕獲得埋置槽,然後進行晶片埋置及後續的布線層加工,然後所述步驟S3中,通過介質層通孔將所述晶片與布線層連接。具體地:
1.選用鋁基材料為襯底,本實施例選用鋁矽金屬基底101。用化學或機械的方法對鋁矽金屬基板101進行表面拋光,再清洗以去除表面油汙和雜質;
2.參閱圖3A,在鋁矽金屬基板101表面旋塗或噴塗光刻膠111,然後使用波長為355nm的紫外雷射112根據晶片一103和晶片二107的尺寸分別進行定深加工,獲得晶片一埋置槽110和晶片二埋置槽113;
3.參閱圖3B,電鍍Cu/Ni/Au層,用去膠液去除光刻膠,獲得接地屏蔽層102,厚度為3-5μm。將晶片103和107埋置在含有接地層金屬的晶片埋置槽內,利用導電膠粘接。
4.參閱圖3C,沉積金屬布線層TiW/Cu,然後塗光刻膠111,根據所需布線圖形進行光刻,通過溼法腐蝕獲得晶片電極金屬化布線104和金屬化布線105;
5.參閱圖3D,選擇介質層(PI或BCB)先對背面進行旋塗,獲得背面介質保護層108,接著正面旋塗獲得介質層106,通過光刻及布線層製作獲得埋置晶片與電路的連接。
具體實施例二:
本實施例為中置型埋置晶片互連方法的實施例。進行中置型晶片埋置時,在形成布線層期間,在已經進行部分布線的基板上根據晶片的埋置需要在布線層或布線層與基板上進行雷射燒蝕出所需深度與尺寸的埋置槽,然後進行晶片埋置及後續的布線層加工,然後所述步驟S3中,通過介質層通孔將所述晶片與布線層連接。其中,布線及進行具體的晶片與布線層連接等具體過程與具體實施例一相同。
具體實施例三:
本實施例通過圖4、圖5A至圖5C詳細說明後置型埋置晶片互連方法實施例。參見圖4,本實施例中提供的先置型埋置晶片互連結構包括:基板101、接地屏蔽層102、晶片一103、金屬化布線105、介質層106、晶片二107、背面介質保護層108及鍵引合線。
在對圖4中的結構進行後置型晶片埋置時,在形成了布線層的基板上的預設位置處,通過雷射燒蝕獲得埋置槽,進行晶片的埋置,然後所述步驟S3中,通過引線鍵合實現晶片與基板的電氣互連。具體地:
1.參閱圖5A,首先在基板101上進行布線層的製作,包括背面介質保護層108及正面金屬化布線105;
2.參閱圖5B,使用紫外雷射112根據晶片一103和晶片二107的尺寸分別進行定深加工,雷射根據布線層材料及基板材料進行相應的參數調整,獲得晶片一埋置槽110和晶片二埋置槽113;
3.參閱圖5C,在埋置槽底部製作接地屏蔽層102,然後將晶片貼裝於埋置槽中,晶片與基板通過引線鍵合的方式連接,埋置晶片通過鍵合引線109實現電路連接。
在一優選實施例中,介質層為低介電常數的液態或膠狀聚合物構成,例如光敏介質BCB(苯並環丁烯)。則薄膜互連線通過光刻的方式排布在固化後的所述的低介電常數的液體或膠狀聚合物上。
在一優選實施例中,參見圖6,通過納米加工技術進行埋置槽110的加工時,控制雷射光斑通過振鏡形成環狀的旋轉軌跡114,根據旋轉軌跡114的半徑以埋置槽邊緣為加工起點115,通過調整光斑的移動速度來控制單列刻蝕槽的環狀圖案重疊面積,以及通過控制光斑的圓心的加工(移動)路徑116來控制刻蝕槽列與列之間的重疊,以實現開設出埋置槽。這種雷射冷加工的方式類似銑床的方式進行埋置槽的高精度加工,雷射能量參數、光斑移動速度、光圈重疊率均由加工材料及加工圖形尺寸所決定。
該方法選擇低成本、高導熱率及高強度的金屬(如鋁矽合金)作為晶片埋置基板,利用雷射納米加工技術獲得埋置晶片的腔體結構,實現不同尺寸晶片的高精度共面埋置;以低介電常數的液態或膠狀聚合物作為介質層,並依次通過介質層填充、介質層光刻、薄膜金屬層布線等工藝,實現埋置晶片互連結構。
本發明是基於雷射納米加工技術,利用紅外雷射波長短脈寬小的特點,通過對基板或介質層的脈衝冷加工方法實現晶片埋置槽的高精度加工,為晶片埋置提供了高效率與高精度的加工方法,解決了化學方法周期長程序繁瑣的問題,實現晶片在基板或布線層埋置及互連的方法。
以上所述,僅為本發明的具體實施方式,但本發明的保護範圍並不局限於此,任何本領域的技術人員在本發明揭露的技術範圍內,對本發明所做的變形或替換,都應涵蓋在本發明的保護範圍之內。因此,本發明的保護範圍應以所述的權利要求的保護範圍為準。